Introduction: Solid Wood Turned Clock [Working!]
Woodworking is a fantastic way to create functional and long-lasting works of art. With quality pieces easily outliving their creators, why not make a wooden piece that keeps track of time - A Solid Wood Turned Clock. Using a lathe, some spare lumber, and creative thinking, I will provide you with a step-by-step guide toward creating a wooden clock of your own. Whether you are interested in taking up woodturning as a hobby, or consider yourself an expert, making a clock is a different approach than the usual turning projects of pens, bowls, and peppermills.
Why Turn a Wooden Clock:
- Unlimited design possibilities
- Functional art
- Great gift idea
Approximate Time to Completion:
- 2 - 5 hours (Depending on Skill Level & Chosen Design)
Supplies
Materials:
- Clock Movement Kit (Amazon)
- Solid Lumber: Preferably Hardwood without Cracks (~ 8 x 8 x 2 inches)
- Wood Finish of Choice (Odie's Oil)
Required Tools:
- Woodturning Lathe
- Lathe Chuck w/ Jaws (Nova)
- Lathe Faceplate Chuck w/ Woodscrews
- Woodturning Tools:
- Roughing Gouge
- Skew Chisel
- Saw (Hand, Table, and/or Bandsaw)
- Wood Chisel & Hammer
- Drill (Hand or Chuck)
- Screwdriver (Hand or Electric)
- Sandpaper (Grits: 150, 240, 320, 400 & 600 - Amazon)
- Measuring Ruler and/or Compass
- Pencil / Marker
- Safety Gear:
- Safety Glasses
- Hearing Protection (Earplugs)
- Face Mask (While Cutting & Sanding)
Nice to Have:
- Woodturning Tools:
- Scrapper - For a Smoother Turned Finish
- Scissors - If Needed to Cut Clock Hands
- Electric Rotary Tool - To Aid in Recessing Clock Kit
- Tape - For Visual Depth Marker on Drill Bit
- Glue - If Affixing Clock Numbers or Markings
- Paper Towel or Cloth - To Apply Finish
- Notebook / Paper - For Sketching Designs
Step 1: Select Lumber
Consider your clock's desired size. It is ultimately up to you and might depend on the size of your clock kit's hour and minute hands, maximum lathe size, or available lumber options. I chose lumber I had leftover from a previous project since I liked its dimensions and thickness.
If you are purchasing lumber or already have a wide range of options, a good starting point is to measure the length of the hands included in your clock kit. The minute hand of my kit measured at just under 4.75 inches from its center hole. That means an interior diameter of 9.5 inches is needed for these hands to travel a full circle unimpeded.
Since I did not have a board of that size, I decided to cut each hand to reduce its length to match what I already had available. There was no math involved in choosing where to cut. Instead, I found a length that looked visually appealing for my clock's size.
Step 2: Prepare the Wood Blank
Using a ruler, find and mark the center width of your board. A compass can help determine the potential size of your clock's outer diameter. Place one end of the compass at your center mark, then adjust its width until you find a size that best utilizes as much of the board as possible. I even used the compass to etch a line as a visual guide and traced over it with a pencil.
Technically, you do not need to define the clock's shape since you will eventually create a perfect circle with the lathe. Although, in doing so, you will have a better idea of what can be cut away to reduce your lathe time.
Use this time to determine how thick you want the edge of your clock. This edge will act as a raised rim surrounding the clock's face.
Tip: It might be helpful to mark the areas of the board you will be cutting away. It can help you visualize your design but also help in the following steps.
Step 3: Cut From Board
Now it is time to turn your piece of wood into a more manageable turning blank.
If your selected board is on the longer side, start with a table saw to separate your blank from the rest of the board. Set your fence so that the blade will cut a vertical line outside of the outer circle made in the previous step.
For smaller length boards, or if you do not have a table saw, use a handsaw, circular saw, or proceed to the next step.
Note: Use caution when using power equipment, especially a table saw. Check out this helpful Instructable on How to Use a Table Saw by Sci_Fi_Mind to learn the basics. Remember to wear your safety gear!
Step 4: Remove Corners
Using your previously drawn lines, remove any excess wood so that only a rough circle-shaped piece remains.
A bandsaw makes cutting curves a breeze. Following the outer edge of my clock's diameter, I cut off each corner keeping slightly away from the line itself.
Important: When cutting closer to the circle, stay a few millimeters away from the line. There is no need to be perfect since a circle will evolve when turning the blank on the lathe. It is always better to have a little extra room than to cut too close and end up with a smaller turned piece.
Note: If you do not have a bandsaw, you can use a handsaw or mount the entire square on the lathe. It will require more work when turning but will ultimately give you the same result. Want to learn the finer details of using a bandsaw? Check out this awesome Instructable: Steps for Using a Bandsaw by darbinorvar.
