Introduction: Solid Body Electric Ukulele
I'm a high school industrial technology teacher in Indiana. I teach manufacturing and engineering classes.
For almost a decade I have been using this project in my classes. I had no prior experience with building (or really playing for that matter) any instruments.
The ukulele below is the first one I ever built as a test to see if I felt I could run it in a class of 15-20 high schoolers.
Almost ten years, and many electric ukuleles, later I still have basically no idea how to play a song on one. But, every year I run this project I get just a little bit better at making them and a whole lot better at teaching manufacturing with it.
Get your popcorn ready because this is a long one! This is by far the longest Instructable I've ever made. I think the word count is close to 9000 words. (Sorry about that I was trying to make sure I covered everything.)
I'm not the most organized teacher in the world. I'm getting much better as I approach fifteen years teaching, but still admittedly I'm not great. Because of that fact this project has mainly lived in my brain and on bits of scrap paper that cover my desks all school year.
This is my attempt to put my scattered brain onto "paper."
I hope to show how we have learned to make these solid body electric ukuleles and share my thoughts and tips on running it as a project with a group of students.
First up let's cover what you'll need with the....
Supplies
Ukulele Materials
-Wood for body blank (Preferably around 1.25"x10"x13")
-Hardwood for neck blank (around .75"x1.5"x25")
-Hardtail Bridge
-Guitar/Ukulele Tuners
-Electric Guitar Strings
-Wood Glue
-Single Coil Pickup
-Potentiometer
-Output Jack
-Volume Knob
-Wire
-Solder
-Paint or wood finish
-Fretboard
-Fret Wire
-1/8" or 3mm Acrylic Sheets
-Screws
-Metal (for neck plate)
-Ukulele Nut
Tools/Equipment
-Laptop with CAD/CAM
-CNC Router
-Laser Cutter
-Rasps and Files
-Random Orbit Sander
-Belt/Disc Sander
-Bandsaw
-Drill Press
-Power Drill
-Clamps
-Rubber/Brass Mallet
-Wire Snips
-Soldering Iron
-Screwdrivers
Step 1: Overview
I use this project as an entire semester of curriculum for my level two manufacturing class.
If I just had the students work on this project alone and I didn't worry about teaching other manufacturing topics and skills, I could run this whole thing in a single nine-week quarter.
I've found for my class the best pace has been as an entire semester project. During which I teach the students about:
-CNC Programming
-CNC Setup and Machining
-Tooling
-Print Reading
-Tolerances
-Precision Measurement
-Quality
-Process Flow
-Takt and Cycle Time
-Work Holding
-Material Selection
-Employability Skills
We will also cover a few other odds and ends topics that change or rotate in and out of my curriculum from year to year.
Usually, if I start this project rolling the first week of school, we will finish up with a few weeks of the semester left. This lets us display the kids work for a little while in a public area of the school.
My engineering students have been asking to complete this project in one of their classes next year. If I were to do that the project would overall stay the same but the content during the semester would focus more on CAD, how electric instruments work, electronics, design process, and testing of materials.
Every year I think of new ways I can link a new manufacturing topic to this project. It's been fun having a project that has evolved so much and I still don't feel like I've really got it perfectly dialed in for my curriculum yet.
The other great thing about this project is almost all of the students completely "buy in" from the start. I very rarely get any low effort days from my students during this project. Which in my book is impressive!
The fact that students, who I sometimes can't get to focus and put effort into a project for two class periods, put in a max effort for almost half of a school year with these ukuleles is amazing.
With that little bit of insight into how and when I use this project in my classes, we can get started with .....
Step 2: Designing the Ukulele Body
I’ve done the design portion of this project with three different methods since I began using this project in my class.
1) CAD Software (Design with Inventor or Fusion 360)
2) CAM Software (Design with Aspire or similar software)
3) No Student Design
All three ways work. For me the choice on which way I go I primarily hinges on the class and it's course standards. I’ve always run this as a manufacturing project.
My manufacturing courses and the standards associated with them have changed drastically since I first started using this project. Most recently, I switched to option three as the focus of my manufacturing courses have shifted from a more general exposure to manufacturing skills to a more direct teaching of industrial maintenance skills.
Method 1 - Full Design with CAD software
Currently, I teach CAD with Autodesk Fusion 360. With this option I have the class design their ukulele body from scratch. This provides a pretty straight forward project to teach or utilize beginner CAD skills. This would be my preferred method if I used it in a CAD or engineering class.
When I started this project my manufacturing course had specific standards around learning to use CAD software to design a product. Because we have pivoted away from those standards, I haven't used this method in a few years.
Method 1 Design Steps
The steps I had my students follow when I used this method are outlined and shown below:
Body Profile Design Steps
1) Find an image online of a ukulele/guitar body you want.
I always show previous students' examples and other basic ideas in class before I let them get to work. The biggest point of discussion I have with my students during this part of class are the pros and cons of different designs and issues we have run into in the past that the current crop of students should try to avoid.
