Introduction: Rubberwood Furniture
we were asked to build some massive tables (4meter by 1.2 meter) with added benches and a wardrobe with sliding doors.
I decided to use the festool domino connector system and not screws or glue for the simple reason that all of the tables/benches/wardrobe had to be easy to assemble and disassemble. the choice for rubberwood is because it's a very sturdy pressurised wood and it's a whole lot cheaper than it's oak counterpart (I still prefer to work with oak but rubberwood does have it's advantages)
materials:
- rubberwood (4,5meter by 1.2 meters 30mm)
- about 200 festool connectors and domino's
- black mdf (3.05 meter by 1.2 meters 18mm)
equipment:
- track saw
- table saw
- festool domino xl df 700
- glueclamps
Step 1: Sketch Up
as always I started by making the drawings in sketch up to get the measurments right and making a cut list.
Step 2: Understanding the Festool Domino Connector System.
go online and brush up on how this system actually works. Once you got the hang of this system it's actually straight foreward.
there are other system like this on the market like the one from lamello or you could try to make these kind of projects with pocket holes and screws but I decided to use the festool system because it looked the sturdiest and i already had the festool df 700 Xl so for me it made sense to use this.
one of the things you need to keep in mind is the thickness of your wood when you decide to use this system. The DF700 works with fixed positions in height (15mm, 20mm, 25mm,30mm, 40mm) this translates into using thickness of wood muliplied by 2 so: 30mm, 40mm, 50mm, 60mm or 80mm thick wood pieces. Any other thickness will give you a massive headache and numerous mistakes in positions. the wardrobe in this instructable was made in 33mm thick rubberwood, so I know what I mean with headache...
Step 3: Wardrobe Bottom and Top
after cutting up all the pieces we needed for the wardrobe it was time to start drilling all the holes with the DF700xl.
I put the base and top of the wardrobe alligned to each other and started drilling all the holes for the upright pieces.
Step 4: Wardrobe Uprights
once the bottom and top pieces had all the necessary holes drilled it was time to prep the upright pieces and do a test fitting.
Step 5: Cut Outs for the Sliding Doors
before doing a complete testfitting I stil had to make cut outs for the sliding doors. You can use a track saw or a router to make these cut outs. The doors themselves are 18mm thick so the cut outs I made are 20mm wide to make sure the doors have enough room to slide.
Step 6: Testfitting the Wardrobe
once all the cuts and holes were made, we testfitted the whole wardrobe to see if everthing worked and could be assembled/disassembled easy. It worked out just fine.
Step 7: Finishing the Wardrobe
once the assembly/disassembly process was easy enough we could put the wardrobe in place and added the sliding doors (which are just sheets of black mdf).
the whole assembly proces is done by 2 people and takes up about 20min. Same goes for the disassembly
Step 8: The Tables and Benches
again the first step was to cut all the parts for the tables (4) and benches (8)
Step 9: Drilling the Holes for the Tables and Benches
nothing glamorous here, just measuring a lot drilling a lot of holes. main tip here is to stay focused when measuring and drilling. It's very easy to make a mistake in this part of the build the you will only notice when testfitting.
Step 10: Adding Supports to the Tables and Benches
after the first testfitting it became very clear the additional supports would be needed to make both the tables and benches extra sturdy.
Back to the drawing board to make same triangle supports and adding those to the tabels and benches. This meant some more drilling and measuring...
Step 11: Testfitting Succesful
once all the supports were put in place the tables and benches clearly benefitted from the added supports.
Step 12: Quick Overview Before Disassembly
just a few overview pictures before we disassembled everything...
Step 13: Reassembling the Tables and Benches
same as for the wardrobe the assembly of the tables and benches in their place.
1 combo (1 table and 2 benches) takes up about 30 min to assemble/disassemble with 2 people.
Step 14: Final Thoughts
most important:
- when working with the festool connector system, use set thickness of wood (30,40,50,60 or 80mm).
- the cost of the wood was kept down because we used rubberwood instead of oak.
- the festool connectors are expensive. the hardware for all the projects (4 tables, 8 benches, wardrobe) was about 2700 euro, but keeping in mind that we will be using these tables for various projects the cost will be worth it in the long run.
- the main focus of this projects was the easy assembly and disassembly of the furniture (along with a modern design)
- this is not a 1 man project. It took a team of 4 people to work on this project for about 3 weeks
- the finishing of the tables and benches is a matt hardened varnish
- no video from the build, because I simply don't have the equipment to film/edit/... big fan of those who do though.
don't hesitate to ask me questions if you have any.
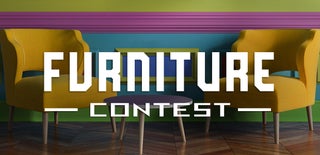
Participated in the
Furniture Contest 2018