Introduction: Solid Wood 3D Catan Board
I really like playing board games, but I find that when you're not playing them you just pack them up, stick them away in the basement... they're kind of out of sight out of mind. I wanted to try to find a way to take a board game that I really like and make a really nice version of it that I could have on display even when I'm not playing it.
Supplies
Files: https://github.com/ExplodedViewProjects/CatanBoard
Ingredients
- Ash wood board 1" thick
- Wipe-on polyurethane (https://amzn.to/3gmi6Zu)
- Paint (https://amzn.to/36EXlnz)
- Velcro (https://amzn.to/2X1D1cC)
- Magnets (https://amzn.to/2TFFMhQ)
- Toothpicks (https://amzn.to/2zt9nUI)
- Grey Filament (https://amzn.to/2XrDYKh)
- Super Glue (https://amzn.to/3gpo2B8)
Tools
- Sandpaper (https://amzn.to/2X2m81v, https://amzn.to/2X0LX1W)
- Latex Gloves (https://amzn.to/2AU9mJK)
- Paint brushes (https://amzn.to/2LYfl2s)
Step 1: Model the Tiles
Inside Blender, create a circle mesh. Only give it six vertices, which forces it to be a nice hexagon. Set the fill to "triangle fan" inside, which will give you a few vertices to start working with. From there, do a subdivision a few times to bump up the number of verticies/detail. Switch over to sculpt mode and just start pushing the land up and down to make different features. Remember to add lots of little details into the tiles. They may not be super visible when you first machine them, but they will show up in the end after they are painted. Areas like rocks falling down to the mountains, a little path, or a lake will give you lots of details to highlight, which will add life to your world.
The images in this step only show a mountain tile, but the process is the same for all other tile types.
The only minor exception to that is for the brick tiles. For those, I created some cylindrical shapes and removed them from a hill with a boolean modifier. That made some nice sharp cuts, which made it appear to be excavated, which is hard with sculpting.
Step 2: Make the Tiles Exist
I had the tiles machined at a local machine shop since I don't have a router. I used ash because that's what I had in my shop. It has a fairly coarse grain to it, which worried me at first, but it ended up turning out really well, partly because of the grain.
I've provided the files that I had machined, as well as some different ones that can be 3D printed.
I put 3 coats of wipe-on polyurethane on all of the edges and the tiles, making sure to not coat the areas that are to be painted. I want to paint directly on the wood to get good adhesion. Between coat 2 and 3, I sanded everything down with 220 grit sandpaper. This really gave it a smooth feel and a great surface finish.
Step 3: Start on the Edges
I used another piece of ash that I had laying around and planed it down to roughly the height of the edges that I wanted. I used my table saw to cut them roughly into shape.
Using my router, I cut these little grooves into one side of the boards. They are actually used for storing the pieces when we're not playing with it. I printed out a scale drawing of these slots and then measured them one at a time. I feel like this was a slow way to do this, but I'm also not entirely sure how I would do it differently.
Step 4: Add the Mitre
I'm cutting the edges to the right width, making sure that it's as close to the right size as possible. This really helps because I have to use the outside tip as a reference when cutting the angles. If this width is wrong, the whole ring of pieces might not fit around the tiles. I'm using calipers on my table saw to make sure they're accurate.
I had a really hard time getting the bevels on these to be really nice and accurate. I tried a couple different ways and kept having issues where the angles were too wide or too short. I used an angle copier to copy the angles off of a printout and put that onto my chop saw. This worked out the best out of a lot of different things that I tried. The angle gauge on the bottom of the chop saw isn't super accurate either.
Once all your edges are cut, do a test fit around the tiles. This is also the first time you can step back and get a good look at the progress of the project as a whole. You want it to be a reasonably snug fit, but not too snug, as throughout the seasons your pieces will expand and contract a bit. You want a little bit of play in your edges holding it together. About 1/8" across the whole board is probably enough.
Step 5: Start Painting
With 19 tiles and all of the water, there was a lot of painting to do. I just used the cheapest matte acrylic paint that I could find on Amazon and also the cheapest paintbrushes.
