Introduction: Refurbish Old Axe
Recently my tomahawk wasn't cutting it when it came to splitting large chunks of Australian hardwood.
So I decided to cut to the chase and get an old axe and make my own handle. I have re-handled a few axes in my time and so I'm starting to get a handle of it.
If you have an old axe laying around, why not spend a few minutes reading my instructable so you don't end up axing yourself or someone else.
This tutorial will show you how I refurbished 2 axes, changed the shape of an axe head and made a laminated handle for each. You may not wish to laminate an axe handle so just skip past that if you just want to learn some tips and tricks.
Step 1: Things You Will Need
Though many of the tools in my video are industrial this does not mean you have to have them to re-handle an axe. All other axes I have done have been with hand tools only. If you have the hand tools to cut a circle out of ply and round the edges, you have all you need to make an axe handle.
Here is a list of tools and materials you will need.
- Timber for your handle. If your in the USA hickory seems to be the go to timber (Correct me if I am wrong) You could probably use a nice solid piece of walnut in a laminated handle also. If your not going to laminate a handle just go with a solid piece of hickory. Choose a piece with nice straight grain running the length of the handle when viewed from the top. If your really lucky the grain will follow the curve of the handle thats even better
- Rasp
- Sander, belt and orbital
- Angle grinder (if you wish to touch up the head of an axe)
- Flap discs for angle grinder head, 40 grit for ripping steel away fast and 120 for cleaning to a shiny finish
- Glue (Exterior polyurethane)
- Clamps
- Hacksaw (if modifying head of axe)
- A saw to cut out your shape - band saw, jigsaw or if you're really patient, a coping saw
- Inox or a similar lubricant used in marine. Linseed oil is also a popular handle/anti rust protectant for axes
Step 2: Mark Out Axe Head (skip If You Aren't Modifiying Axe Head Shape)
Here I used a paint marker to give me clear lines to cut my axe head shape to.
You can buy these markers at most office supply shops. They are great for marking out steel that is rusted or hard to draw on.
I wanted a lighter axe that someone smaller could also swing with ease while camping but also maintained the splitting weight needed to pop apart the hardwoods we have here. I chose to make the head a sorta "Hudson river" design to reduce this weight.
Splitting axes have a good wedge shape. Speed axes or axes for felling trees have a more flatter appearance. Consider what you want to do with the axe before fixing it up.
Step 3: Cutting the New Shape Axe (Skip If You Are Not Modifying Your Axe Head)
Here I used a 4 inch angle grinder with a stainless steel cutting disc. These are very thin and cut so fast that the steel barely heats up. The brand I love the most is called "Pferd" - it means horse in German. Interesting huh??
After you have made your cuts as deep as they will go finish them with a hacksaw if need be. Use your hacksaw one stroke a second to maintain the teeth on it. Furiously hack sawing will take you longer because you will heat the teeth up. Mine was blunt so I used a reciprocal saw to finish it.
Next it's time to fit your 40 grit flap disc to your 4 inch grinder and clean up those cuts till you can no longer see any angle grinding marks.
Use a bucket of water or a hose to cool the head as you go. Remember that safety thing though. Water and electricity do mix! Dangerously well.
Step 4: Removing the Old Handle Material.
Often when someone is selling an old axe head it comes with part of the old handle in it.
Free handle right? Well sadly you will have to remove this. Depending on the age of the head you have will depend on how hard it is to remove. The smaller head I have here was very old, maybe 80 years judging by the stamp.
As time progresses you will see rust on the inside of the head turn to flakes and this compresses the timber in the head even more then it was originally. Striking a really set one with a large steel punch will do... nothing.
This head was one such head, so I first drilled a series of holes and then gently angled the drill bit to side-cut the excess material out. A sharp drill bit is needed for this. Do not put too much pressure on the drill bit when angling it. Drill bits are tempered for compression and torque rather than tension so they will snap! Let the flutes of the drill do the cutting and take your time.
Once you have taken out enough timber you should be able to knock out this piece of timber very easily. I used a piece of timber cause it was handy.
