Introduction: Sectional Sliding Gate
Sectional Sliding Gates are a great alternative to swing gates where higher security levels are requires and where there's not enough space to for a standard sliding gate to slide open. Swing gates are easily pushed open in a double configuration and when there are not extra locks fitted.
When a sectional gate is used with a sliding gate motor it is locked secure when closed and can't be moved. These gates are visibly appealing and draw quite a bit of attention. I have posted a video of one of them on my Facebook page and got over 80000 views and loads of comments and orders.
These gates are fairly simple to fabricate but there are a few rules that you have to adhere to otherwise it will be a expensive disaster.
So happy fabricating
Step 1: What You Will Need
Bill of materials:
50mm x 50mm square tubing (you will need to work out how much according to the size of your gate)
15mm x 1.6mm round tube
12mm round bar
whatever you desire to fill in the panels
80mm radius gate wheels one for each panel plus extra one
nylon top rollers 2 x sets
parliament weld-on hinges 2x for each 2 joining panels
50mm x 5mm flat bar (for the rail)
16mm round bar (for the rail)
75mm x 50mm lip channel (for the rail)
paint
sliding gate motor (minimum 500kg pulling force)
rack
concrete mixture
Tools:
Angle grinder
cutting and grinding disks
drill
15mm drill bit
welding machine
spray gun
spirit level
nylon building line and line level
pick and shovel
Step 2: Fabricating the Panels
The gate consists of several vertical panels, that make up the complete assembly. For driveway and other large gates I use a panel of 600 mm width. The height you can make to your liking or the height of your boundary wall. there's no specific height there.
The formula that you use to work out the amount of panels is simple. You take the gap between the two posts or walls that the gate needs to fit in. Divide it by 600 mm and add 2 panels. These 2 panels are needed to stabilize the gate and to connect to the gate motor that sits on the side, adjacent to the wall that you need to slide it against. Example: gap is 4 meters. 4000mm / 600mm = 6.6 panels. I round it up normally to be on the safe side, Thus you will need 7 to close the gap plus 2 extra to take up the turn and the gate motor.
Use 50mm x 50mm square tubing to fabricate your panel frames, cause the gate wheels you need to use has a base of 50mm. now you are ready to fill the panels with which ever design you prefer. In the video I have used louvres that I have bent from 1.6mm mild steel sheeting, but you can have anything you like. Maybe get a nice pattern or picture laser or water jet cut and weld them in.
Next up is to fit bushes in the bottom of the frames where your gate wheels will swivel in. Drill 15mm holes in the bottom horizontal part of the frame. one hole 40mm from the left in the center and the other one 40mm in the center from the right. I use 15mm x 1.6mm wall round tubing that I cut into 50mm lengths and then weld into the bottom on both left and right sides holes drilled in the frame.
Last you need to fabricate the roller bracket. I use a double configuration as in the picture, that is a very strong and precise method of keeping your gate where it needs be
Step 3: Gate Assembly
Now you are ready to assemble the complete gate. Place the panels next to each other and make sure that the bottoms of the panels are 100% level with each other. It's very important, if your panels are not 100% equal length which happens normally, don't worry, the top of the gate does not need to align perfectly. The bottom does.
Weld in the Parliament hinges, one 200mm from the bottom and one 200mm from the top. The hinges I use has a offset of 30mm. the hinge pin needs to be 30mm from the pin and not flush otherwise your gate motor rack will not work and will bind and break everything.
The gate wheels that you normally buy are weld on, for this application they need to be modified to be able to swivel. Take out the pin that holds the wheel in the bracket. Remove the wheel from the bracket. Now mark out a point in the center of the bracket and drill a 12mm hole. cut a 50 mm piece of 12mm round bar and weld it in the hole on the inside of the bracket. NOT THE OUTSIDE. Assemble your wheel.
Test fit if the 12mm round bar will fit in your 15mm bushing. If not use a reamer and clean out the inside of the bushing until it fits. Add a 12mm inside diameter flat washer between the wheel and frame on the shaft. put enough grease on everything. It will just make it easier to move and operate.
In the previous step I had you put 2 bushes in per panel, you are not going to use both of them. The Wheels start at the end where the gate closes against the wall or post, thus the panel where you stand infront of the gate and it closes to your right, it will be the first panel on your right. You skip one bush and insert the next wheel in the same bush as the previous panel. One wheel per panel, except the very last panel will have 2 wheel in that panel. You will see why when you assemble the gate
Paint your gate
Step 4: The Dreadful Rail
The rail will make or break your project. It took me several weeks to perfect this. Follow my instructions and your gate will be a success from the start. I had gates derailing and topple over etc. etc until I found the correct way to make and install.
Use 50mm x 75mm lip channel for the straight parts of the rail. Make sure when you purchase them, that it is 100% straight. Now measure the length of your gate assembled. That will be the length of the rail on both sides of the bend. Turn the lip channel onto one of its sides and weld the 16mm round bar onto the side in the center.
For the bend I used 50mm x 5mm flat bar and bend it in a 90 degree configuration around an inflated 15 inch truck or pick up tyre. That seems to be the ideal radius for these gates. Then bend the round bar also around the tyre and weld it onto the edge of the flatbar.
You don't need to weld the whole round bar. I use short little space welds about 300mm apart to try and keep the rail from warping.
Dig a trench in a L shape where you want your gate to slide, about 200mm deep and 300mm wide. I weld off cut pieces of steel perpendicular to the rail on the bottom. That will help tremendously to strengthen the whole structure and most of all when you level the rail, you hammer them in the soil to keep the rail in the air and level. It makes it much easier when you pour the concrete.
When you level the rail, use spirit levels, building line and line levels, laser levels or what ever you have at your disposal. JUST MAKE SURE THE RAIL IS 100% LEVEL. The gate will derail even if there is just the slightest divot in the rail.
After you're sure that your rail is straight and level, mix your concrete and pour it up to the top of the lip channel and flat bar so that only the round bar is exposed. Leave it to cure about 2 days
Step 5: Installation
The top roller guide will differ, depending on what you have to mount it to. It can be mounted against a wall as in the picture or you can concrete in two 100mm x100mm square tubing's where you can mount the rollers, as long as you have a sturdy mounting point to prevent the gate from toppling over.
I normally put the gate on the rail with the center of the gate on the rail bend. That keeps it upright and easy for you to mount the roller guide in the correct position.
Now that the gate is on the rail and secure, you can fit the gate motor and weld the rack on the gate. I have said in the previous steps that the hinge pins needs to be 30mm offset from the gate panels. Your rack needs to be in 5mm closer to the panels (25mm from the panels) this will allow the rack to move apart around the bend other wise it will bind and try and push the gate in a straight line. Cut the rack after you have welded it right in the middle under each hinge pin. Then move the gate one panel forward and weld another piece on
The last thing you have to do is to bolt the catch in the end where the gate closes, that just makes it more sturdy and secure and you can fabricate something where you use a padlock as extra security
That is it, a lot of work but well worth it in the end when you see it operate flawlessly. it really give you a sense of accomplishment.
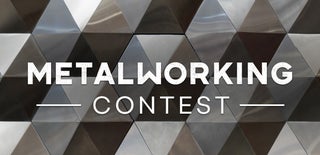
Participated in the
Metalworking Contest