Step 5: Separate Wood Blank
With cutting complete, you should now have a circle-shaped blank ready for the lathe.
Discard the corner pieces (or add to your "cutoffs bin"), as you will only need the center circle moving forward.
Step 6: Sketch Design Options
Since you have now turned a piece of lumber into a turning blank, things might be easier to visualize at this point. Now is a great time to sketch out designs for your clock's face.
To create the face, you will be cutting into your blank similar to how one makes a wooden bowl on a lathe.
Typically when I turn, I prefer to designs on the fly based on the grain pattern in the wood. Although for this project, I decided to brainstorm a few concepts first as there a countless ways to go about it.
You do not have to be an artist. Simply putting your ideas on paper might help you decide which look you like best. You might even incorporate a few features from each into your final design.
Note: You can sketch two views of your designs; one looking at the clock's face, and another as a cross-section. Both provide different perspectives and help you visualize how to go about turning your design.
Tip: You can trace along the bottom of a soup or soda can to create perfect outer circles when designing.
Step 7: Center Faceplate Chuck
With your plan on paper, it is time to start turning. There will be three "sides" of your blank you will need to address: the front (clock face), the back (battery mechanism), and the edge.
First, we will address the back of your clock. This step will provide a double benefit. First, you will need a way to mount your blank when turning the clock's face. To do so will require the creation of a mortise recessed into your blank. Second, this recessed cavity will also act as a place to insert the clock mechanism and battery. A win-win!
To create the mortise, you will need to mount a faceplate chuck to the front of your blank. You will want this to be as centered as possible to maximize the overall clock size.
Again, I used a compass to confirm the chuck was centered using my drawn exterior line as a reference. Once centered, hold in place and trace an outline around the chuck onto the wood itself. That way, if it were to get misaligned, or move during drilling, you know where to reposition it.
Step 8: Anchor Faceplate
Using a drill and a slightly smaller bit than my woodscrews, I predrilled each hole of the chuck into the wood blank (using the chuck itself as a guide) and then sank in the screws with a cordless drill.
Make sure the chuck sits flush on the blank's surface and feels firmly attached.
Important: Take note of the screw length. Too long, you will be leave holes in the face of your clock. Too short, you risk the blank separating from the chuck while turning. Consider using screws with widely spaced threads for a more secure grip.
Step 9: Mount on Lathe
Now we can head to the lathe. Take your blank and thread the faceplate chuck onto the headstock (powered side) of the lathe.
Check to confirm everything feels solid and firmly connected. If it does, it is time to begin turning!
Step 10: Measure Mortise Depth
Since we will use the mortise cavity to recess the clock mechanism, we want to make sure it is deep enough to fit. That way, you will create a finished look and make it easier to hang your clock on a wall.
Measure the thickness of your clock kit's mechanism body. You can measure with a ruler or eyeball it. Either way, make the total depth slightly longer than its actual thickness.
Find a drill bit sized to match the protruding center shaft of your clock mechanism. In my case, I found a 5/16 inch drill bit worked perfectly.
Using a piece of tape, place it on the bit to mark the total width of the mechanism body. The tip of the drill bit to the edge of the tape should be slightly wider than the actual width of the mechanism. That way, you will have a clear visual of when to stop drilling and eventually turning.
Step 11: Drill Depth Guide
Using either a handheld drill or a drill chuck (pictured), drill into the center of the wood blank until you reach the edge of the tape marker.
Using a drill chuck simplifies this process as you only need to turn on the lathe and slowly advance the drill into the blank.
Note: Ultimately, you could skip this step altogether and check the depth while turning, but drilling a hole acts as a timesaving tip so you do not need to check and recheck any measurements during the turning process.
Tip: If you only have a handheld drill, it might be easier to unscrew the blank from the lathe and work on a level surface. You could also use a drill press if available.
Step 12: Measure Jawed Chuck Width
When turning the clock's face, you will use a jawed chuck. This type of chuck requires either a tenon or mortise that it will grip onto with its dovetail-shaped jaws.
It is important to make sure your mortise is the right size. Too small, you will not be able to attach it. Too large, you will not be able to open the jaws to apply enough pressure.
Using a ruler or compass, measure the width of the jaws while positioned so that they create a perfect circle. In most cases, this will be somewhere in the middle of their travel range when being opened or closed with the chuck's key. Turn the key in the chuck until you see each jaw align into a circle.
Take this measurement and either mark it on the blank or keep the compass nearby to reference while turning.
Step 13: Turn the Mortise
If your lathe has the option, set the speed to around 800-1200 rpm. A lower speed is more forgiving when creating specific-sized shapes since the blank has not been rounded true and could produce a mild vibration at higher speeds.