Step 5: Descaling Rust!
Once of the cheapest ways to remove rust is vinegar!
Vinegar!???? Whaaaaatt?
Yes vinegar! It's also good to take away sunburn after a shower too!
Anywho, get some cheap stuff and fill a bucket with enough vinegar to cover your axe head. Leave it 24 hours and then take it out and give it a scrub with steel wool, a wire brush or even a scourer.
If the head needs more rust removed, place it back in and repeat. Be sure to get any flakes out of the eye of the axe.
Important note!
Once you are happy, immediately spray the head with Inox, WD40 or similar. The vinegar strips steel so well that it will be exposed to flash rust! Yep you will see rust appear like an orange surface within a minute depending on your humidity where you live.
Interesting fact!
See that dark line on the axe head back from the cutting edge? That's the temper line! On some axes a piece of quality steel is pinched in the head and hammered flat.
Step 6: Dressing the Head
Once your axe or axe heads are done descaling it's time to remove some pitting.
Polishing an axe or any tool will prevent it from rusting as easily. On a microscopic level the steel is pushed down and this creates a flatter surface that has not as many places for rust to stick. A high level of polishing and work is required for this though so I left some patina on the older axe head.
If you want to polish to a mirror finish, use various flap discs increasing in grit to remove the pitting. Once this is completed, move onto wet and dry sandpaper starting at 400 grit, then 600, 800, 1000 and then finally use a buffing wheel with a stainless steel polishing compound.
Step 7: Ripping Handle Laminations
When I talk of industrial machines this is what I am talking about. I loooooved seeing this machine work.
When we first tried to use the normal band saw to rip the timber (beefwood is hard as!) smoke came pouring out, so we opted to use this horizontal band saw with a much larger blade in it.
I don't expect anyone re-handling an axe to have one of these machines but I thought I would put it in the instructable so you can see how it was done.
Try to buy timber that has already been dressed to size if you opt to make a laminated axe handle.
Once the timber has been ripped we also took advantage of the industrial sander to clean the timber up and make sure it was straight for gluing. You can use a normal belt sander to clean your timber up.
Beefwood is hard enough that you can hit it full swing with a hammer and barely leave a dent in it. :)
Step 8: Reading the Grain
Just before gluing your timber up, it is important to have a look at the grain of the timber and what it is doing.
Using your template try to lay your timbers in such a way to support the shape of your handle. Things like not placing a knot directly under the axe head and facing the grain the same direction for finishing purposes are good things to think about.
Interesting fact:
Timber will always plane or finish better in one direction. One way you will see it chip and the other will see it flatten nicely.
Step 9: Gluing
I'm glad my brother works at a place where he glues stuff together a lot. It made the job fast and mess free.
Thanks bro!!
We used a German made glue that is a marine polyurethane with fiberglass in it. It expands within 15 mins and fills the whole area nicely.
A good set of clamps and good glue will see your job with no visible gaps between laminations and prevent water from entering your handle when it is left out in the weather. A very desirable trait for an axe handle.
Step 10: Trace Your Template
Once your axe handle blank is finished drying, take it out of the clamps and draw your axe handle shape onto it. Be sure to put that grain the way you planned.
Use a band saw or what you have on hand to cut it out.
How to get a template
I went to a local hardware and traced the handle I liked best. I changed the two shapes I cut slightly to my needs. For a splitting axe, straighter handles are required. For an axe used to split fine timber a slight curve up the neck of the handle is nice.
Step 11: Shaping
Shaping is like tasting a fine wine or a the spark of love for someone inside your heart. No one can tell you why it tastes like that or how to do it you just start and your eyes tell you the rest.
I know a good handle is an oval shape so I sanded the handle into a "diamond" shape first before my brother hit it with the orbital sander and finished it.
Both the head and tail of the handle are left alone at this point.
3 laminations will give you a center point for reference for sanding and shaping
Step 12: Preparing to Fit the Head.
Next shape the head. A course rasp is a very fast way of roughing in the tang that goes through the head of the axe.
A good axe head will have a smaller hole at the base then the top of the head so that once your wedge is set your timber is shaped like "V" and will never come off.
