Introduction: Simple Manual Star Tracker for Astrophotography
A barn-door or Scotch-mount or Haig star tracker compensates for the rotation of the earth for longer exposures in photographs of the sky. Without a star tracker, one gets circular trails and loses detail (see last photo above).
I wanted something really simple. I didn't want to deal with motors, electronics, batteries or power outlets, so a hand-powered design is what I went for--surprisingly, that's good enough at lower magnifications. I also didn't want to deal with the rounded drive shafts of other designs, and by chance hit on a design that gets high tracking precision over a significant period of time with a straight drive shaft.
If you have a very solid camera tripod you can mount the tracker on the tripod. Otherwise, you can build something out of scrap wood, which is what I finally did, and which gave me much more stability.
By the way, note the meteor track in the first photo.
Supplies
- camera ball mount
- four hinges
- four (or fewer, if using tripod) 1/4"-20 carriage bolts, about 4.5" long
- two 1/4"-20 T-nuts
- wood, screws and other miscellanea
- camera (DSLR or mirrorless; I used a Lumix G1)
- optional (for smoother operation): chunk of Teflon
- optional (for aiming camera): green laser, 3D printer
- optional (for additional corrector): CNC router, laser cutter, 3D printer or a jigsaw and a steady hand
- optional (to avoid making a wooden tripod): very steady camera tripod and another 1/4"-20 T-nut
Step 1: Background
The basic idea is simple. You have two pieces of wood connected by a hinge, with a bolt going through a T-nut in the bottom piece of wood, the bolt head pressing on the top piece, and a camera on the top piece. The hinge points at the North Star (or the Southern Celestial Pole), and as you turn the bolt, the camera swivels to follow the stars.
My design uses a 1/4"-20 carriage bolt. If the bolt is 292mm from the hinge, one turn per minute is what one needs to follow the stars. One can then have a rotation wheel attached to the knob with second markings printed on it, and then rotate it by hand in sync with a stopwatch. Being within 5-10 seconds of what the stopwatch is showing is generally good enough at lower magnifications, and this is quite easy to do by hand--one can either rotate continuously, or once every 5-10 seconds. A technical difficulty is "tangent error": as the bolt extends, the angle that the hinge swivels per rotation of the bolt decreases. One solution is to use a design with a circularly bent bolt (usually, a threaded rod).
But there is a simple way to get error compensation by using a carriage bolt with a rounded head in the tracker. The rounded head significantly reduces error. The attached graph shows the error in seconds of arc over time: the upper line is an uncorrected straight-bolt mount and the lower line is my mount with a rounded head carriage bolt. For 60-90 second exposures the error with the rounded head is very small. For maximal correction, after a few minutes of running you will rewind the tracker.
You can also attach a carefully cut or 3D-printed corrector to all but eliminate tangent error. There is an optional step at the end for this.
Step 2: Sand Bolt Head
Carriage bolt heads have embossed text on them. File it off and sand as smooth as you can. I did this by chucking it into a drill press and using a file and sandpaper.
Step 3: Main Assembly
Cut two 3/4" thick boards into a long isosceles triangular shape as in the photos; the short end is where the hinges will go. The shape is not crucial. The only crucial dimension is that height of the triangle must be sufficient that the bolt hole 292mm from the hinges be some distance from the end to allow for room to mount a camera.
Attach the boards with hinges.
Draw a line at right angle to the hinges and drill a hole 292mm from the center of rotation of the hinge. I recommend that the hole be slightly smaller than the 1/4" bolt to reduce wobbling.
Hammer in the T-nut from the inside (i.e., when you close the hinges, the T-nut flanges will be between the boards), so that the bolt will go as shown in the last photo above.
Step 4: Bolt Wobble Reducer
If you put the bolt in the T-nut, you will find that it wobbles, though the wood below the T-nut may damp the wobbling a little. What worked really well for me was to attach a piece of 1/4" Teflon that I got from another amateur astronomer friend, and drill a very tight hole for the bolt through it, and put it on the bottom of the board. A piece of wood or plastic with some lubricant might work, too.
To make the hole fit nicely to the bolt, I rotated the bolt through the hole a number of times, with both a wrench (on the square section of the bolt) and chucking the bolt into a drill. Be careful not to damage bolt threads (on reflection, using a spare bolt is smart).
Then I attached the wobble-reducer with two screws.
Step 5: Camera Mount
I bought a cheap camera ball mount somewhere online and mounted it on the top of the top board with a piece of dowel to raise the camera a little more to allow for even more freedom of movement.
Step 6: Knob
Screw the carriage bolt through its T-nut. You will now want to attach a knob at the bottom. You will be manually turning this knob while photographing. When I make holes with a hole-saw, I tend to save the circles, so I initially attached a 2.4" circle to the end of the carriage bolt. That turned out to be too small for comfortably and smoothly turning, so I eventually switched to a 5" disc, which I attached with nuts and washers. The holes in it are for ease of turning and/or decorative. I also printed out numbers from 0 to 55, every 5, to put clockwise along the top edge of it for ease of timing.
Step 7: Optional: Mount for Camera Tripod
You will need a very heavy duty tripod as the whole assembly will need to be angled at an angle equal to your latitude, which will put eccentric forces on the tripod.
The board with the T-nut will be on the bottom. On the upper side of it countersink a hole (with a Forstner bit) for a T-nut whose threaded sleeve will come close enough to the bottom for the tripod bolt to hold it. I haven't actually tried this as I don't have a good tripod, and the exact location on the board that makes for good balance is something you'll want to figure out.
