Introduction: Reclaimed Plywood Guitar With Scratch-Built Pickup and 3d Inlay
I built this guitar to test the viability of making a fully working instrument using almost entirely scraps from my workshop. I had a lot of fun and learned a great deal in the process! I did most of my measuring and building on the fly, so I'm going to exclude my mistakes and fill them in with what I learned. There are many variables to this build, such as the inlay, the overall shape of the body/headstock, neck thickness, and such that can be changed depending on your preference or available materials/tools.
If you want to build your own, here is what you'll need:
MATERIALS
- 3/4" Plywood: about half a sheet's worth (4'x4'). The better quality you can find, the more stable it will be and fewer voids you'll have to deal with. I used some construction grade plywood along with some really nice stuff from old cabinet doors.
- 1/8" plywood or hardboard: for the back plate of the guitar. You need only enough to cover the back of the guitar body, so about a 2.5' x 2.5' square
- Hardwood strip: For the fret board. I used some salvaged walnut, but any durable wood will suffice. The piece needs to be at least 3/16" thick, 3" wide, and 21" long
-1/8" wood: I used a piece of an old folding ruler for this, but any piece of wood will do. It has to be about 1/2" wide and 4 inches long. You will need two of these. The cooler it looks, the better
- 6 machine screws: About 1" long and 1/8" diameter, panhead type.
- Fret Wire: for making the frets.
- Misc Guitar Parts: You need the following, and I can recommend the items linked, a volume potentiometer, volume knob, input jack, 20 gauge audio wire, tuning pegs, and a nut.
- Door Hinge: I used an antique cast iron hinge, but any standard sized door hinge you can drill through will do. This will be the saddle to hold the strings.
- Plastic: I used an old vinyl record, this will be used for the bezel to surround the pickup. You can use acrylic, HDPE, or anything you want, so long as it's about 1/16" thick and you can drill through it. The record looks really cool, though.
- Copper Wire: about 30-35 gauge. I salvaged mine from one of those "wall wart" type plugs.
- 6 neodynium magnets: the strong, little silver round types
TOOLS:
- Jigsaw:Necessary for cutting out the body, headstock, and tapering the neck. You could use a coping saw, but that'd be a lot of work. Use blades designed for cutting wood cleanly.
- Router: helps with making the slots for the electronics. You can substitute a drill with a forstner bit and a chisel, it will just be more work. I used a 1/4" straight bit.
- Table Saw: Necessary if you want to make the 3d inlay part of this guitar. Otherwise you can get away with any saw capable of making reliable, straight cuts through the plywood.
-Sanders: I used an oscillating belt sander, a handheld belt sander, and a random orbital sander. You can get by using just the random orbital sander. You can also use a rasp and do some hand sanding, if you're into grueling manual labor. I used 80 grit paper on the belts for shaping and 120, 200 grit paper on the random orbit for flushing and finishing, and also used 300 grit for a hand sanded finish.
- Drill/Driver: You'll need to make some holes and put screws into them. Pick your favorite tool for doing so. You'll need bits that are sized properly for installing your tuning pegs and input jack, and a 1/8 inch bit for the pickup screws, and a small bit that matches your small screws.
- Fine Tooth Saw: For the frets. I used a gent's saw and a coping saw for this. You can use any fine tooth saw with a narrow enough kerf to properly seat your fret wire. Be wary of any saw with a flexible blade, as it will be more difficult to cut a dead straight line.
- Files: a rougher file and a fine file will be adequate for shaping the frets.
- Wood Glue: I used titebond, you can use whatever type you're comfortable with
- CA (super/Krazy) Glue: Pretty self explanatory
- Planer: For reducing the thickness of the fret board. If it's already at the desired thickness, don't sweat this one. You can also use a hand plane or, carefully, your belt sander.
- Screws: 1 inch wood or drywall screws will work to hold on the back plate. 4 smaller screws (about 1/4 inch) for securing the pickup bezel.
