Introduction: Splatoon Ink Tank
Hello and welcome to my Instructable for a green Splatoon Ink Tank. This is a continuation of my first Instructable, the Splatoon Inkling Wig, to create a green Splatoon Inkling character Halloween costume for my son.
Unfortunately, as I do not have a fancy 3D printer (...yet), much of this Ink Tank was created with foam and other miscellaneous parts and pieces.
Step 1: Tools & Materials
Tools:
- glue gun
- heat gun
- sharp cutting tools; xacto knife
- drafting compass
- brushes
- Dap Kwik Seal Kitchen & Bath Adhesive Caulk
- Mod Podge
Materials:
- 2mm craft foam
- 9mm EVA foam
- 5" OD acrylic round tube (mine measured 12" long)
- Toothed Timing Belt (Gates T252 was a good size for my piece)
- 1" PVC Pipe
- 1" PVC Union Fitting with the non-threaded insert removed (i used the insert for the Ink Roller I constructed)
- 9 x .625" Flat Rubber Washers
- 3 x .75" plastic leg tips
- Red turn signal lens cover for Harley Davidson (fit the PVC union perfectly)
- .75" PVC Pipe (very very short piece)
- 1" wide webbing strap
- 2 x Webbing strap plastic click-in buckles
- 2 x 1" Chicago screws
- 4 x washers
- 2 x .75" Chicago screws
- Crazy Glue
- White Oracal Intermediate Cal 651 PVC film
Red Oracal Intermediate Cal 651 PVC film
Step 2: Base
For the main body of the ink tank, i purchased a large round acrylic tube with an outer diameter (OD) of 5", from my local industrial plastic hardware store.
The Cuts
- Trace the outer diameter and inner diameter of the acrylic tube onto 9mm EVA foam.
- Cut the outer diameter, and trim and hollow to the inner diameter to effectively create a lid to the ink tank.
- Trace and cut out another piece of foam to the size of the outer diameter (5"); this will form the middle layer.
- Create a smaller round piece of foam, approximately 4.75"; this will be the top layer.
- On 2mm craft foam, cut out the ink tube base pattern (referenced online and as pictured above) to cover the 4.75" top layer.
- Cut a 1" wide strip of foam, long enough to wrap around the acrylic tube; this will form the band around the bottom of the ink tank
- Cut a strip of toothed timing belt (Gates T252 worked perfectly) the length of the 1" wide foam previously cut
Putting The Pieces Together
- Center and Glue all the round layers together.
- Using Dap Kwik Seal / Silicone to fill the gap and create a beveled angle from the 5" middle layer and 4.75" top layer
- Glue a small strip of 2mm foam to cover the Dap Kwik Seal / Silicone (another option to create a beveled edge would be to use a Dremel Tool to shape a larger piece of foam)
- Using a heat gun, form the 1" strip of foam to the curvature of the acrylic tube; then attach the timing belt to along the center of this piece
Note: When cutting and gluing the pieces, keep in mind what is going to be exposed especially if one side of the EVA foam is textured.
Painting
- I applied two coats of Mod Podge to all of the pieces in order to seal the foam and provide a solid base for painting
- Paint the 1" strip and timing belt piece with a dark green paint
- Paint the outside of the base piece light green and the inside a dark green colour
- I used spray paint for sake of time (Halloween was approaching quickly) but in hindsight i think acrylic paint might have provided a richer and tougher finish
- Follow-up with a couple of coats of Mod Podge to give the pieces an extra seal to protect the finish and an extra sheen
Step 3: The Ink
To create the ink inside the tank, i used a smaller, narrower plastic tube (cut from a 4oz / 113g container of cotton candy) for support:
- Cut out the bottom of the container and push into the bottom of the base piece of the ink tank to create an indented mark.
- Slightly score along the indented mark, and insert the tube ensuring you have enough material inserted for a) support and b) gluing later on.
- Cut the top part of the tube in the shape of splashing ink.
- Wrap and glue 2mm craft foam around the support tube and cut along the top pattern, just above the "ink" line; this will provide extra material to fold over and glue onto the back of the support tube.
- Cut out and glue 2mm foam to cover the top of the support tube.
I applied two coats of Mod Podge then painted the ink structure with a couple coats of neon green spray paint. The top piece started to rise after painting and drying; this was not intentional but it added a great dimension to the piece. After painting, I added a couple more coats of Mod Podge to seal and finish the piece.
