Introduction: Reclaimed-Hardwoods Dining Table and Matching Benches
It is amazing how much excellent wood you can get for free out of things people have thrown out in their trash or dumped by the road. I made this dining table and its two matching benches almost entirely from such reclaimed wood. The only wood that was not from domestic scrap, was the beautiful decorative stripy wood. This is spalted beech. I converted this myself straight from logs from a tree, felled because it was diseased, that I had dragged out of the woods.
All the types of wood you can actually see on the table and benches are types of beautiful light and dark hardwoods like oak, beech and various unidentified tropical hardwoods that may include sapele, teak, mahogany, and Victorian Spanish cedar amongst others. There is also some pine and blockboard planks that form part of the internal structure, which you can't see.
All the reclaimed wood was salvaged from old furniture, shelves, pallets, posts, and some discarded fireplace mantlepieces. To buy the same quantity of this new could cost several hundred pounds/dollars. Some of it is not even available any more because of import rules to prevent deforestation.
I designed the structure of the table round two principles: it should be functionally practical and it needed to be something I could build just from the reclaimed wood I had available.
I developed the aesthetic design around a light and dark theme, making use of the lovely woods I had extracted from found objects. The common factor that binds it all together is the wavy contrasting stripes of the spalted beech that forms the centrepiece of the table and is also used on the drawer front, in the trim on the table base and on the legs of the bench. This is complemented by the more rigid contrasts of light and dark timber (lumber) that form the planks, posts and rails in the rest of the structure of the pieces.
You may not want to build this exact table, but there should be a few ideas you can use. I have included a separate step for all the different tasks involved in the build. I have packed in as many tips as I can about the various pieces of work, based on what I did, why I did it that way, any challenges I had and how I addressed them.
It is not a beginner's project to build something like this, but if you already have some tools and do a bit of carpentry you really can. Some of the joints here are quite fiddly, but some are nothing more than glue, screws or pegs, so there are plenty of different things you can think of using.
If you have made smaller things, you should definitely try something bigger each time and the basic table and the benches are relatively simple. The hardest part is the decorative inlay panel and mitred surrounds. You could make these much plainer or even leave them out.
Step 1: Tools Used and Possible Alternatives
The tools I actually used to make the table and its benches are listed here. These are mostly general tools with a few specialist woodworking tools. If you don't have all of these, you could definitely build the same with fewer tools. I have indicated how important each tool was and suggested alternatives where possible. Some are much more useful than others.
Hand tools
- Claw hammer - if you had to pick one hammer this is the best. You can smack nails with any hammer, but with a claw hammer, you can also remove nails when reclaiming wood, which is what I needed it for in this build when ripping apart the sofa
- Cross-pein hammer - best hammer for driving panel pins in. You can avoid hitting your fingers easier with the narrow pein (as long as you aim it between your fingers when holding the pins!) - not essential if you have another hammer
- Small ball-pein hammer - it is useful to have a small hammer to get into tight spots. I used a small ball-pein hammer but the ball-end is irrelevant as I only used the flat face. Alternatively you can use a normal hammer and a punch (even nails) - not essential
- Handsaw - In this build it was the only saw long enough to cut right through the large mantlepiece to make the bench seat boards
- Tenon saw - if you are cutting joints by hand, this is essential. They are cheap though. You could use a handsaw, but handsaws cut much less accurately than tenon saws, so you'd need to cut well wide of your markers lines and trim back
- Mortice chisel - I only used one, which was the same size as the router bit used for morticing. This was pretty handy for creating straight square ends to rounded router holes. You could get away with a single bevelled chisel, but you'd need to take more care
- Small bevel edge chisel - useful for trimming into corners of mortices
- Rubber-headed mallet - I used this for hitting the chisels, but mainly it was to help knock the joints together tightly without damaging the wood. You don't need a separate wooden hammer
- Marking gauge - dead handy, but if you have a mortice gauge, you could get away without a plain marking gauge. If you have neither, then you can use a pencil held in your hand as a guide instead. It just needs more care
- Mortice marking gauge very useful for aligning the marks accurately. If you don't have one, you can do it with a plain gauge, but it needs much more care. You can use a pencil alone too as above, which is even harder
- Large builder's try square - used to check the large frames were true and square. Pretty handy, but if you only have a general try square, that is probably good enough, unless it is really small
- Medium try square - Used for almost all joints to mark any lines across the wood. You can get away with just a mitre square as long as it is one of the adjustable sliding ones. They can be used at 45 degrees and 90 degrees
- Mitre square - pretty essential to have for the corners. If you only have one of these, that is usually enough. If you dont have any squares, then most disposable handsaws have 90 degree and 45 degree edges to their handles compared to the back of their blades
- Pencils - yep, you need pencils for marking and sketching when designing. I have a whole box of drawing pencils but you could get away with any old pencil. Having said that, just buy a woodworking pencil. they are a joy to use
- Jack plane - used to level out the tabletop. It is hard to do this with an ordinary smoothing plane. The jack plane's long base makes all the difference by riding over hills and troughs - use wax with your planes
- Jack plane (wooden) - it was really good to use my grandfather's plane. This was lovely for me, but not essential for anyone else - to be honest, the metal one is much easier to use!
- Smoothing plane - the normal size bench plane. Needed for lots of trimming jobs like trimming down the legs after gluing
- Baby plane - I LOVE this plane. It is a tiny little orange beauty that is only 3 inches long. It is so handy for trimming in tight spots. Also, because it is so small, it gives you really pinpoint control when a larger plane can accidentally catch adjacent bits of wood. Probably not essential, but if you have one, then enjoy!
- Rebate plane - This is a specialist woodworker's plane for planing in tight spaces. It will trim a joint true and square, due to its dead-square steel body. The blade is flush to both its edges. If you don't have one, you can come close to its accuracy using a large, well-sharpened mortice chisel. To do this, you use a two-handed grip, where one hand is actually pulling back as the other pushes forward. This stops it veering out of control
- Wood rasp - I used one of these to roughen up surfaces before gluing. Not essential, but it does make this job dead easy
- Artist's palette knife - used to spread glue and push paste into recesses. It's a versatile tool for these fiddly finishing jobs, but any old flat knife will do if you don't have one (butter knives are excellent for this)
Also, a lot of the subtle stuff is often done with the fingers - Old small kitchen knife - useful when you need something stiffer to spread glue/paste in tight corners. Again, not essential
- Decorator's scraper knives - with its big wide bendy blade, it was dead handy for spreading the huge amounts of glue needed when I built the table top. Not essential
- Crow bars - note, plural. If you are regularly dismantling things to extract the wood, get two. When you prise wooden pieces off other pieces, using two crowbars on opposite sides really reduces the risk of splitting the wood
- Pincers - pretty essential for reclamation tasks. There's always a nail in there somewhere. These are cheap tools and if you use them to get all the nails out, you don't mangle the much more expensive blades of your planers and routers if you hit one. If you are serious about doing woodwork and don't own pincers, don't scrimp - buy some!