Take your time to make this a fairly nice fit to your head. You want the last part to be forced on nice and snug. I took a little too much off.
Hints and tips to make your axe head stay put.
- Don't over-clean. I once cleaned an axe head too much because I wanted the inside of the hole really really clean. Because I cleaned the head out too much and fitted a spotted gum handle (oily timber when fresh) the head kept slipping off. Leave a little texture inside the axe head. Don't get oil, WD40 or anything inside the head before fitting.
- Dry your timber first. If you want your axe head to never come off make sure the moisture content of your timber is low low low! leaving the timber out on a hot roof prior to fitting is a good idea. Once fitted moisture sets into the timber and it will swell.
- Steel wedge placement. Some people like to bang a steel wedge in the top of an axe after the handle is finished. If you choose to do this do not put the wedge in parallel to the axe head because pulling the axe out of a cut will loosen the steel wedge. Do not put the wedge in horizontal to the axe head, twisting motions of removing an axe from wood will loosen this wedge. Instead place the wedge in at 45 degrees to the axe head. This will counter both above problems from happening to you. I opted for no steel wedge because I know the timber I used is very dry and the timber wedge I place in will never come out.
- Shaping the shoulders of tang. When shaping your tang do not cut the timber around the handle and then shave it to that line so that the base of your axe head is flush on the handle. This traps water and gives you a 90 degree shoulder. If you do this over time someone will overshoot a log and the handle will connect with the timber, this means the full force of the blow is taken on the handle by the weight of the head. It will break the head off the axe! Make the shoulder a gradual curve going into the head of the axe. This way the strength of the grain is maintained right into the head. You will see the last swing I did in the video I overshot the log. No broken handle though, and this is why.
.
Step 13: Setting Your Head
Tap the head down till you have the head exactly where you want it, then invert the handle.
'Member we didn't shape the base of the handle? This is why, cause it's.... hammer time!!
Tap the base of the handle repeatedly till the axe head no longer moves upwards. Oh and your axe head is not on the ground, it's being held in mid air while doing this.
Step 14: Placing Your Wedge
Here I cut a wedge on a drop saw. The pointy end of the wedge is actually not paper thin. It is the width of the slot to maintain strength.
I am using Bondcrete glue which is like an exterior PVA but better. It's slippery stuff.
Hammer this wedge in until you see your oval tang hug close to the walls of your axe head. Use a block of timber to prevent the wedge from breaking while hammering it.
My wedge was not wide enough so I just cut a smaller one and hammered that in after the large one was set. Use glue on it also.
Step 15: Cut the Tang Overhang
I like to use a scroll saw to trim off the tang because the scroll saw blade bends to the steel on the axe head. The photo above has had no sanding done to it.
Look at that wedge! Nice and solid.
Step 16: Shapening Your Axe
Because I am wanting my axes for splitting, I don't need a razor edge. I dressed the existing shape of the edge with a 120 flap disc on an angle grinder.
For a speed axe I would first use a file filled with chalk and finish with a stone. Diamond file if you're really fancy.
Step 17: Shaping the Base of the Handle.
Here instead of a traditional deer's foot, I chose to go with a rounded look. Simply cut it with a scroll, jig or band saw and sand till you're happy.
Step 18: Finishing the Handle and Head
Here I used Inox again. I love this stuff, it doesn't go gummy, it lasts longer then WD40 and protects timber and steel very well. Spray it on and rub it around. It will give a satin finish once it soaks in.
Linseed oil is also a popular choice for an axe handle.
Step 19: Test Your Axe!!
Once everything is dry, take your axe to the hills... or your back yard, and chop some wood! Mine is still going well and I have used the smaller one almost every night since making it.
I hope this instructable helps people to bring old quality axes back to life and put them back to use. They really are the best axes!
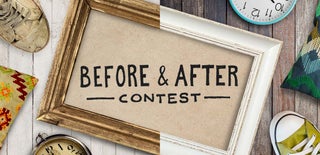
Participated in the
Before and After Contest 2017