2) Save the image to your computer
I stress they should find multiple images they like in case one of their selections doesn't work well with Fusion. We have always had the most success with PNG files, but JPEG, and BMP have worked for us as well. I usually have to demonstrate how to properly save the image to the class or else most of the students end up with a file that was saved as a webpage file which won't work with Fusion 360 easily.
3) Open up Fusion 360, start a new design, and save it.
I always have them save it with a file name like “FirstName_LastName_Ukulele”
4) Sketch a rectangle to represent the block of material the ukulele body will be made from.
The size of the body blank has varied over the years but generally I have my students create a rectangle around 12”x10.5”
5) Insert the image into the design using the INSERT CANVAS tool.
6) Use the body blank rectangle as reference to size the image to the correct size.
7) Use sketching tools to “trace” the image.
You may have to create a new sketch to start tracing your design.
8) Extrude the design to the desired body thickness (1.25 to1.5 inches)
Once the body outline is done and it has been extruded to a solid model the next step is to create the pockets for the ukulele neck and the electronics.
This works best if you physically have those components to measure and work from but could be done without them if needed. You should be able to get the dimensions of your components from wherever you plan to purchase them from.
We make our own necks so I can size that opening on the body to whatever I want, we make our necks 1.5 inch wide.
I routinely have trouble finding a supplier who can get me the same electronics components I need year in and year out. If you are going to run this project with a group of students I highly recommend buying all the stuff you need first, going through the project yourself, and then adjusting the dimensions of your model and toolpaths to fit what you can find available.
The basic steps to model those pockets on your body are as follows:
Neck Pocket Steps
1) Place a new sketch on the front of the uke body
2) Sketch a construction line that bisects the model in half
3) Sketch a rectangle that the neck will fit into and make sure it is centered on the construction line you created in the last step.
We position our necks to sit into the body by at least 2 - 3 inches.
Fillet the bottom corners to fit whatever size end mill will be used later on the CNC router
Electronics Pocket Steps
1) Measure (or find the dimensions for) the pickup, wires, volume control, and jack.
2) Place a sketch on the front face of the ukulele body.
3) Use the measurements of the pickup to make a rectangle that will be big enough for the pickup to fit into.
It needs to be centered to the neck pocket from earlier.
4) Offset the outline of your body inward .25 inch.
5) Sketch a profile that will house your potentiometer and jack.
Try to make it as small as possible without making it be a pain to work with later. It’s a fine line the first time you design this part.
6) Connect the pickup area shape with the electronics shape using the line tool.
Make it thin. This channel will be used to connect the wires from the pickup to the other components. The smaller you make it the less work you will have to cover up that area later with the pickguard. Just be sure it is wide enough for the endmill you plan to use later.
7) Finish the sketch and extrude cut that material away from the body to your desired depth.
I’ve found leaving 1/4-inch of material on the backside of the ukulele is about perfect. So, if you have a 1.5-inch thick body cut this pocket to 1.25 inches deep.
That’s the process I’ve used with my students in the past. It works out really well, the students get to say they designed their ukulele body completely from scratch. Overall, it's a pretty simple, straight forward process that most students can grasp and learn without taking up a massive amount of class time.
Method 2 - CAM Design with Aspire (or similar software)
This method tends to be much faster than using a full-fledged design software like Fusion 360, but the actual design skills needed are much less. I started using this method the first time my course standards changed and the specific standards around learning and using CAD in class changed.
The “designing” aspect of this option is really limited as the only thing the students do is find an image for the outline of the body they want, and then use Aspire software to transfer that outline to usable lines. All that is left after that is for the students to create the areas for the neck and the electronics.
But, boy oh boy can you do some fun designs, very quickly, with this way of creating your ukulele body.
Method 2 Design Steps
1) Find an image online of a ukulele/guitar body you want.
2) Save the image to your computer (Find Multiple)
3) Start a new design on Aspire
4) Set the material setup to the size of your body blank
5) Insert the image (bitmap) to the work area
6) Use the Trace Bitmap tool in the software to convert the outline of image to usable lines
The image above is the reason I have my students find multiple images.
If you trace an image with a lot of detail or background noise you end up with a design you have to do a lot of clean up design work on.
To get around this problem, I always have my students find a silhouette image they like. This takes out all the extra detail and leaves them with just the outline they want.
7) Clean up the lines from the image if needed.
8) Size the image outline to fit into the body blank
9) Create a rectangle for the neck.
It should go into the body at least 2-3 inches and go outside of the body on the top side to make sure the CNC will create a clean pocket for the next later on.
It should be centered on the design so that you can also center pickup pocket and eventually the bridge to the neck.
10) Create the areas for the pickup, wires, volume control, and jack.
The pickup area needs to be centered to the neck pocket.
11) Use the offset tool to help create the border area for the jack. ¼ inch is what we use.
When I switched to this option I had more students be super creative with their body styles. My favorite being a student who made their ukulele look like a fish.
Most of my students tell me they just want to display their ukulele instead of actually learning to play it, so making the design something out of the norm works really well for that.
There are a couple of downsides to this method. The software isn’t as user friendly for the students to learn to edit their designs, Fusion 360 is much more intuitive to use for my students.
