Introduction: Rotatable Custom Picture Lamp - 3D Printed Lithophane Lamp
If you've never seen a lithophane before, you're missing out on one of the coolest 3D printed projects in existence! They work by transforming pictures into 3D printable files where darker parts of a picture are printed as thicker areas and light parts as thin areas. Then, when the lithophane is backlit, the light shines through the thin areas more easily than the thick ones and the picture is revealed.
After I discovered lithophanes and had some fun playing around with them, I thought that they would make an amazing gift for any event, so I set about designing a lithophane that could be easily lit and displayed. I created this particular lamp as a birthday present for one of my closest friends who absolutely loved it. I was so pleased by how it turned out that I decided to make an Instructable for it so that others could enjoy them as well! I hope that you make a lithophane lamp for yourself or a loved one, and have as much fun along the way as I did!
Supplies
Tools
- 3D Printer
- Pliers
- Sandpaper (if needed)
Supplies
- White Filament (I used Overture White PLA)
- 4 W, E12 LED Light Bulb (I used the warm white)
- E12 Light Socket and Cord
- 3-5 Pictures of Your Choice
Programs
- Website Used to Make the Lithophane
- Autodesk Fusion360 (or another CAD program)
- 3D Printing Slicer (I used PrusaSlicer)
Step 1: Choosing the Photos
The first step is to choose the photos you want to use. I would recommend anywhere between 3-5 photos, depending on the size you want your lithophane, and the size or "cropability" of your photos. I went with 4 photos for my lamp. The process behind determining the correct number of photos for your lamp will be detailed more in the next step.
While photos with less detail and more contrast are typically better when making lithophanes, I've found that pictures that don't follow those guidelines still look great once printed!
Step 2: Creating the Lithophane
Go to itslitho.com (or another lithophane generator) and select the button "Get Started". This should take you to a 3D environment where you can design your lithophane. Select "Cylinder" from the drop down menu in the upper left. (Picture 1)
Before we insert the pictures, we'll want to define the dimensions of our lithophane. There are 3 ways of going about this:
- Locking the height of the lithophane. Type the height you'd like (in millimetres) into the box titled "height" on the left. This will ensure that your cylinder stays that height, and your diameter will then change according to how many pictures you insert and their sizes. Now upload your pictures using the "Upload" tab. Edit them using the "Edit" tab if you'd like. Return to the "Model" tab and make sure that your height is still the same. If it has changed, type in the number again. If your lithophane's diameter becomes too large, you can remove pictures or crop them to be shorter in width, which will decrease the diameter.
- Locking the diameter of the lithophane. Type the diameter you'd like (in millimetres) into the box titled "diameter" on the left. This will ensure that your cylinder stays that diameter, and your height will then change according to how many pictures you insert and their sizes. Now upload your pictures using the "Upload" tab. Edit them using the "Edit" tab if you'd like. Return to the "Model" tab and make sure your diameter is still the same. If it has changed, type in the number again. If your lithophane grows too tall, you can remove pictures or crop them to be shorter in height, which will decrease the height.
- Locking the height and diameter of the lithophane. If you want to control the exact size of your lithophane, you can fix both the height and diameter. To do this, you must turn on the setting "Crop" in the "Shape Options" box in the menu on the left. This will allow you to manually define the height and diameter by automatically cropping the photos you upload to fit the requested dimensions. You can also crop the photos yourself to fit your chosen dimensions if you want more control over which parts of the image are showing.
I used option 1 and locked my height at 5.5 inches (139.7 mm). I ended up with a corresponding diameter of about 4.5 inches (115 mm). Keep in mind that the larger you make your lamp, the longer it will take to print. At the size listed above, my lithophane took 24 hours to print. (Picture 2)
Now it's time to add the details! Scroll down through the menu until you come to the section titled "Frame Options". This is where you can choose whether or not you'd like to have a boundary along the top and bottom of your lithophane, and/or between the pictures. There are two options for doing this if you choose to include it:
- Frame. This is a raised line printed thicker than the rest of the lithophane, which will allow less light to pass through and make the line appear darker than the pictures surrounding it.
