Introduction: Simple Metal Scrap Stool
I made a classic design stool out of metal scrap pieces. This was my first metalworking project. It is not something fancy and I made this to get some welding skills. The scraps were iron square hollow section pipes which I took from my job site for free.
Materials:
- Iron SHS 20 mm
- Pine wooden panel
- Screws
- Plastic pipe end caps
- Iron putty
- Black primer
- Spray varnish
- Minneral oil
- Beeswax
- Woodglue
Tools:
- Hacksaw
- Drill
- Jigsaw
- Palm sander
- Screwdriver
- Hammer
- Grandpa's very old welder
- Sandpaper (80, 100, 150, 240 grit)
- Grinding disc
- Drill adapter for cutting discs
- Dril bits (2,5, 4 mm)
- Putty knife
- Paintbrush
- Clamps
Step 1: Cutting the Pipes
The base of the stool will be a pair of "A" like shapes joined together like pyramid. I formed a rough shape of the first "A" and marked where the pipes must be cut and at what angle the cuts will be. I did all the cuts with a hacksaw, because I didn't have an angle grinder, but fortunately they didn't take so much time. Cutting with hand tools is not very accurate, for me at least, so not all the cuts had exactly the same angle. It was not a big problem and I will try to fix that later while welding. I ended up having four long pieces for the legs, four short pieces for the top and four bigger pieces for stretchers. I trimmed the upper end of the legs flush with the top pieces.
Step 2: Welding and Grinding the Base
I never did any weld before. This was going to be my first time. I grabed a scrap piece and tried to maintain the arc. It wasn't too difficult and after a few times I became an expert! I tack welded the first "A" from one side, turned it backwards and did a full welding on every joint and at the first side again.
I bought a small adapter to let me use cutting or grinding discs to the drill. I tested it only with a grinding disc. It's not the best solution, but the job was done well, in more time. I grinded the welded joints to be flat and the welding quality was revealed. There were some few small and shallow gaps, but I was very happy with the result.
I clamped the pieces of the second "A" to the first and did full weldings from the beginning. After all the joints were welded, I grinded them to be flat.
The two "A" were ready and I could form the base. I tack welded the remaining tops and stretchers to one "A" and then I tack welded the other "A" to them. Since all they seemed ok, I proceeded to full welding the joints. After all the welds were done, I grinded them to not be visible.
The last thing I had to do was to drill holes with a 4 mm bit through the top of the base, to secure the seat with screws. I drilled two holes in each side.
Step 3: Puttying Gaps
To fill all the gaps from the close-to-perfection welds, I bought a can of iron putty. I mixed up a small amount of soft putty with a drip of hardener and spread it over the gaps with a small putty knife. I let the mix dry and after that I sanded the excess with 80 grit sandpaper. The joints were looking like a single piece of metal.
Step 4: Finnishing the Legs
I put the base on an even surface and mark the legs where they needed to cut, to be parallel to the ground. I trimmed them carefully with the hacksaw, so in the end the stool doesn't wobble. I didn't cut well enough and there was a slightly wobble.
I bought some plastic pipe end caps to put on, so the bare metal doesn't scratch the floor. Although the size was right, they needed to be a bit thinner to fit in the pipes. I trimmed each side with a utility knife. I put them in place with a hammer and the stool didn't wobble anymore.
Step 5: Painting the Base
The first step before any painting was to clean every metal surface from dust and oils. I took a clean rag, wet it with acetone and rubed the base twice, until it was clean in touch. I applied two coats of black primer, letting one day between them to dry. A day after the second coat, I applied two coats of spray metal varnish for shining and protection.
Step 6: Wooden Seat
To make the seat I bought a wooden panel of pine from my local hardware store. I cut with the jigsaw two square pieces 30 x 30 cm and glued them cross-grained together to double the thickness. I used almost every clamp I had handy, even my 90 degrees corner clamps for the edges.
After the glue dried, I put all the clamps aside and marked the center point of the square piece. With a compass I marked a circle with 30 cm diameter. I cut the disc out with my jigsaw. To make it smooth I did a lot of sanding. I started with 80 grit sandpaper and proceeded to 100 and 150 grit progressivly. Then, I did a hand sanding with 240 grit sandpaper. Also, I rounded both the edges of the disc to be smooth.
I soaked the finished seat in mineral oil to pop the grain out. I found out that this was the most inappropriate oil I could ever use, because it never cures. I should better use linseed or tung oil, but mineral oil was cheap and more easy to find. Anyway, it was too late to throwback and I tried out a beeswax paste over the oiled wood, just to make a protection film to prevent any oil marks on someones pants.
Step 7: Attaching the Seat to the Base
Everything was ready and it was time to put them together. I turned the seat upside down and put the base above it. I found where it was centered on the seat and with a punch I marked where the pilot holes will be. I drilled them with a 2,5 mm bit. I screwed the seat in place using flathead screws to look nice.
The stool was ready and waited for someone to sit on. This was a funny project and I discovered that metalworking is interesting as much as woodworking. In the future I'll do another metal project for sure. I also gained some welding XP.
I hope I got someone inspired to do simple and nice projects, having limited tools and without any particular experience, like me at this project. If you liked my work, please vote.
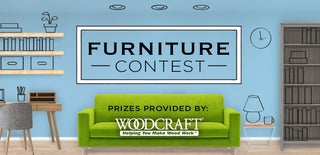
Participated in the
Furniture Contest 2017
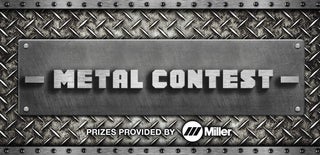
Participated in the
Metal Contest 2017