The other downside is it takes more time to test and troubleshoot the unique designs. Trying to figure out where all the electronics will go, where the bridge will be installed, how the pickguard will be designed, and all the other little things you don't think about until you have made a few of these ukulele takes a lot of time compared to using a more traditional style of body.
Method 3 - No Student Design
My manufacturing course standards changed drastically again this last year (2022-2023) and pretty much all standards related to CAD were removed. The only standard that I have left that somewhat relates to CAD is “Utilize and apply software where appropriate to the course."
I pivoted away from the design aspect and focused on teaching about CNC programming, machine setup, tolerances, material selection, and process flow. To fit all of those lessons in I decided to just provide my class a file with a standard ukulele body style which they use in the next portion of the project to learn about CNC programming.
This method works great and is super simple. The downside of this method is it takes most of the creativity and ownership over the design from the student.
Students who really want to take on the challenge of designing their own body style I still allow them to, but they mostly have to work extra outside of class time, usually during a study hall, to get it done.
If you have limited experience with running big projects like this in your class, this is the option I would recommend you start with. This way all the students should end up with a decent ukulele. You can always move to one of the other methods down the line if you plan to use it more than once.
While some students preparing to or working on running the router I have the rest of my students move onto.....
Step 3: Making a Neck Plate
You can make this neck plate at any point during the project as long as you have it done before you either paint/finish your ukulele body or need to assemble the neck.
I have my students work on this while they are waiting to run their ukulele body on the CNC router.
This is a review activity for my class. I teach how to read manufacturing prints and sheet metal fabrication in the level one course which my students would have taken the year before.
Most of the time I give my class a metal blank and the drawing.
From there, I let them work without much help from me. I use this time to assess how much of a review I should do on last year's skills. Most of the students don't need any help from me and maybe just a quick hint from a fellow classmate.
The steps that I always recommend the class follow is:
1) Measure and mark the center points of all the holes
2) Use a center punch on those marked locations to give the drill bit a starting place
3) Drill your holes
At this point the screws you will use will be sitting like this:
4) Countersink the holes on the top side of your neck plate.
Go slow and check the size of your countersink with your screw so you don't widen the hole so much the screw head can pass right through. Your screws should sit something like this when you are finished:
5) Clamp your neck plate in a vise and round the corners with a file.
6) Stamp your name on one side of your plate
7) Apply a coat of paint or clear coat to stop rust
If you take your time the end result should look like something this:
And with that done the students can move onto .....
Step 4: Creating the Ukulele Body
From our understanding you can use pretty much any type of wood you want, when you make a solid body electric guitar/ukulele. We started out using reclaimed locker room benches, which were made of oak.
Then during the pandemic, we used plywood as I couldn't find any place to purchase enough hardwood at a decent price. I'm back to using hardwood, this last year we used Ash for the bodies and Maple for the necks.
We have always made our body blanks to be around 1.25 inches thick, 10 inches wide and 12 inches tall. Those dimensions change slightly from year to year depending on the lumber we are able to get.
Next, we need to take our design from the previous step and set it up to run on a CNC router. If you used Aspire or a similar software your design should be ready to program the needed toolpaths.
If you used Fusion and need to transfer your design to a different software to set up your G-code, follow the steps below.
Steps to a Fusion design as a DXF file
1) Put a sketch on the FRONT FACE of your model.
2) Use the PROJECT (P) command and transfer any lines needed to your current sketch.
3) FINISH SKETCH and rename it in your BROWSER to "CNC"
4) Right click on your "CNC" Sketch and select "Save as a DXF"
For the method I use in my class we create three different toolpaths.
We cover the basics of CNC programming before we jump onto the software, this way my students understand the terminology and what they are actually trying to produce.
We use two different types of simple toolpaths, profile and pocket. If you are unfamiliar with those terms you can think of these toolpaths as the difference between a connect the dots drawing and a coloring page.
Profile toolpaths are like a game of connect the dots.
The CNC machine will follow a set path of coordinates over and over again until the depth that was set has been reached.
Pocket toolpaths are like coloring pages where the goal isn't to necessarily follow a path, but to work in a given area without going over the lines.
The CNC machine, while running a pocket toolpath, will work within a given closed off shape to remove material until the depth that was set has been reached.
The three toolpaths I have my students program we call the NECK POCKET, ELECTRONICS POCKET, and the BODY PROFILE.
I go over the information for these toolpaths with my students using a notes page like the one below:
During the notes session I give them the type of toolpath they need to create, where it needs to be, what tooling to select and the depth each one needs to be set to. I also give them recommendations on where they should place their tabs on the BODY PROFILE toolpath.
They take their notes, create the toolpaths needed in the software, and then I look over their work before we set up the body blanks on the router.
If you are using Aspire here are some tips we have figured out with these processes.
Aspire and CNC Router Tips
-The smaller the endmill the longer your toolpaths will take. If you are doing this as a singular project for yourself the runtime of the CNC process may not matter. If you are running this with a class of 15 or 20 students you don't want each ukulele to take 20-30 minutes each. We use a 1/2-inch flat endmill and each ukulele takes about 7-10 minutes in machine time. Each student should only take around 15 minutes total with setup if they paid attention in class.
