Introduction: SHALLOW SPACE TRUSSES FOR ANALYSING SNAP-THROUGH BEHAVIOUR
This work analitically and experimentally investigates nonlinear snap-through of a simple class of elastic space trusses in the shape of a regular pyramid. Joints located at the vertices of the base polygon are pinned while the joint at the apex is subjected to a proportionally increasing load acting in the vertical direction. A pyramid truss model has been designed, machined and successfully tested in learning environments to facilitate understanding of the mechanics of truss structures, geometric nonlinearity and stability. Solutions are derived for each load condition under the common hypotheses of linear material law, small or moderate axial deformation in bars and large nodal displacements. For pyramidal truss we determined a function of force in dependence of vertical displacement of uniaxial structural elements for different starting angles at which the uniaxial structural elements were clamped. Accuracy of analytical solution for snap-through system, which we got for different starting angles of uniaxial structural elements, was verified on experimental results obtained in the laboratory.
Step 1: Theoretical Analysis
A classroom demonstration model has been designed, machined and successfully tested, as shown in Fig. 1 and 2, in different learning environments to facilitate understanding of the mechanics of truss structures, in which struts are subject to purely axial load and deformation.
For the shown four-bar pyramid truss it is assumed that the struts are initially straight, that their Euler buckling load is so large that they never buckle, and furthermore that they remain linear-elastic throughout. If length L and height h are known, then also the radius d is known. On the node, where uniaxial elements meet a vertical load F is applied. Under the acting force F, all four uniaxial elements will compress and will move vertical down. Vertical displacement is marked as f, as it is shown in Fig. 3.
Final equation in a form of F=F(f) shows a diagram in Fig. 7. In the region from point 1 to point 2 the system is in stable equilibrium state. In the region between points 2-3-4 the system is in non-stable state. Vertical displacement f is increasing although vertical force F is decreasing and even becomes negative. Between points 4 and 5 the system is again in stable equilibrium state, because with increasing vertical displacement also the force is increasing. The maximum force that also defines its critical value is marked as Fcr. The system snaps through from point 2 into point 5 at a constant force F=Fcr. That is why the process follows the curve 1-2-5. When the system achieves point 5, the uniaxial elements are under tensile load.
At the limit point 2 and 4, the tangent to the equilibrium path is horizontal, i.e. parallel to the displacement axis. As will be seen through the paper, the limit points are of special importance in the load control path following technique, where after passing a limit point, due to a further load increment, no static equilibrium exists nearby and therefore the structure dynamically snaps through into the next post-critical equilibrium position, as shown in Fig. 7.
The main purpose of the path following techniques is to draw the equilibrium path of a nonlinear structural analysis in the framework of a load-displacement response diagram.
Step 2: Experimental Analysis
For analitical calculation of critical force Fcr and for plotting a load displacement diagram, the spring constant of the shock absorber had to be measured, as shown in Fig. 8. The procedure for determination of the spring constant was repeated 10 times for each shock absorber. Shock absorbers are of length 115 mm, the length between the clamping points is 105 mm and compression length is 30 mm.
For the value of spring constant k for the whole system, an average of all four springs was taken, as shown in Table 1. The average spring constant value of a system was 0.957, and was used in the equation to determine the theoretical critical force for the mechanism for simulating snap-through at different starting angles of clamped uniaxial elements.
Shock absorber Average
1 0.973
2 0.950
3 0.962
4 0.942
Average 0.957
Step 3: Measuring Equilibrium Stability Curve of Four-bar Pyramidal Truss
The investigation of nonlinear snap-through of a four-bar pyramidal truss with ability of setting different starting angles of uniaxial structural elements was performed analitically and experimentally. With sliding supports of shock absorbers we ensured setting of different starting angles of uniaxial elements. From the experiment we determined the function of force F in dependence of vertical displacement f at different starting angles α of uniaxial elements.
In the experiment, a four-bar pyramid truss was placed into the Zwick/Roell Z050 testing machine, as shown in Fig. 9. A function of F(f) was determined for a four-bar pyramid truss at starting angles of clamped shock absorbers for 20°, 30°, and 40°. Experiments were made at deformation rate of 100 mm/min and temperature 25°C.
Step 4: Comparison of Analitical and Experimental Equilibrium Stability Curve
For every starting angle of clamped shock absorbers 20 measurements were made. The results are given in Table 2 and diagrams in Fig 10, 11 and 12. In Table 2 are given average results of critical snap-through force of measurements, theoretical critical force obtained from last equation for different starting angles of uniaxial elements, and the error. The average critical force obtained from experiment is a little bit higher than the theoretical critical force. This was also expected, because the equations do not take into account friction. From Table 2 it can be seen that the error decreases by increasing the starting angle. The reason for this is a difficult setting of angle for setting a shallow structure and it can also be concluded that the system is very sensitive to initial conditions at which experiments were performed. The results also show that the critical force Fcritical is decreasing with decreasing starting angle α.
