Introduction: Side Table From Scrap Offcuts
About two years ago, I started walking the long, winding, occasionally dangerous path, that leads to building fine furniture.
I still don't have any fine furniture to speak of, but what I do have is PILES of offcuts. A ROOM full. TWO ROOMS. It's becoming a real problem.
In most new projects, I just don't use that many scrap pieces, and so the pile has begun to wildly outpace my scrap usage. Rather than admit I have real issues with throwing anything away (I think there's a word out there for that), I've been attempting to invent more premium feeling scrap builds for my [and other people's] scraps.
This side table is one such attempt.
Attachments
Step 1: Collect Tools and Materials
- Safety Goggles
- Measuring instruments
- Chisels
- Hand plane or electric planer
- Hand Saw or Table Saw
- Hand Drill and/or Drill Press
- Lathe
- A Router, jigsaw, or a CNC (you'll need to cut some circles)
- 7/8 in Forstner bit and a 7/8 wrench
- Scraps -- whatever hardwood you have is fine
Step 2: Choose Your Offcuts and Do Your Prep Work
Any size of offcut will work really, but I've found that 4-6 inch pieces are easiest to work with (for both safety and aesthetic's sake). The first step is really just to get all of the pieces square, flat, and of equal [or at least close] width.
Step 3: Layout Your Pieces
Now that you've made square little building blocks out of your offcuts, you'll want to lay them out into a pattern that you find pleasing. The fusion 360 file attached earlier in the Instructable features side table that is 15" in diameter, but if you can only manage a 13", don't sweat it ;). I found a 15" table to be a nice, useful size, but I'm sure a 13" table will hold a cup of coffee just the same.
If you're having trouble visualizing what your table will look like, cut a 15" circle out of paper and overlay it onto your block pattern. I used the husk of another side table.
Step 4: The Glue Up (slow and Steady)
When I first started building these, I tried to glue everything up at once. That was dumb. Don't be like me.
Glue your table up in small 2-3 block sections. Or don't -- sometimes panicky glue-ups can be exciting.
Step 5: Turn a Square Into a Circle
There are a ton of ways to cut a perfect circle. I cheated and used my CNC (but to be fair, I had to build the CNC first), but a router will work just as well!
Step 6: Add a Chamfer to the Top and Bottom of Your Table
I used a 60º chamfer bit on my router table to cut the chamfers. One large chamfer on the bottom, and one subtle chamfer on top (to prevent break offs on the edge of the table top).
Step 7: Let's Cut Some Legs
Cut 3 pieces that are 24.5" x 1.5" x 1.5". This design uses 23" legs at a diameter of 1.2" at its widest, but anything between 1.2" and 1.5" thick still look good and provide good support.
If we want our legs to be 23" long at their final length, we'll need to add 1" at the top of the leg where it meets with the table top, and 1/2" at the bottom to give yourself a little wiggle room. That leaves us with 24.5".
Optional: Turn your square lengths into an octagon (for easier turning on the lathe).
Step 8: Let's Turn Some Legs
- Turn your leg round (preserving as much of the diameter as possible)
- Turn the top 1" of the leg down to 7/8"
- Turn the very bottom of the leg down to 7/8
- Taper your leg down to that 7/8 inches.
Step 9: Build the Table Base (where the Legs Will Attach)
Cut 3 pieces that are 2" x 5", and cut one end into a 120º angle (30º off each side of one end to form a point). These are all essentially going to be end grain to end grain glue ups, so it's worth adding some dowels for additional strength.
If the cuts don't fit perfectly, don't panic! You can always adjust the angles on one of the 3 base pieces slightly to compensate for the slightly obtuse or acute 120º ends.
Step 10: Step 8: Drill Holes for Your Legs
This step can definitely be completed with a handheld drill, but it's definitely easier with a drill press. The angle you're looking for is 10º. Drill all the way through!
Step 11: SAND. EVERYHING.
I mean it. Don't get lazy on this step. 80 -> 120 -> 240 -> 320 -> good on you if you're going higher.
You won't be sorry.
Step 12: Assembly Time!
Glue the 7/8" legs ends into their 7/8" sockets and drill holes with which to attach the base to the underside of the table top. I didn't specify screws here because this is also a place where you use the spare screws you found under your bench last week, whatever reasonable size they might be (although they should probably be wood screws).
Step 13: Finishing :)
Everyone's favorite part. Put some finish on that bad boy.
Arm R Seal, boiled linseed oil, Rubio Monocoat if ya fancy. You call it, but make sure it's the appropriate finish for the usage it will be getting.
Enjoy your new table, and look with pride on your shrinking scrap pile.
Step 14: Change the Design! Use Some Crazy Species.
I've only ever made walnut and oak versions of these tables, but I'd love to see some new species in the mix.
I also have no woodworking pedigree, so PLEASE improve this design. And send me pics!
Also, this is my first Instructable and I entered the furniture contest. Vote for me if you don't hate this!
Attachments
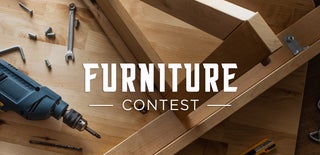
Second Prize in the
Furniture Contest