Introduction: Space Bowl
I remember watching spray paint artists and loving the simplicity to their work when it came to making planets. I thought it would suit a shallow bowl, with the center acting like the sun or a larger platter. The nature of the bowl being round adds to the look. I had never done the spray painting before but the basics were easy to pick up.
Step 1: Preparing the Blank
Timber choice: I chose mahogany of colour and grain. The orange colour suited the the sun characteristics. The grain is not too open so that means I get a relatively flat surface for the paint. Its also an easy timber to turn and quite cheap
After making the circle on the board, I cut it out on the band saw. Using the pin mark form the compass, I drilled a hole about 6mm deep with a 50mm forstner bit. This is how I then hold the blank on the chuck, expanding the jaws into it. It might take a few minor adjustments to true it up with as little wobble as possible. To do this, I back off the clamping pressure and tap the high points with the chuck key or the palm of my hand.
Step 2: Turning the Back
Step 1: Flatten off the foot area.
Using the gouge, I flattened off the foot area, with a slight concave so the piece would sit flat on a table. I could have done the entire surface but this is all you really need to do as the rest will be removed a few minutes later. Then mark the diameter of the foot. This should be about 2mm larger than the diameter of your fully closed jaws.
Step 2: Roughing the shape
Using a heavy pull cut, you can quickly shape the form of the bowl. There isnt any bevel contact, so perfecting the shape into an even curve is a lot more challenging. However, a clean finish is not the purpose of this cut. This is just to remove the waste efficiently. I normally go about 3mm oversize and dont care too much about tear out.
Step 3. Cleaning the surface
To get a good surface finish, I use a push cut. This is a bevel riding cut so it is much more controlled. With the tool handle up against my body, I used the movement in my entire upper body to move the tool. This is how to get a well controlled cut. Before my final pass, I will sharpen my tool. To get into the tenon, I use the corner of the skew to cut the edge. As this is a scrapping action, a sharp tool is very important
Step 4: Sanding
As I had a very clean finish, I only had to use 180/240/400 grit sand paper. When sanding, I aim to have the lathe at about 800rpm or slower. Variable speed makes this easy. I constantly move my hand in circles so that I am not sanding in ruts in the piece.
Step 3: Turning the Face
Step 1: Mount the blank
Using the larger jaws, mount the platter to the lathe. These jaws are 81mm in compression.
Step 2: Truing the face
Using my 3/8 bowl gouge, I trued the the face with a push cut. This shouldnt take much time as it should be relatively flat already. The 3rd photo should show the angle of the tool when presented to the timber. Sanding should be done in the same way that the back did. Another thing that I did was mark a quick V groove for sizing of my rim.
Step 4: Marking the Planets
To do the planets, I used anything circular that I could find. This was mainly done with bottle top lids and coins. After placing them in the rough positions, I traced them. They will be needed for later but I wanted to know my placement
Step 5: Spray Pattern 1
Green, blue and white for an earthy look.
I started with 2 green lines that taper towards each other with quick passes. I then sprayed the blue in the gap. I liked the mix between the 2 colours off the first go. To get the white, cloud like look, I held the spray can far away and held the the nozzle at half pressure until it started to spit. Thats what gave it the dots rather than a full spray pattern I liked how this came up
Step 6: Spray Pattern 2
Stripped pattern with red and yellow
I started with a red and yellow parallel spray. With the use of cans, its hard to get tight lines between the 2 unless you use a blocker. This is another piece of paper or board that blocks the excess. To get tighter lines, actually spray at the paper about 25mm on the paper and let the over spray hit the timber. The over spray allows the paints to blend a bit rather than taping up areas and having solid lines which I dont think would work for this.
Step 7: Spray Pattern 3
Creating highlights, white on blue
I started with a blue horseshoe shape. I wanted to fill that smaller section with the white. It ended up being much larger than I had hoped but thats alright because it lends itself perfectly to layering. I then used the blue again on the edge and the over spray blended it perfectly. On the other side, I did one focused spray on the edge with the white. That will create a highlight. I also did a slight splattering with then nozzle held at partial pressure. I think this one is my favourite
Step 8: The Background Spray
This shows all the different spray patterns on the piece before adding the black. I think it actually looks pretty cool at this stage, looking quite cosmic. I used a hair dryer to help dry off this layer. I wanted it to be fully dry so that then next layer doesnt blend in to this and so that the bottle caps dont stick.
After that I placed the caps and coins in the areas that I though best highlighted the painted sections
Step 9: The Top Layer
After the cap are in place, cover the entire surface with the black spray paint. You might need to come from different angles to get around the caps. So it doesnt look flat, I lightly sprayed a bit of blue and red from a distance (pics 2 and 3). If its over done, you can go back with the black.
To get the stars, I used a silver to spit from a distance. I only did this lightly to not over do it. The white lines were sprayed using the paper as a blocker to get some thinner lines. I also used a bit of yellow on the edge, just so the over spray was hitting the timber.
When this is done, remove the caps and hopefully it works out well. I was really happy with mine. It was heaps better than I expected
Step 10: Back to the Turning
Step 1: remount to the lathe
The reason I use a tenon that is also a foot is so that I can easily remount the piece.
Step 2: Hollowing out the bowl
When using a gouge to hollow out a bow there are 2 steps in getting the cut right. Start with the flute directed to 3 o'clock. That creates a groove for the bevel to rest in. Then you can open up the flute to between 1 and 2 o'clock where you get the good cuts. Like shaping the outside, move your body with the cuts as you sweep down into the middle. I got a little bit of tear out so I sharpened the tool and increased the speed. I got another very clean cut that required little sanding.
Step 3: Sanding
My tip to sanding a bowl when protecting is to fold the sand paper up and have the flap to the center. That way you are controlling up to the edge and no sanding off the paint job. Work through the grits again form 180-400. I also resanded the back with 400 to get the small amount of over spray
Step 4: Dusting
I uses the compressor to blow off most of the dust. There was still a bit that stuck so I carefully had to wipe it with a rag. It is now ready for polishing
Step 11: Finish
A spray can lacquer is good choice for finish. I used pylon satin lacquer. It only does thin coats but dries quickly. I did about 5 coats, cutting back after the 4th. When cutting back, be careful not to go through the paint.
This piece was so much nicer than I had expected. It was also a lot of fun learning a new skill. If I want it to be a little more refined, I would use an airbrush but I like this
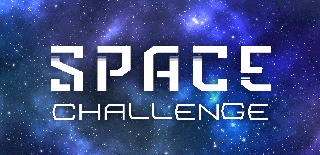
Participated in the
Space Challenge