Comparison of experimental and theoretical calculated critical force at different starting angles
α [°] Fmax,teor [N] Average Fmax, exp [N] Error [%]
40 26.395 26.913 2
30 11.118 11.432 2.8
20 3.29 3.446 4.7
From Fig. 10, 11 and 12 we see that stability curve obtained from the experiment is very similar to the one that theory predicts. Although the stability curves are shifted, similarities between the curves can be seen. From the curves in figures we see that the theoretical and experimental curves are parallel and that the crucial points, maximal force switching from positive to negative load, appear at the same distances. From the diagrams it can be concluded that the force of friction at standing point is around 1 N, and for this force the experimental stability curve is shifted to the left from the theoretical one. That is why, from Fig. 10, 11 and 12, it looks that with higher initial angle of clamped uniaxial elements, the curves are moving closer together.
Step 5: Laboratory Exercise for Students
After comparing experimental and theoretical results we decided that this is a great exercise for students to get a deeper insight of what is happening when a snap-through of a system occurs. With this exercise we got students attention, because they are involved in making experiment by themselves.
The students investigate the snap-through phenomenon in such a way that they follow the procedure, in Fig. 13, of marking the position of the system when there are no weights in a cup. When they put weights in a cup, they mark and measure vertical distances f for every weight they put in. Also they do not throw the weight into a cup, because when the system is near the critical force Fcr of snap-through, the inertia of the mechanism would cause the measurements not to be accurate. That is why they put it into a cup. They stop loading the cup when the system snaps-through.
Fig. 13 shows three different configurations of the deformed structure representing important moments in the analysis. At the first configuration, Fig. 13(a and d), a small displacement can be observed, the structure is close to the initial configuration and therefore it is in the linear regime. At a certain level of loading, the structure begins to exhibit behavior essentially nonlinear as shown in Fig. 13(b). The displacement is greater in the second case but not enough for the loss of structural stability. The analysis continues until the load reaches a position that triggers the reversal of the structural behavior due to a larger displacement. Thus, the structural members that were initially compressed, to reach the new equilibrium configuration, are now fully tensioned, as shown in Fig. 13(c).
After the snap-through of the system, students weigh the weights on the scale, as we can see from Fig. 14. Weights weigh 332g. We must also take into account the weight of a cup, which is 13g. The critical force of a system to snap-through is 3.45 N, which is 0.004 N higher than critical force obtained from experiment.
Step 6: Conclusion
In the presented work the equilibrium stability problem for a wide class of elastic space trusses in the shape of a regular pyramid was studied theoretically and experimentally. My goal was to analyse the snap-through curve also in non-stable region of stability curve. We determined the stability curve for a pyramidal truss with different shallowness of structure. Instead of beams or rods, shock absorbers were used. In the experiment we followed the whole equlibrium path of the system, the stable and non-stable.
A simple physical model has been shown to effectively facilitate the understanding of the mechanical behaviour of truss structures. The model is simple and cheap, and is allowing the setting of different shallowness of a four-bar truss system. The study of the stability of structures involving such materials was done for the first time. It demonstrates the qualitative behavior at the loss of stability for more complex structures, such as plates and shells, for which results are not available. We find bifurcation points on the static load diagram for the truss. These are elementary structural forms crucial to the understanding of several conceptual models employed in different technologies. The difference between the experimental and theoretical results is in the region of 5%. From experimental results it is seen that the force of friction at standing point is 1N. The stability curve obtained from experiments is basically the same as the one obtained with the help of equations.
Firstly, the equations for snap-through of a system were obtained, and by analysing the equations students saw that, since we were dealing with a simple physical system, it is also described by a simple equation. On the other hand, the experiment described in this paper provides us with not only an understanding of geometric nonlinearity but also a better understanding of the basic concepts of stability. Important topics, including concentrated loads, linear elastic materials, large displacement, symmetry, stable region, unstable region, snap-through and stability curve are considered in this experiment.
Finally, we have shown that the stability and snap-through of the system may be easily studied with a simple, easy-to assemble, low-cost experiment, which allows us to experimentally study the force in dependence of displacement by means of a series of simple measurements, such as lengths and initial angles of uniaxial elements.
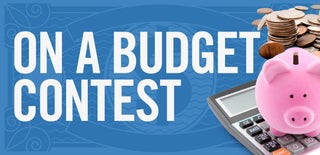
Participated in the
On a Budget Contest
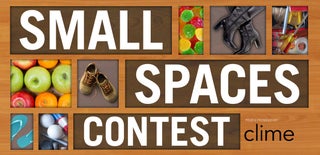
Participated in the
Small Spaces Contest
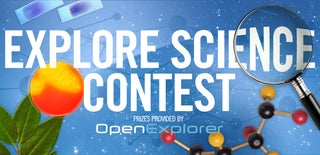
Participated in the
Explore Science Contest