- G-cramps - I used a lot of cramps. G-cramps are pretty reliable. They lack the quick-release convenience of trigger-type clamps and spring clamps, but they can apply a huge amount of pressure and they are virtually indestructable
- Spring clamps - really handy for just holding things together. Like an extra hand. They have limited pressure, but still useful
- Quick-release threaded bar-clamps - these are like a G-cramp in that they have use a screw and can apply good strong pressure, but they are much faster to put on and take off, due to the sliding head. In these pics, they have round red wooden handles. If you have no clamps already and want to buy some, these are the best type I think
- Sash Cramps - extremely useful for holding large frames together whilst gluing. They are specialist tools though and expensive if you need to buy them, especially if you need four like I did. If you don't want to buy some, an old traditional alternative is to use string and a twist stick to pull the frame together
- Bench vice - to be honest, woodworking without a vice is hard work and can be quite dangerous. If you don't have one, you will need to use clamps
- Sharpening block and strops - Your chisels and plane blades should be sharpened diligently before you start you project. It not only makes the job much easier and more accurate, it is safer as your tools cut evenly and don't snag and slip as much
- Scissors - for cutting steel wool. Not essential, although if you tear steel wool, it messes up the roll a bit
- Surface wipes - these are convenient for wiping off glue from joints, but nothing a wet rag can't do
Power tools
- Planer/Thicknesser - OK, this is the big one. On this build, almost all the wood I reclaimed was made smooth and true using it. It would have been much harder to do without it, BUT not impossible. If you don't have one, and assuming you don't know someone who has one, you have two main choices - you can choose to do all the thicknessing and smoothing with a hand plane (a power plane makes the thicknessing part much easier) OR you can choose to make something that uses the existing smoothed sides of the wood you reclaim. Doing all the planing etc is a lot more work, but is possible. Only being able to make something from what is available might seem limiting, but it can also be seen as a design limitation that encourages creativity. It also works really well if you have access to a lot of wood of the same size. (e.g. pallets, old floorboards or railway sleepers)
- Plunge router - the best tool for cutting mortices as it puts less stress on the wood than hitting it with a chisel. Routers also give an excellent smooth finish and are great for cutting rebates and grooves for tongue and groove joints. However, if you don't have one, you can use an electric drill to cut mortices if you are careful (a bench pillar drill is best, but even a hand-held portable drill will work. You need to clean the joints more, but it does the job. For rebates, you can cut these with a circular saw, so if you have one of those, you may not need to buy a router. Having said that, if you intend doing more things, then routers are excellent tools, so you should think about investing
- Portable 18v drill/drivers x 2 - Lithium ion battery-powered drills are excellent tools. If you do any sort of DIY, you probably own one (and probably should, if you don't) I have two of these. This is handy because you don't need to change bits. If you are drilling a load of pilot holes that also need countersinking, this is a real time saver. You only need one if pushed for resources
- Portable 18v impact drivers x2 - Like the screwdriving function of a drill, but way more torque. I also have two of these. This means you don't need to change screwdriver bits. This is most useful when disassembling furniture that tends to have different screw heads (flat-slot, philips, posi-drive etc). Not essential to have if you have a drill/driver (but two of those and two of these is a nice luxury)
- Random orbit sander - These are the ones that go round and oscillate. They are pretty powerful, so good for the initial coarse-grade sanding. Again, if you have a normal (and much cheaper) sheet sander, this is not essential
- Standard sheet sander - these are cheap and cheery but actually pretty handy tools. They use spring clips to hold the paper (some also have velcro bottoms) The good thing about these is you can buy whole sheets of sandpaper and cut them up. This can be cheaper than buying loads of different papers especially for sanders. (Paper is quite cheap, but money is money!)
- Circular saw - one of the most useful tools for this sort of job. The best tool for cutting single pieces lengthwise, especially with a width guide. You can use a hand saw for that, but it is much harder work for big pieces and generally not as consistent unless you are meticulous. Handsawing takes much longer. What circular saws are really good for is rebating and cutting grooves if you don't have a router. They are also good for general trimming lengths of wood
- Table saw - a big circular saw in a bench with guide rails. Great if you have one, but almost everything what you can do these can all be done with a hand circular saw. It is generally easier and safer with a table saw, but these are quite expensive things to buy, so definitely not essential
- Chainsaw - For most jobs like this, you really don't need a chainsaw. However, the spalted beech pieces that are central in the look and feel of the design were cut from logs using this. This is possible with a handsaw, but blimey - I wouldn't want to do that. It is extremely hard work with a handsaw and would take ages
- Multi-tool - I used this with a saw attachment to trim down overlapping pieces of wood. Not at all essential, but these are really good for fine trimming.
Protective clothing
It's best to consider protective clothing as a tool. Luckily, you don't need much for wood working...
- Protective glasses - These are essential when you use any form of power tool, but especially circular saws, routers and planers. Oak chips are sharp and really hard. If you get hit directly in the eye with even a small one of those and it is serious
- Ear protection - you need these for the louder tools. I actually don't use ear defenders. I use over the ear bluetooth headphones. That way, you can listen to music and tell when messages come in.
- Dust protection - this is really only needed when using routers, power saws and especially sanders indoors. If you are outside, it's not so important as the dust tends to blow away. You still need eye and ear protection though.
Transportation
If you are aiming to gather scrap stuff for reclaiming wood, you need to get it home. The first rule is "grab it when you see it". If you don't pick waste wood up immediately, it's often gone when you come back later.
- Car - a bit obvious, but some things like sofas need a vehicle. This doesn't need to be your own though :)
- Bicycle - You can move really big bits of wood, especially long pieces, quite easily on a standard bike. Quick and easy and you don't need to worry about parking
- Sack trolley - I have been known to take one of these out to pick up things in the street for recycling. You can attach them to your bike too.
- Parcel tape and plastic bags - these are useful light things to make handles and pad corners with, so that you can pick up wood. Parcel tape is the cheapest strong tape
- Legs - quite a lot of stuff can be carried. keeps you fit too
Step 2: Materials List - All Reclaimed Woods From Various Sources
All reclaimed
The woods used in this build were all sourced from scavenged, salvaged wood. They come from old furniture, bookshelves, post, pallets, mantlepieces, and in one case, some foraged part-rotting logs that I successfully converted into the much sought-after stripy spalted beech. That felt good.
