Introduction: Sculpting a Christmas Tree
I deconstructed my Christmas tree to make an ornament.
It was a short project, with less digital fabrication than usual, and more manual craft.
Most unusually though, I had no intention of making a product. I intended to find this thing a function as it was fabricated, or just cross the bridge and call it art.
This is my favorite way to get doing, and experiment.
Supplies
Walk outside. Has anyone left a Christmas tree on your street?
Step 1: Peeling the Bark
I took a Stanley knife, bracing the blade with my thumb, and peeled small chips from the trunk. With a different Fir variety, in the past, I have been able to peel it off cleanly in sections, but this one required carving. It was made easier by the fact that the wood was still very wet. The difficult bits are the branch stems: it's hard to get the knife in and get a long cut.
This process took a while, but was very therapeutic.
Beneath the bark remains a pithy layer. It tends to discolour after being exposed to the air. It is soft, and can be scraped off to reveal the lighter, clean wood beneath.
Step 2: Modifying the X Carve
The clearance on my CNC is far too low. Luckily, I realised it would be a very simple mod.
I unbolted the bottom plates of the Y axis from the aluminium frame of the bed. I cut out a MDF frame to drop down below. Measuring the diameter of the log at the correct intervals allowed me to decide on grooves for the log to rest whilst carving it.
Of course, this setup is too shaky for normal use. I chose the pocket design that follows for this reason - it won't show flaws from the drifting bit due to flex. I'd need to be flipping the tree constantly so I just used quick release clamps to press it into its mounts at either end.
Step 3: Pocket Pattern
After fumbling with Easel and Illustrator .svg files for a bit, I realised Easel misinterprets the shades of grey from the 'blend' tool. Eventually I came across the Easel app 'Super Gradient Generator' by Ethan Kinney. This worked perfectly.
This creates a series of outlines from white to black, which correspond to the depth of the cut. I kept the step resolution down, because I want to show off the stepped aesthetic.
As I moved up the tree, I created pairs, reducing the pocket width, height and depth each time. Flipping the tree over meant I had to ensure the pocket on the underside was aligned for the matching pocket to meet it. This was straightforward.
Step 4: Cleaning Up
The cheap router bit, cut direction and softness of the wood make for a mess of fibres around the openings. Folded sandpaper is the only way I've really found effective, and some still remained.
The knife strokes left a very smooth exterior to the tree, which the sandpaper roughened slightly. After that was done, I took some height off the tree and blunted the end with the knife.
Finally, I masked off the pockets, running masking tape around the the perimeter with a screw head. Painting it before mounting and carving would have left me with some scrapes, so this was a better alternative.
Step 5: Giving It a Coat
I filled up an airbrush with some yellow, orange, green and purple to give it a vibrant finish. Spray paint was too thick. The colour choice here came from cacti.
This project was a means to finally try out carving thicker stock with the CNC, and have a go at some hand carving too.
Thanks for reading!
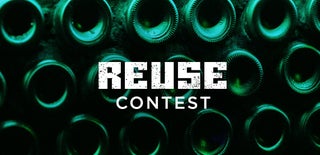
Participated in the
Reuse Contest