Introduction: Simple Reusable 3D Printed Mold
Sooo... here's the TLDR version (Full story in the last step)
I screwed up making a silicone mold for a pen turning blank (it ended up as a big sticky mess). And sometimes I'm a little low on that patience virtue...
Since I wasn't able to get material to make another mold locally, and I didn't want to wait for shipping... I went with an "I think it should work" idea and 3D printed a mold for the pen blank with flexible TPU filament. I've made TPU molds before, but never with the intent to put resin in them.
Enough talk. Time to find out just how non-stick thermoplastic polyurethane is...
As you can see, the epoxy casting resin did not become one with the mold! It works! Read on to find out how to make one for yourself!
(If you're asking what is a pen turning blank and why do I need one here's a bunch of instructables on how to make your own writing pens to inspire you!)
Step 1: Tools, Materials, Safety, Digital Files
Affiliate links to the products used in this instructable:
Tools:
(Or printing service like 3D hubs ((or shoot me a message!))
(Don't use solo cups, styrofoam cups or paper cups. They can react with the resin and ruin your project)
-Stirring sticks
Materials:
-Casting resin
(Casting resin will work best, it's designed to be poured and will self degas. (I've used Liquid Diamonds and Easy Cast, I like that liquid diamonds is cured in a day, but easy cast seems more forgiving when it comes to trapped air bubbles))
-Pigment or whatever you're planning to put into the resin
-TPU Filament for 3D printer
(Not 100% required. I was able to get the blank out of the mold fine without it, but it does make things go a little easier)
-Non-stick area in your workshop 😁
Safety:
-Disposable gloves
(Use them, this stuff is a PITA to wash off if it spills...)
-Well ventilated area
(The amount of resin used here is small, I was in my office about 8 feet from an open window)
Digital Files:
I've attached the files for the mold to this step. You've got the STL file for 3D printing plus the Fusion 360 model file and a 3D model file in .step format if you want to modify the mold.
*Note: My posts may contain affiliate links to products I use and feel comfortable sharing. Which means when you click the marked product links in my post nothing changes on your end, and I earn a small % on qualifying purchases. Thank you for your support!*
Step 2: Bonus Step - Another Mold!
OK, I held off adding this one until I knew it would work, and guess what - it works!
So what is it? This is a mold to make a 1 inch cube. It is intended to be used to test how colors or other objects will react with the resin before you commit to pouring a full size blank. Files to make your own are attached below.
In the pictures, I'm testing how shredded cash reacts in liquid diamonds resin. You can see the paper sinks/settles a little bit, so I'll need to add more shredded monies than I initially thought.
Woah there, wait a minute... Shredded Cash?!?!?! How can you af...
No, No, No, I'm not literally shredding my own money... The US treasury shreds the currency that gets taken out of circulation and allows some portion of the shreddings to be sold to the public. If you'd like to get your hands on some, here's the Ebay link to the Cashola I'm using (Ebay is the cheapest place I've found it).
EDIT - 1/25/22 - Ebay no longer has the shredded cash I was using, here is an Amazon Affiliate link to the product I'm using now.
BTW, if we believe the bag o' money contains $500 or more like it says, there's $25-$30 worth of cash in the 1" mold 😎
Step 3: Printing Info
I did do a couple things different while printing since I knew this needed to be a water tight print or I'd end up with (another...) sticky mess.
First - Print a little hotter. I printed this 5*C hotter than I normally print with TPU. This can cause stringing in the print, try to keep your print head from crossing the inside of the mold and try turning up retraction if you have issues.
Second - Turn up the flow rate a skosh. This ensures all the layers and lines get squished together.
Third - Print with finer detail. This is for two reasons. One, it gives the epoxy less "tooth" to hang on since the layer line ridges are smaller. Second, we can't sand out or fill in the layer lines. That's not a huge deal since we're post processing the blank but it will look better when it comes out of the mold.
Fourth - Print at 100% infill. Make it solid. We can get away with less infill for casting things like concrete but for resin, keep it at 100%. Especially since we're going to be twisting and pulling on this thing, we don't want any chance of a layer tearing.
Step 4: Pour It, Pour It Gooood!
It's Go Time!
Mix up your epoxy per the instructions from the resin manufacture. Yes, you already know that it's important, and yes I'm bad at this too... but this is one time we really do need to read the instructions. For example, easy cast is mixed 1:1 while liquid diamonds is 2:1.
Add your pigments.
Dunnna nunn ah nunn, mix it, mix it good!
And then mix it some more.
OK, now we can pour! Have fun with it, swirl the colors, stir the colors, layer the colors, don't be afraid to play with it!
For the video in this step, I'm filming Wiferneer using my 3D printed mold to make a blank for her next pen!
