Introduction: Router Plane System
I know there are a number of flattening sled Instructables and on other sites. The design presented here is different in a number of significant ways, mainly its versatility and storage foot print. Most of the Router Planer jigs I've seen are permanent builds made of wood and large enough to be a nuisance when not in use – this thing could literally be kept in a drawer in your shop.
The concept was to build a Router Planer system that would not consume valuable floor space when not in use, would be adjustable to used on virtually any size material and provide flexibility to reconfigure the system for specific uses.
One of my goals was to use as much recycled content as feasible (not out of some lofty environmentalist ideals; but, more for the goal of building this thing as inexpensively as possible, which many times comes through re-purposing other items). That it has a positive environmental impact is a bonus.
Hopefully, as we walk through the development, construction and use of the system, you will see it's applicability to many uses, such as: board flattening, thickness planing, slab processing, beam making, etc.
Step 1: Materials
Initially, bed frame “L” steel was envisioned for the box frame, these would provide a flat and stable base to slide the router sled across, that wouldn’t be susceptible to nicks and gouges or environmental changes and could be taken apart easily. I scoured CL for a couple of weeks to find free or almost free bed frames; but, was foiled when I didn’t seem to be able to respond quickly enough to those “free” postings. I decided to head down to my local thrift shop, thinking they may have an old bed frame or two for this purpose. I learned they don’t take anything associated with beds, other than linens.
While I was there, I poked around a little - you never know what you’ll find – I sometimes pick up distressed furniture for next to free to harvest hardware from them and re-purpose the wood. If I don’t keep in mind what I’m there for, I can leave the place with another four or five projects!
While wandering, I found an over-the-toilet shelving system (~5’ tall x 23” wide x 9” deep) that looked like it might have some value for something. Then it struck me that this might be a sound alternative to the bed frame metal, and will be a heck of a lot lighter. The pieces are all straight, and many cut to lengths I could use. Another factor, the cross pieces had nuts embedded into the ends of the bar stock to which should allow me to attach and square the unit without corner bracing. These had held the shelving unit upright over someone’s toilet for some period of time, so the strength should be sufficient to keep it square if I’m not torque-ing on it in use. This thing cost me less than $10 – comparable raw steel tubing would have cost at least double that.
Materials:
5/8” square steel tubing
¾” Angle Aluminum
#10 bolts, washers, nuts
3/8” threaded rod (2x6’) ($10)
Wing nuts, washers, nuts for 3/8” rod ($5)
Plastic cutting board
Tools:
Screw driver
Wrenches
Bolt cutter
Hacksaw
Rototool with cut-off disks
Flat/rounded files
Vise
Drill press, drill bits, hand drill
Router and bits
Draw knife
Broom, dust pan and shop vac
Safety Equipment:
Respirator
Hearing Protection
Dust collection
Eye Protection
Flip Flops
Step 2: Preparation
When I got the thing home, I disassembled it and laid out the components to see what I was really working with; many of the components were welded together. I went to work with my trusty bolt cutter, hacksaw, roto tool and flat file.
Step 3: Engineering
After cleaning up the components I started to piece the thing together, and quickly realized that the joints in the bar stock in the middle of the horizontal runners was not stable enough to hold the components flat and true. I needed to stabilize those joints, or my $10 investment in this steel tubing was wasted.
I thought aluminum angle metal was the way to go and ran out to pick up a two foot section. Unfortunately, the aluminum had too much flex, due to the extension on either side of the joint and had to be abandoned for the upper rails. I was thinking about running out to get some angle steel, when I remembered the “waste” material I had hacked out of the shelving frame. Bolting the steel I had cut out when liberating the longer sections across the rail joint provided the needed rigidity - looking down the assembled rails showed them to be dead-straight. Since I had fitted both the upper and lower rails with the aluminum, I left the aluminum in place on the lowers, as those won’t have any vertical stress on them and may add some horizontal stability.