- Border. This is an unraised line that is flush with the face of the lithophane. It will not appear as dark as the frame and won't be as clear a divider.
Select your choice of boundary (Frame, Border, or None) from the "Frame" drop down menu and set the thickness of the lines as well as where they'll be placed with the settings below. I went with a 2.5 mm frame on the top, bottom, and between each picture with a 3.25 mm depth. (Picture 3)
The final setting to adjust is under the section "Quality Options". The setting is titled "mm Per Pixel" and will determine the quality and detail of your photos. It also has a large effect on the size of your file: The smaller the number, the larger the file. I've found that it's best to keep the file size between 300 and 400 MB in order to ensure that your slicer can properly process it. Increase (or decrease) the mm per pixel number until it says that your file will be between 300 and 400 MB. I used 0.115 mm per pixel and my file was around 370 MB. (Picture 4)
Finally, view your model in the 3D viewing environment. Adjust the settings until you're happy with how it looks, and then hit the "Download" button in the lower right corner. Click the "Lithophane" button when it appears to download your lithophane! (Picture 5)
Step 3: Slicing the Lithophane
Import your STL file into your slicer (I used PrusaSlicer). Orient the lithophane so that it's bottom flat side is touching the buildplate. (Picture 1)
Next, choose your layer height. The smaller the layer height, the better your lithophane will look, but your print will also take longer. You can slice at a few different layer heights to see how long the print will take in each case. I ended up going with a 0.2 mm layer height, which resulted in a 24 hour print and great quality photos.
Another important factor to consider when printing lithophanes is that they must be printed completely solid as the light shining through will show the pattern of any infill if it is used. To do this, open your print settings and change your number of perimeters to 22 (or some other large number). The number of perimeters will be thicker than the model itself, and the slicer will print as many as it can fit in the model. This will result in your lithophane being printed completely solid, and give the best results when light shines through the photos. You can also do this by changing your infill to 100%. (Picture 2)
I'd also recommend using a brim to help keep your print adhered to the build plate. This will help prevent warping and detachment from the bed, which can be an issue on long prints such as this one. I used a brim that was 5 mm wide, which is the default for my slicer.
Feel free to fiddle around with your slicer settings to get your lithophane to print just how you want it. I'd recommend quickly scanning through all of the layers to ensure that nothing seems wonky or out of place. Once your happy with your model, you can slice it and save the gcode! (Picture 3)
Step 4: Printing the Lithophane
Before starting your print, I'd highly recommend cleaning off your bed, as long prints can sometimes detach from the print surface if it's dirty. If this happens, it will likely ruin your entire print! I used 99% isopropyl alcohol to clean my bed, and additionally applied glue stick to my print surface before printing just to ensure that my lithophane would adhere well. (Picture 1)
Once your build surface is ready to go, you can load your white filament into the printer, upload the gcode, and print! Make sure to check on it every few hours to ensure the print is still running smoothly. (Picture 2)
Step 5: Designing the Base: the Bottom Piece
Now it's time to design the base! I designed this base to be able to rotate so that you could see all of the pictures, lock to the lithophane as one piece but also be detachable, and keep the cord in the back and make it less visible.
If you choose to design your base the same way I did, it will have two separate pieces: A bottom piece with a bracket for the light, and a top piece that will rotate the lithophane while on top of the bottom piece. We'll be designing the base so that the lithophane is locked on top of it, but can be easily removed by aligning the top and bottom pieces in a certain way. If you want to see an example of how the mechanism will work, check out the video in Step 12. First, we'll be designing the foundation of the bottom piece.
