Introduction: Recycled Skateboard Bowl
Hello! It’s been a while since I have wrote one of these, so when I heard about the skateboard contest I had to get entering.
This is my instructable for how to make a bowl from recycled skateboards.
This is my instructable for how to make a bowl from recycled skateboards.
Supplies
Recycled skateboards - lots of
Wood lathe
Wood turning tools
Heat gun
Palm sander/belt sander
Sandpaper - up to 1000 grit
Glue scraper
Titebond III
Clamps (or bottle jack press frame)
Danish/boiled linseed oil for finishing
Wood lathe
Wood turning tools
Heat gun
Palm sander/belt sander
Sandpaper - up to 1000 grit
Glue scraper
Titebond III
Clamps (or bottle jack press frame)
Danish/boiled linseed oil for finishing
Step 1: Gathering the Skateboards
For this project to work you need to be able to get your hands on some used, broken or unwanted skateboards. You can check local shops, skateparks, friends to see what is lying around. The bowl I made was about 6” diameter which works out at about 18 nose/tails, so if you can get hold of 9-10 skateboards your golden.
Step 2: Preparing the Wood
This part is by far the worst. You want something from oak, you buy a piece of oak. You want something from walnut, you go buy a piece of walnut..... you get the idea. You can’t buy skatewood, you have to make it.
It starts by removing the grip tape and other stickers. This is where your heat gun comes in handy. Then you can sand off all the graphics, clear coats, glue until you finally get to bare wood.
It starts by removing the grip tape and other stickers. This is where your heat gun comes in handy. Then you can sand off all the graphics, clear coats, glue until you finally get to bare wood.
Step 3: Cutting and Gluing
Now you have usable wood you can start to cut up and glue together. As mentioned in the title, I like to use 18 nose/tails for my bowls. This allows for a nice size of bowl with a good depth. It’s that little bit trickier to hollow out with it being deep, but it’s totally worth the effort.
Once you have your board sections ready, do a test fit to make sure the contours will line up ok. Also stack the larger nose/tails in the middle of the block you will glue to make the most out of the material.
Once ready, apply your glue and clamp up tight. I made a steel frame to use along with a bottle jack to allow for a good clamp pressure. You’ll now need to leave this to dry for 48 hours to be certain everything is dry.
Once you have your board sections ready, do a test fit to make sure the contours will line up ok. Also stack the larger nose/tails in the middle of the block you will glue to make the most out of the material.
Once ready, apply your glue and clamp up tight. I made a steel frame to use along with a bottle jack to allow for a good clamp pressure. You’ll now need to leave this to dry for 48 hours to be certain everything is dry.
Step 4: Safety Talk
Before you start to turn please ensure you wear the correct PPE for the task in hand, and operate the machine in a safe way.
I always wear a full face visor to protect me, and also a woodturning smock.
Make sure all your chisels are sharp and take care to avoid snags. Skatewood can blow up on you if your prep work isn’t up to scratch.
If you do get a piece blow up on you, it’s likely you can salvage it by repeating the sanding and glue up steps.
Stay safe please !
I always wear a full face visor to protect me, and also a woodturning smock.
Make sure all your chisels are sharp and take care to avoid snags. Skatewood can blow up on you if your prep work isn’t up to scratch.
If you do get a piece blow up on you, it’s likely you can salvage it by repeating the sanding and glue up steps.
Stay safe please !
Step 5: Time to Turn
Now you should have a huge square block that it ready to be turned. A good tip is to try and mark out your circle shape and cut off the excess prior to turning. This will allow for a much steadier workpiece.
Once in the lathe you can start to rough out your basic shape. Then create either a external or internal tenon for your chuck jaws to grip.
Now all that is left to do it to turn your bowl to the desired size and shape.
Once in the lathe you can start to rough out your basic shape. Then create either a external or internal tenon for your chuck jaws to grip.
Now all that is left to do it to turn your bowl to the desired size and shape.
Step 6: The Finish
You should now have your bowl to shape ready for the finish.
I would normally use Mirka sheets for the sanding with some foam blocks. This gives a nice soft sand that isn’t too aggressive. Go from 120g right through to 600g at a minimum for a super smooth finished. Sometimes I’ll even go to 1000g depending on time.
Apply some danish oil or boiled linseed oil as per instructions and then sand again.
Once the oils have dried I then like to take the bowl to a buffing wheel for a final polish.
So there you have it, your completed recycled skateboard bowl.
I would normally use Mirka sheets for the sanding with some foam blocks. This gives a nice soft sand that isn’t too aggressive. Go from 120g right through to 600g at a minimum for a super smooth finished. Sometimes I’ll even go to 1000g depending on time.
Apply some danish oil or boiled linseed oil as per instructions and then sand again.
Once the oils have dried I then like to take the bowl to a buffing wheel for a final polish.
So there you have it, your completed recycled skateboard bowl.
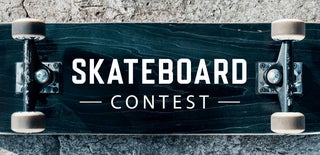
Grand Prize in the
Skateboard Contest