- Clear Coat: Lacquer, Polycrylic, shellac, whatever you have or like to use will work just fine
- Plastic Cutting Tool: For whatever you choose as your pickup bezel. I used a Dremel with a rotozip bit to cut my vinyl record, but a specialty jig saw blade will cut acrylic, scissors can work for HDPE, etc
- Hot Glue Gun + glue sticks: Necessary for the pickup
- Soldering Iron + electronics solder: For the wiring/electronics
Step 1: The Through-Neck
A "Through Neck" is a neck that runs entirely through the body of the guitar. It provides a stable and permanent connection to the body of the guitar, as well as a unique look. It's also simpler to pull off for a beginner/intermediate woodworker than a bolt-on type neck.
1. Cut your ply wood into 3, 1.5" wide strips, about 40" long. This will be a few inches longer than the full length of the guitar, allowing you a little bit of extra room just in case.
2. Glue the 1.5" faces of the strips together into one solid block, spread the glue evenly and clamp, as shown. You should end up with a block that is 40" long, 2.25" wide, and 1.5" thick
3. Leave until cured (overnight) and clean up and glue drips
Step 2: Shaping the Neck
Now we have to start removing material from the neck blank to make it fit the rest of the guitar. We will also be cutting the headstock angle which helps to tension the strings.
1. On a table saw or any other capable saw, carefully cut a .75" deep slot across (perpendicular to the length) the neck block. This cut should be made where your headstock will end. My headstock is only 4" long, I'd suggest something a bit more standard, like 6" or so. This cut is made on what will be the back of the neck. Note, if you're using a table saw for these cuts, you'll need to hog out a bit more of the material between the cut and the tail (bottom) of the guitar, as shown in the pictures and video. This is to avoid over or under cutting due to the round saw blade in the next step.
2. Using the table saw or any capable saw, cut the neck block vertically, from the tail (bottom) to the horizontal cut you made below the headstock. You should now have a block that is .75" thick from the tail to the headstock area, and 1.5" thick at the headstock area.
3. Using a miter saw or any capable saw, measure and cut your headstock angle. The headstock on this guitar design angles backwards at about 14 degrees. You can set that angle to anything you want between about 5 and 17 degrees, just be sure that you have enough headstock material to support whichever angle you choose. The headstock should be about 1/2" thick, or as thin as needed to be able to fit your tuning hardware. This cut should be made on the non-stripey side of the neck block, as shown.
4. I added extra material to my headstock area, that was the same thickness as the headstock, and oriented the same way. I glued it in place and clamped it overnight before the next step.
5. Shape the headstock and taper the neck. I used a jigsaw for this, but any capable saw you are comfortable using should work.measure and mark the shape you want for a headstock. I suggest searching the ones that already exist online and finding one that will work with your tuning hardware. The neck taper on my guitar goes from 2.25" (full width) where it will meet the body, to 1.75" where the headstock starts (18" away from the body). That makes a 2.78 degree taper on each side. You can figure out a different taper angle if you want using this great website: http://www.magafor.com/841/uk.htm
6. Finally, I made a little, angled transition block for the area where the neck will meet the body. this is just for feel and aesthetics, but if you want, it should be 3/4" at the thickest part and be about the same size as shown. Don't glue it in place until the body is joined to the neck.
Step 3: Prep and Cut the Body Shape
I chose to work with plywood for this build because it is cheap, easily available, and I had plenty of it laying around my shop. The boards I chose to use were particularly high quality cabinet doors from the 1960s, but anything without too many voids or gaps will do.
1. Pick out a board that is at least 24" square. This should give you enough material for whatever body shape you choose. You'll need two of these and they should be 3/4" thick.
2. Sand off any finish, and trace the shape you want your guitar body to be on one of the sheets. There are plenty of searchable templates online, or you can just use your imagination, but unless you're experienced with guitar design, I'd pick something that is already proven to work.
3. Using a jigsaw or other capable saw, cut out your body shape from the sheet you drew it onto.
Step 4: Join the Neck to the Back of the Body
What you have so far is just the back of what will be a laminated guitar body. it is 3/4" thick, as is the neck of your guitar. i think you can see where this is going right now.