Open Fusion 360 (or your CAD program of choice) and start a new part. Create a new sketch on the XY plane. Measure the outside diameter of your lithophane (this should be the diameter of your lithophane given to you by the website plus the thickness of your frame) and sketch a circle with that diameter. Finish the sketch. Extrude that circle 0.315 inches (this will be the thickness required by the bracket if you are using the same light socket and design as I am). (Picture 1, Picture 2)
Start another sketch on top of the flat face of the cylinder. Project the geometry of the face you are working on so that you have the circle outlined. Using the "Offset" tool, select the projected circle and offset it inwards the thickness of your frame/lithophane plus 0.25 inches. Finish the sketch. Select the inside circle and extrude it 0.197 inches. (Picture 3, Picture 4)
Next we will be adding the prongs that will lock the top piece in place. Start another sketch on top of the flat face of the smaller, top cylinder. Project the geometry of the face you are working on so that you have the circle outlined. Sketch a rectangle at the top of your circle, so that roughly half the rectangle is on the face of the circle, and half is off. Dimension the rectangle so that it is 0.35 inches in length by 0.315 inches in width as seen in picture . Use the "Horizontal/Vertical" constraint while holding shift to constrain the midpoint of the longer side to be in line with the midpoint of the circle/face you are working on. Then, use the "Coincident" constraint while holding shift to constrain the midpoint of the shorter line to be a point on the projected circle. Finish the sketch. Select the rectangle you have sketched and extrude it 0.079 inches upward (so it is a slab on top of the circle). (Picture 5, Picture 6)
Now we'll be adding in a small wall which will act as a built in support. This will make it so that supports won't be required when printing and will be removed much more cleanly than a typical support structure. Start a new sketch on the bottom face of the slab you created (the closest parallel plane to the top face of the large cylinder). Check the "Slice" box in the menu to the right so that you're able to see the plane you're working on. Project the face of the rectangle/slab that you are working on. Sketch a rectangle that shares a side with the short side of the projected slab, and aims inward towards the base. Dimension it to be the same length as the side it shares, and 0.3 mm wide (or just slightly smaller than your extrusion width. Mine is 0.4 mm). Finish the sketch. Select the small rectangle you just sketched and use the "Extrude to Object" setting in the extrude tool. Select the top face of the large cylinder as the "Object" face.(Picture 7, Picture 8, Picture 9)
Add a 0.1 inch fillet to the top inside edge of the slab. Select the slab feature, built in support, and fillet using the "Circular Pattern" tool. Then, select the rounded face of the small cylinder as your axis, and input 3 as the quantity of times you want the pattern repeated. (Picture 10, Picture 11, Picture 12)
Step 6: Designing the Base: Adding the Bracket
Next it's time to add the bracket that will hold the light socket in place! I highly recommend purchasing the exact light socket I have provided the link for in the introduction as I've designed the bracket to fit that socket perfectly. The socket I used has flexible metal "wings" with small cutouts, and I designed the bracket to be a hole with small pegs that fit into the cutouts and lock the bracket in place. If you have a different socket, you will need to find another way to design a bracket. (Picture 1)
Create a new sketch on the top face of the small cylinder. Project the geometry of the face you are working on so that you have the circle outlined. Sketch a rectangle measuring 1.083 inches in length by 1 inch in width. Use the "Horizontal/Vertical" constraint while holding shift to constrain the midpoints of both sides of the rectangle to be aligned with the projected circle's center point. Finish the sketch. Extrude the rectangle so it cuts through the entire base. (Picture 2, Picture 3)
Create a new sketch on the top face of the small cylinder. Make sure that your model is oriented so that the longer side of the rectangle (measuring 1.083 inches) is at the top. Project the geometry of the face you are working on so that you have the circle and rectangle outlined. Starting in each corner of the large rectangle, draw four smaller rectangles measuring 0.138 inches in length by 0.269 inches in width. Finish the sketch. Extrude each of the four smaller rectangles down (so they connect with the old model) 0.177 in. (Picture 4, Picture 5, Picture 6)
Next, we'll add in a sacrificial bridge, so that the four small rectangles don't require support structures when printing. This will be a small, one layer thick bridge that will support the rectangles above and be easily cut away after printing. Use the view cube to orient the model so you are viewing the bottom. Create a new sketch on the bottom of one of the four small rectangles. Project the geometry of the four small rectangles. Sketch a rectangle between the short ends of each pair of rectangles. Finish the sketch. Extrude the two rectangles you've drawn upward (so they connect with the four small rectangles) 0.15 mm (or whatever layer height you choose to use when printing). (Picture 7, Picture 8, Picture 9, Picture 10)
Step 7: Designing the Base: Adding the Plug Tunnel
Now we'll add a tunnel for the plug to travel through within the base so that the cord doesn't rest uncomfortably underneath it.
