Introduction: Robotic Mechanical Spider
For my year 13 technology project I was tasked to make any project of my choosing for a stakeholder. I decided to design, build and implement a remote controlled mechanical spider, because, why not?
This project is an amalgamation of both complicated and simple components; from the relatively easy frame to a radio transmitter, electric motors and other miscellaneous components. I made the entire project using Autodesk Inventor Professional 2013 first and i will upload my CAD files if requested to.
This project was quite difficult to make I do not recommend undertaking it unless you are competent in a range of different workshop skills including electronics. Also it would make this project a hell of a lot easier if you had access to a water jet or laser cutter or something similar that is capable of automated precision cutting, as I did not and it took me a very long time to say the least (kind of the reason why I’m entering)
I am just a student and I’m sure that there are many alternatives for the different components I made such as the turning mechanism that would be a great deal easier than what I slaved over so any feedback would be greatly appreciated and feel free to chuck your own ideas into the mix and see what works out
The finished product skitters around like nobody’s business and is guaranteed to scare the crap out of any pet, large rodent or small child who happens upon it.
Materials - This project will require the purchase (or stealthy retrieval) of...
- 4 electric motor gearbox sets
- Two channel Transmitter and receiver
- Brush motor speed controller, at least 20 Amp
- A standard servo
- Wires for soldering
- 3mm x 50mm x 1meter aluminum bar
- 1.5m^2 of 3mm acrylic sheet of your desired color
- 1.5m of 5mm threaded rod
- 500mm x 5mm brass rod
- Tiny bit of brass sheet
- 250mm^2 of 20mm plastic for turning gears
- 100 mm of 15mm nylon rod
- 5mm rivets
- The largest pile of 5mm locknuts and washers known to mankind.
Tools
- Hand drill and drill bits
- Drill press
- Hacksaw
- Files
- Scriber
- Scroll Saw
- Superglue
- Soldering iron and solder
- Plastic bender (Or a hot air gun if you don't have access to one)
- Rivet gun with rivets
- Mill
- Belt sander
- Metal lathe
- Blow torch
note: please click on the images to view the annotations that match the text. I apologize for any blurry photos.
This is a link to my finished report which has a more in depth discussion of my project: if you have any intention of making this project i highly recommend reading it!!! https://docs.google.com/file/d/0B4EnwQ3Y1QiGSEhaUDVsbXFmUmM/edit
Also credit to my friend Ben Murton, https://www.instructables.com/member/benmurton/ , who was a great help with my first Instructable.
Step 1: Overall Concepts
* Frame
* Turning mechanism
* Legs
* Power Mechanisms
* Electronics
After that i interpreted my drawings and made a 3D model of what i envisioned the finished product to be like using Autodesk inventor professional 2013. Please note that if these drawings are overwhelming i will be breaking them down and going into detail for every component and how they work in the following steps.
The useful thing about being competent in Autodesk is that every project is saved in the .ipt format that a 3d printer can print. As such it is very easy to print any components that may be difficult to make using conventional methods.
Step 2: Frame
As seen in the provided pictures, the frame is of a reasonable size in order to accommodate the leg pairs. The large amount of vacant space that was left inside was extra area for me to have at my disposal if I need it, for components such as the battery, wiring, receiver etc. A large portion of this space was taken up by the power system and its mounting. The reason why it has the particular spiky shapes is for aesthetics, as these serve no advantage to the function of my project. the frame is the major component that will be noticed the most so in my opinion it has to look as good as possible.
To make it i printed out a 2D net of each half and glued it on top of a large sheet of 3mm acrylic plastic. Then using a scroll saw i cut out the outline and also some slots that allowed the middle sections to slot in to (see pictures) before hand filing off any excess plastic barbs and drilling holes for the different components to attach to. (This step will be a lot quicker if you have some form of laser or CNC cutter you can use instead of manually doing it by hand). After this i heated up the areas that needed bending using a plastic bender and bent the acrylic to the desired shape using wooden guiding blocks cut to the correct angle. Once this was done all that was required was to glue the middle pieces in place and the frame was completed.