1. Place the neck of the guitar where it will go on the body. Make sure you have it placed EXACTLY where you want it on the body, and that there is 18" of neck between where it first meets the top of the body and the headstock.
2. Spread glue on the area where the neck will touch the body, and place the neck there, clamping it precisely into place. Make sure there is heavy, even pressure distributed along the glue-up. Any extra length of the neck can stick off of the bottom of the body for now.
Step 5: The Inlay (Optional)
Okay, so this is a fun design decision I added to make the guitar a little less boring. Since you have some time to kill while the glue dries on your neck/body, you can give it a shot if you want to. It's not necessary, and it doesnt need to be this exact design. I made this upon the fly, so my "measurements" were all trial and error, but I'll explain it as best I can.
1. You'll need a tablesaw to do this properly. You can achieve this look with a router in a table, a v-bit, and a good fence, bu I'm not going to explain that here.
2. Choose a piece of plywood that is 3/4" thick, square, and large enough for the section you want to inlay.
3. Tilt the saw blade to about a 45 degree angle and raise it so that it will cut halfway through your plywood.
4. Adjust your fence so that the first cut goes just barely all the way through the far end of your board. Note the position of your fence.
5. After making the first cut, move the fence about 1/2" closer to the blade and cut again. Repeat until the fence is no longer able to safely move toward the blade without touching it.
6. Rotate the board 90 degrees and reset your fence to the original position. Adjust it so that your next cut will connect to the top of the previous cut to form a v-shaped valley, as shown. (I know this isn't very mathematical or scientific, I did it by trial and error, myself)
7. Make the cut and adjust the fence so that your next cut will complete the next valley in the same way. Note the distance you adjusted the fence.
8. Adjust the fence closer to the blade in increments of the distance you noted in step 7, making a cut each time, until the fence is no longer safely able to be moved closer to the blade. Your board should be a series of equally spaced and sized ridges and valleys.
9. Rotate the board 45 degrees and repeat steps 4-8. Your board should now have a geometric pyramid pattern thoughout, with some weirdly shaped ones on the edges.
10. Use the table saw to trim off the messed up pyramids on the edges, and to cut out any sections that may have gotten messed up. Luckily this part is easy because everything is a straight line one way or the other.
Step 6: Cutting and Laminating the Body
Now, if your neck-to-body glue up is fully cured, we will be adding the "top layer" of the body lamination. I chose to use an old bench top that was made of plywood because it had a ton of old paint splashes and work marks that I thought looked cool. You can use whatver wolid or plywood you want (or another material you are familiar/comfortable with) so long as it is 3/4" thick.
1. Make sure the bottom of the material you want to use is clean and ready for gluing.
2. Trace the shape of the body onto the material you wish to use. Cut out the area where the neck will go entirely. I used a jig saw for the curves and a table saw for the straight cuts, but you can use whatever saw can get the job done accurately and safely.
3. (optional) If you are adding an inlay, choose the location and make the appropriate cuts, being sure to position your body sections appropriately. I added mine to the areas typically reserves for pick guards.
4. Apply and spread glue to the underside of the top pieces, affixing and clamping them in place until dried.
Step 7: (optional): Apply the Inlay
No real steps here, but if you're going with an inlay, this would be the time to cut it to shape, apply the glue and bond it to the body just as we did with the material from step 6.
Step 8: Sanding and Shaping
I used all sorts of sanders for this step, mainly because I have them. It CAN be done with just a random orbit, the proper grits of sandpaper and some patience. It can also be done with other tools suck as a router in a router table, a draw knife, and anything else you may be comfortable using safely that will get the job done. Essentially we are flattening the face or the guitar body and neck as well as matching up all the edges.
Step 9: The Fretboard
1. Find a strip of hardwood (I chose walnut) that can be cut to be 1/4" thick, 19.25" long, and 2.25" wide, then cut it to those dimensions using the tools you feel most comfortable with.