All the wood you can see externally on the finished table and benches is lovely hardwood. Some was nearly 140 years old as it was salvaged from a broken door of a Victorian specimen cupboard from the Natural History Museum in London. Some softwoods were used but you can't see them as they are only used internally.
Materials listed
- One english oak mantlepiece beam of more than six foot in length used for the four table legs and the lightest of the table top mitred trim. This is really hard and heavy.
- Two mahogany (or mahogany-like wood like sapele) mantlepiece beams that were even bigger used in the outer planks of the table, for the bench seats and the main central core of the bench legs. One of them weighed more than 24 stone and was seven foot in length, eight inches in width and nearly three inches thick. I got that home on my pushbike!
- Spalted beech (beech with nice fungal discolouration), which I found as logs and ripped into planks with a chainsaw and seasoned for 8 months. This is the tigery stuff, used for the central decorative panel on the table top, the end-cladding on the bench legs, the drawer fronts and as an inlay in the table base cross-rails.
- A damaged vintage cupboard door. This was from an old broken specimen cupboard salvaged from the Natural History Museum, London. The wood may be something called Spanish cedar (Cedrela odorata), which is a hardwood similar to mahogany with an incredible play-doh like smell. This apparently repels insects. It was used for the inner broad dark framing round the central decorative panel on the table-top, for all the drawer frames and the upper cross-rails of the bench leg-pillars
- An unknown light tropical hardwood from the wooden frame of an old sofa used for the central rails of the lower I-brace of the table frame that gives the legs stability and for the lower cross-rails of the bench leg-pillars
- Some dense dark hardwood planks from a broken garden bench, possibly teak. These were used for the cross-rails of the I-brace and for the drawer front frames which the drawers fit into.
- Another type of unidentified light-coloured tropical hardwood from an old post that previously was used to hold up a rope barrier for controlling queues in a pub.
- Some common beech from the same sofa frame used for the lengthwise cantilever braces that stabilise the joint between the bench seat-planks and the bench leg-pillars
- Some oak-faced plywood from the back-panel of an old bookcase used for the drawer bottom panels
- Some blockboard panels from old library shelves used for the main supporting bed of the central table-top panel (these are softwood lengths bound in veneer and are the only wood not visible)
- Some 4" by 1.5" softwood baulks, that were reclaimed from old pallets. These were used for the internal carcassing frame that forms the drawer compartments in the table base.
- There are also some reclaimed beech dowels from old IKEA furniture used for strengthening the butt joints between blockboard panels in the table bed and to anchor the bench leg-pillars into the seating plank
Step 3: How Raw Logs Were Converted Into Spalted Beech Timber (lumber)
The beautiful stripy wood in the middle of the table-top, on the drawer fronts and the bench legs is spalted beech. The contrasting light and dark veining is created by fungal colonisation of the fallen logs. As the fungus grows through the log, it changes its colour. I believe the very dark regions are the boundaries of a fungal colony and that there may be more than one type of fungus in different parts of the log. You can see the white bloom of fungus on the end.
Apparently spalting can occur in various woods, but it is most common in beech. The planks were cut from logs from a felled tree, that I found while walking the dog.
I don't have a bandsaw for ripping logs, so I cut these planks by eye, using a chainsaw. Obviously, chainsaws are dangerous tools, so protection is essential. I use a helmet with face-guard, ear defenders, gloves and leather apron for safety (although bare arms are possibly not the recommended level of protection for using a chainsaw)
I used a cheap electric chainsaw. It's nothing fancy, but it is good enough for the occasional use I give it. Being electric, you can use it indoors inside the shed without worrying about fumes or storing petrol etc.
When I sawed down this log, it had been standing in the woods for at least a year, possibly longer. It was very wet. The cut planks were stacked with spacers and left to season (dry out and stabilise) outside. They were covered to prevent rain getting on them, but open to the air to allow them to dry out. You just need to forget about them for months. I think it was about 6-8 months between ripping down with the chainsaw and using as timber.
I cut the planks deliberately thick, because when I cut them, because I wasn't exactly sure what I was going to use them for. At that time, I hadn't decided to build a table. This turned out to be useful as I could cut them in different ways.
As they dried, they curled a bit. Later, when I used them, I ripped them down with a circular saw and planed them square. You need to leave them a bit between sawing and planing because they curl a bit more as the moisture in them stabilises and the various shrinkages inside the planks create warping forces. Really, you should bring the wood into the final place it will be used and leave it for a while before planing.
Step 4: How Timber Was Salvaged From Discarded Furniture and Other Things, and Prepared
What is not to love about salvaging and reclaiming materials?
It's free wood. In this case most of it was free hardwood and that is really expensive if you have to buy it. Some of it was wood that you can't even buy at all anymore because of import restrictions that prevent tropical deforestation (quite right, too). Building new things out of old materials is proper recycling.
All the wood in this build was reclaimed from defunct, discarded and otherwise unwanted things. To find decent wood, the most important thing is to keep an eye out for scavengings at all times, and to pick things up quick if you see them. I frequently have to grab things and strap them to my bike to move them before someone else spots them! It is surprising what you can transport by bike. The heaviest was a 24-stone mantlepiece strapped to my poor folding bike. You could barely lift it, but once on the bike, all it needed was effort and balance, and a general lack of embarrassment at tootling along with a massive plank strapped to a tiny bike.
There's a load of stuff that contains wood that can be used. The real art here is see the objects around you not as what they are currently used for, but look for what they are constructed from. I use the old creativity trick of ignoring an object's name, and describing its components instead. A sofa is not a sofa - its a load of cheap softwood, occasionally some great hardwood, some screws, some foam rubber, wadding and maybe some usable leather. The wood you want will need to be extracted from its current state, which might be decorative, curved, stained, dirty, massively thick or whatever.
I was lucky on this build, in finding three mantlepieces. One was oak and two were dark hardwood (sapele, probably). They were long, wide and thick, so they could be cut lengthways into wide planks (for the bench seats), into chunky baulks (for the table and bench legs) and into long thin strips (for the main mitred table framing bezel and inserts round the decorative panel on the table top).
In general, extraction usually involves ripping pieces down lengthwise using a circular saw. I either use the table saw or a hand-held circular saw. I then size them to consistent thickness and smooth them with the planer thicknesser. Almost all of the exterior visible wood is prepared this way.
For example, I found a severely broken garden bench, which looked like crap, but was actually just very dirty, weathered hardwood, quite possibly farmed teak. Once cleaned up the wood was top-notch. Really hard and with a beautiful even dark grain. It was not very thick, but was just right to form the framing rails that contain the drawer openings. I got lucky with this bench as it was held together with screws. This is the easiest, because not only is it easy to dismantle, but you know all the metal has been removed. This is important when you plane it later.