Step 3: Turning Mechanism
I built a 3D model out of scrap wood for my initial design (obviously my final product would not be made of wood, though now thinking of it buoyant spiders are even more terrifying). It worked via the joining of two sides of a turning mechanism frame by a rod through two pivot points. One of these Pivot points was in the exact center of a single cog and the other was on the edge of the radius of the half cog (see images). When the half cog side was rotated then the teeth mesh and interacted which caused the adjacent side to move in the opposite direction, similar to a universal turning mechanism. However after several tests with this design and building a 3D model on the computer I found that this mechanism is constantly either jamming or coming loose. This is due to the fact that when the short side rotates there is nothing to stop it from keeping going, until it eventually separates from the single cog, losing all running movement with it until it is moved in the opposite direction.
Using what i found from my initial concept i developed on it and came up with a new idea. It featured a much more appropriate pivot point and the short frame is on the outside in this design. when built like this (as long as all of the gear teeth are proportionally sized and fit together well) it acted as a self limiter, as when the longer internal frame collides with the shorter frame during rotation it is forced to stop. This self limiting means that this module design functions perfectly as anticipated and matches all requirements for construction. I therefore found it appropriate and began construction. If you are making this project yourself i recommend my second more developed idea even if it is harder to make.
First i made two cogs out of 20mm acrylic plastic and drilled a 5mm hole in the center of each before cutting one of the cogs in half and drilling and tapping the full cog ready for a grub screw. After that i scratched a net of the turning mechanism onto sheet aluminum using a scriber and drilled holes in it. Once this was done i cut it out with a hacksaw, before bending it at right angles until the frame pieces of the turning mechanism were finished. After that i placed nylon in the metal lathe, drilled it out 5mm and parted it off at the desired length for it to be used as spacers between the cog and the frame. Also, because nylon is self lubricating it ensures a smooth rotation. Finally i bolted the half cog to the small side of the frame and ensured the teeth were interlocking on both cogs before using a 5mm brass rod to attach the two frame halves together and bolting everything in place. A grub screw was used to attach the large cog to the brass rod. Testing by rotating the large rod showed that the small side of the turning mechanism was force to move in response. (see picture)
Step 4: Legs
I didn't just want a project that walked on 8 legs. I wanted the leg movement to actually look like that of a spider and so i modeled it my design after a spider walking simulation. This method had two legs walking out of phase from each other by exactly half a cycle, so i translated this into mechanical moment by making my design out of 4 pieces, replacing each joint in a spiders leg with a pivot, redesigned it so the fixed points during movement were mounted on a frame and then came up with a method of powering the walking motion. Each leg had 4 pieces to it therefore 32 individual components had to be made (pictured)
To power it i tried to replace where in a spider a muscle would be with a wheel, and attach each leg 180 degrees from another. This would allow the legs to walk out of phase. However this raised another issue that as the circle rotated the legs would spin and immediately be jammed by the axle the wheel was on. This was solved by making a crankshaft design (pictured) that allowed for 360 degree rotation of both legs.
Once this crankshaft design worked on Autodesk inventor i set about making all of the leg components by hand.
Then i began construction of all 32 of the individual leg pieces. While I knew that I was going to cut these out of a 3mm aluminium sheet I was unsure of the method. A first i entertained the idea of using a plasma cutter to quickly cut them out however I had never used one before and I did not want to risk damaging the integrity of the legs. Instead what I did was this. I printed out actual sized 1:1 ratio shapes of all leg pieces and then stuck them to the aluminium sheet with an ordinary glue stick in groups of similar components. After roughly cutting out these individual pieces with a hacksaw ( a grueling task as there were 32 of them) I then drilled out all of the holes . This gluing step would not be necessary if you had an automated laser capable of engraving.
