Introduction: Self Adjusting CNC Dust Boot
- Very effective dust boot for a 2.2kw 80mm Diameter water cooled spindle.
Let me start this off by saying that this is actually my second attempt at creating a dustboot for my DYS CNC router. At first I was impressed with a product sold by probotix ( https://www.probotix.com/CNC-ROUTERS/ACCESSORIES/... ) because of its $179.95 price tag I decided to build a boot along the same line and style with the same specs myself. It seemed to work OK for me. After a week or so I realized there might be some ways to upgrade this idea.
I wanted to address the following:
- The brush was long and therefore bent dramatically in an attempt to maintain contact with the work piece.
- The long bristles tended to grab and either pull out or get caught in the blade and get cut up.
- Because the attachment stayed up away from the work piece, the suction strength dissipated when the spindle would rise and lower
- The vac hose while connected to the attachment would get in the way, swing around and would cause me to lose precious working travel area.
- The overall footprint of the boot also caused me to lose an inch or so of travel area.
I found that the advertised advantage of being able to see the blade cutting was negated by the long brush and hose issue.
I did some looking around and saw other dust shoes that looked pretty inventive. One was a boot that had a ridged holder that kept the brush and hose at a constant on work piece height.
- This seemed to lack the ability to adjust to variable 3d carving heights while cutting.
- Because of the opening for the spindle to rise and lower. I noticed the potential for suction leak here as well.
- The overall footprint was too large for my needs.
- It required a complicated support system to work as well
I then came across an amazingly simple yet very effective boot Idea by a maker on YouTube. Called (CNCSwede) his idea was called the “The Floating Dust Shoe”. You should see this! So, dam obvious, simple and so great! ...Here is the link: (https://www.youtube.com/watch?v=T1K1gFbxv2M)
Using a Shock Absorber Boot billow to help adjust to the height changes was a great idea.
I will put a link to an amazon source down below
So, these are the features I decided that I wanted the most while borrowing the strut boot idea that I like so much:
- Have the smallest foot print possible that would still be effective.
- Keep the suction closer to the work piece
- Keep the hose up above the spindle
- Keep the boot adapter down low to the base of the spindle
- Have a shorter stiffer brush that would not get cut up or pull our bristles
- Create a small chamber to direct the suction nearer to the cutting blade
- Use only a single billow and a smaller brush contained area
- And to keep it as simple as possible
Supplies
- 12 x 10-inch .50" thick plexiglass sheet
- 8 x 10-inch .25" thick plexiglass sheet
- 8 x 10-inch .125” plexiglass sheet
- strong two-sided tape to adhere the plexiglass to the table surface.
- down-cut single O flute spiral endmill designed for acrylic cutting
- IPS 4 4 Oz.Weld-On® 4™ 4 oz.---6 plus $ USD
- Hypo 25 Applicator Applicator for Weld-On® Hypo 25 industrial solvent adhesive--- 2+ $ USD
- “Magcraft” Rare Earth 1/4 in. x 1/10 in. Disc Magnet (50-Pack) from home depot.
- for the suction extension: 32.6 mm Dia cut to the length you need white painted closet rod
- a Shock Absorber Boot billow: click here for link
Step 1: Acquire These Supplies If Possible
List:
1. 12 x 10-inch .50" thick plexiglass sheet
2. 8 x 10-inch .25" thick plexiglass sheet
3. 8 x 10-inch .125” plexiglass sheet
4. I recommend a Down-cut single O flute spiral endmill designed for acrylic cutting click for link
but this is only if you desire a super clean finish...they are not cheap!
You can always use bits you have in stock
5. IPS 4 4 Oz.Weld-On® 4™ 4 oz.---6 plus $ USD click for link
6. Hypo 25 Applicator Applicator for Weld-On® Hypo 25 industrial solvent adhesive--- 2+ $ USD“ previous link
7. Magcraft” Rare Earth 1/4 in. x 1/10 in. Disc Magnet (50-Pack) from home depot. click for link
8. For the suction extension: 32.6 mm Dia cut to the length you need white painted closet rod at home depot
9. A Shock Absorber Boot billow: click here for link
10. 2 adjustment knob screws one option here: click for link
11. Strong two-sided tape to adhere the plexiglass to the cnc table surface click for link
Step 2: Define Your Needs. Design Your Parts
I use a 2.2kw 80mm Diameter water cooled spindle (Chinese).