I also found a particularly unfashionable sofa which looked pretty ugly aesthetically, but once sawn down, yielded several long tropical pieces that I incorporated into the I-base that braces the table legs. I had to join the two pieces lengthwise to form a single long thick beam. Pulling the sofa pieces apart was more difficult because the frame had been constructed using metal staples, not screws. These are quite fiddly to remove. You can split the wood if you wrench them out in the wrong direction too. Also, you have to be sure you have got all the staples. If you leave a bit of metal in, it will totally knacker your plane blade. This gets harder if the staples or nails are rusty as they often snap off leaving the ends still in the wood.
The big mantlepieces were so wide, I couldn't cut right through them with the power saws, so I had to complete the cut with a hand saw. That took about 40 minutes for the really big mantlepiece and was pretty exhausting.
The other major source of goodness was the old museum specimen cabinet. This was really good Victorian hardwood. I had to cut out the splintered pieces from where it was broken, but there was still a load left that could be used. This was used on the table-top and for all the drawer sides.
Some wood you find doesn't need converting. The library shelves that formed the hidden bed of the table top needed no cutting or planing. They just needed joining together with dowelled butt joints to form a single broad piece. Similarly, the oak-faced plywood used in the drawers simply needed cutting to size, to fit the recess in the drawer frames.
Step 5: Researching Old Furniture for Ideas
It's always a good idea to see all the ways other people have solve a problem before trying it yourself (this is what Instructables is all about after all...)
Before making this dining set, I spent a good few hours wandering round the V&A (Victoria and Albert Museum, London) which is an art and design Museum and has a shed-load of great furniture in it. This varies from 20th century classics to medieval refectory tables, from Arts and Crafts pieces to the functional classic designs for the house of parliament seating.
I was trying to expand my possible options for a few things:
- aesthetic look. I like weathered, used furniture that has the mark of living on it, but everything starts new sometimes. I was always going for something fairly simple as the main decorative look was from the swirls and curves of the spalted beech.
- the best way to create a strong base. There are lots of ways you can support a table. Legs obviously, but also pedestals, columns, boxes, etc. I wanted legs and could have had freestanding legs or rails between each leg, but decided eventually on the fairly minimal I-frame bracing because it allow you to freely out a chair under the table if you ever needed to. It also gives you a foot rest in the middle. and is slightly lighter.
- comfort. You can't sit on museum objects, but museums have a whole load of public benches to use that gave me an idea of what works
If you can't get to London, their collections website is one of the best so you can browse design ideas there any time. Here's what they have just on benches for example...
http://collections.vam.ac.uk/search/?q=bench
Step 6: Using Drawing and Photoshop to Develop the Construction and Panel Design
When I make anything complex, I always spend at least a few weeks thinking it through and a big help with this is drawing out ideas. Ultimately, I work by developing the concept by exploring out possible variations until I get close to what I like. At that point I spend a fair amount of time drawing the ideas out. For me, this burns a mental picture in my mind, that I can use like a plan. Once you can see the finished object in your mind, you can use it to work towards. It always works for me.
And just to show that these don't need to be works of art, here are some of my working scribbles, that I used to visualise possible solutions for this build. It is about exploring ideas, not perfection.
The method of using exploratory drawing to capture some of the possibilities of what does not yet exist is very powerful. Sooner or later you can see the right future that you want to make. I usually draw roughly at first and and deliberately get a bit random to break up any pre-existing ideas of what something should look like. After while, the thing that works will emerge from the random variations.
Once I know what I want, I draw a few more detailed drawings of it until I can see it clearly in my mind. After that, it's fairly easy to make something without any plans. It's definitely worth trying this - you can see what you haven't yet built.
I also took photos of the spalted beech planks and the beech bezel and used Photoshop to try out different ways to arrange and colour them. This is a quick way to mock up something close to what the actual object might look like.
Step 7: Building the Basic Table-top Outer Frame and Inner Bed
The table-top was, by far, the most complicated piece of work in this project. The first thing I needed to do was build a really solid base-frame to which all the more decorative woodworking could be added.
In simple terms, the table bed is made from a strong frame of broad, thick planks about 4" wide and just under an inch thick, forming an outer rectangle. These have really strong blind mitred mortice and tenon joints at each corner. Inside the outer frame, there is a solid bed of blockboard planks, locked in place with a tongue and groove joint all round he edges.
Outer frame
The frame joints are mitred blind mortice and tenon joints, and were quite fiddly to make. The first step is to mark the mitres on all four corners. When you do this, it is a good idea to mark the two pieces that are joining. Although the joints are the same, there can be slight difference in position when cutting the mortices. This can be due to minute shifts in the router path or how the mortice is trimmed with the chisel. The same applies to the tenons. The two halves of each corner once cut, should be treated as unique to that joint. It just makes it easier
For each corner, the mitre that will contain the mortice is cut right across the diagonally marked mitre line.
NOTE - do not cut across the whole mitre for the ends that will contain the tenons! .
This mortice side of the joint is always cut first. To cut the mortice, it is worth clamping another piece of wood to the rail being cut, so that the surface the router will sit on is wider. This makes it much more stable and you don't get wobble, which can distort the trueness of the interior angle of the mortice.
Once the mortice had been marked, each one was cut using the plunge action of the router. When you do this, don't attempt to cut into the mortice by starting on the edge and moving it horizontally into the rail. This tends to cause the router to catch and can split the grain. A plunge close to the inner edge of the mitre is best. Once that is made, you can route outwards more easily. As ever, don't attempt to cut exactly to the marked line with the router. It is better to cut close to it and trim it accurately later with the chisel
Once the mortices were cut, the tenons marks were checked for alignment and and adjusted if needed. To cut the tenons, the saw cuts are again not made all the way through, but almost through. This leaves a little extra waste in the corners that can be accurately rimmed with the chisel. The tenon is trimmed in width at the outer end of the mitre end, so that it would fit into the blind mortice. This trimming should be done in small passes, checking the fit each time until it just fits. The trueness of each joint should also be checked as you trim, as you can sometimes get tiny shifts from 90 degrees in the mortice vertical alignment. You can trim either the mortice or the tenon to adjust for these as you clean up the joint. until you get a good true joint.
Once all four joints had been made, the frame was rigid enough to hold its shape without glue, from the friction alone. It was useful to be able to put the frame together so I could can mark out where the boards needed to be positioned when building the table bed that sits inside it. I was then still able to disassemble it, to mark out the recesses for the internal tongue and groove joints that would lock the boards in place. This recess was also cut out with the router while the frame pieces were separated.