I'm by no means a great painter. This is the first time I've ever really done any kind of a bigger painting project, especially with this level of detail. There was a lot of trial and error.
If there is one piece of advice I can give for this step, it is this: It is just paint. If you do something wrong, just paint over it. No matter how badly you mess up, you can paint-out the whole piece and start again. Relax and try things. Not everything will work.
For all of the tiles, regardless of type, I mixed up a base colour that was darker than I wanted and did a good base layer of that. After letting that dry, I added progressively lighter layers on top of the same colour, just lightening with white or yellow, making sure to have less and less paint on my brush each time. This emphasized the highlights on the pieces that were added when the modelling in Blender was done.Those thin, lighter layers accentuated some of the details that actually brought out a lot of the grain in the wood. Originally I thought I wouldn't like it, but I actually really did. It added a lot of detail to these pieces that just 3D printing or really hard, smooth wood wouldn't give you.
Step 6: Keep Calm and Paint On
In a lot of cases I would pull out the actual Catan tiles, just to get a reference of what color I was looking for.
In the case of the desert, it is pretty bland. There aren't really a lot of details in it, so when I modeled it, I brought in a picture of a dinosaur skeleton and added it so that that could be embossed. This light extra height was picked up by the lighter layers of painting and added depth to the world
The wood tiles were the ones that I was most concerned about, which made me procrastinate about them until the end. There is grass around it and bush in the middle. Both of those are green. My concern is that it would just turn into this green lump and you couldn't tell what it was. I ended up going outside and pulling some grass out of my yard and some leaves off the trees and bringing those in and trying to colour match them as best I could. This seemed to go a really long way. Grass is more of a yellowish tinge as it dries out whereas leaves are usually a hardier green
Step 7: Protect It!
After putting all of this work into machining the tiles and sanding them down and painting them, I really wanted to protect my work to make sure that nothing damaged the paint. This paint can chip off fairly easily. Adding a coat of wipe-on polyurethane is a good way to protect the paint, and it also accentuates the colours slightly. I put on a fairly heavy coat with a paint brush to make sure I got into all of the details.
Step 8: Magnets!
To hold everything together while you are playing, I put magnets in the end of each edge-piece.This way you can easily snap the pieces together they'll hold, but it doesn't add a whole lot of extra hardware.
The problem with magnets is they are somewhat forgiving on positioning relative to one another, but they're not super forgiving. I wanted to make sure that the holes they were mounted in were all accurately aligned.
There are lots of ways you can do this if you have finesse. I don't. I ended up modeling up a tiny, little jig inside Blender that I can slide over the end of each of the edge pieces. This is a guide for the drill bit.
Step 9: Put in the Magnets
When all the ends were drilled out I used some quick clamps to clamp them together and hold them as one piece, which made it much easier for me to work on them. I used some 5 minute epoxy and a nail to hold the magnets. One thing to keep in mind when doing this is make sure that all of your pieces are clamped the exact same way. By doing this, it makes it so you can just quickly stick in the magnets from a stack and then they will all have their poles in the same direction. You will see by one of the pictures above that I missed this. That means I glued 2 of my magnets in backwards. I couldn't use that piece anymore. I had to throw it out and make a new one as there was no way to remove the magnet. I used the head of a nail to push them flush. Not too deep, but they are rare earth magnets, so they should be strong enough, even if they are a little recessed.
Step 10: Final Touches
For storing all of this, you could put it all into a box or a bag. What I did was use those slots that we cut in the backs of the edges. You can slot the playing pieces into the backside of the edges. Once they're all in, you can sandwich them on three sides and use a piece of velcro to wrap around and hold them all tight. It holds reasonably well and it packs up fairly small too.
Unfortunately, my design had some flaws. This system only worked for the main pieces. I have no idea how I thought the edges would hold the remaining tiles. They definitely didn't.
Step 11: Intermission...
This is a long instructable. Take a break here and relax. You've earned it :)
Step 12: Model the Flags
In Blender, add a circle. I'm making the radius of the circle one and a half millimeters, which makes the diameter three. That is about the size of a toothpick plus a little bit of room to spare.
