Introduction: Secret Compartment Box With Silver Inlay
This box was constructed as a gift from cherry and walnut. The cherry was cut, dried, sawed, and planed in my hometown in Virginia then moved out west with me. The walnut was purchased locally in California. The only fasteners used in the construction of the box are the screws attaching the hinge, everything else relies on splines and glue. This process can be adapted to many different shapes, sizes, and species of wood. I will not be providing any measurements because there are none. The shape and size of this particular box were dictated by the materials I had on hand.
Step 1: Cut Your Pieces
I believe that it is aesthetically pleasing to have the grain wrap around the sides of a box. In order to achieve this look you will need to do a little planning. Start by laying out the material you are going to use to construct the sides of your box. For the first part cut everything at 90 degrees, we will miter the edges later. From left to right start with cutting the back of your box first, label this one number 1. Then measure and cut the left side of your box, label that number 2. Next cut the front, this will be number 3 and finally the right side is number 4.
Now that all of your sides are cut you will need to lay them out in a row and reassemble the puzzle. Make sure you align all of the grain once again. Notice that the match is not 100% perfect because the saw blade took away what is know as the kerf, aka the width of the blade. Don't worry only the pickiest of friends will ever notice this. On the back of all your pieces (the side you want on the inside of the box) draw an arrow pointing to the bottom edge. Be consistent, this will make assembly easier. I should note that all of these marks should be in pencil so they may be sanded away later. No pens and absolutely no sharpies.
Once your pieces are marked cut a 45 degree miter on the sides of your pieces. This will be the sides to the left and the right of that arrow you drew. Be careful not to take off too much otherwise your pieces will no longer be the same length. The idea is to not remove any material from the top edge of the board and only take away a triangular section of the bottom. To do this I used a table saw and a sled jig. If you choose to go this route be sure that the side the arrow is on lays flat on the table and isn't facing up. If you mess this up the inside of your box will become your outside.
Once your pieces are mitered do a dry fit of the pieces and measure for the bottom and lid of your box. The bottom and top of my box were recessed into the sides. I used a dado blade to rabbit the top and bottom of all four sides. Make sure that the depth of your dado matches the thickness of your top and bottom material. I used a slightly thicker piece of walnut on the bottom than the top just to give the bottom more weight and to increase the size of the secret compartment on the top.
Step 2: Glue Up
Take all of your pieces and do a dry fit. Make sure everything is fitting just right, make adjustments if necessary. There is nothing worse that having to clean all the glue off a project because you have to stop and fix a piece. Gather your clamps and have them close by. If you have an extra set of hands it can really help in this process. Grab your bottle of trubond (wood glue) and apply to all of the edges that contact other edges. Use a brush or your finger to spread the glue evenly over the entire surface that is to be glued. Not too much and not too little, Goldilocks. Assemble the pieces just like you did in the dry fit and start clamping. Notice how the pieces now slide back and forth because you applied the slippery wood glue. This is where the extra hands come in to play to help you hold things in place while clamping. I did this one by myself so it is possible, but I wish I had help. Make sure that everything is lined up just how you want it and let it cure for 24 hours.
Be sure to get enough clamps on all of the edges. It may look excessive in the picture, but I could have actually used a couple more... There will be some glue that squeezes out on the edges, this is an indication that you have good coverage. Take a damp rag (make sure there is no oil on it) and wipe the glue away before it dries. When you come back you should have a 6 sided box with all the sides glued shut.
Step 3: Splines
Splines are used to strengthen joints and to provide a decorative touch. Realistically if you had a proper glue up then your box will be strong enough not to need splines, but this was part of my design. I used the contrasting walnut to highlight the edges.
Add two blocks with 45 degree miters on them to your table saw sled. The idea is to create a cradle for your box to stand upright at a 45 degree angle. Raise the blade to the desired depth of cut. The idea is cut almost all the way through but not quite into the inside of the box. Use a scrap piece of wood to determine if your depth is set where you need it.
Each spline recess required a couple of passes on the table saw to achieve the desired thickness. I screwed in a stop block on my sled to make sure that I got a consistent cut all the way around. I didn't use a tape measure at all on this step, everything is guess and check.
Once all of your recesses are cut use a chisel to even out the bottom of the cut. This will allow for a better seat for the spline to sit on thus a stronger glue joint. Cut small strips of walnut (or whatever wood you choose) that fit snugly into the recesses. If any spline pieces are not snug cut some more. We will be relying on the snug fit to do our clamping during glue up.
Clean all the saw dust off your splines and the recesses. Apply glue in the recess using a brush then press in the splines. Use a wooden mallet (or something that isn't going to damage the wood) to tap the pieces into place. For this step I did one corner at a time so that the glue did not start setting before I had all the splines in place. Take your time and make sure everything is seating properly. Let cure for 24 hours.
Once the glue has set use a flush trim saw or a ryoba to flush up the corners. Note that a ryoba has different teeth on both sides, one side is for ripping the other is for cross cutting. The side with finer teeth is for crosscutting which is what we will be doing here. If you don't have a ryoba I suggest picking one up, they are extremely useful and are around $20 USD. If you don't have one any crosscut saw could do the job, just be careful not to cut into your box.
Once all of your splines are cut flush give the outside a quick sanding. Decide where you want the lid to hinge, keep in mind the taller the lid the more space you have in your secret compartment. Once you have made your decision set the fence on your table saw to the lid height and set the blade depth to be just slightly taller than the wall thickness of your box. This should be no more than 1/32. Use a scrap piece of your side material as a guide to set the depth don't try and use a tape measure, most only go as small as 1/16 ths. Cut the lid off by passing your box through the table saw and cutting all four sides. If you set the depth properly it should come right off.