Inner bed
The main table bed was made from good strong blockboard planks which used to be library shelves. They were fixed together with simple dowel-reinforced butt joints. For this, each plank was drilled with two 10mm holes to take the dowelling rods. It is essential to mark the positions of these holes accurately or the planks don't line up true.
Marking the dowel holes should be done by lining the two planks together face to face, making sure the planks are aligned at the ends and clamping them together, before using a try square across both boards.
Marking how far from the edge the holes should be, was done with a gauge.This should be in the centre, but it doesn't have to be dead centre. You just need to make sure that when you mark the boards, the gauge is run along what will be the upper face of each board, NOT the bottom face. This is because boards can vary slightly in thickness. If you mark all board on the face side, then when you attach them with the dowels, the face will be perfectly in line, even if the underside may have slight steps between any boards of different thickness.
Before gluing, the edges of the boards were scored to roughen them, to increase the purchase for the glue.
After the boards were joined, the reassembled frame was laid over them, so that the inner edges of the frame could be used as a template to mark where to cut the tongues that would later fit into the grooves already cut in the inner edge of the frame . The tongues were cut along the jointed board with a router. As with tenons, these were cut slightly too thick so they could trimmed down for a good tight fit. This was done with a small rebate plane.
Step 8: Building the Table's Central Decorative Panel in Spalted Beech
The spalted beech panel is central to the overall aesthetic feel of the table and benches. This lovely stripy wood has a beautiful zebra-like pattern to it, which really comes out when finished and polished later.
The reason it is stripy is because of fungal colonisation of the felled log from which it is made. It may look lovely, but the fungus will have started to feed on the wood and in doing so, the structure of the wood gets compromised. This means the timber produced can vary in softness in different parts of the board. Also, I converted this timber myself by simple air-seasoning, which is a slightly unpredictable process (especially when you haven't done it before!)
Basically this wood is beautiful, but was unpredictable to work with.
The biggest concern I had was making sure the boards could be reliably fixed to the base without coming off. As a precaution, I brought the seasoned planks into a warm place for about a month to make sure they had shrunk as much as they were going to. Even so I decided that glue alone was probably not enough and so I decided to use cut tongues into the ends of the boards to lock them into a recessed groove in the surrounding decorative mitred inner frame that they sit in.
The mitred panel frame was made using relatively simple mitred lap joints. These had an inner groove cut to take the tongues of the spalted beech planks. Because the beech was not consistently strong along its width, tongues cut into it would have been too fragile. Because of this, I cut recesses in the ends of each planks and glued in inserts of much harder stable woods to form the tongues. By having a strong edge, the likelihood of the boards curling across their width was also reduced. The beech planks are not joined on their long edges. They were just carefully planed so they fitted tightly. Any minor gaps would be filled later.
The panel frame was made of a similar wood to the strong main outer frame. For contrast, a separate oak frame was fitted, also using mitred lap joints. This gave the mitred frames an alternate dark-light-dark design, that mirrors the more curvy light and dark contrasts of the stripes in the spalted beech. This allowed the more formal square outer frame pieces to blend into the decorative style.
Step 9: Installing and Gluing the Central Decorative Panel Into the Table Bed Recess
After all the inner frames had been cut and I'd tested that there was a good fit, it was time to glue them all in place. This is always a slightly daunting job. Once things are glued, it's not easily to fix stuff if anything isn't quite right. This why you dry test it. Once you have the parts ready, you just have to go for it.
Before gluing, the upper face of the table bed was scored quite deeply, using a wood rasp, to roughen up the smooth surface of the planks, so the glue could get into the wood fibres.
Gluing all the various frames in place was quite a fiddly job and used a surprisingly large amount of glue. The frames were glued from the outside inwards. Each new inner frame was tapped back into the previous one with the rubber mallet and a piece of waste wood, to get a good butt up against it. The final frame containing the spalted beech was glued together as a unit first, then levered into the surrounding frame. I had deliberately not glued this panel separately and let it set, because it was easier to fit all the pieces in, while the glue was wet. This allowed me to use the mallet/waste-wood to tap the pieces to adjust them to get the best alignment.
Once all the pieces were in place, the next step was to wipe off the excessive glue. I used kitchen surface-cleaning wipes for this. They are great as they are ready wetted and slightly soapy. The only thing you need to watch is that any rough ends of grain can snag in the fibres in them. The boards here were all pretty smooth, so that wasn't a problem.
Finally, the glued boards were all clamped down against the bed to make sure the glue was fully in contact with both surfaces. This was achieved using long pieces of wood to spread the pressure out evenly. I used pieces of waste beech between the table surface and the clamp heads, to avoid denting the surface of the beech, which is quite soft in places.
The whole rig was left for about a week to make sure all the glue would be set.
Step 10: Levelling the Table Top Using Hand Planes
Once the table-top was fully assembled into one piece, it needed to be smoothed off. Even though the various individual components had been planed, the composite surface was by no means level. To get it good and flat and level, I planed it. Before I did this, I left it to set for several days, so the glue would be properly set and any movement or shrinking of woods was stabilised.
Before starting the planing, I took the cutting blades out of the planes and gave them a thorough sharpening. This doesn't take long, but makes planing much easier.
The levelling was done by first using a straight edge to see where areas sit higher than others. I used three planes for this. One of which is the lovely long wooden jack plane. This belonged to by grandfather. The only problem with this, is that the blade can come loose and it is quite hard to adjust. I decided to swap over to the more modern metal jack plane, which belonged to my father. This was much easier.
One very useful tip when planing a table top is to rub some wax onto it from a candle. The plane flies over the wood after you've done this. It makes a huge difference.
I planed the beech across the grain diagonally in two directions. You get a more even cut cutting across the grain and varying the angle helps keep it even. After a lot of planing down, the top was more or less level. At this point, I swapped over to the smaller smoothing plane to finish off. This has a finer finish.
Planing a surface smooth is a really satisfying job. You really have to feel the wood as well as eye it up. Wood is such a lovely tactile material.
Step 11: Filling in Gaps, Cracks and Holes in the Table Top and Sanding
The last job to do to finish the table-top was to fill in any gaps, cracks and holes. For this, I used two types of filler paste. Both were made from sawdust mixed with glue. This is a simple recipe for making your own filler, which is not only free, but because you use the sawdust from the wood you have used, it is easier to match colours.
I normally use PVA as the glue binder, although I also discovered that builder's caulk is excellent for this, because when it dries, it remains more flexible. I used three blades for this job: a small bendy pallet knife, a slightly more rigid old kitchen knife and a decorators wide scraper knife - the type normally used to remove paint and wallpaper.