Step 4: Top Cover
The Cuts
- Trace the inner diameter of the acrylic tube onto 9mm EVA foam and cut; this should just fit inside the tube and will form the bottom piece of the top cover.
- I cut out a small rectangular opening to this piece to provide internal access into the top cover to illuminate the top of the Ink Tank.
- Trace the outer diameter of the acrylic tube and cut; you will need 3 of these.
- Trim and hollow one of the circular pieces to the inner diameter (as depicted above); this will be your top layer.
- I trimmed and hollowed the edge to create a beveled edge using Dap Kwik Seal; this is not necessary if you can create a beveled edge using a dremel tool.
- Locate the center point of this piece and, using a drafting compass, draw a circle approximately 1.25" plus; this will snugly accommodate the bottom of the 1" PVC union fitting.
- Locate the center point of the other 2 pieces and, using a drafting compass, draw a circle the size of a 1" PVC pipe.
- Trim and hollow one of the circular pieces to the inner diameter (as depicted above); this will be your top layer.
- Insert a 1" PVC pipe into the PVC union fitting and insert the 3 round pieces through the PVC pipe.
- Mark and cut the PVC pipe at the end of the 3 round pieces, ensuring that it does not go beyond the 3rd layer
- Center, stack and glue all 4 circular pieces, ensuring proper alignment with the center PVC fitting hole.
- Remember the small round piece goes on the bottom of the stack and the beveled piece is the top.
- Cut and wrap a 2mm piece of craft foam (approximately 1.5" wide) to cover the sides of the top 3 round pieces; glue in place.
- Using Dap Kwik Seal to fill the gap and create a beveled angle on the top layer (or create a beveled edge would be to use a Dremel Tool)
Note: When cutting and gluing the pieces, keep in mind what is going to be exposed especially if one side of the EVA foam is textured.
Step 5: Top Cover - Detailing
The Cuts
- Cut 9 small rectangular strips, approximately .625" x 1.875"
- Cut 3 large rectangular strips, approximately 1.125" x 2.75"
- Cut a strip of 9mm EVA foam approximately 1" wide, long enough to wrap around the acrylic tube (my EVA foam wasn't long enough so i glued two pieces together)
- Cut a strip of 2mm craft foam, just under .75" wide, and glue over the 1" wide strip
- Cut 9 x .625" flat rubber washers into a 'U' shape (as shown above); these will form the hinges
- Glue 3 of these onto 3 x .75" plastic leg tips
- Cut a small strip of 2mm craft foam and cover the PVC union, gluing it between the top layer of foam to the bottom of the thread
Putting The Pieces Together
- Measure .5" from the bottom of the third layer and lightly draw a straight line around the top cover.
- The 1" strip previously cut will eventually be glued to cover this .5" space
- Split the top layer into thirds, marking the 3 points.
- Take the 3 - 1.125" x 2.75" rectangular strips and center them at these points.
- Lightly mark it's side edges on the sides of the top cover.
- Glue 3 of the small rectangular strips evenly between these marks, lining up the bottom to the .5" line drawn.
- Using a heat gun:
- a) form the 1" strip of foam to the curvature of the acrylic tube
- b) curve the 3 large rectangular strips
Painting
- Following techniques of Bill from Punished Props Academy, i filled in gaps, seams, and imperfections on all the pieces using Dap Kwik Seal
- Apply two coats of Mod Podge to all pieces in order to prep for painting
- Paint:
- Light green: main body of the top cover; PVC union; 6 'U' shaped hinges; bottom layer of cover
- Dark Green: 3 large rectangles; 1" strip; 3 hinge piece/leg tips
- Follow-up with a couple of coats of Mod Podge to seal
Putting More Pieces Together
- Insert the PVC union into the main body of the top cover, making sure the bottom of the 1" PVC pipe doesn't go beyond the 3rd layer into the bottom layer
- Glue a red turn signal lens on top of the PVC union to cover the hole; i had to use a dremel tool to shave off the clips of the lens
- Glue the 1" strip around the main body of the top cover, at the bottom of the 9 small rectangle pieces
- Glue the 3 large rectangle pieces from the 1" strip, evenly bookmarking 3 small rectangle pieces
- Carefully align and glue all of the hinge pieces together, making sure:
- PVC union hinge pieces are flush with and lined up on the top piece of the union
- all centered between 2 large rectangles (should be just above the middle rectangles)
Step 6: Illuminating the Top Cover
For a functioning red light at the top of the ink tube:
- Glue velcro strips to secure the cover (bottom layer to the third layer)
- Slide a small bike light through bottom of the 1" PVC pipe to the very top end of the PVC union
- Slide a .75" PVC pipe to support and hold the small bike light in place
- Mark the .75" PVC pipe at the bottom of the 1" PVC pipe and third layer, and trim
Step 7: Straps
The Cuts
- For the back support, i created a bone-shaped pattern on a 9mm EVA foam measuring 10" long x 2.5" wide (at it's widest point) as shown above
- Make a 1" long vertical cut approximately 1" from both ends (centered vertically) of the back support; this is where the webbing strap will be fed through
- To strengthen the back support, i also cut a piece measuring 1.25" x 7.25"
- For the shoulder straps, i started with pieces that measured 1.5" wide x 20" long; this was way too long for my son and in the end it was 12" long
- Using a heat gun on the shoulder straps, i created a curve that would naturally follow the shoulders from back to front
Painting
- Apply two coats of Mod Podge to all pieces in order to prep for painting
- Paint:
- Dark green: back support and support piece
- Light green: shoulder straps
- Follow-up with a couple of coats of Mod Podge to seal
Putting The Pieces Together
- Cut an 11" long piece of 1" webbing strap.