Step 4: Frame Assembly
The frame assemble with only the addition of two new holes, and used the original screws from the shelving unit, except to attach the stabilizing pieces, at the joint in the rails. Consideration for this part of the assembly was to have a completely flat surface on the top and inside of the upper rails, to not interfere with movement of the sled (more on that later).
The back side of the original unit was about four inches taller than the front, so one of the frames (bottom) ended up being longer than the upper. I could have trimmed the longer pieces; but thought that the added length might provide a little additional strength to keep from bending the frame due to the leverage amplified by long risers.
I lined up the upper and lower (with the aluminum) frames to determine where to drill the holes for the risers, disassembled the frames and drilled holes on the drill press, working up to 3/8".
Step 5: Building the Sled
Since the shelving unit was built with the shelves inside the vertical components (now my horizontal rails), the shelves were already sized to fall between the rails.
I cut out the wire mesh between the cross members with the bolt cutter, filed them and then used two more of the remaining short cut-off sections from the disassembly for the ends of the sled. The distance between the long sides was measured to fit my router base well and allow freedom of movement.
Since the long sides of the sled are the same width as the ‘box’ the ends of the sled will sit directly on the top rails of the box. To help reduce friction when the sled is on the box, I used thin strips cut from an old plastic cutting board (another thrift store find); it doesn’t matter how thick these are, as long as they are the same. A plywood base was attached to the sides (only) and the plastic strips attached to the runners using epoxy and also screwed the plywood to the frame. I hit the plastic sliders with 220 sandpaper to remove any ridges allowing a smoother ride down the rails.
The sled was now ready for my router – almost. I have a 2” flattening bit for my router, with a 2” shaft extension. I didn’t want to modify one of my factory parts for the router so made a sub-base specifically for this bit. From the same cutting board, I cut a square to fit the router diameter, then cut a 2” hole through the base with a hole saw on the drill press. This is an easier task in concept than execution, as the plastic melts and gums up everything pretty quickly. This melting property actually turned out to be a benefit, as the 2” hole turned out to be a bit larger – enough to accommodate the 2” bit without interference. You’ll need to do a little clean-up on the hole to remove the solidified plastic blobs, a knife, file and sandpaper do the job in short order. I left this base square to keep it from twisting on the sled – I don’t know if this is helpful or not, the router will stay in it’s orientation; but, I won’t be able to turn it for comfort during use, it’s a matter of preference I suppose..
Oh, and there’s another thrift store treasure. I picked up this adjustable light for $4 and clamped it to the bench between the drill press and bench band saw. It swivels and adjusts to work for both.
I’m not overly concerned with seeing the router working the wood for this application, so the opaque plastic and plywood sled are OK here. There’s a big slot in the sled to see what has happened, and this is not detail work.
Here, I'm going to jump ahead a little, while we're talking about the sled build... During the first couple of test passes with the system, I noticed the upper frame was spreading outward in the center. This was fixed by attaching angle aluminum to the sled, to keep the lateral forced from dropping that 2” flesh destroyer, unexpectedly. The overhang is just enough to keep the sled on the tracks. I should probably mention the plastic runners work great for reducing friction, the sled will slide from one end of the box to the other with just a 12 inch incline – waxed rails don’t hurt either.
Step 6: Risers
I purchased two six foot 3/8-16 threaded rods for use as the risers. Initially, I had planned for four 2’ risers (on the corners only). After assembly and putting the weight of the router onto the sled, I decided to put another set of risers at the joint of the horizontal sections (the middle) to eliminate potential sag. (It’s inevitable that at least some body weight is going to provide some additional downward force). I cut four 1” x 3” pieces from some old steel framing brackets I had from a deck project. These were drilled to attach to the frame reinforcements in the middle of the rails on one end and to fit the riser rods on the other ends. These sit outside of the main frame to all the sled to move the entire length of the box without interference.
I used hex nuts and washers to attach the risers to the lower frame and out-riggers (one nut and washer set below and one set above) – tight but not crushing, and a set of wing nut and washer above and below the rail frame on each riser for height adjustments and leveling when the system is being set up to use. The wing nuts at the top corners also serve as stops and keep the bit from coming in contact with the frame.