In most cases the holes needed a fine filler, which is best made from the dust that comes off after sanding. In one or two places there were gaps which were a little deeper and for this I used a slightly coarser sawdust, mainly because it is more fibrey and is a bit stronger across the wider gap.
Once filled, I left the filler to almost dry before scraping off any excess, then left it a few days to dry out fully before sanding smooth.
When sanding the top, I started with a coarse 40 grit paper to even out the surface. This works, but was a bit savage, so I needed to use several other increasingly finer grades of paper to progressively smooth out the coarse sanding of the last paper. Eventually I got it down to a fine 240 grit paper, which leaves a good smooth finish.
Step 12: Building the Table Base Frame and Supporting Legs
Once the table-top had been built, it needed a base.
The exact design needed some thought because the table has drawers. This is more complicated to build. Normally for a table without drawers, making the base would have been a pretty straightforward task of cutting four legs and joining them with strong rails along the ends and sides using mortice and tenons. Obviously, the sides in this case needed to have openings for drawers. The solution here balances strength and rigidity against having drawer-surrounds thin enough to maximise the size and therefore capacity of the drawers.
All the parts for the base were cut and assembled without glue initially. The joints were strong enough to hold it in place without the glue. This allowed the base to be part-assembled to calculate the dimensions and mark the positions of the inner drawer-frame and then take it apart to cut new mortices to fit it, before final assembly.
Essentially, the base is formed of two end-frames that are joined by cross rails . At the top, the rails house the frame for the drawer compartments. At the bottom, an I-frame braces the legs for stability.
Building the base end-frames
The two end frames are incredibly strong and carry all the weight of the table. They are braced with strong cross-rails at the very top and close to the bottom of the leg, using shouldered mortice and tenons. I used oak for the legs. It is extremely strong and using it allowed me to have legs that were more than rigid enough, yet not hugely thick. The legs were made by sawing down an oak mantlepiece. They are about 2" by 2.5" (or about 50mm by 65mm).
The top rails were cut from a thick post that used to hold a rope barrier from a pub. The wood is an unknown type of light-coloured, fine-grained hardwood. I have no idea what type it is. These rails are about 1" thick by 3" high (or about 25mm by 75mm) so are really strong.
The lower rails are more complex. Each is a composite made from three separate pieces. The main bulk of each lower rail is made from two thinner sections joined lengthways. The wood for these came from the slats of a wooden garden bench which were about 1/2" thick. The wood is teak or similar. The individual slats were quite strong. Gluing two together gave the required thickness and is actually stronger than using one single thicker piece.
To hide the central glued joint, a recess was routed into the middle of the top and a thin slat of wood inserted to cover it. For this, I used the same decorative spalted beech that is used in the centre of the table-top. This ties the base into the overall colour and pattern design that flows across the table-top, drawers and benches . It's a subtle detail, but it really works.
Joining the end-frames with the side rails
Once the two end-frames were built, they were joined together using pairs of long, thin rails that form the tops and bottoms of the drawer openings. Originally I had considered having drawers on the ends as well as the sides, but I decided to keep them together along the sides. Because the long rails on the sides of the base needed to thin, they were a bit bendy when first assembled. The rails act as the outer face of the drawer fronts and although they also tie the end-frames together, they are not strong enough on their own to provide the rigidity needed. What gives the rails their real strength and rigidity is the central drawer housing frame.
The central internal drawer frame and boxing
The drawers sit inside compartments form from a central housing frame. This was built from fairly solid pieces of softwood, reclaimed from pallets. It has a central solid rail that is jointed into the inner face of the end-frame top-rails, using mortice and tenon joints for strength. This forms the back of the drawer compartments and also further strengthens the support for the table top by spreading the load along its length. The sides of the compartments use shorter pieces of the same softwood.
At the outer end, these shorter rails fit exactly between the thin upper and lower side-rails. At this end, they are fixed onto the long table side-rails by simply gluing and securing with screws top and bottom.
On the inner end, they are joined into the central rail slightly differently on each side of the table.
On one side, the rails were connected as a T-joint to the central rail by simply gluing and screwing through the central rail into the shorter side-rails. On the other side of the table, it was not possible to fix the side rails to the central rail using screws, because of the rail on the opposite side. In this case, dowel joints were used to connect them to the central rail instead.
Later on, plywood panels were fitted to the underside of the drawer frame to complete the boxing of the drawer compartments. This was not done until assembly.
Step 13: Gluing and Assembling the Table Base
The final assembly of the base-unit was quite a fiddly task.
I started by gluing and assembling the leg-frames together as units, using sash cramps to keep them tightly together while the glue dried. These were quite tight already for dry-assembly, but clamping is required when gluing.
After the end-frames were put together, I glued and fitted the various cross-rails to link them - the lower lengthwise leg-brace, the upper drawer-frame central lengthwise brace and the four lengthwise side-rails that form the top and bottoms of the drawer openings.
Finally the drawer frame divider rails were fitted in. These were fitted at the inner end first. The first pair along one side were glued as T-joints and screwed in place through the central frame rail. The second pair on the other side were fitted in line with them using dowel joints (they couldn't be screwed in due to the opposite rails getting in the way). The outer ends were then attached to the thin side-rails, by gluing and screwing in place with screws top and bottom.
In all cases, you should drill pilot holes for the screws and countersink your screw holes. You can sometimes get away with this in softwoods, but if you don't do this properly in hardwoods, you will just split the wood.
While setting, I also used clamps to hold in the open mortice joints on the side rails and long sash cramps to hold the central rails in.
The whole frame was then left to dry for a few days.
After the frame was dried, I attached the underlying plywood base beneath the drawer compartment rails to complete the boxing in. These were screwed in place with the table base upside down. (needs pics)
Step 14: Building the Drawers
The drawers were made as plain box trays first, without any decorative fronts, which were added later. The front, back and sides of the box frames were made from a Victorian museum cupboard door. They have oak-faced plywood bases from an old bookcase. When worked, the framing wood had a lovely, sweet fragrant scent, not unlike Play-doh. I believe it may be Spanish Cedar (not really a cedar at all). This is a wood traditionally used for cupboards because it is insect repellent.
Drawer construction
The drawer frame is made from four reasonably solid planks (about 1/2" thick or just over) of the fragrant wood. Each of these had a recess routed on its bottom edge on the inner side to fit the plywood base.
The drawers are joined with simple glue-and-screw joints to connect the front and back faces to the sides. The front face is recessed to take the side rail. This adds a little bit more strength as it means the glue is holding the joint on the ends and the sides. To be honest, the screws alone were more than thick enough to hold these drawers together, but the glue makes them even stronger.
