Introduction: Red on Black: Homage to Tatlin
This kinetic sculpture is inspired by the Tatlin's Tower, a project that the Russian architect Vladimir Tatlin created in 1920. The tower’s steel framework having the form of twin helix was supposed to support four geometric forms (a cube, a pyramid, a cylinder and a hemisphere) made of glass and rotating at different rates: one turn per year the cube, one turn per month the pyramid, one turn per day the cylinder, one turn per hour the hemisphere. These figures were intended to be venues for meetings, conferences, artistic performances.
The height of the tower was planned to be 400 metres, its tilt from the vertical 23.5 degrees (the same that the Earth’s mean axial tilt). The project, too ambitious both for its time and place, was never realized; however, it inspired several modern artists and architects: for example, figure 1 shows you a model of the tower at the Royal Academy of Arts in London
(https://en.wikipedia.org/wiki/Tatlin%27s_Tower#/media/File:Model_of_Tatlin_Tower,_Royal_Academy,_London,_27_Feb_2012.jpg)
or this project
(http://www.evolo.us/envisioning-a-new-tatlins-tower-at-ciliwung-river-in-jakarta/) ;
figures 2 gives you an idea of how the tower would have been in St-Petersburg where it was intended to be.
(http://www.architecturetoday.co.uk/tatlin-tales/)
My sculpture has a height of 20 cm without the base; I chose the size of the other elements proportional to the height.
Supplies
The sculpture is made of 2 mm thick plexiglass, 2 mm thick plastic and 3 mm thick hardboard (for the base). That’s what is also needed: a small motor like one used in walkmans, an ON-OFF switch, a battery holder for 3 AA batteries, wires, steel round bar of 2 mm diameter, two 30 teeth sprockets, two 10 teeth sprockets, a sheave of 6 mm diameter.
The tools used are:
plexiglass cutter
exacto knife
fretsaw
drill with drill bits
screwdriver
soldering gun with solder
a pair of pliers
file
painting brush
sandpaper
Step 1: Geometric Forms
The cube has a size of 50 x 50 x 50 mm, it’s made of plexiglass, figures 1 through 4 show the parts of the cube, its assembly and the cube together with its lower sheave. The cube and the 60 mm diameter sheave which is under the cube are fixed to the shaft by means of epoxy glue, the proceeding being explained in Technology section.
The base of the pyramid is an isosceles triangle (its base is 50 mm long, its heigh is 50 mm); the pyramid’s height is 40 mm. It’s also made of plexiglass, and fixed by means of epoxy glue to its shaft, see figures 5 and 6.
I made the cube and the pyramid of transparent plexiglass available at my workshop and sandpapered them to dim their surfaces.
The cylinder is made of liquid Fimo gel; a mould with a central core was necessary to make this element, see figures 7 and 8. The outer diameter of the cylinder is 14 mm, the diameter of the core is 8 mm; the cylinder is 30 mm high. Figure 9 shows the cylinder ready and assembled with its shaft. As the previous figures, the cylinder is glued to its shaft.
The hemisphere is also made of liquid Fimo gel and has a diameter of 10 mm. The mould is made of decorative cement, a small bulb served as a model to make the imprint. Figures 10 and 11 show how the mould was made. The hemisphere ready is shown in figure 12. To fix the shaft to the hemisphere, first, a spacer (2 mm thick, 8 mm of diameter) should be glued to the hemisphere; then, the shaft is inserted into the spacer and glued.
After the gel is put into the moulds, it should be cured at 130 deg Celsius during 20 minutes.
Step 2: Inner Tower
The inner tower and its beams that support the mechanism and the outer ‘helices’ are made of transparent plexiglass. The tower’s parts are shown in figure 1, the assembled tower is shown in figure 2. The positioning of the beams and the axis of the rotating figures are shown in drawing (figure 3). Each beam is made of two identical parts glued together, 2 mm diameter holes are drilled in the beams to serve as sleeves for the shafts of the geometric forms.
The lowest beam (base beam) is 10 mm wide; the other beams are 7 mm wide.
The tower’s base is made of plexiglass and glued to the base beam; this element would be fixed to the hardboard base by means of small wood screws.
Step 3: Outer Tower
The parts of the tower are made of plastic according to the template shown in figure 1. The openings are cut using a fretsaw and filed. The sides of the tower are fixed together by means of 8 mm wide spacers; the assembled tower is shown in figure 3. the tower is painted carmine.
The outer tower is fixed to the inner tower using small screws; thus, the internal transparent tower becomes ‘invisible’.
Step 4: Towers Assembled
The figures 1 and 2 show both towers with the beams. The outer tower is fixed to the inner tower by means of small screws that enter the holes in the end faces of the beams. The tower is inclined at 67 degrees to its base. The bright colour of the outer tower is supposed to visually 'dematerialize' the inner tower; thus, the spectator would have illusion that the geometric forms are suspended in the air.
Step 5: Base With Spacers
The lower part of the base is made of hardboard and has 170 mm in diameter, see figure 1. The upper part consists of two half circles, the overall diameter of which is also 170 mm, see figure 2. Each half circle is fixed to the lower part by means of two 24 mm high spacers 24 mm. Three fiber felt pads (see figure 3) are attached to the bottom surface of the lower part; they can also be of soft rubber. They are supposed to reduce the vibration transmitting from the sculpture’s base to its support, thus reducing the noise.