Your spindle might have different specs.
After measuring twice, I sketched out my design in fusion 360. And designed the series of models I would need to cut in order to assemble the dust boot. You can use what ever software you are comfortable with. I believe “CNCSwede” used Vetric. This might sound like a cop-out but the video he made gives you a nice step by step look in to how you might sketch and model create tool-paths for cutting his design. As such I will recommend you watch his video first. I’ll start from there and then step you through what seemed to work for me.
(https://www.youtube.com/watch?v=T1K1gFbxv2M)
next:
I used three different thicknesses of cast plexiglass as base material for the parts,
plexiglass acrylic sheets:
- 12 x 10-inch .50" thick plexiglass sheet
- 8 x 10-inch .25" thick plexiglass sheet
- 8 x 10-inch .125” plexiglass sheet
There are lots of distributors online, amazon and eBay also have it available. I was lucky enough to have scrap stock in house
When cutting:
- I recommend using strong two-sided tape to adhere the plexiglass to the table surface.
- Make sure to use a down-cut single flute spiral end-mill designed for acrylic cutting for milling the parts.
- With acrylic milling it is best to slow down the spindle speed and use a slightly faster federate in order to avoid melting the work piece. The end result will be much cleaner.
- Make sure to vacuum the chips during the cutting process, as the chips can fall back into the pockets and effect the cutting results.
- if you need help with your design you can email me here: george@greenlimedesign.com
- (we can discuss giving you access to my fusion files as a starting place for your design)
- I have attached a file that you may use as a basis to rework to fit your own Spindle
IT IS ONLY FOR MY SPECIFIC SPINDLE AND MIGHT NOT FIT YOUR SPINDLE.
As such my Gcode would be useless for you.
Step 3: How to Bond the Acrylic Pieces
After cutting, separate and clean the cut edges.
In order to bond the layers correctly I purchased on amazon: IPS 4 4 Oz. Weld-On® 4™ with 4 oz. USDApplicator for Weld-On® Hypo 25 industrial solvent adhesive Here is a link that will show you the best way to use the acrylic adhesive – click here
Step 4: Collect Part A
Select part A from the parts list (the top most plate that attaches to the spindle at the bottom of the spindle). Place it on the work bench- magnet pockets up.
Step 5: Separate and Prep the First 9 Magnets
Take 9 magnets from your magnet source. they should have the polarity of each magnet same facing up away from a hole in the acrylic base.
It might help to have magnets in contact with those magnets that you’re going to place in the pre-drilled holes in the acrylic in contact so that you understand which way the polarity goes.
Step 6: Super Glue the Magnets
Using gloves preferably medical latex gloves to cover your skin, carefully place a drop of super glue into the first hole. Be careful to not deposit more than you need. You definitely do not want overflow. It will be much hard to clean up later. Push one of the magnets in to the hole with the other magnet attached. Now slide the other magnet off the one that is in the whole, and clean any remaining residue on that magnet. Also clean any extra glue that might have overflowed onto the outside surface of the acrylic. And make sure that the magnet is flush with the facing surface. After you are sure that you have a solid bond, and a clean finish, prepare for the next hole and repeat until all holes are done on that one acrylic plate.
Step 7: Mark the Adjustment Screw Holes
When you have all the magnets cleanly placed in: the base acrylic plate, mark with a sharpie marker, the positions where you’re going to pre-drill centered holes into the acrylic where the adjustment holding screws will be placed. Use the photo you see above as a guide.
Step 8: Where to Drill and Tap the Adjustment Screw Holes
Drill and tap the holes according to the photo above. In the hole where the spindle will be attached, only tap the back hole as shown in the photo above and make the front hole slightly larger than the tap in the front part so that the adjustment screw can enter and then only tighten the its grip with the acrylic accordingly.
Step 9: Place Part B Magnets
Place part B, 2nd Level connecting plate holes up. Using the same process as in the spindle attachment plate, place magnets with the correct polarity up into each of the holes. Again, be careful not to over fill the holes with super glue. The overflow will make a plate ugly and hard to clean afterwards. Afterwards check that both plates are magnetized correctly and will attract each to connect correctly.