As mentioned previously, I had applied wax to the sled runners, I also applied a couple of coats to the upper frame rails to help things slide around more freely.
Step 7: The Test Subject
For demonstration purposed for this Instructable, I went out to my wood pile to grab a log to work. As there is still snow on the ground and puddles almost everywhere else, I selected one I could easily get into my basement shop. I point this out as one of the intended uses of this sled system is to take it to where the wood is outside and let the sawdust and chips stay out there and not in the shop. This process makes a big mess!
The log I chose was ~2’ x 10” and had been cut long enough ago that it was starting to show some evidence of deterioration. Before doing anything with an expensive router bit, I used a draw knife to remove nearly all of the bark from the log – a couple of reasons for this, first to remove the potentially bit damaging crud that lives in bark (the draw knife is easy to sharpen) and second, to try to minimize the number of little critters living in the bark from being flung into all the hard to reach places in my shop. The draw knife cuttings were swept up and taken out to the firepit as soon as I finished debarking, the bugs were starting to wake up in the heat of the shop, so out they went.
Step 8: Setting Up the System
Getting to the point of the project...
First things first, you need to stabilize the stock when working on it. I screwed together a couple of scraps to cradle the log and keep it from wobbling.
After stabilizing the stock, you will need to lower the upper rails to just above where you will engage the wood with the router by spinning the lower wing nuts down (or up) to support the rails at the desired level. Use a long level to span across two points and lock those into place, tightening the upper wing nuts; then level the rest of the rails from there. It is important to make sure that all connections are tight, to minimize wobble and tilt - double check the riser feet and end bars, immobilizing each of these junctions. The set up presented here is surprisingly stable, even with the upper rails at the full two feet elevation. I was prepared to put some braces in for side to side forces; but, found they weren't needed, they could be easily added if it adds a level of comfort.
Step 9: Turn on the Router and Start Making a Mess!
Set your plunge router to take about 1/8" off for the first pass or two, it helps to get a feel for how the whole thing works together. HOLD ONTO THE ROUTER and never start up in contact with the wood!
Have some patience with planing, trying to cut deep will stress your router and may cause the router to run or the stock to shift unexpectedly. I found I could cut about ¼ inch at a time as long as I worked from the outside toward the center and taking ½-1” passes – not more than ½ the width of the bit. If you start out in the middle (like cutting a dado) you may run into some shifting and control issues, depending on your depth. I used the plunge base for my router, to let me make multiple passes on the log before having to adjust the risers and level the rails again. I’ve found that the bit extension is also helpful for this – providing greater reach below the bottom of the sled.
If your rails are level with each other and your stock is immobilized, you will end up with a nice flat surface after a couple of passes.
Step 10: Squaring the Stock
When you get to a point where you don’t want to take any more off of this side, flip the log over and set it directly on you base surface (floor in this case), you don’t need the anti-roll contraption for this step, though you may want to add a friction pad or otherwise keep the log from sliding around. Be sure to sweep or vacuum up the accumulated dust so the log sits level.
When you have the ’top and bottom’ of the log flattened, it’s time to move onto the sides. I used a simple set up to keep the log oriented nearly square when making this next cut. Take a couple of 1x6 pieces and clamp them to either side (flats) of the log and adjust until it sits square to the floor.
After a couple of passes on the ’side’ I checked for square – pretty good for all the way around.
You could continue with this process to make beams or dimensional lumber of any size you like. I’m not sure what I’m going to do with this log, so I stopped here, at least it will be a lot easier to work with on saws at this point.
You may be wondering about the 'other' log popping up here and there in the photos...When I started this Instructable, much of my wood was still frozen in place. The weather has warmed enough that a piece I've had designs on was ginally free to play with. This is a piece of a large buckthorn (as buckthorns go) I cut down last summer. (Yes, this is the same buckthorn that is a scourge in the US). I had cut up a few pieces previously and found the wood to be spectacular. The picture in this step shows the color and grain - my intention is to this piece into chair rockers, using the natural curve of the grain instead of trying to bend the wood.
