Introduction: Resin Casting Tutorial - Moldmaking
When I started to make my Umi costume, it soon became apparent that I would have to make my own custom molds. You can usually buy or find something to cast common gem shapes, but sometimes the size you need won't be commercially available. In the above pictures, all the front tabard gems, headband gems, and waist cincher gems were made from custom molds using silicone rubber from Smooth-On. (The small ovals and small circle gems were made from a Michael's resin casting tray and a generic $1 paint tray respectively.)
For this project, you will need:
-sculpey, sandpaper, and clear spray glaze to create the model gems
-sulfur free oil based clay to make the mold walls, and/or a conveniently shaped takeout container (playdoh might even do in a pinch)
-OOMOO 25 silicone casting rubber to create the molds (available at Smooth On and Dick Blick's)
After your molds are finished, you'll probably want to get some clear resin so you can cast the gems. For this sort of project, I recommend:
-Castin' Craft Easy Craft Clear Casting Epoxy (usually available at Michael's, Dick Blick's, or Amazon)
Step 1:
The first step was to figure out how large I wanted the gems to be. After working out what size they should be with paper or tagboard, I cut them out of chipboard (extremely stiff/fine grained cardboard). The chipboard is stiff and provides a solid foundation for whatever type of clay you choose to put on top of it. Numbering your pieces is also a good idea if you have a lot of similar shapes you need to keep track of throughout the process.
Step 2:
The next step is to sculpt your gems. I used wax paper to help keep the sculpey from sticking to anything.
Step 3:
After I finished shaping and beveling my sculpey gems, I baked them and then sanded them with a lower grit sandpaper. I worked my way up to the highest grit I had before hitting them with a few coats of clear spray sealant so that they were nice and smooth and shiny. I probably would have sanded with an even higher grit if I had known where to find it at the time (apparently automotive stores extend into a higher range).
Since at the end you'll be casting something that's clear and will reflect light, ANY sort of tiny imperfection or roughness that was left on your original will be EXTREMELY noticeable, so be sure to take your time at this stage to get everything absolutely perfect and smooth. This is the most important step!!
Step 4:
After thinking a while on the most efficient way to arrange the pieces, I decided on this configuration and then walled it in with some oil-based clay on top of some wax paper.
Step 5:
I then repeated the process for the front pieces and headband pieces.
Step 6:
Time to mix your rubber! OOMOO 25 has a 1:1 ratio, so you should mix equal parts blue and pink. They will turn a nice purple color.
Incidentally, if you let your bottles sit around after opening for several months too long, the rubber will still cure, but just be really, really stiff. I had to go buy new rubber for this project since the old stuff was too viscous to flow properly around my originals or let the bubbles escape.
Step 7:
Pour it on!
Step 8:
It'll level itself out on its own. OOMOO 25 has a 15 minute pot life and a 75 minute cure time. This means you will need to finish all your pouring before you get close to the 15 minute mark and then refrain from poking it for at least an hour or so.
Step 9:
After curing, just pop your originals out, mix up a batch of Castin' Craft resin according to the instructions, and cast away!
If you spilled any OOMOO you will notice it was fairly easy to clean up. This is NOT the case with the resin, so take care not to spill it!
Step 10: Assorted Finishing Tips
There are a lot of different methods of backing gems, so I won't cover them all here.
Tin foil tends to wrinkle, so I don't advise using it. I also wouldn't advise tinting the gem with dye if you have many different gems to cast--keeping the color intensity consistent across resin batches of varying size can be a pain.
What worked for me was casting clear resin with no dye, and then backing it in my desired color.
At first, I tried painting the gem backs with blue sparkle paint, and then once dry, hot gluing them to my costume. DON'T DO THIS unless the place you're attaching them is really flat! The flexing caused my shoulder gems to detach as the paint was insufficiently "sticky" and peeled away from the clear gem as the day went on.
WHAT WORKED FOR ME:
I painted some tagboard with blue sparkle paint, and allowed it to dry. Then I dumped a VERY large amount of hot glue onto the paper, and smashed a clear gem down on top of it. (Use a heat gun on the pile of hot glue before smooshing the gem on top if you're having troubles with the hot glue cooling too fast.) This worked REALLY well as the hot glue is clear, and stuck to both the gem and the paper very well. Now that your gem has been backed you can attach it to your costume or prop with whatever means you prefer.
So to summarize, the order from top to bottom should be:
-clear gem
-hot glue layer
-tagboard painted whatever color
-hot glue or other adhesive
-costume piece
Step 11:
Congrats! You're done.
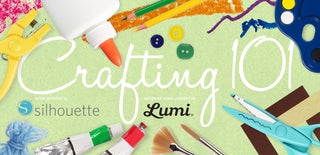
Participated in the
Crafting 101