-Be sure the endmill is fully and securely installed into your router. At least once a year we have a mishap with the 1/2" endmill being pulled out of the collet while the machine is running.
-Be sure to double check the toolpaths, especially if you are doing this in class with students. The most common mistakes I see are students putting in the wrong depth values (forgetting to put in a decimal so instead of half an inch deep its programmed to go five inches deep) and forgetting to include tabs on the profile toolpath.
-We always set a very conservative pass depth for each toolpath. With our 1/2" endmill we set the pass depth to about 3/16". This decreased issues with the endmill being pulled from the collet and that we get an increased lifespan from our endmills.
-Be sure your design is all closed profile shapes. When you click on a shape in your design in Aspire all lines should get selected and turn in a different color. For example, if you click on your body profile and every line but one turns a different color, you do not have a closed shape. You need to join your lines together. Otherwise, you may not be able to get your toolpaths to generate correctly.
If you use the Aspire software like we do, the following are the steps I demonstrate to my students to create the toolpaths the need for the ukulele.
Aspire Pocket Steps
1) Open the Toolpaths Tab.
On Aspire 4.5 that is located on the right/top side of your screen.
2) Select POCKET TOOLPATH from the menu
3) Select the shape/outline to apply the pocket toolpath to.
4) Set your CUT DEPTH
5)Set your TOOL
6) Rename your toolpath.
We use the name of the area and the type of tool for that toolpath. Example "NECK POCKET HALF END"
7) Select CALCULATE
Aspire Profile Steps
1)Open the Toolpaths Tab.
2) Select the PROFILE TOOLPATH from the menu
3) Select the shape/outline to apply the profile toolpath to.
4) Set your CUT DEPTH
5) Set you TOOL
6) Be sure your MACHINE VECTORS is set to OUTSIDE/RIGHT
7) Click the checkbox to ADD TABS TO TOOLPATH
8) Set your tab length and thickness
9) Click the EDIT TABS button
10) Either manually add tabs to your profile or set a constant number and hit ADD TABS button
11) Select CLOSE to return to the profile toolpath menu
12) Rename your toolpath.
We use the name of the area and the type of tool for that toolpath. Example "BODY PROFILE HALF END"
13) Select CALCULATE
After you have created your toolpaths, save them as .nc or .ncc files to be used with your CNC router.
Grab the body blank and get it set up on your router. Along with the vacuum table to hold the spoilboard to the router table, I have my students fasten the body blank to the spoilboard with screws.
The big thing to remember with setting up your body blank for the CNC process is to just make sure your material is flat on your table or scrap board. One of the most common mistakes my students make is when they fasten their body blank down with screws, they don't check to see if their body blank is still flat on the table.
From here you can run the toolpaths you generated. Start with pocket toolpaths and end with the profile. We run the neck pocket first, then the electronics pocket, and end with the body profile.
If everything runs smoothly you should get something like this:
Cut through the tabs to remove the body from the overall blank. You can use any number of saws to do this, we generally use a bandsaw.
Sand off the leftover tabs and start shaping your ukulele body to your desired form.
With the standard Gibson style that I have my classes work with, we start the shaping process by using rasps to get the bulk of the rough shaping done. From there we move onto using files to start smoothing out the form. We end with running through sandpaper grits starting at 60 or 80 and ending with a 180 to 240 grit.
There is one area on the front of body where I don't have my students shape or round off the hard edge. That is front side of the 1/4" wall of the electronics pocket. The way we have designed our ukulele, the pickguard goes right up to the edge of the body in that spot. If the students round that portion too much they will get big gap between the edge of the body and their pickguard when everything is put together.
The last steps to making the body are to drill some holes. They need to drill a hole for the jack and holes to attach the neck.
Input/Output Jack Hole Steps
This process is pretty simple. But, there are two main errors my students make all the time when during this part of the project. First, they don't let the drill bit do the work, they use too much downward force which can cause that 1/4-inch thick wall of their ukulele to break or crack. The second mistake is they drill the hole for the jack either too high or too low.
If the hole is too high the jack will stick out above the face of the ukulele and the pickguard won't be able to be installed correctly.
If the hole is too low, either their jack will go through the wall of the ukulele at an angle making it hard to install or they have to do extra work to remove material on the floor of their electronics pocket to make room for the jack.
The process I have my students follow is as follows to drill this hole are:
1) Place the ukulele body into vise so you can easily drill at a perpendicular angle to the body
2) Place a jack on the end of their finger like this:
3) Position the jack in the electronics pocket where it will be installed
4) Mark the center of the jack on the outside edge or the uke with pencil
5) Double check the marked position and have someone else check it as well
6) Use a scratch awl to mark that placement and give the drill bit a starting point
7) Use power drill to drill through the wall of your uke body
Let the drill bit do the work, don't use too much force
8) Test the jack in the hole
It should be a snug fit
9) Sand the area around the hole to prep for finish/paint
Neck Screw Holes Steps
The neck plate screw holes are pretty simple as well.
1) Line up the neck plate on the back of the ukulele opposite of the neck pocket.
2) Use pencil and then a scratch awl to mark the center position of the holes.
3) Use a drill press or power drill to drill all the way through your wood.