(If you are going to add a truss rod to this build, which I did not, You should do so now, before you glue down the fret board. Here is more info on installing a truss rod: https://www.stewmac.com/How-To/Online_Resources/Le... if you install a truss rod, note that you may need to install the nut of your guitar into the top position of the fretboard instead of above it, as detailed later in this guide)
2. Add and spread glue on the neck of your guitar, starting at about 1/4" down from where the neck meets the headstock, to where the end of the fretboard will be.
3. Place and clamp your fretboard to the neck, using evenly spaced clamps, being sure not to mar the surface.
4. Let dry until fully cured.
The mistake I made here was tapering my fretboard to match the lengthwise taper of the guitar neck BEFORE I marked where my frets were going to be. So let's add that step right here, shall we?
5. After the fretboard is dried, remove the clamps and begin planning your fret layout. I used a 24 inch scale on mine, but you can use whatever type you feel like. More information on fret layouts and scale length can be found here: https://en.wikipedia.org/wiki/Scale_length_(string...
And here is a great tool for calculating your fret layout: https://www.stewmac.com/FretCalculator
6. Use a combination square or a speed square to mark the areas where your frets will go. (the reason we are doing this now is because once we add the taper, the square will no longer work.
7. Use a sander, handplane, router, or capable tool to taper the sides of the fretboard flush to your neck.
Step 10: The Pickup
This step can be undertaken while you are waiting for the fretboard glue-up to cure. this is a really fun part of this guitar build, and can be skipped if you just want to buy a pre-made pickup, but I encourage you to give it a try. You can find a separate video I made, which delves into the pickup construction for this project here:
1. Gather your materials.
2. Cut the wood (I used an old ruler, which helped a LOT with measurements) to a length of about 3.5 ". The width should be 1/2". The thickness should be about 1/8" - 3/8". Cut two of these.
3. Drill 6 holes the size of the shaft of your machine screws, at 1/2", 1", 1.5", 2", 2.5", and 3", leaving a half inch to the end of the wood. Do this in both pieces of wood
4. Thread your machine screws through one of the pieces of wood, all the way up to the screw head. I used a little dab of hot glue under each screw head to secure it in place to the wood.
5. Thread the next piece of wood up the screws, about 3/4" down the length of the screw from the top piece of wood. Secure it in place with a little hot glue.
6. Trim the bottoms of the screws flush with the bottom piece of wood using a hacksaw or any capable tool you are comfortable using.
7. Get your copper wire ready. (I got mine from the inside of one of those "wall wart" type plugs. The wire I use in the video is thicker than I wanted, but you can use anything that is about 30-45 gauge.)
8. Leaving about an inch and a half of wire exposed, start carefully winding it around the outside of the screws between the pieces of wood. this should be done extremely carefully, as any break in the wire will rewire you to take it all off and start over again. this takes a long time, and I made a simple jig using my drill to help out. there are plenty of other designs for helpful pickup-winding jigs out there if you want to find one that suits your needs.
9. After winding the pickup until the copper wire is almost thick enough to reach the edges of the wooden parts (should be a few thousand winds... I know!) leave the last inch and a half exposed somewhat nearby to where the first one was. Either take note, or label the exposed wire ends with some tape or nail polish. The end that you STARTED the wind with is the GROUND, and the end that you FINISHED the wind with is the HOT.
10. Use hot glue (or wax or lacquer) to coat the coil of copper wire, leaving the "lead" ends uncoated.
11. Attach a small, neodymium magnet to the cut end of each of the screws on the bottom of the pickup. I secured these afterward with some more hot glue.
12. If you have the capability, you can splice the wires to a 1/4" input jack and test your pickup on an amplifier. You just have to play a guitar over the top of the screws, so that the strings are facing the screws and nearly touching them.
Step 11: Installing the Frets
This was my first time installing frets on a guitar by hand and I made a bit of a mess of things. I encourage you to look around on the web for guides that will help you choose the method and procedure that is right for you AND your toolset and skill level. Here is what I did.
1. Mark your frets (we already did this earlier in this guide)
2. With a saw that is the same thickness as your fret wire's tang, cut the marks you made to the depth of the fret wire's tang.