Now for the clever bit. I bolted all eight of every component together in stacks through their drilled holes and put them all in the mill together. I used this to neatly remove excess aluminium from the edges easily because of the nature of the machine. All that was left after completing this step was filing and sandpapering all the leg pieces to remove any sharps burs produced during this process and giving them an attractive shine. (Though i'm still unsure as to whether this shine is from the sandpaper or from all the blood sweat and tears i shed during this step)
Step 5: Rotational Power
I came up with three different ideas for the method to power the rotation for the legs, all using electric motors as i wanted to be able to control the movement remotely. I have posted all 3 to show alternatives to the method i actually followed through with if you want to try something different when making it yourself. They are as follows:
Sprocket (pictured)
While not a sprocket per se, this concept exhibits many similar features, thus the comparative name. My idea does not mesh on a belt to work like an actual sprocket does, but rather uses two belt less sprockets themselves which interact and spin the crankshaft at a 90 degree angle. This can be seen as a similar concept to a bevel gear. The reason why I didn't use a bevel gear for this concept is because they are expensive and comparatively it would take me relatively little effort to construct this idea myself to the same standard as a purchased item. However ultimately it is quite a complex design, prone to jamming if measurements aren't perfect and ultimately not an effective way of transferring momentum.
Belt (pictured)
In this option a belt is run between the powering electric motor and the crankshaft, therefore when power is applied the motor rotates, which in turn forces movement on the legs. For this concept to the work I would require a bendable high friction material to use for the belt itself, as well as a means to attach it to both sides of this system. Possibilities for these include lathing a small groove in the crankshaft to prevent slipping of the belt and making a nylon head piece that the belt slots into attached to the end of the motor. Cons of this method are expensive components, risk of slippage, constant lubrication needed, difficult to repair, requires very fine engineering skills.
Gearbox
This is the option i ended up following through with. For this concept the electric motor powers either a ready made or bought Gearbox. When the electric motor is turned on it rotates a certain number of gears (with a preferred gear ratio) which in turn spins the crankshaft. If the gear ratio is optimal then I will get a specified RPM which allows me to choose an ideal speed for the spider to walk at. The gearbox may not be attached to the crankshaft, and might act as one itself depending on the chosen product. Because the gear ratio is so vitally important to this design I ensured that I obtained a gearbox with ideal gear ratio.
Ultimately i bought 4 gearboxes to use (pictured). I did this because they came with built in electric motors and acted as crankshafts themselves so i did not have to make one myself, however this was most certainly the most expensive part of my project. Each of these gearboxes would be attached to the legs and also to the frame by a rectangular piece of acrylic plastic with some give in it which allowed the gearbox to move up and down instead of snapping off the acrylic it was glued to if the legs began to move too fast (pictures and a video of this can be seen later)
After the final picture of my assembled gearboxes i had to cut down the axle lengths so they would fit in side my frame.
Gearboxes i used: http://www.jaycar.co.nz/productView.asp?ID=YG2740
Step 6: Electronics
This circuit diagram is a very simplified version for understandings sake and does not include the electronics inside each of the major components.
The battery used for this project was a standard 8.4 volt rechargeable modelling battery. Using Kirchhoff's law (voltage splits in series) I could have used all 8.4 volts or split it and used 4.2. I chose to use this battery for a number of reasons, namely the fact that it is rechargeable which is very convenient for a toy such as this that will use power quickly, it is lightweight and therefore will not add much mass that requires moving, the plastic adapter fits with other radio equipment I have such as a speed controller and receiver and the fact that I never had to buy it, as it was a spare battery in my garage. While 8.4 volts ran the risk of burning out the motors i had no choice but to put them in parallel as putting each pair in series meant not enough power was being used and under the strain of the legs the motors would not rotate. So therefore when using my project i have to make sure not to use the throttle too violently or risk destroying the motors.
The servo is for providing movement of my turning mechanism and works as any regular servo would
The receiver takes the signal from the transmitter and sends it to both the servo and speed controller. It is this device that is synchronized to the controller and is what allows me to receive radio signals due to the built in aerial.
The speed controller is the central piece of this project and is what controls both the servo and the electric motors by limiting their rotation proportional to the amount forced upon it by the transmitter. It is attached to the battery, all four motors in parallel, the receiver and a switch.
Luckily i was able to use the receiver, transmitter and speed controller from an old remote controlled car as well as finding an appropriate battery which saved me a lot of money and allowed me to recycle old components.
