Introduction: Rebuilding a Service Jack Power Unit
We are all here because we are cheap. Save a few dollars doing things ourselves. Some of us are stubborn and others want to learn. This tutorial will go over the repair of Sears Craftsman aluminum floor jack 50239. I will also give tips about general floor jack principles and hydraulic work.
I bought this jack on sale for 200$ about 10 years ago and I have used it to work on all types of vehicles. Recently, I was driving cross country and my friends were off on the weight of the trailer which might have blown out my jack seals. I found this out when I went to go and lift another trailer.
Floor jacks, or service jacks have a removable and rebuildable power unit once they have reached certain cost threshold. You will need to make a decision on the cost effectiveness of repairing the tool. In my case, I spent $200 on the jack and was able to purchase a rebuild kit with all seals and ball bearings for 50$ including shipping. I could purchase just the ram seal for 25$ and source the o rings locally at the hardware store. This would likely save me money, but paying 20 dollars for all of the correct items in a kit is well worth my time. If this seal was not available, I would make one out of leather. Now is the time when I have to lie to myself about saving money by repairing this. The 200$ jack lasted 10 years. 20$ per year. I could replace it with a similar jack for 100$ to 150$. Lower quality, but a throw away unit. The two replacements I would like to get cost 300$ and 550$ respectively. If I could get another 2.5 years out of the jack for 50$, that is worth it right? I also believe that when you rebuild something correctly, it will last longer than the factory assembly. In this case, I took extra time to clean and debur edges that are rough. I can bed in each seal and make sure everything moves fluidly. The dude getting paid 7 dollars an hour for assembly could care less. I also can validate my large investment in tool ownership by doing projects like this.
Approximate time to complete repair 20 minutes depending on experience. This also assumes you have removed the power unit from the jack frame. (4 button head bolts, a cotter pin and two springs.)
Safety
Safety glasses should be worn at all times.
The jack fluid can be reactive on skin. Use gloves if you need to.
You are working on a tool to hold heavy loads. NEVER get under a vehicle or load that is only supported by a hydraulic jack.
Tools
Paper towels or shop rags
Absorbent laminated pads (good to have around the shop anyways)
2 inch socket with breaker bar
Bench vice with soft jaws
Brake cleaner
Alcohol
Flat head Screwdriver assortment
Pipe wrench
Flashlight
File
Scraper
Needle Nose Pliers
10 mm offset wrench
Jack Fluid Can I just use ATF or Brake fluid? No, Jack fluid is a specific formulation that flows well at all temperatures. It has anti corrosion and foaming additives and will stay stable over long lifetimes. Automotive products are designed to function at higher temperatures.
I link to Amazon affiliate links as a way to earn something from the work I put in. You are more than welcome to strip them out. I also link to good tools. They cost more, but will last a long time.
Step 1: Mark Over Preasure Settings
You will see a few adjustment screws on the top. These screws adjust the maximum pressure and the over pressure of the jack. I don't have the ability to set these so I try not to mess with them. I always like to mark them so I know where they are set if I do have to open them. If you have two or three adjusting screws that are exactly the same, use unique marks for each screw. Use multiple indentations, so screw one gets one tag , screw two gets two, etc. If at all possible, do not mess with these screws.
If you do need to mess with these, you are doing so with risk of letting the jack operate beyond it's capacity.
You will not be able to get a good torque reading off of the fittings, so marking the clock position is a great way to ensure everything is back where it should be.
Step 2: Empty the Reservoir.
The jack cylinder has a reservoir jacket that needs to be emptied. in my case, it had all leaked out in my tool box so this was not an issue. As you disassemble things, doing it over an oil catch pan is a great plan. Oil will find it's way out of little passages as you remove parts. You will also have a tiny little ball that will likely end up on the ground otherwise.
Step 3: Remove the Plunger
The eclip requires removal while under tension. Grip the power unit base in the vice to act as a third hand. Press it down and use the needle nose pliers to remove the clip. Having a clean work area makes finding the clip possible.
Step 4: Rebuild the Plunger Mechanism
Once you have the spring removed, use a 10mm wrench to remove the retaining screw and clip. Back out the pressure relief valve until the threads have fully disengaged. Pull it out and clean it completely. A loose ball will be in the hole you have just opened up. if you do not intend to replace it (comes with the kit), be careful not to loose it.
A standard deep well socket will not fit onto the plunger housing. You will need to use a pipe wrench to get it off. Be careful to not scratch any of the sealing surfaces. If you do, you may render the jack unusable. Replacement parts are likely unavailable.
Using the pics, carefully remove the black o rings. Clean everything with alcohol. Only do one at a time and keep track of what order they were removed in. The white spacers need to be in a specific orientation to work. When you replace them, pre dampen them with jack fluid to aid in installation and bed in. If you do not pre oil everything seals can tear upon first installation
In the fourth picture you can see a photo of a marred housing. I used the file and scrapper to remove the burr and clean up the inside of the matting surfaces.
By taking this extra step, I am taking what was an ok jack and making it into something with much better fitment than as manufactured that will last a long time.
Step 5: Remove the Cylinder Cap
This requires some strength. It is also very dangerous. You can see from the photo it required me to push against my house in order to get it off. I was pushing on a 2 inch socket on a 3/4 inch breaker bar with 350lbs of Rob hard on it. I can't think of many better solutions than a really big wrench. Be careful, when this type of setup lets go, you can run a fist right through a window.
Step 6: Tear Down the Cylinder
You have it apart! Now we can have a look at what might have failed. In the first photo you can see what looks like a steel mesh cylinder. This is intended to be a screen to keep any fluid going into the pump fresh. looks like we might know how the jack failed. it is important to clean everything and replace this filter.
Pop the entire cylinder sleeve off and clean up the reservoir surfaces. The cleaner this goes back together, the better. The O rings provided are slightly over sized when they go back on. When you go to reassemble the cylinder, use a screwdriver to press in the O-ring so it does not squeeze out and get pinched by the wall.
For the nose, inspect surface for and burrs or marks. use the scrapper to remove them and clean the surface. Replace all O rings and make sure everything is oiled before reassembly. For the main cylinder seal, this needs to be clean and installed in the order it was removed. This little blue piece of rubber lifts a car. Treat it like your life depends on it. When installing everything back together, make sure the fill port is at the top of the power unit and accessible while installed.
Step 7: Fill and Purge
It is time to test the jack. Fill it with Jack oil and pump with the lowering valve completely open. Pump 10 times and close valve. Raise jack and lower it and repeat cycle until you have no air bubbles in the system. Refill reservoir periodically during this process. if you grab air, you will need to begin the process again. As you can see from the last picture, i have a non leaking, functioning Jack.
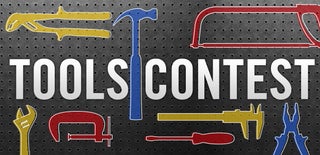
Participated in the
Tools Contest