Create a new plane, parallel to the face corresponding to the long side measuring 1.083 inches of your large rectangle, and tangent to the large cylinder of the base. Start a new sketch on the plane you just created. Project the rounded face of the large cylinder. Sketch a rectangle measuring 0.315 inches by 0.217 inches and constrain it using the "Colinear" constraint to be on the same line as the bottom of the base. Then, use the "Horizontal/Vertical" constraint while holding shift to constrain the midpoint of the long side (measuring 0.315 inches) of the rectangle you just drew to the midpoint of the projected rectangle's long side. Finish the sketch. Select the small rectangle you just sketched and use the "Extrude to Object" setting in the extrude tool. Select the closest plane of the large rectangle/bracket hole so that the new hole cuts through the base until it hits the bracket. (Picture 1, Picture 2, Picture 3, Picture 4)
Use the view cube to orient the model so you are viewing the bottom. Start a new sketch on the bottom face of the large cylinder. Project the geometry of the face so that the circle and tunnel are outlined. Sketch four small rectangles along the edges of the projected tunnel rectangle. The rectangles should share one side with the tunnel edge, and then aim inwards towards the tunnel. There should be two rectangles per tunnel side, with the end rectangles touching their corresponding end of the tunnel. Dimension the width of each of the small rectangles to be 0.148 inches, and dimension the distance between each rectangle to also be 0.148 inches. Use the "Equal" constraint to constrain all of the lengths of the rectangles to be equal to each other. This should leave you with a tunnel for your cord to snake through, with pegs of equal size to trap the cord in the tunnel. Finish the sketch. Select the four rectangles you drew and extrude them upward 0.079 inches. (Picture 5, Picture 6, Picture 7, Picture 8, Picture 9, Picture 10, Picture 11, Picture 12)
Congratulations! The bottom piece of your base is now complete!
Step 8: Designing the Base: the Top Piece
Now its time to model the top piece! This piece will have holes that match up with the pegs of the bottom piece. The top piece will slide onto the bottom, and then just barely underneath the pegs, allowing it to rotate, and only be detachable when the pegs and holes are realigned.
Create a new part. Start a new sketch on the XY plane. Sketch a circle centered on the origin with a diameter equal to the diameter of your lithophane. Use the "Offset" tool to sketch another circle within the first one, offset by 0.25 inches minus 0.15 mm. (You may need to adjust this value later after a test print, depending on your printer's tolerances.) Finish the sketch. (Picture 1, Picture 2)
Start a new sketch on the bottom face of the ring you previously extruded. Project the geometry of the face you are sketching on so that the ring shape is outlined. Sketch a circle centered on the origin with a diameter equal to that of the large cylinder of the bottom piece of your base. Finish the sketch. Select the ring and the outer circle and extrude them downwards 1 mm. (Picture 3, Picture 4, Picture 5)
Start a new sketch on the top face of the small ring. Project the geometry of the face you are sketching on so that the ring shape is outlined. Sketch a rectangle near the top of the circle measuring 0.375 inches by 0.164 inches. Use the coincident constraint to constrain both bottom corners of the rectangle to lie on the inside circle of the ring. Finish the sketch. Select the rectangle you just drew and use the "Cut" and "All" settings in the extrude tool to cut a rectangular hole completely through the base.(Picture 6, Picture 7, Picture 8)
Select the rectangular hole using the "Circular Pattern" tool, and select the rounded face of the small ring as your axis. Input 3 as the quantity of times you want the pattern repeated. (Picture 9, Picture 10)
Congratulations! The top piece of your base is now complete. You're ready to print!
