Introduction: Simple Sturdy Low Cost Furniture
This Instructable will show how to build simple, low cost, sturdy, wood furniture that can look good and last for a long time. I recommend reading through the entire Instructable before you begin. I am not a professional wood worker and some of my methods/materials may highlight this fact. I have added a lot of notes on the pictures, if you don't completely understand part of the text, refer to the notes in the attached pictures. This Instructable will show how to build two simple end tables/ bed side tables that are about 25" tall, but these methods can be adapted to make any size desired(pictures are attached of stools, and tables made with the same techniques.). Safety is always important, so I recommend using a minimum of safety glasses/ goggles for this Instructable, a dust mask is a good idea as well. I also used ear plugs to avoid a headache. If you like this Instructable, I would really appreciate a vote in either or both of the contests that it's entered into. The vote button is in the top right corner of the page. Thank you for looking at this Instructable, and if you do end up building it, please post pictures in the comments, I'd love to see what you make.
Required Tools:
Clamps => 14.5" long
Drill
Sander
Sand paper
Block Sander(Optional)
Pocket Hole Jig
Pocket Hole Drill Bit
Small Drill Bit (for pilot holes, slightly smaller diameter than screws that will be used.)
Tape Measure
Phillips Head bit
Pencil
Jigsaw/Table saw/Hand saw/Circular saw (optional)
Required Materials:
Two 2"x2"x8' (AD 1.5"x1.5"x8') boards (I use Select Pine from The Home Depot)
One 1"x4"x8' (AD 0.75"x3.5"x8') board
One 1"x8"x8' (AD 0.75"x7.25"x8') board
Wood glue
Screws (I used 1 1/4" decking screws)
**Update**
The 3D model file for the table I made in this Instructable is attached. It is a Google SketchUp file.
Attachments
Step 1: Gather and Cut Materials
I used select pine boards from the home depot for these tables. The total cost of the wood was right around 50 dollars (USD) to build two tables. If you purchase your boards from Lowes or The Home Depot, you can have them cut to length for little or no cost. For each table you will need Four 2"x2"x24" boards for the legs, two 1"x4"x14" boards for the front and back faces, two 1"x4"x10" boards for the left and right faces, and two 1"x8"x18.5" boards for the table top. If you prefer, you can replace the two 1"x8"x18.5" boards with a single piece of plywood 0.75"x14.5"x18.5". If you use the two 1"x8"x18.5"(actual dimensions: 0.75"x7.25"x18.5") boards for the top of the table, you will need to glue and clamp them to create one board with dimensions 0.75"x14.5"x18.5" and leave it to dry overnight.
Step 2: Drill Pocket Holes and Sand
Using the pocket hole jig and the pocket hole drill bit, drill 3 pocket holes on one side, at each end of each of the 1"x4"x14" boards and at each end of the 1"x4"x10" boards. Then drill two pocket holes on each of the 1"x4"x10" boards perpendicular to the existing holes and the grain of the wood and drill three holes on each of the 1"x4"x14" boards perpendicular to the existing holes and the grain of the wood. (I didn't take pictures, but a diagram is attached and the pictures in later steps can be used as reference.) Note: Do not overheat your drill bits, it will cause them to become dull more easily, especially if you use an aluminum pocket hole jig like I did. If your drill bit gets dull you'll end up tearing the wood like I did and it makes it more difficult to drill the pocket holes.
Sand the table top, sides, and legs and remove all sharp edges.
Step 3: Assembly (sides and Legs)
Attach one 1"x4"x10" to one 2"x2"x24" board. To do this, line up the end of the 1"x4"x10" board with the center of the end of the 2"x2"x24" board. Use a small drill bit pushed into the pocket holes to mark spots to drill pilot holes. Once the holes are marked, remove the 1"x4"x10" board and drill pilot holes for the screws that will go into the pocket holes. Then put glue on the end of the 1"x4"x10" board and screw it into the 2"x2"x24" board. Repeat this process to attach another 2"x2"x24" board to the other end of the 1"x4"x10" board and set this piece aside. Repeat the same steps to create a second identical piece of two 2"x2"x24" boards attached to a 1"x4"x10" board. Then attach the 1"x4"x14" board 90 degrees relative to the 1"x4"x10" boards. Ensure that the pocket holes drilled perpendicular to the grain of the board are all facing the same direction (towards the top, they will be used to attach the table top.) Be sure to use glue on all joints, it will significantly strengthen the table.
Step 4: Prepare and Attach the Table Top.
With the base fully assembled, sand the top surface of the base to ensure that all surfaces that will mate to the table top are flush. Then place the tabletop face down on your work surface and place the base upside down on top of it. Use the tape measure to perfectly center the base on the table top working on one side at a time. When the side is centered, trace the sides that are aligned properly onto the tabletop. You should end up with 4 right angles on the bottom of the table top. I recommend making a key mark so that you can re-align the base with the top after gluing. Once the base is centered on the top, use the small drill bit to mark the spots that pilot holes will be drilled into the top, once all 10 pilot holes are marked, remove the base from the top, and drill the pilot holes. Remember to drill them at a slight angle to match the angle of the respective pocket hole. Apply glue to the top surface of the base and spread it completely. Set the base back onto the table top, ensuring that the key marks are lined up. Screw the base and top together ensuring not to over tighten the screws or they can come through the table top or crack the table top. If you do pierce the table top with any of the screws, back the screw out until it is no longer protruding from the surface and apply a drop of wood glue. When the wood glue dries you will be able to sand it flat. Once the top is screwed to the base, it is a good idea to clamp them and leave them to dry over night.
Note1: The base will probably slide around slightly while placing it back onto the top before it is screwed in, so be sure to line it up before screwing it together.
Note2: A key mark is a good idea because it is highly likely that the opposing pocket holes are not perfectly aligned, and if you attempt to attach the base to the top after drilling the pilot holes and you rotate it 180 degrees the pilot holes and pocket holes will likely be slightly misaligned.
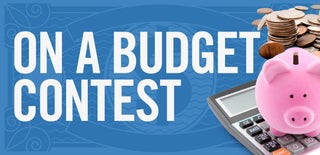
Participated in the
On a Budget Contest
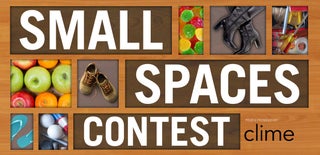
Participated in the
Small Spaces Contest