Introduction: Repairing Environmental Damage to Glass Solar Cells
These are more of the solar lights I gather from my neighbor’s waste bin after being tossed in the garbage when the lights have stopped working. As usual the ones that only need minor repairs, I repair, and the ones that need major work I strip for parts and reverse engineer the circuit boards. Just like the polymer solar cells, some of the glass solar cells suffer from environmental damage.
Soldering new leads onto glass solar cells can be next to impossible; however it is one of the first repairs I managed on glass solar cells is replacing the leads. I found an answer to replacing the leads when there is no solder bead on the back of the solar cell and published it in this Instructable.
https://www.instructables.com/id/Repairing-Solar-Ce...
And now I am going to tackle Environmental Degradation to glass solar cells. Oxides, dirt, and grime, prevent reattachment of leads and continuity. Missing coatings on the back can cause the cell to short or reduce the cells effectiveness. In this Instructable I am going to take on the challenge of repairing environmental damage to glass solar cells.
Step 1: Tools & Supplies
Multi Meter
Soldering Iron
Small Paint Brushes
Utility Knife
Red or black Marker
Tape, I used scotch tape but just about any kind of tape will do.
Damaged Solar cells
Red and Black Wires
Solder
Liquid Plastic Coat
5 Minute Epoxy Resin Glue
Conductive Paint or Conductive Glue. A Rear Window Defogger Repair Kit will do if you can’t get conductive paint or conductive glue.
Step 2: Disassemble and Sort the Solar Cells
After repairing any of the salvageable solar lights; disassemble the rest and sort the parts. There are a many salvageable parts like LEDs, photo resistors, switches, and other components that can be used in a multitude of other projects.
Next sort and test the solar cells with lead wires, and put all the working cells aside.
Many of the solar cells without lead wires but with a bead of solder still on the back of the cell are relatively easy to repair by attaching a new lead wire, so I test them and put the working ones aside.
Step 3: Soldering on New Lead Wires
Start by testing the solar cell with your multi meter making sure the leads of your multi meter contact with the solder beads on the back of the solar cell.
After making sure the solar cell works use the leads of your meter to mark the positive or negative on the solar cell. Since my marker was black I marked the negative side of the solar cell.
Step 4: Soldering the Wires
This part is important; tin the lead wires first. If you do not tin the wire before you attempt attaching the wire to the solder bead on the back of the solar cell, you may lose the solder bead on the back of the solar cell from overheating.
Place the tined wire on the solder bead and heat it with your soldering iron.
As soon as the soldered bead melts to the tined wire remove the heat.
Test the solar cell before you secure the lead wires.
Step 5: Secure the Leads
I would recommend doing this to all solar cells with good lead wires. To make sure the wire leads will not come off while you are working with the solar cell secure the leads with epoxy resin glue. I used 5 Minute Epoxy Resin Glue.
Mix the epoxy and hardener on a pad and spread it over the soldered joint and insulation at the end of the wire.
Although it is called 5 Minute Epoxy Resin Glue; and it sets in 5 minutes, let it harden for 24 hours before using the solar cell.
Step 6: Extreme Environmental Damage
By this point you should be left with solar cells missing leads and solder beads. The environmental degradation will cause the backing to peel off even some of the conductive material to oxidize off around the places where the wire leads connected to the cells. As bad as these solar cells look, many of them are salvageable.
So start by washing the solar cells with soap and water to remove dirt, oxides, and any loose flaking backing.
Step 7: Testing
If you just connect a multi meter to solar cells with environmental degradation; chances are you will not get a reading on your meter. Protective coating or missing conductive film on the back of the solar cells will interfere with the connections to your meter.
Start by peeling any insulating lawyers or paint off the back of the solar cell, you should be able to do this with a sharp knife.
Now when you test the solar cell; make sure you connect the leads of the meter to conductive material on the solar cell, if the cell is good, you should get a reading even with indoor lighting.
Mark the positive or negative just like step 3.
Step 8: Attaching New Wire Leads
Start by tinning the wire lead ends just like step 4.
Secure the solar cell so it won’t move, for this I taped the solar cell to a flat surface with scotch tape.
Secure the new wire leads in place with more tape.
Connect the new wire leads with conductive paint or conductive glue; I used the conductive paint from a Rear Window Defogger Repair Kit. Make sure you spread the glue or paint across the end of the solar cell from the wire to points where you have continuity to the rest of the solar cell.
Wait one hour and use epoxy resin glue to secure the new leads to the solar cell and wait for the epoxy to set.
Step 9: Final Test and Coating
Before replacing the protective coating on the back of the solar cells test them and make sure they produce a good voltage. You get the best voltages with full natural sunlight or very bright artificial lights.
Wipe any dirt off the back of the solar cell.
Paint the back of the solar cell with lacquer or some other protective coating. I used black plastic coating I make.
https://www.instructables.com/id/Plastic-Coat/
After an hour you have working solar cells ready to use in your next project.
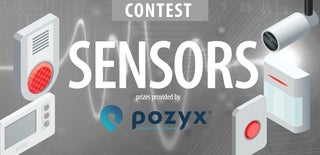
Participated in the
Sensors Contest 2017
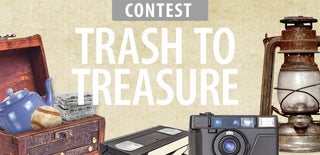
Participated in the
Trash to Treasure Contest 2017
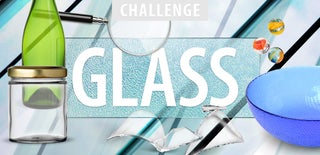
Participated in the
Glass Challenge 2017