3. OK. We are gonna veer off from what I did in the video again in order to make things easier for all of you. Once all of your fret slots are cut, take this opportunity to shape the fretboard into an arched shape (I did this by sight, and ended up with a comfortable-to-me radius of about 9". 7.25" is more standard. Again there are jigs and guides online if you want to do more research.) After that, you should shape the back of the neck (where your hand will be gliding along while playing) into a more rounded, comfortable shape for you. I used a series of sanders for this, you can use whatever tool you find most useful and comfortable. Also shape the edges of the guitar to the desired roundness with this same method.
4. Cut the fret wire into lengths a tiny be longer than the width of your fretboard.
5. Tap the fret wire into place in your grooves until it is fully and securely seated against the fretboard and it's radius. Carefully widen or deepen any slots as necessary.
6. Clip the ends of the fret wire as close to flush as you can with the sides of the fretboard.
9. Lay tape between the frets to protect your fret board.
8. Use a file to smooth the ends of the frets and add a very small radius to them for comfort.
9. Use a piece of sandpaper (i used 220 grit) attached to a dead-flat board to sand the tops of all of the frets to the exact same height.
10. use a file again to radius the corners at the top of the frets left by your flattening, being careful not to undo the nice, even top you just sanded.
11. Polish the frets using a higher grit sandpaper (400 or so) and then 4-ought (#0000) steel wool to finish.
Step 12: Tuner Hardware
1. Choose a layout in your headstock that suits your tuning hardware and allows the tuners to function properly.
2. Drill your holes and install the tuners according to the manufacturer's instructions.
Step 13: Cutting the Pickup Slot
So, pickups can go almost anywhere between the bridge of the guitar and the bottom of the fretboard. Where you position them will affect how they pick up the sound from the strings. Do a little research and decide where you want this pickup to be placed. I chose the middle area, slightly closer to the neck.
1. Use a router to carve a slot 1/2" wide x 3.5" long and deep enough so that your pickup sits inside with the top 1/4" piece of wood sitting just above the surface of the guitar.
2. Drill a hole for your wires from the bottom of the fret slot through to the back of the guitar body. Make sure this is on the side of the guitar where your exposed leads are. If it's not, it the wiring will be doable, but possibly a bit more annoying.
3. Check the fit of your pickup and move on to the next step.
Step 14: Cut Your Wiring Channels
I chose to do my wiring on the back of the guitar in order to make it simpler to upgrade and part pieces later. I recommend it for this design.
1. I went all the way through to the back with my pickup slot. this isnt necessary so long as you have followed this guide properly.
2. With a router or other capable tool, cut a path from the wiring hole beneath your pickup slot to the space where you want to install your volume control and output jack.
3. Cut a cavity with enough space for your electronics to the required depth to install those parts. I went about 1" deep and made sure to cut the hole for the jack into this cavity from the side.
4. Clean up any jagged bits and clear out any and all sawdust.
Step 15: Mount the Volume Potentiometer
1. Find a comfortable place for your volume knob on the front of your guitar, which will sit above your electronics cavity, leaving enough room inside for the volume pot and the input jack.
2. Install the potentiometer as per the manufacturer's instructions.
Step 16: Adding a Pickup Bezel
I did this to hide the space around the wooden part of the pickup and to add a little more flair to the build.
1. Find a suitable material. I chose and old, vinyl record. Your material must be thinner than the wooden part of your pickup so that it sits lower.
2. Decide on a shape for your bezel.
3. Mark and cut your material. Be sure to include a slot for your pickup to fit through
4. Place it around your pickup, between the top of the device and the slot in the guitar body
5. Fasten it in place
Step 17: Attach the Nut
1. Prep the top of your fretboard. It should be flat and sitting exactly 90 degrees to the center line of the guitar.
2. Use a file or sanding block to flatten the area of the headstock just above the fretboard so that it makes a perfect 90 degree angle with the top of the fretboard.