At this stage you should have a ukulele body that is basically ready to be painted, stained, clear coated, or finished in some way.
I don't have my students paint, stain, or clear coat their ukulele body until they have figured out where their bridge needs to be installed. But you could finish the body at this point and be pretty much finished with this part of the project until it's time to install the pickguard or assemble the whole instrument together.
Next, we move onto ...
Step 5: Making the Pickguard
With the ukulele design I have my students use, the front face of the ukulele body always has the pockets created for all the electronics to be placed. To cover all the openings and to have something to hold the pickup and the volume control we make a plastic pickguard using our laser cutter.
With a standard body design for the ukulele the pickguard design cab be based on an already available electric guitar style pickguard.
Knowing how to use dial calipers comes in handy for this step. I will either use this an opportunity to teach my students about dial calipers or as a review if they had learned it in a previous class of mine.
For this step you will need to have the electronics and the screws you plan to use to fasten your pickguard to your body, so you can make your design fit those specific parts.
I have my students measure the width and depth of the pickup, as well as the screw hole locations for that part. They measure the diameter of the post on the potentiometer. Finally, I have them measure the diameter of the screw head that will hold their pickguard onto the ukulele body.
With those measurements you can jump back into whatever design software you're using and start working on your actual pickguard design/shape. The way I show my students how to do this is to use the offset tool again. If you offset the entire profile of the body inwards a certain distance, that will give you a good starting place for your design.
With that you can then use the other sketching/design tools to get the shape of your design. You can cover up as much of your body as you want. But remember you need to provide space to install your bridge later on.
The other issue we ran into when first starting this project is the small gap that is left where the jack is installed, that 1/4-inch wall of the electronics pocket. We design our pickguards to go right up to the edge of the ukulele body at that section.
Eventually you will want a pickguard that is aligned properly to be able to install your pickup and volume control, that doesn't leave any open gaps visible, and that has holes where screws can be used to install the pickguard to your ukulele body.
I have my students test their design out with cardboard on our laser cutter to catch any errors that might have been overlooked. Once they can show me their design works with cardboard I let them pick the color of acrylic they want to use and run their final version.
The method above is what I have used in the past and it worked out well. When I started transitioning to just providing my students with the design for the body I also started providing them the file for the pickguard. This way I could spend more time teaching other manufacturing topics and less time teaching CAD/design. Also, if everyone uses the file I gave them, theoretically it should always work and we have less waste of material.
If you let your students create their own unique design, then they should be able to use this method as a template to create a pickguard to work with whatever they come up with.
Once you have a working pickguard, we can move onto....
Step 6: Installing the Bridge
Before starting to build these instruments in class I couldn't tell you a single name of any part of a guitar/ukulele other than the strings. So, if you are anything like me, the picture below shows the bridge of the ukulele.
Specifically, this a 4 String Hard Tail Bridge. At least that was the name given on the site where I purchased them. We have found these types of bridges the easiest to work for this for our style of ukulele.
From our experience and understanding you have some leeway with where you can install this on your body, you just want to make sure its centered to your neck.
Sometimes the students have already started making their ukulele neck before I have them install their bridge, in that case I have them use their own neck for the next step. If they haven't started their own neck I'll either have a test/classroom neck they can use or at the very least a simple unused neck blank to help them out.
The steps you'll want to follow are:
1) Insert your neck into the neck pocket in the body and clamp it in place.
2) Use a long rule/straight edge to project the edges of the neck down to the ukulele body
3) Place your pickguard onto your body
4) Find a position for you bridge in the space available that will keep it centered to your neck
5) Mark the bridge hole locations
6) Drill the holes
7) Fasten the bridge to the body with screws
8) Erase or sand away any pencil marks
Voila, your one step closer to a working electric ukulele!
Next up we move to ....
Step 7: Making the Neck
I make up a bunch of neck blanks, just like I do for the ukulele bodies, that I then give to my students to complete the build for this part of the project.
The neck blanks are usually around 3/4" to 1" thick, 1.5" wide, and somewhere around 20" - 22" long.
Before explaining further, I want to say I don't think this is the best way to make the necks, this is just the way I have found to work best so far with the equipment and time my class has for this project. Ideally, I think figuring out a way to use the miter saw for the angle cut would be a better, cleaner option.
Creating Headstock Angle
1) Use a jig/fixture to cut neck blank to the desired angle
The simple setup we created helps my students cut their neck at a roughly 15-degree angle with a bandsaw.
2) Clean up the cut so the shorter/smaller piece will sit flat and flush on the underside of the longer piece
We then take the short piece and glue it to the underside of the longer piece to create the space for a future headstock. Because this cut was made with the bandsaw the faces of the wood that need to be glued up are usually in need of a little clean up with a belt sander.
The goal here is to get the two pieces to fit together in a flat position without any gaps. My students who take their time and go slow hardly ever have any issue with this and can finish up in five to ten minutes.
Any of my students who try to rush usually end up taking half a class period, or more, to get this portion of neck finished.
3) Glue the shorter/smaller piece to the underside of the longer/larger piece.
