Introduction: Shelly Sense - Wireless Powered (WPC Qi Standard)
PLEASE NOTE: following this tutorial you will loose your warranty and you will also risk to break your Shelly Sense. Do it only if you know what you are doing and if you are aware of the risks.
The Shelly Sense is an amazing product to sense all the relevant things you may want to know about your indoors such as temperature, humidity, air quality, presence detection and it even embeds an IR blaster for controlling your IR devices.
It is a battery powered device, with a microUSB connector on the back, but I noticed that having to connect and disconnect the wire every time I moved it from one room to the other discouraged me to move it at all, thus not making the best benefit from the presence of a battery.
Having wireless chargers everywhere in my home for charging my smartphone, I thought that I could customize the Shelly Sense to support the Qi WPC standard so that I could just move it in every room just placing it on a charger.
Supplies
For this project you will need:
- A Shelly Sense
- A 3D printer (I have a Creality Ender 3 Pro with some customizations on it).
- A very small quantity of 3D printable material as the parts are very small. PLA or ABS both work well as heat involved will not be very high. I used black PLA.
- A Qi wireless power sticker receiver (any similar to the picture will work). You can find many on Amazon and eBay. Shelly Sense needs around 5V @0.45A while charging (measuring from wired USB), so any cheap 5W wireless power receiver will work well.
- Some flexible isolated electric cable, AWG is not too important, just make sure that 500mA will be able to pass through. Any spare cable should work.
- A soldering iron.
Step 1: Print the Attached 3D Parts
For achieving our goal, we will need to print two parts to replace the original base of our Shelly Sense.
One part is the adjustable base support with articulated head that will allow the body of the Shelly Sense to still be oriented as it was possible with the original verison, the second is the bottom panel that we will use to close the wireless power receiver.
The head of the articulated head needs to be smooth enough, but cannot be sanded down too much because you will remove too much material and it will come loose. Thus, it is important to set 0.1mm Z-resolution since the printing stage. No supports are needed.
You can start the print of the two STL files attached, then while the printing goes you can go on with the following steps involving the electronics.
Step 2: Disassemble Your Shelly Sense and Make the Electrical Connections
Whiloe you are printing, disassemble the Shelly Sense unscrewing the two screws you find on the bottom part, once you removed them, the Sense should be able to split vertically into two parts.
Use the picture attached as a reference for the GND and the 5V planes on the PCB: in order to solder your wires (5V RED, GND BLACK), I recommend to scratch the solder mask with a cutter to expose the copper, then solder to the two exposed areas two different pieces of electric cable.
For the moment keep a good cable length, we will cut it the right size afterwards.
You can use the holes present in the housing for your wires to go out from the internal part as shown in the second picture.
Step 3: Close the Shelly Sense Original Enclosure With the New Base
Once your 3D print has finished, you will be able to close the Shelly Sense using the original screws, while enclosing the articulated head into the original housing.
Use the hole onto the 3D printed part to let the wires through.
Step 4: Disassemble and Solder the Wireless Power Receiver
Peel off the paper enclosure of your wireless power receiver to expose the copper coil, the ferrite (black flexible part attached to the coil) and the PCB. Pay attention to the wiring between the coil and the PCB, because it can be very fragile. De-solder the USB/lightning connector from the PCB to expose the GND and 5V pads. The pads are usually labeled with some silkscreen: 5V can also be found as OUT+, VCC, V+, while GND can also be found as OUT-, G, V-.
Place the coil facing towards the bottom part of the 3D printed closure panel, with the ferrite on top of it, then fold the two wires for the PCB to sit on top of the ferrite, as shown in the second picture. You might need to cut the flexible ferrite if it is too big for the space inside the base, you can easily do it using a common pair of scissors.
Now measure the ideal cable length, cut the cables and solder the GND and 5V connections to the wires soldered inside the Shelly Sense.
Step 5: Test and Close!
Once you are done, you can close the two 3D printed pieces together, make a test on top of any Qi wireless power transmitter, and if everything is working as expected put two drops of glue in between the parts to seal the new base.
Congratulations, now your Shelly Sense can be powered wireless on any Qi standard transmitter!
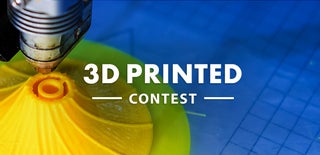
Participated in the
3D Printed Contest