Adjust your tool rest to be close but not touching the blank. Grab your tool of choice and turn on your lathe. I prefer using a pointed carbide when making mortises, but a skew chisel will work just as fine too.
Starting in the middle (near the drilled hole), begin carving towards the center. Always be sure to work in a "downhill" direction when turning. Doing so will prevent a catch that could damage your blank and force you to reconsider your design.
Using the drilled hole as a guide for how deep to cut, continue carving away until you reach the end of the drilled hole. Once flush, make the top of the mortise as flat as possible and add a slight angle to the sidewall. You will want this angle to resemble the jaws on your chuck. This dovetail shape helps to hold the blank in place and provides a better gripping surface for your chuck.
Once you complete the mortise, insert the chuck to confirm it fits securely.
Note: No need to sand the inside of your mortise. The added roughness will provide a better grip for your chuck. But if you want to sand the flat back of the blank, now is the perfect time to do so. It is not necessary since it will be the rear of the clock but feel free to do so if you so choose.
Step 14: Mount the Jawed Chuck
With the lathe turned off and tool rest moved out of the way, take your jawed chuck and insert it into the mortise.
You can use the tailstock of your lathe to help hold it flush against the blank while you secure it in place. Slightly ease the tailstock into the rear of the chuck to press it against the wood so that it will hold in place on its own.
Using the chuck's key, open the jaws to provide outward pressure on the mortise. You will want to make this as tight as possible. Keep turning until it feels secure, but be careful not to overtighten.
Step 15: Remove Faceplate & Remount
At this point, you should have a wood blank with two different chucks attached.
Remove the faceplate chuck from the lathe and take it to a flat surface.
With the faceplate chuck facing up, remove the screws holding it in place. You will only need the jawed chuck moving forward.
With the blank and attached jawed chuck in hand, remount it to the lathe by threading it onto the headstock as pictured.
Spin the blank by hand to confirm it is connected securely to the chuck and lathe.
Step 16: Turn Outer Edge
Now for the more creative steps. With your blank securely mounted to the lathe, it is time to turn the outer edge.
This step will true the blank and make it perfectly round.
The goal here is to turn the edge so that it matches your previously drawn outer circle.
Using a roughing gouge, position your tool rest on the outside edge, and begin turning. I kept my lathe on its slowest setting until it became a more unified roundness.
Depending on your design, you might want to make your edge completely flat, curved, angled, or patterned. It will be the final look for the outside edge of your clock, so feel free to get creative.
Tip: You can use a skew chisel to create a reference cut following your drawn outer line.
Step 17: Turn Inner Clock Face
With the exterior edge round and complete, it is time to address the clock face. You can now increase the speed of your lathe if desired. I turned my clock while set at around 1200 rpm, but choose a speed to match your comfort level.
At this point, let your creativity take control. If you created one, follow your design. If not, let the wood be your guide. Either way, this will become the final look of your clock. You can keep things simple or create something complex, but there are a few key things to keep in mind:
- Keep a cylinder of wood at the center. It will help to hide the center clock shaft. 3/4 inch should work but is dependent on the size of your clock kit.
- Mind the screw holes. The holes made from affixing the faceplate chuck will be evident initially but can be removed by turning them away.
- Watch your thickness! Do not get too carried away. If you remove too much material, you might break through to the mortise cavity on the other side.
Note: If you are new to woodturning, you might enjoy reading this Instructable on Getting Started With Wood Turning (Tools, Techniques and Top Tips) by world of woodcraft. It provides an overview of the different tools and techniques that might help you with this project and many more to come.
Tip: As a final step, use a scraper chisel to create a smoother surface.
Step 18: Drill Clock Kit Hole
After finishing the design of your clock's face, drill the center hole for the clock mechanism to run through.
Confirm the diameter of the center column shaft to your clock kit (the part which the hands will eventually connect to) and find a drill bit to match or is slightly larger.
Set your lathe to its slowest speed. Using the drill chuck in the lathe's tailstock, drill a hole that goes through the entire piece. You should be able to look through the hole and see through to the other side.
Tip: When starting to advance the drill, go very slowly. Let the bit do the work. This initial step will let the bit "settle" into its position on the wood, which will give you a perfectly centered (and even) hole.
Step 19: Final Sanding
Now to wrap up, you need to sand your clock by making your way up in different sanding grits.
Sandpaper comes in different "grits" or roughness, typically indicated by a number. The lower the number, the rougher the grit. In most cases, you can probably start standing at around 300 grit and make your way to up to 600. There is a wide selection, but for this project, a final sanding at 600 should suffice.