Step 11: Scalability
The overall length of the full system set up requires a lot of space to work on long stock. I have this designed to allow assembly of only half of the unit, making working with smaller projects like checker boards, cutting boards, etc. a bit less cumbersome. Also, after working with the 2’ long threaded rods, I realized I won’t want to spend 5 minutes spinning wing nuts into position for low profile work – and then to back them off for disassembly. One nice aspect of this set up is that you can have a variety of riser rod lengths for very little money. Here, I show the half unit set up with carriage bolt risers and also with a second set of threaded rod risers (this set cut to 12") – this is likely how I will use it most often.
Using the 3/8" - 16 threaded rod(16 turns per inch) provides a great amount of accuracy when making finishing passes, turning the wing nuts just a quarter turn moves the sled 1/64".
This full set-up will accommodate some large logs – 2’+ in diameter and 5’ long and allows expansion to whatever length or width project - acquiring extension rails and additional risers won't be a big challenge nor expense considering the cost of lumber.
Step 12: Cautions
I'll assume you all know the basic precautions of working with power tools and specifically routers.
When milling wet or green wood, pay attention to your bits and blades, they tend to get fouled fairly quickly, you may want to build time into your projects to take care of your tools to help them stay sharp longer. I've had great success with soaking for 20-30 minutes in a 1:3 dilution of SimpleGreen and then using a tooth brush to scrub off the blades and bits; you may need a longer soak if the resins got baked onto the blades.
Another serious obstacle to staying sharp (and safe) is the presence of foreign objects in the wood. Working with wood that was harvest from urban/suburban areas - or anywhere people may have hung something on the tree - means that you will encounter nails, screws and other things that may have been attached to the tree at some point and grown over. These two pictures of buck thorn show the discovery of a screw after taking over a half inch off the log.
I've found rocks grown over and embedded in root wood and crotches where two trees have fused near the ground.
Step 13: Final Thoughts
This simple sled system proved to be easy to make, and not overly time consuming. Given the constraints I placed on myself at the beginning, the overall cost of this tool was around $30 including the shelf unit, threaded rod, washers and nuts. When the weather warms and I can get outside a bit more, I'll apply a coat of paint to make it look a bit nicer and protect against rust.
When the component part were all assembled, I wrote numbers and letters on the mating parts with permanent marker to make reassembly a bit easier and to ensure the proper orientation of the parts.
Assembly and disassembly requires one phillips screw driver, and three wrenches. My first timed assembly of the entire system from storage took about 20 minutes. It will take less next time. The half unit is much quicker.
Storage for the entire thing is a minimal and the total weight is around 10 pounds. The ruler in this photo is 16” for scale. It will fit into a long drawer or I might just put a strap on it to hang from a wall – however its stored, it will be easy to keep it out from under foot.
Not everyone will be able to find and re-purpose an old object for this type of build. If you build this from new steel tubing, you could use small (#10) threaded rods to secure the box ends to the rails, put the rod through the inside of the end tubing and through holes drilled into the rails, secured with nuts; or you could just drill a few more holes and bolt the components together. You can get by with smaller steel tubing if you use the outrigger concept on the corners as well as the center supports - you'll likely need corner braces to keep things square. Electrical conduit may offer a viable alternative to square tubing, try it an let me know how it goes.
If you actually read the Safety Equipment listed at the beginning, you may have caught my feeble attempt at humor - please do not wear Flip Flops when working with this stuff; common sense goes a long way in keeping you safe and healthy. I probably don't need to mention it; but, I accept no liability for any injury or damages caused by trying to make one of these - if you're not comfortable with it, don't do it.
Thanks for reading. If you recognize the utility and flexibility of this system, please let me know. If you do choose to build one, please share pictures and descriptions of the modifications you make. I'm sure this creative group will find many ways to improve this design.
Step 14:
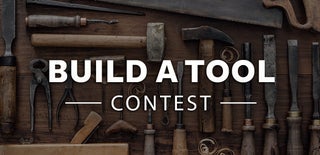
Participated in the
Build a Tool Contest