Step 7: Assembly
Turning mechanism to frame
I mounted the turning mechanism on to the back of each frame piece using the holes in each i drilled earlier. I did this using 5mm bolts leading from the turning module which passed through holes on the frame and then though a 3mm aluminium square which was used as reinforcement to spread the weight evenly, if this is not done then there is a risk of the whole back face of the frame snapping off. These bolts were then attached with lock nuts and the turning mechanism was made secure.
Leg piece assembly
Now that the frame was fully assembled I started to attach the leg pieces together through their pivot points and then attach them to the gearboxes and electric motors. The leg components were attached easily enough with lock nuts and then attached in pairs to 4 individual gearboxes
Gearbox to frame
Now that the leg sets and gearboxes could fit inside the frame I was ready to start the mounting process. First of all I attached the leg pairs to my frame using the rods through the pivot pints, spacers and locknuts. After this was done the legs were fully assembled and exactly out of phase except for the gearbox hanging off the back. In order to secure this down I tried two different methods. The first failed for me but either would work if done correctly. Both methods involved using acrylic plastic to make a mount for the gearbox (pictured). It was made out of 3mm thick acrylic plastic cut out with a power tool and attached to the inside space of the frame with half of it overhanging under the gearbox. The thin side is where the motor would sit.
For the first method I believed that the legs would spin more effectively if I attached this mount halfway up the frame height. I built a supporting constraint in order for this idea to work. However after testing the leg sets with the gearboxes at this height the mounting actually snapped under the pressure generated. I realized that the reason for this is because by having the gearbox mechanism up high then a lot of the force usually transferred into the frame is conveyed into this small bit of plastic. Even though the legs moved faster this way it just would not work for me so for my second attempt i changed the height of the mounting. instead of raising it up I decided to attach it to the very bottom of the main frame. after attachment and initial tests this height worked perfectly for the project and the legs walk exactly as intended, albeit a little slower
Electronics
First of all I mounted all of my electronics and did all of my wiring (clearer pictures of this can be seen on the last step). On one side I had the switch, speed controller and battery and on the other the servo, aerial and receiver.
Before I attached the servo to my turning mechanism I had to make an appropriate mounting method for it. First of all I hack sawed out a small rectangle from a sheet of brass and drilled nine holes in it, four pairs of which emanated out from the central hole at specified distances. Next I secured the brass rectangle on the brass rod connected to the large cog and after ensuring that it was parallel to the back of the servo frame I soldered it with a blowtorch. Once this was attached I was then able to run push arms between both the servo and my crafted reaction arm.
After the electronics were all mounted I began to test them to see if everything worked as expected (pictured below) In the first test I used stretched out paperclips instead of the push arms to ensure that the system worked before risking more equipment.
With this proof that the servo works via remote control I was then able to physically mount the real push arms that I crafted out of acrylic. Tests of this mechanism as well show that it works perfectly as intended even with the full weight of both sides of my project attached.
Here is a video of a set of legs working.
Step 8: Finished Project
Over the course of this project there are several things I would have changed. Number one would be to make the legs and gearboxes first and then base the frame size around these measured distances. If I had of done this it would have saved me a lot of time which I spent fixing little errors and in my opinion would have aesthetically looked a lot better. Also access to a laser cutter or something similar would have sped up the progress of this project as well.
Overall i am very happy with the finished product and it is a hell of a lot of fun to use.
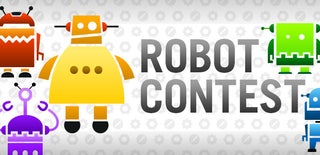
Runner Up in the
Robot Contest
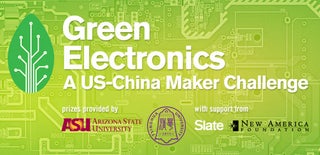
Participated in the
Green Electronics Challenge
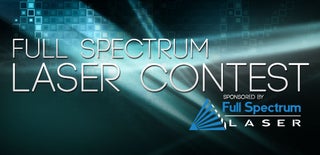
Participated in the
Full Spectrum Laser Contest