Introduction: Resin Honeycomb Serving Board
The idea had 2 goals, to have a nice serving board and to use it to explain my children where the honey is coming from.
The intention was to have an object that resembles a beehive frame, something light that could be easy moved.
Supplies
Materials:
- Polyester/Epoxy resin (3 liters) *****
- Resin catalyst if using polyester resin
- Dyes: Yellow, Red
- Pigments: Yellow, White
- melamine faced MDF
(1) Base: 13 x 11 inches
(4) Strips: 13 inches
- Lumber (Maple, ash or pine): 5 x 13 inches, 1 inch thick
- CA glue
- Wood glue
- 1 1/4 screws (2x)
- Butcher block conditioner
- Polishing media
Machines:
- CNC with 1/2 and 1/8 flat end mills
- Table Saw
- Drill with a countersink and a 1/8 wood/metal drill
- Orbital sander
Other materials:
- Disposable 12oz cups
- Disposable stir sticks
- Wax paper
- Sand paper: 60, 120, 150, 220, 400, 600
- Micro mesh sanding pads: 1500 to 12000 grit
***** Disclaimer
No all resins are food grade, please consider this before selecting your material. There are some options
1) On this web page there is very interesting information: https://resin-expert.com/en/guide/food-safe-epoxy
2) I used a final coat of Butcher block conditioner that is 100% food safe to create a temporary film.
Step 1: Design
The design is easy, it is just an hexagon pattern,but, it had to be adjusted to the manufacturing constraints, in this specific case it was the 1/8 diameter flat end cutter.
If I had a smaller diameter tool I might have reduced the general hexagon size, but, the smaller the tool the higher the chances to break it or it could have take a lot longer to CNC the resin board.
The final resin board was planned to have 12 inches long x 10 inches width x 1/2 thickness. If you want to change the dimension consider to recalculate the total resin volume.
I have included the DXF file in case you want to have a guide. Please review the design three times, measure always twice and finally cut or pour ounce.
Attachments
Step 2: Cut the Parts and Build the Box
You need to cut the base, 13 X 10.5 inches and four 1 inch strips.
I used CA glue to fix the strips, if you want to do it faster consider using CA accelerator. When the sides were fixed and dry I just put some more CA on the internal box joints to make sure there were no gaps.
Step 3: Prepare the Resin
I used disposable 12oz cups, 30 drops of Yellow dye per cup. Once the dye was included I mixed for 2 to 3 minutes. I used 2 cups at the same time.
I had pre-measured the Resin catalyst and once added I mixed it again for 2 minutes.
Step 4: Start Pouring the Resin
Depending on the resin you are using you will need to add some scrap pieces under the box. As some resins have strong exothermic reaction they will create a lot of heat !! and if you don´t have ventilation and heat dissipation under the box you will get a concave board.
If you have slow curing resin you don´t have to worry as much about this.
I had something like 10 minutes before the resin started to change its consistency. In order to reduce the amount of air bubbles I poured the resin slowly forming a thin section, please see the second image on this step.
Step 5: Add More Resin
4 layers were included for the board. There were a one hour waiting between the resin layers to help with the heat dissipation. If I have decided to pour everything at the same time it is 100% probable to have the board cracked due to excessive heat.
I decided to change the tone a little bit during the second and third pour adding 2 red drops to one of the cups and then I poured on opposite corners. during the investigation I noted the real bee hives have different yellow shades instead of one single solid color.
On the image you can see the different yellow tones.
The total board thickness was 3/4.
Step 6: Demold the Resin Board
I let the resin to set up for a couple of days. Once the surface wasn't tacky it was very easy to demold the board mainly to the natural resin´s contraction. I just twisted the box a little bit and if separated by itself.
Step 7: Level Up the Board
I used a regular end mill to flatten both sides.
Step 8: CNC the Honeycomb Pattern
After flattening the board was a little bit more than 5/8 thick. A 1/8 diameter and 1/2 long flat mill was used. The intention was to leave some solid material at the bottom.
More than 12,000 code lines and a few hours later the honeycomb pattern was done. I just had to play around with the CNC clamps to avoid them during machining.
Step 9: Clean Up the Machined Board
Compressed air was needed to clean up the deepest sections.
Step 10: Prepare for More Resin
I used simple masking tape to create temporary side barriers for the new resin.
This time I used white and a little bit of yellow to come up with a warm creamy tone for the honeycomb cell walls.
Step 11: Pour the Cell Walls Resin
Pour very slowly the resin. Remember to rise up the box so you have proper ventilation under the box, otherwise you will get a concave board that you will need to flatten later.
Step 12: CNC to Your Desired Thickness
I flattened both surfaces again up to the desired 1/2 inch thickness
Step 13: Sand to Remove CNC Tools Marks and Prepare for Wet Sanding
60, up to 600 grit sanding paper was used with an orbital sander. Then I used wet sanding pads.
Step 14: Micro-mesh Wet Sanding
The minute I started wet sanding the final board came to life !
Step 15: Build the Beehive Frame
I used a simple piece of lumber to have 4 sections (1x7/8) for the frame. The length was more than 13 inches for each sections. The table saw was used to create 1/2 dados for just 3 sections (2 laterals and the bottom).
Step 16: Finishing the Bottom Side
The lower section has 45 degree joints.
Step 17: Finishing the Upper Frame
With a table saw sled I cutted dados to complete the upper joints. You also need to cut the lateral sides to adjust the length.
Step 18: Upper Side Assembly, Using Screws
For the upper section I decided to use screws In case I had to remove the resin board from the frame to deep clean it, re-polish the resin, etc.
Step 19: Polish, Glue Up, Install Wood Screws
I glued up the lower 45 degree joints and installed 1 1/4 inch wood screws on the upper frame section.
Before using the board a food grade conditioner was applied to have a safe surface to contact the food.
Step 20: Have Breakfast on Sunday
That´s it, the bee hive serving board is ready !
Just remember it isn't a cutting board, as a sharp knife will dent the resin !
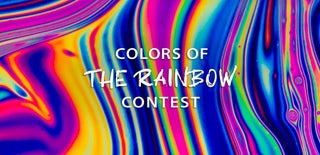
Fourth Prize in the
Colors of the Rainbow Contest