Step 10: Flip Part B
Now flip part B, the 2nd Level connecting plate magnets down.
Step 11: Align Part C With Part B
Find part C, third level cap plate 1/8-inch acrylic and place it over part B, the half inch 2nd level contact plate careful to line up and not cover the side with the magnets installed.
Step 12: Adhere Parts With Acrylic Adhesive
Carefully align the outer edge of both plates precisely, tape with small strips of blue painters masking tape, to ensure clean tape removal. Again, double check that you are not adhering the one 8th inch plate to the side of the ½ inch plate where the magnets are installed and then carefully apply the Weld-On® 4™ acrylic adhesive as instructed using a capillary action as in the demonstration video mentions in the above paragraphs.
Step 13: Place Part Precisely Over the Assembled Sections of Part C
Find part D, 4th level spacer plate (1/4-inch plate).
Using the center hole of part C, place part D, 4th level spacer plate directly over the hole.
Step 14: Bond Both Plates
After aligning the parts, tape in place with blue tape. Using the Weld-On® 4™ acrylic adhesive, glue both plates together carefully. After they dry, remove the tape and clean any residue.
Step 15: Part E to Part D
Find part E, 5th level cap plate (1/8th inch plate). Using the outside edge of part D align part E precisely and secure with blue tape
Step 16: Bond Part E to Part D
After aligning both plates precisely and taping, glue using the acrylic adhesive. Then remove the blue tape and clean any residue.
Step 17: Align Upper Billow Plate Precisely Over the Hole
Find part F, the sixth level billow lip plate 01. Place the center hole directly over the hole in part D.
Be careful to allow the lip space to remain between the two plates as in the above photo.
Step 18: Bond the Billow Plate to the Rest of Assembly
Carefully align both plates and tape together using the blue tape. Now repeat the process of adhering the two acrylic plates using the acrylic adhesive. Be careful when applying the acrylic adhesive to not let any of the acrylic glue to fill in the lip space. Now carefully remove the tape and clean any residue.
Step 19: Align the Billow Lip to the Lower Brush Holder
Find part F, the sixth level billow lip plate 01. Place the center hole directly over the hole in
part D. Be careful to allow the lip space to remain between the two plates as in the above photo.
Step 20: Assembling the Lower Brush Holder Section
Carefully align and tape the two in place. Using the Weld-On® 4™ acrylic adhesive, glue both plates together carefully.
After they dry, remove the tape and clean any residue.
Step 21: Setting Up for Attaching Upper and Lower Parts
Collect both assembled parts along with the billow cut to size. You can use 2 or three ribs depending on the depth you need. Align the three Parts.
Step 22: Attaching Billow to the Two Lower Sections
- Now slip one lip of the billow into the lower attachment plate billow slot. Use super glue and from the inside adhere the billow lip to the inside of the slot.
- Slip the other lip of the billow into the brush attachment plate billow slot. Use super glue and from the inside adhere the billow lip to the inside of the slot.
Step 23: Final Assembly and Bush Add On
- When all parts are assembled and clean in to the one, turn the part over so that the brush slot is up facing. Try to insert a part of the brush in to the slot, take a measurement of the diameter and then cut the brush to length.
- carefully use super glue to adhere the brush into the slot while the brush is in the slot. Clean any superglue residue that might over flow.
- here is a link on eBay for the brush i used: click here
- this is the diameter of the tube I used for suction... 32.6 mm Dia cut to the length you need (it was a white painted closet rod)
Step 24: Just a Few Thoughts
When attaching your boot keep in mine to place it at the spindles lowest point above the moving parts. If you need to have it higher up on the spindle you will meed to add more ribs from the shock absorber boot.
I realize that many people have different spindle specs. so when you designing and building your version of the boot. please keep me in mind and show me your upgrades. I would love to see them. this one is working great for me but there is always room for improvement.
GOK
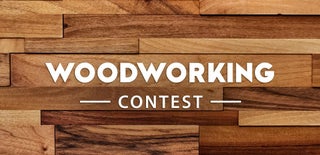
Participated in the
Woodworking Contest