Hit extrude (usually E) and then escape to extrude extrude new vertices, but not make them go anywhere. Scale the new verticies (usually S) out until they look like a good size. Next, extrude the whole thing up fifteen millimeters. This is also an arbitrary number, but it seems to fit. View the model from the top view and make sure you're an orthographic not perspective mode. This makes it a lot easier to work. Select just a few vertices on the side and extrude them out again aling the X-axis by whatever amount looks good. Also a fairly arbitrary amount. With just the end of the flag selected, scale them to zero along the x so there is a flat end.
Add some text and rotate it around the X so that it's upright and aligned with the flag. Edit the text to be a numbr for the flag. Press Enter and add a period for the dots that represent how common that number is.
Under the text options, set the line spacing much lower so the dots are brought up into a nice position. Also change the horizontal spacing to centered, so it looks nice and is consistent. Scale the numbers up so they look like they are in the right spot, then modify the flag itself so the whole thing looks to your liking.
To give the flag just a little more style, press CTRL + R to put in a loop-cut around the middle of the flag and press ESC to centre the cut. This will give you some extra verticies to move around for style
Go through and create the numbers for all of the the different tiles. Remember to update the dots for each number too. Once all your numbers are created, go into object then convert to mesh using the Convert menu. This will take all of your numbers and give them vertices as a mesh instead of as a text object which lets you modify it easier. Select all of your numbers and hit tab to go into edit mode. In blender 2.8, you can edit multiple objects at once, which makes this step MUCH faster. Extrude the numbers so they stick out the front of the flag. Then, duplicate the numbers and their dots and rotate them 180 degrees around to the back-side of the flag.
We need to add a boolean to combine the numbers and the flags. This is super important if you're 3d printing. When you're 3d printing you, can't have different intersecting bodies. A lot of slicers will have problems with that. Select one of the numbers and add a boolean modifier. Make the operation a union and choose the flag object. To apply this to all of the numbers, select all of the numbers (and the one with the modifier last) and press CTRL + L. Choose modifiers. This will copy the modifiers from the one mesh to all of the others.
We need to export them each as their own STL to be 3d printed. Go to file > export STL. In the options, you need to set batch mode to the object. This will export each flag as its own STL file. This is much faster than doing one at a time.
Step 13: Print the Flags
Once we're all exported, take your STL files and 3d print them. I used a 0.1mm layer thickness to keep cleanup to a minimum.
Step 14: Paint the Flags
Once they're 3d printed, just get some cheap latex paint and really small paintbrushes. Add a fairly thick layer of black paint on top of all of the numbers and the dots on the bottom of the numbers. For the standard numbers, I use black, and the the 8 and 6 flags, red.
If you do over paint a little bit and you get it on the areas you don't want, you can usually go back with a sharp knife and scrape it off so it's not really a big deal.
Instead of making a different port sign for each material, I added a little bit of a bevel around the edges and then just painted the edges of the port signs the colors of the resource that the port is for. The three-to-one ports are painted blue.
Step 15: Flag Poles
This is optional, but what you can do is just take some wipe-on poly and put this on some toothpicks. Yes, I'm putting poly on toothpicks. I know that's overkill, but it will make them last a little bit longer and it makes them blend in closer to the rest of the set. Once they are dried, use some nippers to snip off the ends. You could use side-cutters as well, but since they are a sheering motion, you might end up getting a rougher cut. If the end of the toothpick does fray/splinter, you can use some 220 grit sandpaper to clean them up.
To attach the flags to the toothpicks, a drop of super glue in each one works well. Make sure to spin the toothpick when you put it in to ensure good coverage.
Step 16: Pole Holes
To give the flags somewhere to stand, drill a small hole into each resource tile. For the ports, drill the holes in between the two areas where you might have settlements. When drilling the holes, try to find somewhere near the middle in a slightly thicker piece of wood. Also, look for an area where the wood is flat on top. This will help keep the the drill bit from bending/walking.
Step 17: The End
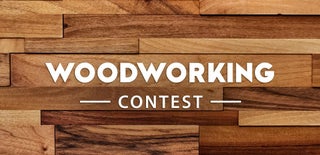
Participated in the
Woodworking Contest