- Center the webbing strap on the main back support and glue; insert the ends of the webbing strap through the 1" cuts, wrap around the other side and glue.
- Center and glue the support piece on the inside of the back support (side that touches body)
- Cut a 6.5" long piece of 1" webbing strap and glue over the back support
- Cut 2, 20" long pieces of 1" webbing strap; giving approximately 1.5" on either end to attach buckles
- Glue the webbing straps over the top of the shoulder straps; with the female end of the buckle at the back of the shoulder strap
- placing the buckles at the back of the armpit was the most comfortable
Step 8: Putting the Ink Tank Together
Back Support
- Drill two holes, approximately 2" apart a the center of the back support piece
- Insert the female end of a 1" Chicago screw into each hole
- Center the back support piece approximately 2" down from the top of the acrylic tube
- Mark where the Chicago screws meet the acrylic tube
- Carefully drill holes in the acrylic tube for the Chicago screws
- I believe acrylic is brittle and prone to chip and crack when drilled
- To drill the holes safely, i started with the smallest drill bit and increased the size incrementally, letting the drill do the work
- Using Krazy Glue, glue some scrap rubber pieces over the holes and drill holes through them
- Krazy Glue the back strap to the acrylic tube, aligning the Chicago screws to the holes in the tube as you do so
- Place a small washer through the male end of the Chicago screw and attach to the back support through the rubber and acrylic tube
Note: Using Krazy Glue on the acrylic tube left some reside on the Ink Tank. I would caution that you use it sparingly and be careful with excess glue (ie on fingers as well).
Bottom Cover - I waited to glue bottom piece onto the acrylic tank until this point as i was concerned about how drilling into the acrylic was going to turn out.
- Krazy Glue the base piece onto the bottom of the round acrylic tube
- Glue the 1" strip with the timing belt around the unfinished part of the base and the acrylic tube
Top Cover - To make sure the top cover stays in place, i used a short thin piece of velcro along the top rim of the acrylic tube and the corresponding side inside the channel of the top cover
Shoulder Straps
- Abut the shoulder strap, with the buckle end to the back, to the inside support piece of the back support;
- Carefully drill through both pieces, ensuring that you drill through the webbing strap (for extra support).
- With a washer through the female end of a .75" Chicago screw, insert through the back (outside) of the back support.
- Glue the shoulder strap to the inside of the back support, pushing the female end of the Chicago screw through.
- Screw in the male end of the Chicago screw from the inside of the shoulder strap.
- Do this again for the other side.
Ink Level Indicator
- Referencing online images and screenshots, i replicated the Ink Tank's ink level indicator using red and white Oracal Intermediate Cal 651 PVC film
Comfort - After trying on the Ink Tank, my son noted discomfort at his shoulders with the shoulder straps and his lower back with the bottom cover / timing belt. I attached a couple of strips of soft foam under the shoulder straps and at the base of the Ink Tank (as shown above) and it worked great to relieve the pressure.
Step 9: Concluding Remarks
Thank you for checking this out! Any photos, comments and/or feedback appreciated!
And now for the final piece... the Splat Roller.
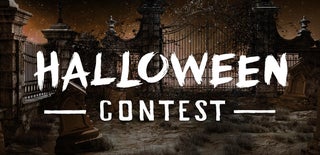
Participated in the
Halloween Contest 2018