The spacers are made of a 14 mm diameter round wooden bar, their height is 24 mm. Two 2 mm holes for wood screws should be drilled at each end face of a spacer.
The base and the spacers are painted black.
Step 6: Geometric Form Units
The shafts of the units are made of a 2 mm diameter round steel bar; each unit sits on its respective beam through an 8 mm diameter spacer made of 2 mm thick plexiglass.
A 36 mm diameter grooved sheave is fixed to the cube’s top surface. Figure 1 shows the positioning of the elements.
A 30 teeth sprocket is installed on the pyramid’s shaft as shown in figure 4. A 6 mm diameter sheave is placed on the lower end of the pyramid’s shaft after the shaft is put into its sleeve.
A 30 teeth sprocket is installed on the cylinder’s shaft. A 10 teeth sprocket is put on the lower end of the cylinder’s shaft after the shaft is inserted into its sleeve.
The hemisphere with its shaft is inserted into its respective sleeve, and a 10 teeth sprocket is installed on the lower end of the shaft.
Generally, there would be no need to glue the sprockets to their shafts because they fit tightly enough to transmit the present torques which are quite small indeed. I also realized that the 6 mm sheave fitted tightly enough not to slide on the shaft during the rotation.
Step 7: Gear Motor
My goal wasn’t to exactly reproduce the original rates of the rotation, I just wanted to make the figures rotate at different speeds, the speed increasing with the height at which the figure is positioned. Thus, the ratio between the cube and the pyramid is 1 : 6; between the pyramid and the cylinder it’s 1 : 3; between the cylinder and the hemisphere it’s 1 : 3.
I used the magnetic tape drive of an old answering machine that was available at my workshop; figures 1 through 3 show you how the device was transformed.
It’s important that the motor make as less noise as possible, and motors of walkmans or discmans do the job perfectly. However, these motors rotate at about 3000 rev/min, so a big reducing ratio (about 60 : 1) is needed to ensure that the tower’s figures turn slowly.
Step 8: Assembly
Figures 1 through 5 represent different aspects of the assembly. I proceeded as follows:
Fix the spacers to the lower part of the black base
Fix the tower to the lower part of the black base
Fix the external tower to the internal one by means of small screws; at this stage don’t put the screw into the top hole
Fix the aluminum bracket to the top of the external tower by means of a small screw
Place the cube unit into its respective sleeve in the base beam, put the belt on the top sheave
Put the first beam (that with the pyramid unit) in its place, take care that the shaft turns freely in the sleeves. Drill two 1 mm diameter holes in the tower and beam at the same time, pass pins into the holes to fix the beam Thus, the joint would be dismountable to allow to change the belt, if needed. I made the belt of three layers of elastic thread
Determine the position of the gear motor; the rubber roll on the motor’s output shaft must adhere to the lower sheave tightly enough to prevent the sheave from sliding during rotation
Fix the gear motor to the base. I fixed it on one screw, so the mechanism can tilt around it; a thin steel bracket serves as the second attachment point; this setting allows to adjust the pressure of the rubber roller on the sheave, if needed.
Install the switch and the battery holder
Make the wiring (see figure 5)
Place the two half circles of the black base onto the spacer and fix them
Install the second beam (that with the cylinder unit); I just glued it in its place
Install the third beam (the hemisphere unit); I also glued it
Insert the ends of the plastic stripes into their respective slots
Wind the stripes around the tower, fix them with small screws to their respective pads* on the external tower (see picture 4).
Two additional pads were needed to fix the snails, I installed those pads during the final assembly.
Step 9: Technology
I transformed my electric drill into a kind of lathe (see figure 1) and turned all round parts by means of that device; I used an exact knife as a cutting tool, it’s quite feasible when working with thin plexiglass. When turning the spacers and the small sheave, a bolt with 2 washers and a nut passed through the spacer’s hole and tightened was sufficient to prevent the work piece from sliding. To turn the big sheave, I fixed it to a kind of chuck plate that I made of an Ikea piece (a plastic disc with a threaded rod in its centre, normally serves to adjust the height of furniture’s legs). The aluminum bracket to which the drill is fixed also serves as a support for the cutting tool. Wear goggles when working!!!
Figure 2 explains how to fix a sheave to its shaft. Two grooves on the opposite sides of the shaft’s diameter are made by means of a fine file; the glue enters the grooves and prevents the sheave from sliding. In fact, I made these grooves only on the cube’s shaft because it transmits the maximum torque.
The ‘helices’ are made of 2 mm thick and 4 mm wide plastic stripes. I rolled each stripe into a coil of about 70 mm diameter (see figure 3), placed them into a pot, poured some boiling water there and let it cool down. After this proceeding the stripes kept the round form, and I was able to transform them into a kind of helices.
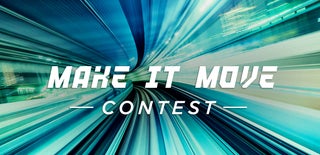
Runner Up in the
Make it Move