I have to reiterate, multiple times, over multiple classes that the short piece is glued to the bottom/flat side of the longer piece. Don't forget!
Creating the Headstock Blank
Once the glue has dried, we take a scrap neck blank and make up the headstock area of the neck.
I make my students design a headstock that would fit within a 3.5" x 5" area. To do this my students follow the same process I went over in the body design step.
Students find an image and produce a digital design of the headstock that would fit the given area. Their design needs to include the placement holes for the tuners. We use our laser cutter to cut out their design from cardboard. It takes my students two or three attempts to get a working template and from there they can work on their neck again.
1) Clean up the neck glue up from before
Before moving forward with the creating the headstock blank, I have my students clean up their neck glue up and any imperfections on the headstock area of their neck.
If they took their time earlier, they should just have to sand away or scrape off any dried glue.
2) Use your headstock template to cut down the headstock area on your neck to the proper length.
To do this the students take their headstock template and place it on the angled area of the neck they made earlier. They can then mark off any extra length of material they won't need to create their headstock and then cut it off.
3) Use the headstock template again to mark and cut out a length of material from a scrap neck.
It should look something like the image below when you are done.
4) Cut that short length of wood in half down the middle, length wise.
5) Clean up the pieces of the headstock blank so that they can be glued together without any gaps between the pieces.
This again, takes just a little bit of sanding to get the pieces to fit together correctly. If we worked in a more traditional woodshop I can see us using small hand planes to help with this.
6) Glue up the headstock blank.
Once that has dried, just like before, I have my students clean up their headstock area by removing the glue and sanding the headstock clean and flush where needed.
Cutting out the Headstock
From here I have my students trace their cardboard headstock template onto their headstock blank area of their neck.
They can use whatever tools needed to create their headstock shape, but most of the work is done with the bandsaw and spindle sander. At some point they will get their headstock looking like their template.
You could do the next few steps of making the neck any order you want. Since we just talked about the headstock I'll go over installing the tuners.
Drilling the Tuner Holes
1) Use the template again to mark the needed hole locations.
2) Use a drill press and the proper sized drill bits to drill the needed holes.
Most the tuners I have purchased have usually come with a small insert of instructions. Some of the tuners need a through hole with a counterbore on top for a ferrule. Others needed just a through hole for the tuner and the ferrules. If we are ever unsure during class I just have my students drill holes in some scrap to find the right size drill bit for whatever tuners we are using that year.
3) Insert tuners through the holes and mark the locations for the screws needed on the back of the headstock to hold the tuners in place.
4) Drill the holes for the tuners' screws
These screws will be small. I always have to stress to my students to take their time so they don't snap the drill bit.
Make sure you don't accidentally drill all the way through the headstock.
5) Fully install the tuners and check to make sure everything works in their current position.
I always have my students fully install the tuners at this stage, and then remove them until after they apply a finish coat to the neck. This just makes reinstalling the tuners easier at final assembly time.
Cutting to Scale Length
At some point the neck needs to be cut down in length to produce the right scale length. We have played around with concert, tenor, and baritone ukulele scale lengths. The one we have used the most has been the tenor ukulele scale length which, from our research, should be right around 17 inches.
1) Round off the corners of the bottom side of the neck to match the neck pocket on the body
2) Clamp the neck in place and measure from where the bridge is up towards the headstock to the desired scale length, 17 inches in this case, and mark the neck at that spot.
3) Measure from the mark you just made to where the neck angles off into the headstock,
That distance is the difference you need to cut off from the bottom of the neck.
4) Measure and mark that same distance from the bottom of the neck and cut it off.
This should give you a neck that is the desired scale length for your ukulele
5) Round the corners of your neck again so it fits into the pocket on the body.
Clamp it back in place and remeasure. The distance between the bridge and where the neck transitions into the headstock should be the correct scale length.
Neck Shaping
We don't want a sharp edged, rectangular neck. That would be uncomfortable when you play the ukulele when it's finished. To round the underside of the neck we use the same process we used with shaping the body.
1) Mark the area of the neck that will be installed into the neck pocket
2) Clamp your neck into a vise and round the underside of the neck with rasps, files, and sanders.
Don't touch the area you marked, that will fit into the ukulele body, when you are rounding off the rest of the underside.
For the rest of the neck, I tell my students to shoot for one smooth curve from one edge of the neck to the other.
When you are finished your neck should look similar to the neck in the picture below.
Fretboard Glue Up
From here, we can install the fret board. We buy these in bulk but you could also do the math for the fret spacing and make one yourself.
1) Mark the position where your nut will be installed at the top of your neck.
The nut should be installed right where your neck angles and transitions into your headstock.
2) Glue the fret board down flush with one side of your neck. The fret board should stop in line where you marked the nut position.
Be sure you glue the fretboard down correctly. The most common mistake my students make at this point is gluing the fret board upside down on their neck. The fret slots that are really close together should be positioned at the end of your neck, farthest away from your headstock.
3) Cut the fretboard to the same width as the neck and round the corners to match the neck at the end.
The neck should now be in a similar condition to this:
Fret Wire Install
With the fret board in place we can start installing the fret wire. We do this process with a small mallet, fret wire, and some wire snips. I have my students start at the headstock end and work their way down. Try not to leave a lot of overhang on the sides.