Step 5: Caveats
Using this 3D printed mold to make epoxy resin pen turning blanks has worked great!
There are a few caveats though.
You can't get rid of the 3D printed layer lines in the mold. Which means this is not a final mold for casting something with fine detail. This is a mold for a blank that will be processed further.
While the mold is plenty flexible, it is not as flexible as a silicone mold would be. Because of this, I'm not sure how long the mold will last. So far I've pulled 4 blanks out of it and it is starting to get a slight bow out in the middle near the top. I think if I make another one I'll add some "wings" to the side of the mold to give me something to grab onto and help keep the sides straighter.
I realize not everyone has a 3D printer (yet?!?!). There are many other ways to make a mold, if you're interested in learning more checkout the free Instructables Mold Making & Casting Class
Pen making is fun, but I still have a lot to learn! So we'll keep this Instructable focused on just how to make the pen blank.
Step 6: The Backstory and a Finished Pen
Here's a couple pics of the pens we finished using blanks made from the 3D printed mold. I'll be turning the blue "ocean" blank from the previous pictures soon and I'll upload a pic here when it's done (It's finished! Pics added!).
OK, without further adoo doo, below is the epic battle story of the attempted mold making!
_____
Recently Wiferneer and I went down the pen making rabbit hole. And making our own resin pen blanks didn't look that hard... so we jumped into the deepend right off the bat...
That's OK though!
We had a plan, we had material on hand, we'd watched YouTube and browsed Instructables, and pinned pins, we were prepared and organized and ready! Rar! Lets make some pens!
First, we need a mold for the pen blank. So I whipped open Fusion 360 and made a fabulous rectangle. I extruded that rectangle to the size of the pen blank we wanted, I even gave this rectangle a teeny bit of draft angle so it would pop out of the mold easier. So I guess that means it's not a true rectangle anymore? A for sided object with angled sides is a... come on geometry class... TRAPEZOID!
Right, back on topic. Then I 3D printed said rectangle. After it was printed I carefully sealed it and sanded it and lovingly caressed it and it took longer than I want to admit. But it was a perfect cuboid specimen and would make an outstandingly perfect mold.
Then onto making the box for my rectangular trapezoid to sit in. I carefully measured twice, possibly thrice even, and then cut out my corrugated plastic sheet. Carfulling to guide the blade with a metal ruler. Carfulling to cut away from myself. Carfulling, carfulling... ok, score the bend lines and fire up the hot glue gun.
Come on, I even cleaned the hot glue gun and put in new glue! We have a plan!
Last step was to put double sided tape on the blank and stick it down into the bottom of the mold.
Done! Lets pour!
Dun dun dun... cue the ominous music!
So we were using two part silicone. This would have been fine if the pink part hadn't already "siliconed" on it's own in the sealed container...
I tried cutting it and smooshing it but Nun-uh. It was solid. Fine. Whatever. I'm still pouring the blue stuff in, maybe it'll do something? - Nope. Well, not exactly. It did make a bigger mess than I had before and I guess that's not nothing.
Huh. Well then. Guess we learned the hard way silicone casting materials have a shelf life...
Now what? I still want to make a pen...
To the 3D printer! TPU is flexible and I think it's mostly non-stick-ish. I mean it's a PITA to glue it to anything so it must be non-stick-ish right?! Right. Good. Lets do this. Go team!
OK, now we just need a rectangle like we had but inside out. Yes, an inside out rectangle. And space for a moat around it. And a wall so the moat doesn't leak out. Got it?
No! We don't need a moat. Keep it simple, we don't know for sure if this will work, stick to just a rectangle with an open top. Fine. But I'm adding fillets to the bottom. Fine. Make it so, just hurry up and lets get it printed.
And about here is were we pick up with step one of this instructable so I'll stop with the stream of consciousness disguised as a backstory...
_____
Alrighty then. That's that, and this is also now unofficially the instructable with the most "..." 's in it. What's that even called?! To the internets! - The interwebs says it's called an ellipsis. OK then, and now we know. That's all. Really. Bye bye for now!
_____
If you'd like to see what I'm up to when I'm not Instructable-ing you can find me at these places:
My Website: https://www.makerneer.com/blog
Instagram: https://www.instagram.com/makerneer
Facebook: https://www.facebook.com/Makerneer/
Pintrest: https://www.pinterest.com/makerneer/
My Etsy Shop: https://www.etsy.com/shop/Makerneer
Note: This post contains affiliate links.
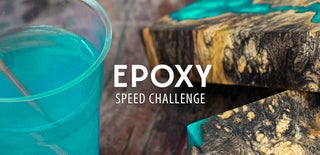
Second Prize in the
Epoxy Speed Challenge