On the back, the back face of the drawer uses an even simpler 90 degree butt joint. Again these were simply glued and screwed together. As with all screw-fixings on this build, countersunk pilot holes were drilled first to avoid splitting the wood.
Once the drawer frames were fitted together, the plywood bases were measured for each. This was done individually, to make sure each base was the exact size for its frame. This is important because it allows you to cut them so they fit really tightly into the recess on the bottom of the frame. This makes the join much stronger.
To do this, each board was cut slightly too wide and then trimmed back to the right size, by trial and error, using a hand plane. If you get this right, a snug fit can be achieved so that the board will hold in place by friction alone.
Once the board was completed for each drawer frame, it was fixed by gluing and then nailing into the recess using panel pins. A handy tip is to tap the pins in at different diagonals, so that they form a slightly more claw-like grip. The combination of a tight fit, glue and angled pins makes for a surprisingly strong joint
Fitting the decorative drawer fronts and handles
Once the drawers were complete, they fitted nicely into the drawer compartments, but of course they had no fronts. To continue the overall look-and-feel design the drawer fronts were made from the same stripy spalted beech planks used on the table top, table lower rail trims and the bench leg-pillars.
The drawer fronts are one of the highlights decorative of the table. Some considerable thought was put into choosing and cutting the planks so that a continuous curvy swirl pattern could be lined up across all three drawer fronts on each side.
The planks were first cut roughly to size for the pattern, then checked and trimmed with the plane for the exact fit. This was done without the drawers attached. This allowed them to be exactly lined up and cut to the perfect size.
Finally, once the faces were all complete, each one was fitted by putting its drawer into the right drawer-compartment and then lining up the drawer front in the right position. Clamps were then used to hold it in position while attaching it. This was done with screws from the inner side of the front of the drawer frame..
Once the fronts were fitted, the clamps were removed and handles could be attached. A ruler was used to make sure each hole was exactly in the middle of the draw front, vertically and horizontally.
Step 15: Making the Bench Planks by Ripping Down a Huge Mantlepiece
The two benches were made from one humongous mantlepiece. My scales weighed it in at 24 stone, but I can't be sure they were accurate as they were only bathroom scales. It was about 7 foot long (2100mm) at least 8" wide (215 mm) and nearly 3" thick (65mm).
The bench seats only needed to be the same length as the table-top which is 1600mm (just over 5 foot 2"), so the first job was to cut it to length using a circular saw. The remaining 500mm long block was used later to make the bench legs.
The next job was to saw the big piece in two lengthways, through the middle of its thinnest face. This was hard work. I started by sawing as far as I could on both sides using a table saw. The piece was so wide though that this still left a lot of wood in the middle to saw through to separate the two pieces. I had to cut this by hand. This took about 40 minutes and was exhausting. Rip-sawing down the grain is always hard work and the heavy wood made this harder still.
Eventually, I sawed it through. The two planks are very slightly different thicknesses, which doesn't matter as the benches sit on opposite sides of the table in use. They also had a load of saw marks. I planed these off using the planer thicknesser.
The two planks are really solid and could easily support three people's weight.
Step 16: Building the Benches
Structural design
The benches are relatively simple in structural design. Each one is really just a big heavy plank supported by two leg pillars. Each pillar has two thick, composite legs about 50mm (2") square in section and just under 500mm (20") high. These are joined with a tall, stout rail at the top for strength and a smaller rail at the bottom to tie the lower ends of the legs strongly together, whist appearing quite delicate.
The pillars are quite close to the ends to give a sense of width. I decided not to place them right at the end, to reduce the total span of the central section. This was to ensure that it would be strong enough to cope with three heavy people all sitting on a bench at the same time.
As well as setting the legs in lightly from the ends, each bench is further strengthened on each leg pillar with an inverted triangular buttress locked into it that runs along the underneath bench seat towards the middle. These two extra supports distribute the weight along the plank in the middle making are deceptively strong.
When three people are sitting on a bench, most of the weight of the outer two people is balanced across the section of plank immediately above the the leg pillar putting very little bending stress on the plank. In fact the greatest bending stress that is likely to be placed on a bench is when two people are sitting together in the middle of the bench. Even then, the planks are quite a dense hardwood and are more than an inch thick. They are more than strong enough.
The leg pillars were attached to the seat planks on the underside of each bench using dowel joints and screws. There is a dowel fitted into the top of each leg in the pillar to a corresponding hole drilled in the bench to lock it in position. Finally, brace was also glued along its top edge and locked on with a fairly large-gauge screw. As always, countersunk pilot holes were drilled to make sure the screw didn't split the brace.
Decorative design
The dark and light design of the table is carried over onto the benches. The legs are made up from a central core of the same dark wood as the bench planks. Attached to these are some quite thick facing-pieces made from the stripy spalted beech. The legs are bonded as pairs into pillars using stout rails between them. These cropss-bracing rails are from a lighter wood to contrast with the dark core and the bench top, and continue the mix of square contrasts alongside the curvy striped contrast of the beech.
The cores of the legs were ripped down from the remaining block off-cut left over when the mantlepiece was cut down in length before ripping down the long block to make the bench planks. This shorter block was cut into halves, which were then halved again twice to form eight lengths of 50mm (2") by about 25mm (1"). The spalted beech planks were planed to about 12.5 mm (1/2"). Because each leg has two facing plates on opposite ends of the core, this made them up to the full 50mm by 50mm square section.
The pieces of beech were carefully chosen so that the two outer facing pieces on each leg pillar complimented each other. There were 16 pieces to face the 8 leg cores. These were not cut to fit in width. Instead, each face plate was cut wider than its core and trimmed back with a hand plane, after gluing.
The face plates were attached to the cores simply with glue. The 8 legs were assembled and glued at the same time and all 8 were clamped under a medium pressure at the same time between three long sash cramps.
The legs were left for a few days to set properly, then the beech was planed back on each side of each leg until they were nice and flush.
Once the legs were made, the leg pillars were made by simply jointing in the top and bottom bracing rails. Into each rail, the triangular under-brace was also locked in with a mortice and tenon joint. You can see the component parts of one leg brace in one of the photos
Step 17: Sanding, Finishing and French Polishing
Throughout the build, each component part had been sanded smooth using progressively finer grades of paper. In many cases the faces had been planed to size with the planer thicknesser and this leaves surfaces pretty smooth anyway. Planed surfaces usually needed nothing more than final fine-sanding with 240 grit and 400 grit papers.
Once all the surfaces had been prepared, the table was finished with French Polish. This is a beautiful rich-coloured natural polymer (shellac) produced by insects. It has a lovely transparent chestnut-brown colour. This overall coloured coating blends the various light and dark woods into one flowing range of contrasts with a lovely shared ochre hue.