1) Clamp your neck to a work table
2) Insert the fret wire into the slot
3) Use the mallet to hammer the wire into the slot.
4) Use snips to cut the fret wire off as close to the edge of the fretboard as possible.
Once all the fret slots are filled, you will want to check to see if they are all set at the same height. For this we use a 24" steel rule.
5) Place a long straight edge across all of your frets at once.
Your goal here is to have your straight edge, sit across and touch all of your frets at once.
If there are any frets that are too high your straight edge will teeter back and forth on that fret and you need to hammer it down further.
If there are any big gaps between a fret and the straight edge, you will either need to hammer all the other frets down to match or pull that fret out and install a new piece.
6) Fix any frets that are too high or too low.
7) File the frets flush and at a bevel to the edge of the fretboard.
After all the frets are set you'll want to file the ends of the frets at a bevel. We use a bevel file, which I think are specifically made for this process
You should be able to run your fingers along the edge of your fret board and not feel any fret wire catching your skin or scratching you.
Final Neck Assembly
8) Install your ukulele nut.
For this step we just make sure the nut can sit flat and flush on the neck. We use superglue to hold it in place. Not sure if this is proper way to install the nut but it works for us.
You could do this step after finishing/painting you're neck too.
9) Finish or paint your neck
If needed give your neck a once over with sandpaper, working your way up the grits as needed until your ready to finish the neck.
10) Reinstall your ukulele tuners and Bob's your uncle you have a finished ukulele neck!
Which allows us to move onto....
Step 8: Soldering the Electronics
I have my students work on their electronics whenever they have a lot waiting happening. This can be when they've painted their body or neck and they are waiting for it dry, during one of the CNC operation times, when the laser cutter is backlogged, or any other point where they are waiting or done with everything up to that point.
I'll go over with the class or have them watch a video on how the electronics are supposed to be soldered together. During this time the students will create a simple pictorial schematic of how they should wire their instrument.
By this time my students have learned to solder electronics in the level one class, but usually they forget or lose their touch for it. Before I give them the ukulele electronic components I usually have them solder together two pieces of paper clips.
When they can show me three quality paper clip joints that don't break when bent and their are no pokey bits of solder left on the joint, I'll give them their parts to solder together for the uke.
Soldering Electronics Steps
1) Gather all your needed items
I have my students get all their stuff at a work station before starting. This includes their electronic parts of the pickup, jack, and potentiometer. Their tools and items to solder which is a soldering iron and holder, wire strippers, red and black wire, a set of helping hands, a wet sponge, and solder. Last they should have their simple pictorial schematic ready to reference.
2a) Strip and prepare the wires
Here students should strip the wires from their pickup. If the pickup has a set of three wires (red/white/strand), like the ones we use, the white wire should be stripped and twisted together with the stranded wire.
Students also need to prepare two small (1.5-2 inch) lengths of red and black wire with both ends stripped. These will be used to go from the jack to the potentiometer
2b) File the pin of the potentiometer off
Every potentiometer that we have purchased for this project has a small metal pin sticking up out of it. If you leave it, the potentiometer will not fit correctly on the underside of the pickguard and your volume knob will sit at an angle. If your potentiometers don't have that little bit, you can skip right on to the next step.
3)."Dry" fit your components together according to the schematic.
I sometimes have the students show me their wiring before I let them move onto soldering. This helps alleviate a lot of frustration down the road.
I will tell them if they have their set up correct. But, if they made a mistake I usually just tell them something isn't correct and make them find it instead of me just telling them .
4) Solder the white/stranded wire to the back of the potentiometer through pin three.
This is generally the hardest step of the soldering process for my students. Scuffing up the back of the potentiometer with some sandpaper usually helps.
5) Solder the remaining wires to their respective places
6) Plug setup into an amp to test
We test each students electronics by plugging them into a little amp we bought off of Amazon. The student will plug in the cable to their jack and then tap on their pickup. If we here the tapping amplified through the speaker, we know their good to go!
Once the students have a working electronics system I have them go ahead and install their electronics onto their pickguard.
Finally with all of that done we can move to.....
Step 9: Final Assembly
All that is left to do now is to put it all together and string it up!
My students will do some of the following steps at different times as they move through the project, it doesn't matter a tremendous amount when you do them. You just have to complete them to put the whole thing together.
Remaining Steps/Things to finish off
(Again you can do these in any order for the most part.)
1) Install your pickguard to your body.
Be sure you install your jack onto your body with a washer and a nut before anything else in this step. Position your pickguard with the electronics installed onto your body. Make sure it is where you want it and tape it down. Mark and drill the holes for your screws and then fasten the pickguard to your body.
2) Install your neck
If you haven't done so already, predrill your holes into your neck. Use the same process as before with the neck plate and drilling the holes into the neck pocket part of the body. Clamp your finished neck into place, drill through the holes in your body into your neck and be sure not to drill all the way through your neck. We generally use 1-5/8" long screws to hold the neck on.
Once you have predrilled your holes. Position the neck plate where it needs to be and drive the screws into the neck.