Step 4: Secret Compartment
I picked up some 1/4" diameter rare earth magnets on Amazon for pretty cheap. A pack of 100 was around $10 USD. Using a forstner bit and a scrap piece of wood set the depth of your drill press so that the top of the magnet is flush with the surface. This may take a couple of tries to get right, but that is what scrap wood is for.
Cut a piece of wood the same type as the top of your box. This piece needs to fit perfectly inside the lid. It is better to cut the piece ever so slightly large and sand it down than to cut too small. The closer to a perfect fit the false lid is the more inconspicuous it will look. This false lid should be able to slide into place freely, but not bind. Take your time on this step and get the fit just right, it will pay off in the end. Miter both ends of the lid to 45 degrees so that when you press on one on side to rock the lid up it doesn't bind (see picture)
Cut two more pieces that will act as the rails for the false lid to sit on. These should be just wider than the magnets and can be as tall as you like. Cut a 45 degree angle on one end of the rails. This will allow the lid to rock up when you press on the correct area.
Using the drill press mark and drill the holes for your magnets. The placement of the magnets should be interchangeable so that the lid can go back on the box in either direction. For example place magnets in the middle of the lid and 3/4" in from each end. The Magnets should be centered in the rails and offset from the edge of the lid the same amount. This may sound confusing, but just look through these pictures and you will see what I mean. The idea is to have the magnets on the lid line up perfectly with the magnets on the rails.
Before you epoxy in any magnets you need to determine which side of the magnets are north and south. You want the lid to be attracted to the rails and not repelled. The magnets are not marked in anyway, they are just shiny little discs so you have to get creative. I took a scrap piece of wood and made a little "north-south stick" as I called it. To do this drill a hole in each end of your scrap. Epoxy in a magnet either side up, it doesn't matter and let it cure for about 15 minutes, this will be called north. Take another magnet in your fingers and determine which side is attracted to the magnet that is epoxied into the stick. The side that is attracted will be south (opposites attract in magnets). Epoxy that magnet into the other side of your stick with the side that was attracted facing up. Mark that side as south.
Using your "N-S stick determine which side is which and epoxy them into the lid and rails. Make sure that the rails all use north magnets and the lid uses all south facing magnets. It doesn't matter which side you call north or south, just be consistent.
Step 5: Hinge
I opted for a piano hinge for my box with a nickle finish to compliment the silver inlay I was planning. Feel free to choose any style or type of hinge you please. Most hinges will need to have a mortise cut out for them so they close properly. Notice in the picture there is very little gap between the top and the bottom of the lid. If the space for the hinge wasn't mortised out the lid would not close evenly.
I used a chisel to cut the mortise. A sharp chisel goes a long way, pause and take some time to look at one of the many instructables on this topic.
Take special care to mark and pre-drill all the holes for the screws so that everything closes properly. If you don't pre-drill for the screws you run the chance of splitting the thin wall of the box. I also applied a little wax to make the screws drive in nicely without stripping any.
Step 6: Silver Inlay
This was my first time doing any sort of inlay so take in this information with a grain of salt (i.e. I just made it up).
I started by cutting out the form I wanted from a piece of 18ga sterling silver. This was a scrap piece left over from a fine metal working class I took back in college. I printed out a shape and used 3M Super77 to adhere it to the silver. Using a jewelers saw and this little foot I made out of a 2x4 I cut out my shape. When using a jewelers saw remember that it only cuts in the down motion. Take your time and gently steer the saw around the outline of your shape. Once the shape is cut out use some alcohol to dissolve the adhesive and clean off the silver. File down the edges and clean everything up. This will be a focal point so take your time.
Lay the silver piece on the box where you want to inlay it. Using an exacto knife trace the outline of the shape as close the the edge as you can. No need to cut deep just use enough pressure to score the surface. Remove the silver piece and trace over your lines with a little more pressure. I didn't have tiny chisels to using a dremel grinding wheel and then a diamond stone I sharpened a small screw driver. This of course isn't the proper way, but it worked surprisingly well. You can see the sharpened screw driver in one of the pictures.
Using your homemade chisel remove material little by little until the silver piece fits. Be careful not to go too deep or too wide, there is no going back at this point. Every once and a while use the exacto to clean up the edges of the outline if necessary. Lay the silver over the recess you are creating to make sure you haven't widened the shape too much.
Using 220 grit sand paper lightly scuff the bottom of the silver. This allows the epoxy to get a better grip. Apply epoxy to the recess and press the inlay in place. There will be some epoxy that squeezes out, don't dry to wipe this off. If you try to wipe this off it may get pressed down into the pores of the wood on the lid and this will affect the finish. Allow to cure for 24 hours and then sand the top of the box. start with 120 and work your way up. I went all the way up to 2000 grit around the inlay to polish it.
Finish the box with three coats of high gloss polyurethane. sand lightly with 220 grit in between coats. Thats it, your done!
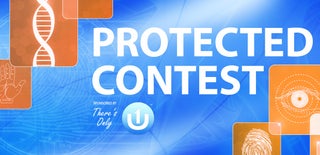
First Prize in the
Protected Contest
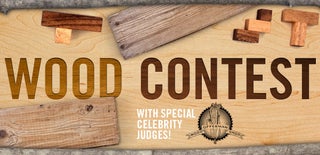
Participated in the
Wood Contest