If you did this, you can skip the next two steps.
Step 8: Wooden Tripod Mount
The barndoor mount will have to be mounted at an angle equal to your latitude. If you plan to travel, you will want to make it adjustable. And even if you don't want to travel, you'll want some adjustment for unlevel ground.
I made a very heavy duty tripod out of some 2x4s with a 3/4" board on top. It's short, roughly made, but super solid and heavy-duty. The photos pretty much explain it all: Cut the ends of the three 2x4s that go along the bottom at 30 degrees. Then for the up-and-down 2x4s, do parallel angled cuts at the top and bottom at the same angle so they are flat on the ground and the board sits on the top. I attached them all with screws and white Gorilla Glue.
Step 9: Wooden Tripod Head
I took a 4"x7"x3/4" board and drilled a 1/4" hole through the middle and then another 1/4" hole nearer the edge (about 1.4" away from the central hole). I then attached this board to the underside of the barndoor mount with two more hinges. These hinges are at right angles to the barndoor mount hinges, but you don't have to obsess about any of the measurements here as it will all be adjustable.
I put a carriage bolt sticking up through the middle of the platform on the top of the tripod. On top of that I put a 7 inch piece of 2x4 with a 1/4" hole drilled through the center. (If you want smoother rotation, put an old CD or DVD between the 2x4 and the top platform on the tripod.) And then on top of that I put the 4x7x3/4 board, and attached it all with a plastic wingnut for easily adjusting tension, and since when I was making the project, I had a lot of spare triwing nuts. You can just an ordinary nut if you like, or if you have a 3D printer, you can print one of my triwing nuts.
Continue the off-center hole in the 4x7x3/4 board through the 2x4. Then remove the top assembly, and make the hole in the 2x4 wide enough that a 1/4" bolt nicely slides through it. Finally, put a T-nut in the hole in 4x7x3/4 board, on the top side. And then put another carriage bolt through that T-nut. This carriage bolt will be used for adjusting the angle to match your latitude.
If you want, you can add two screws and a rubber band to keep things nice and tight.
Step 10: Optional: Laser Mounts for Camera and Polar Alignment
Perhaps the easiest way to aim the camera for astrophotography is to put a green laser in a hotshoe mount. I made a 3D-printed mount. Make sure the laser is turned off or its beam will spoil the photo (see above!). Also, make sure you don't look into the laser and that you don't accidentally point it at another person or an airplane.
Note that my 3D-printed mount allows one to rotate the laser to depress the laser button permanently. BE VERY CAREFUL WITH EYES AND AIRPLANES IF YOU DO THIS, AND MAKE SURE YOUR LOCAL LAWS ALLOW IT.
My 3D-printed mount also has a variant that lets you snap the laser on parallel to the hinges of the mount for easy pointing at Polaris (or the South Celestial Pole).
As another safety measure, I recommend putting an infrared block filter on the green laser, unless you know for sure that there is one. Green lasers emit a lot more light in infrared than in green, which is quite dangerous for eyes, and cheap pointers are missing the infrared block filter. You can buy a filter online and attach it with duct tape or with my little 3D-printable laser pointer filter holder.
Step 11: Photography!
Turn the knob to lower the bolt as much as possible. Mount the camera to the ball mount. Ideally, use a remote cable for the camera.
Sight Polaris along the barndoor mount hinges (or sight the south celestial pole if you're in the southern hemisphere). You can look along the hinges or you can put a laser right up against them. This will ensure that the camera will rotate along the correct axis.
Get a stopwatch or a stopwatch app. Not to destroy your night vision, ideally get one with a red display, like my open source Giant Stopwatch Android app (which you can switch to red mode, and which doesn't have ads that will destroy night vision), which also has a handy countdown before it starts.
Focus the camera manually on something distant (e.g., a bright star or planet). Prepare the camera for a timed exposure for 30 to 60 seconds, pointing at some interesting place in the sky. Set the knob on the barndoor mount to zero (e.g., aligning the zero with the side sticking out furthest from the mount--you don't need to be very precise).
Start the stopwatch (Giant Stopwatch has a delayed-start feature which makes this easier) simultaneously with the exposure, and then manually turn the knob, using the numbers on the knob to stay in sync with the stopwatch. Staying within five seconds is definitely good enough, and is actually not that hard.
Taking multiple 30-60 second exposures and stacking is the best way to proceed, but photo processing is beyond the scope of this Instructable. Here and here is some information on stacking.
Step 12: Optional: Tangent Error Corrector
I designed a tangent-error corrector that may significantly decrease tangent error. You glue it to the top board in the barndoor mount, along the line at right angles to the hinges going to the center of the bolt hole. If you use my exact corrector design, the corrector block should start 287.1mm from the hinge center.
You can make the corrector in one of several ways.
- print out template and cut it out with a jigsaw out of 3/4" wood
- CNC route it out of 3/4" wood; when I cut it out of softwood, it came out so smooth that it didn't look like it needed any sanding, except for the tabs (which I put on the straight side)
- laser cut it out of thinner layers and glue them up
- 3D print and sand nicely (I expect this is going to be hard to get smooth, so I don't recommend it).
The SVG file for cutting and routing, as well as the STL file for 3D printing are here.
I should note that I haven't yet had a chance to try out the corrector.
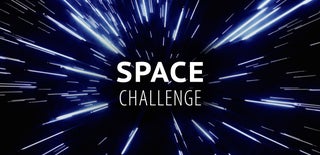
Second Prize in the
Space Challenge