3) Reinstall your bridge
4) Install the strings and tune
FINISHED!
Step 10: Show Off Your Hard Work
With everything done, plug it in and shred!
Step 11: PBL Activity - Workholding
I've been able to finish this project in my classes with a couple of weeks left in the semester, which leaves some time to do other things. In the past I've let the kids make up their own ukulele stands or we used the time to prep for the next quarter of our class, which was usually welding.
This year as a class we took on a project-based learning activity based around designing and making a workholding device for the ukulele project.
The problem that I posed to the students this year was:
"If we were a ukulele building company and wanted to increase our throughput, what process could we design a workholding device for to increase the speed and number of ukuleles we could make."
The students know very little about workholding devices at this stage of the class. We had a class discussion about fixtures, clamps, vises, and similar tools and I showed the class several examples of how workholding devices are used in manufacturing. The examples ranged from very common, like a simple vise, to very complex, like one of a kind fixtures to hold complex aerospace parts during production.
The process we chose to try and improve was the engraving of our initials or a design onto the back of the ukulele body.
As a class we brainstormed ideas, made a few simple sketches, did some quick design work, and then we made our workholding device.
Without the use of our workholding device we timed the operation of engraving two sets of initials on the router. (We ran the actual toolpaths in the air just above the material.) After the engraving operation ran once, we switched the ukulele bodies and ran the initials toolpath again.
That whole process took about four minutes to set up and engrave two sets of initials. The part that slowed us down the most, was zeroing the machine/checking to see if the zero was accurate after the first run.
We then did the same test with our new device.
The design, shown above, was just a simple pocket for the ukulele body cut into a piece of plywood. There is a hole in the center that would use the CNC router's vacuum table to help keep the uke body secure during the machining. The idea being that from one ukulele body to the next we wouldn't need to re-zero the machine.
With the use of the device we cut the time from four minutes down to about one and a half minutes. Which was a massive improvement! Remember though, we were running these processes in the air, not engraving the wood. When we ran a full test by actually engraving initials into the body, we noticed our new workholding device wasn't going to work.
The engraved letters in the picture might look fine, but what we found was the vacuum table with our design was not strong enough to hold the ukulele body in place during the machining. The bodies would eventually shift while the bit engraved the letters, which would ruin the engraving.
We didn't have enough time to fix the problem but we did come up with a possible solution as a class. The vacuum table uses half round foam strips to help create a tight seal to the table. We didn't design any way to use the foam strips in our prototype. If we added some channels on the bottom of the pocket that would hold the strips, we think that would have solved our issue.
In the picture below, you can see the vacuum hole on the table surrounded by the foam strips. The foam helps hold our device down to the table.
After our class experience this year here are my thoughts on how I will set this up next year.
The prompt I plan to use is:
"If we were a ukulele building company and had an order of five ukuleles to build and ship. What is a workholding device we could make or use to reduce the time it takes to complete one of our processes by 25%?
This will run as a small group project, for me this means no bigger than three students per group. The groups will then have to begin researching different workholding devices used in manufacturing.
I will have the groups think through and list all the different steps and processes it took to build their ukuleles. The groups will then decide if a jig or fixture could help reduce the time it took to complete one of the processes that they listed.
At this stage I will just let them run with one of their ideas. The students would have the skills and knowledge needed to be able to build the device they come up with. Each group will have to prove if their device works by running similar tests to what my class ran this year.
To finish the activity, I will have the groups present their solution and findings to the class and to a panel of local industry professionals/teacher/administrators.
In preparation for running this activity I am going to need to prepare the different parts of the ukulele that would allow the students to run tests, without using a bunch of the more expensive material we use for building the ukuleles.
I plan to make around ten ukulele body blanks out of cheap plywood. I would also make ten or so ukulele bodies out of same cheap materials.
I plan to prep the neck blanks using 2x4s. I'll make the blanks in their original form (before any cuts are made) and build out several neck blanks that have been cut and glued up in a state that they would be ready for the headstock design to be cut out.
This is a specific project-based activity around building these ukuleles but I like the idea enough I'm pretty sure I could translate the idea into other projects of mine.
Step 12: The End Bit
Thank you so much for checking out my Instructable. I truly appreciate people taking time to view my work! Please feel free to take this project and turn it into something better than what I have here.
If you make one or use it in your class let me know in the comments below or shoot me an email.
Also, if you noticed anything I'm doing wrong with building these or have ideas on how we can do it better please let me know in the comments.
Subscribe to my fledgling YouTube Channel Here for more shop class projects!
(And future build videos on this project)
If you teach shop class of some kind, I've started a little website to document/compile shop teacher content/curriculum. I'm really just getting started with it but I hope to be posting much more to it soon. If you want a more official lesson or project plan/class overview of this project it will eventually be on my website.
Find it at Shop Class Builds.
Again, thank you for taking time out of your day to scan through my project!
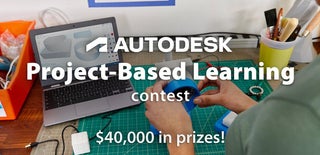
First Prize in the
Project-Based Learning Contest