3. Check to see if your nut fits in place, flush up against both surfaces. It should sit slightly above your fretboard. If it sits too high, file the headstock area more until it seats correctly. If it's too low, you can use a thin shim to get it to the correct height, so long as it remains flush up against the shim and the top of the fretboard.
4. Secure the nut in place with a bit of CA (Super/Krazy) glue.
Step 18: The "Saddle"
I used a hinge as a very simple "saddle," or the part of the guitar that anchors the strings. A hinge works pretty well because it adjusts itself under tension to match the height or "action" of the strings.
1. Make six holes in your hinge with a drill and appropriate bit. Make sure to space them evenly and the first and last hole should be under 2.25" apart.
2. Position the hinge at the base of the guitar, centered on the center line of the guitar. Mark the premade holes positions.
3. Pre-drill your marks where the pre-made holes were. Drill the one closest to your volume knob ALL the way through the guitar body.
4. Install your hinge with the cylindrical "pin" side facing up and your new holes on the side toward the neck, as shown.
Step 19: Finishing and Making the Back Plate
1. Tape off the pickup and remove and hardware or electronics you've mounted to the guitar. Don't worry about the frets.
2. I used spray shellac to finish the guitar. You can use whatever clear coat you wish. Spray a couple of coats on the front of the guitar according to the instruction on your can of finish.
3. After it's dried, cut the shape of the guitar body out of your 1/8 inch plywood (or substituted material)
3. Pre drill holes around the ends of the back plate into the guitar body and counter-sink the holes on the plate. Make sure you don't drill or drive screws into the electronics cavities.
4. Screw on the back plate, use a sander or sanding block to contour the edges.
5. Clean off any lingering dust and spray the back of the guitar, plate and all, with your finish. Do a few coats.
Step 20: Create a Floating Bridge
A floating bridge is a piece of dense wood or metal that holds the strings up and in place between the pickups and the tailpiece (saddle.) It is positioned at the end of your scale length (24 inches from the nut for me) and can be adjusted. I used a trapezoidal piece of plywood in the video, but have since cut a slot in the top of it and inserted a chunk of aluminum to hold the strings.
I created mine our of trial and error. Essentially you want it to:
1. Be able to keep the strings in place
2. Hold the strings up in a comfortable position above the pickup/fretboard while still keeping them seated in the nut so they don't slip around.
3. Not deaden the strings. A dense wood like ebony or a metal like aluminum or brass will help transmit the tone and sound of the strings best.
If necessary, use a file to carve shallow, v shaped slots into the bridge in order to keep the strings from sliding around too much.
Step 21: Wire the Electronics
For this step, you're gonna want to have a passing familiarity with electronics and how they work and also how to solder or AT LEAST use shrink tubing. There, again, are countless youtube videos that explain this process, so if this isn't clear enough for you, about 30 mins of research should fix that. (here's a great one that I used: https://youtu.be/K33Xj95095I)
1. With your router or appropriate tool, carve a channel from your electronics cavity to the screw hole you drilled through to the back from the bridge.
2. Connect your ground and lead from the pickup to the appropriate places on your volume potentiometer.
3. Connect your ground and lead from the potentiometer to the proper places on your output jack.
4. Wire another ground from the potentiometer to the bridge's anchor screw hole. Connect this as best you can to the screw in the hole. and secure it with solder or hot glue. This last step grounds your electronics to the strings and cuts out a LOT of buzzing and frustration.
Step 22: String It Up and Play!
That's just about it! Get your strings installed on the guitar, position your floating bridge properly, and enjoy your new guitar, made for very little money and time!
This project is not for those looking to make a super professional electric guitar. It's a simple build that will help you understand the basics of building an electric guitar and set you up for future builds or modifications to this project.
If you found this guide helpful, or found some errors or missteps (hopefully there aren't any, but it was a LONG guide I was writing from memory of a 6 month old project) please shoot me a message or leave a comment!
Thanks again and enjoy!
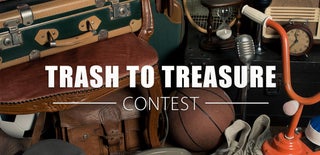
First Prize in the
Trash to Treasure