French Polish is extremely fast drying, so you need to be quick when you apply it. You can't use too much at once or it will set hard in streaks and pools before you have finished. It is used in nail varnish and doesn't easily come off your hands. I use a 2" paintbrush and apply small amounts at a time making sure the polish is brushed out evenly each time. Although it can be tricky applying something so fast-drying, it also means you can apply another coat in about 15 -20 minutes after the last one.
I usually let it dry longer and between each coat, lightly smooth it with fine steel wool. This gets rid of any bumps from pooling or dust that has landed on the wet coat. You should use your fingertips to feel for bumps, it just look for them. You always can feel them. Imagine you are a diner feeling the table or bench. You should be able to run your hand over it anywhere and it to feel like one smooth surface with no catching.
I used four coats on the table and this is more than enough to give a super fine smooth finish. For brush cleaning, use methylated spirits.
Step 18: Joints Used in This Build and How to Make Them
In this Instructable, I have not attempted to give a master guide on woodworking techniques including woodworking joints. I wanted to show that you can combine basic non-technically advanced processes (like screwing and gluing with more advanced jointing (e.g. blind mitred morticing) AT THE LEVEL YOU FEEL COMFORTABLE WITH. It's always good to push yourself, but you can make good stuff without perfecting every aspect of your technique. In that spirit, here's some tips on the joints used here which might be useful to think about.
Mortice and tenon joints - general hints
A very common and fairly simple joint but super-strong joint. It is used to connect the end of one piece of wood somewhere into the middle of the side of another length of wood.
This joint is basically formed with a rectangular hole (the mortice) in one of the pieces of wood to be joined and a matching rectangular piece (the tenon) cut onto the end of the other one. There are several variations used here.
Cut the mortices first
In all cases, the mortice is ALWAYS cut first. This is because the width is determined by the cutting tools available. Traditionally, the mortice width is determined by the width of the mortice chisel available. All the mortices here were cut with a router though. Because it uses a rotary cutter, the router leaves the mortices with round ends. These are squared off by trimming by hand, using chisels.
It is best not to mark your mortices one at a time, but do several together. I marked each end-pair of legs together for the table. You can mark all four at the same time. The marks that cross at 90 degrees to the wood are done with a square. The marks that go lengthwise are made with a mortice gauge. This is a marking gauge with two pins.
When you cut mortices with a router, it is best to do a similar thing and have at least two clamped together. Firstly, the extra width means the router base is more stable and doesn't wobble. With routers you can also use a clamp as a stop to control how far it can travel along the cutting direction. This stops it overshooting the marking. By clamping two legs together, you can use the same stop for cutting more than one mortice. This saves time and makes it easier to be consistent.
Cut the tenons over-sized and trim down
Once mortices are cut, the tenons are cut to match. To mark them lengthwise, the end of the piece is aligned against the mortice and marked with a pencil. Then using the hand as a gauge, the pencil is run down the wood to mark where to cut.
The tenons were cut with a hand tenon saw, which is fine-toothed and braced so it doesn't flex. To cut tenons by hand, you cut each end at a diagonal, then make a connect cut to complete. This keeps it accurate. When cutting, ALWAYS cut on the outside of the marks. Do not try to use the saw to cut the tenon accurately. You cut it too fat and trim it down to fit the mortice with a chisel. This makes sure you get a really tight fit.
Plain mortice and tenon joint
This is the simplest type of mortice and tenon joint. The tenon is only cut along the two wider edges of the piece. Here this is only used for the benches to lock in the lower cross rails of the leg pillars.
Shouldered mortice and tenon joint
The shouldered mortice and tenon is the same as the plain mortice and tenon, except the tenon is cut out on all four sides. This makes it stronger. It is the main joint used in the table base frame. It is used here in these places:
- on the two short ends of the table base, to lock the cross-rails into the table legs
- on the long sides of the table, to lock in the lower drawer-frame rails to the legs
- in the low-level I-beam that braces the table legs, to lock the long central beam into the lower end-rails
- for the leg pillars of the two benches, to lock in the top rails
Open mortice and tenon joint
This is probably not really the correct name for the jount used here, but it is close enough. It is the joint that attaches the two long upper drawer-frame rails of the table base. It is a kind of open mortice, which is really a plain tenon on the rails and a matching open recess in the top of the legs. Most of the strength here comes from the glue, whereas for a normal mortice and tenon with a good tight fit, the friction alone can hold it firmly together.
Blind mitred mortice and tenon joint
This is by far the most difficult joint used here. It is what creates the strong corner joints of the table top outer-rail. It needed to have the strength of the mortice and tenon, but not show it, so that all you can see from the outside is the nice angle of the mitre. This is a joint where you need to be slow and methodical or you can easily cock it up!
But it is not all mortice and tenons. Also used were...
Dowel-reinforced butt joint
This is a very simple joint. Essentially you use specially grooved hardwood pegs to connect two flat surfaces when glue alone is not strong enough. In effect it's like having a round mortice and tenon, but it is much easier to make on of these joints.
I used it to join the flat planks of the table-top inner base. You can use a tongue and groove for this, but you would lose some of the width of the plank.
I also used pegs to anchor the bench seats into the leg posts (combined with glue and screwing)
Mitred lap joint
This is a simple overlapping joint, where each half of the area to be joined is sawn halfway through so the finished joint is the same thickness as the original thickness of one of the pieces being joined. It is used on the inner decorative rails of the table-top that surround the central spalted beech panel
Tongue and groove joint
A classic simple joint for joining locking long edges together. A tongue cut on the edge of one piece fits into a corresponding groove on the edge of the piece to which it is being attached and glued in place. Really strong. This joint is what locks the table-top bed into its outer frame.
Glue and pin recessed panel joint
This is super-simple joint for attaching a panel to a boxed frame. In this case the bases of the drawers. For these small drawers, this was more than strong enough. For bigger drawers which may have heavy contents loaded in them, you can recess the frames to hold the board. Glue and pin joints can be used for box making too.
Screw-fixing
Just like gluing and pinning, you can also just glue and screw pieces together. This is how the back planks of the drawers are held on. It's not classy woodworking, but it is actually quite a strong joint. Once the base board has been nailed on, this makes it stronger still
Screw-reinforced rebate joint
The drawer fronts were also glued and screwed, but an additional rebate was cut to make the glue stronger (it is applied to 2 edges, instead of just one)
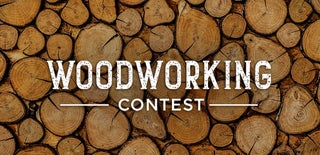
Second Prize in the
Woodworking Contest