Step 9: Slicing the Bottom Piece of the Base
Import your STL file into your slicer of choice and slice with whatever settings you prefer (I used a 0.15 mm layer height). Keep in mind that your choice of infill pattern will show through the bottom of the lithophane when turned over and the light is on. I used the cubic infill pattern and I really like the triangle pattern it got me, but feel free to use whatever pattern you like best. If you don't want to be able to see the infill, you can try increasing the top and bottom layers, and/or changing the infill to 100% or the perimeters to 1000. (Picture 1, Picture 2)
Also make sure that the sacrificial bridges and built in supports are going to print correctly. The sacrificial bridges should appear as one layer thick bridges. If they are more than one layer thick or not printing at all, go back to the model and edit the thickness of the bridge until it slices correctly. The built in supports should show up as one layer wide walls. If they are more than one layer wide, go back to the model and decrease the width of your wall until it slices correctly. If they are not showing up at all, turn "Detect Thin Walls" on, or go back into the model and increase the width of your wall until it slices correctly. (Picture 3, Picture 4, Picture 5, Picture 6)
Once you're happy with your sliced model, you can go ahead and send your gcode to the printer!
Step 10: Print the Bottom Piece of the Base
Prepare your printer and print surface, and print your base! (Picture 1)
When the print is complete, use pliers to remove the sacrificial bridges and built in supports from the piece. Use sandpaper to smooth any bumps or residue the plastic may have left behind if necessary.
Step 11: Print (and Reprint) the Top Piece of the Base
Slice your top piece with using whatever settings you prefer (I used a 0.2 mm layer height and cubic infill) and print! (Picture 1)
When the print is complete, slide the top piece onto the bottom to test whether or not the clearances are correct. If the piece is too tight or loose in some areas, go back to the model and edit the corresponding area by a few tenths of a millimeter. Then reprint and test the fit again. Repeat this process until the top piece slides easily over the pegs, rotates smoothly on the base, snaps in tightly to the bottom of the lithophane, and doesn't wiggle too much in any direction.
Step 12: Assemble
First, insert the light bulb into the socket. Squeeze the metal wings of the light socket together to make the socket as small as possible. Then, slide it through the bracket hole in the base through the bottom, making sure that the cutouts align with the pegs and the cord with the tunnel. The wings should snap perfectly into place and the socket will be locked into the base. Now, thread the cord through the pegs of the tunnel. (Picture 1, Picture 2, Picture 3, Picture 4, Picture 5, Picture 6)
Snap the top piece of the base into the bottom of the lithophane. Then, place the lithophane and top base piece over the bottom base piece, aligning the pegs and holes so the top piece slips over the bottom. Rotate the lithophane so that the mechanism locks it and the top piece on top of the bottom piece. (Picture 7, Picture 8, Picture 9, Picture 10)
Step 13: Plug It In, Step Back, and Enjoy!
Congratulations!! Your lithophane is now complete! Plug it in and show it off to everyone you know.
Thank you for reading my instructable! I hope you enjoyed this project as much as I did! If you have any questions, feel free to leave a comment. Have a nice day! :)
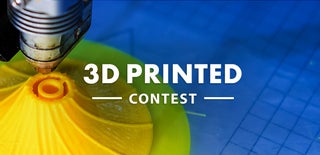
Participated in the
3D Printed Contest