I began sanding with 320 grit. Sand all areas of the clock you want to smooth out. If you have fine detail work, such as the rings I made towards the center, lightly sand these areas or skip them altogether.
After the 320 grit, I then used 400, then 600, until I was happy with the results.
Step 20: Dismount
If you do not plan to use a woodturning finish (which needs to be applied while still on the lathe), you can now remove your clock from the lathe.
At this point, you will have something that looks more like a clock than a block of wood.
In my case, my blank had a knot in the wood that I decided would make a great 12 o'clock marker for my clock. If you come across a knot in your blank, do not worry, use it to your advantage.
Note: If you want to use a woodturning finish, apply as per its directions and then remove it from the lathe. Some finishes are friction-based and require the speed of the lathe to be fully set.
Step 21: Trace Mechanism Outline
Flip the clock over. Remember that rear mortise you initially made? Now you will see its dual purpose.
With the size of my jaw chuck, I could not make my mortise larger and remain securely mounted. Because of this, I needed to chisel out the corners to fit this square shape into the round hole.
Flip the mechanism upside-down so that the shaft aligns into the center hole and the plastic case is flush to the wooden back. Align so that the top of the mechanism is aiming towards the 12-hour marker.
Trace around the case to give you a reference on which areas to remove for a better fit.
Step 22: Chisel Recessed Compartment
With a chisel and hammer, carefully remove these corners while checking the fit of the mechanism itself.
You may need to adjust as you go to make it fit as intended.
Important: Be careful when hammering, as you could accidentally force the chisel through the center of the clock face. Depending on your design, this area might be thinner than others and could be easily broken. If you do happen to punch through, you might be able to fix it with some wood glue.
Tip: You can also use a handheld rotary tool to help carve away these corners. Since this is the side of the piece that is not visible, do not stress over it looking perfect. You can also use a plunge router if you happen to have one.
Step 23: Decorate & Apply Finish
Finalize your clock to your design. You can achieve a more minimalistic look by keeping the design as is, or you can add hour markers or even paint to suit your design.
I prefer the minimalist look myself but decided to try a few options to provide you with some ideas.
Remember those extra pieces I cut off of the hour and minute hands? Those made perfectly sized hour markers. Use a super thick glue to align them in place.
The blackened center is a "Shou Sugi Ban" technique, a Japanese wood-burning finish. With every woodworking project, I make a point to try something new. This process involves burning the wood (I used a small torch lighter) and then brushing away the ashes with a firm brush. I thought the blackened center would fit nicely with the hour markers and clock hands.
I should also mention, there are a wide variety of clock hands out there that can create a different look for your clock. Whether by adding a pop of color or a unique design, you can truly design a one-of-a-kind clock.
After adding any embellishments, you can then apply your finish of choice. I decided on using Odie's Oil, as it creates a smooth yet natural finish without any harsh fumes. Be sure to follow the directions of your chosen finish for both application and safety.
Step 24: Assemble Clock Kit
After your finish has dried and cured, it is finally time to assemble your kit into a working clock.
It is important to follow the directions provided with your specific clock kit. There are usually a few additional components to keep in mind, such as washers and hanging brackets.
Insert the mechanism through the center hole from the recessed cavity on the back.
When installing the hands, it is best to align both of them at the 12 o'clock position (both the hour and minute hands at the 12-hour marker). Doing so will make sure they align correctly with the other and provide an accurate visual of the current time.
Once all together, install a battery and set the time.
Note: If you don't want a wall-hanging clock, you can create a flat bottom by sanding the edge under the 6-hour marker. You can do this by hand or with a belt sander, which will prevent your clock from rolling away while on a shelf or a table. You could even incorporate both to give you options.
Tip: Remember to sign your name and write today's date on the back. It will be a fun reminder that your future self will be glad you did. Plus, it will give it more meaning whether 5, 10, or 100 years from now.
Step 25: Display & Admire
And just like that, you have successfully turned (pun intended) a board into a functioning clock with far more value and meaning than anything bought from the store.
Wood is a satisfying medium to work with, and when done right, your clock will be something to enjoy for years to come.
Did you end up making this clock? Is it for yourself or a gift for someone else? Let me know in the comment section below. Feel free to share an image or two to help others design ideas they can incorporate into their clock. I would like to see what you end up making as well! If you have any questions or suggestions along the way, feel free to share them as well.
I hope this Instructable was beneficial to you, and at the least, piqued your interest in woodturning and woodworking! Happy turning!
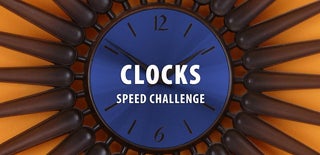
Second Prize in the
Clocks Speed Challenge