Introduction: Stainless Steel Coffee Table
This instructable is different from what I usually build. One of my viewers asked me something about furniture which has irregular shapes and design and he asked me to tell how he himself was able to build that thing. I definitely suggested it to him at the moment but later on, I loved that concept so much that I decided to give it a try. Now usually this kind of furniture is usually built with thicker materials which I knew but I wanted to give it a try with a stainless steel sheet. I really love this material but making this kind of project is definitely a challenging task. This was also my first tig project. I definitely did some practice over scrap pieces and then moved onto this project. Working on stainless is difficult because it warps a lot and a more problematic thing for me is that I am using a thin 18 gauge sheet (1.10 mm thick). But I learned a lot more from many other youtube channels like welding tips and tricks, the fabrication series, and weld.com, definitely recommend you to check these channels if you want some pro tips. The experience I got in this project was definitely used in the future for tons of builds. Being my first tig project and also a sheet metal project I think I did an ok job on this. There are few corners where I actually made small mistakes by spending much more time and because of that there are small dots formed but It's definitely a fixable thing. My initial plan was to make the side with steel and the top with a different material, but my brother suggested keeping the same material to make it more unique so I went that way and was really glad that I used only stainless steel. At the bottom area, I use some acrylic pieces to provide it with some floating effect. I don't know whether it really worked like that but I really like this thing too. If you are worried about structural strength then it can easily bear my weight of 114 kg and I think it's more than enough for a table made only out of stainless steel. If you have some useful tips for doing tig welding then definitely let me know.
Supplies
Material and tools used.
For this build, the material I go with is 18gauge 304 stainless steel. The finish on the steel is a brushed finish. I go with brush finish because it's a bit cheaper than the high gloss finish. The sheet has dimensions of 4ft X 8ft and during this build a huge chunk of sheet still left which I used for my sculpture.
For the tools following stuff is needed.
1. Tig welder (good if you have pulse tig Machine)
2. Angle grinder
3. Brushed finish wheel. (Usually, the grit size used over on this sheet is 80grit with a scotch brite over it.
4. Cut off the disk.
5. Combination square.
6. Flap wheel.
7. Spray glue.
8. Nut Riveter
Make sure to use proper safety equipment while welding. I knew I am not using them on few areas because I was frustrated during the work when I wasn't able to tack weld them. So be careful and use proper PPE.
Step 1: Design
Designing is not the difficult part of this build. The plan here is to make a design for which a full sheet would be enough. Actually, my plan was to make a chair and table combination but I gave it a try first as it's small and I was not sure about the success rate. So being a costly material my plan was not to waste any material whatever is going to cut out for the design that is going to be used for the remaining two sides. By doing this it's zero wastage. Now for the internal design, you can make it as complex as you wanted to but I kept it simple because I have to do this with an angle grinder and for very tight areas it's difficult to go with an angle grinder. My plan was always to demonstrate to the audience that you can do it without CNC, although with CNC laser cuts you are able to get a much more complex pattern and take your ability to a whole new level. Now one thing you need to be aware of is that complexity adds more welds and that welds add heat which may end up in a crooked surface.
Now in the first instance, it might seem to be an easy project but believe me a little bit of overheating will result in an abstract artwork rather than a piece of furniture. Now you can definitely do complex shapes but only by using heat sinks like aluminum because of its higher thermal conductivity and affordable cost. Now, as far as design is concerned you need to have the inner design in such a way that you are able to get the exact dimensions. Now in a 20-inch square table if it's 1⁄8" short on one side then it wouldn't be a big problem. But more than that completely changes the design of your table. Now in this particular design after cutting the middle elliptical shape I counted those materials also which are going to be used for the thickening of the Sheet which is 11⁄2" wide strips of the same material. What I found is that the more you kept it simple the better the table will look. Try to have organic shapes rather than straight lines, more if that definitely depends upon your taste but organic shapes make the thing more alive.
The end conclusion of the design part is to make a shape that is easy to work with since to thicken up the table you also need to add strips on sides and having complex shapes increases your work in those scenarios.
Step 2: Material Cutting
Once the design is ready I save it as DXF and make a printout. I printed it onto 6 sheets of A4 paper. Once the template is joined with tape it's ready to glue onto the material. I use spray adhesive but frankly said I didn't like it because it's very hard to remove the paper from it once the work is finished but there is a good point too that it doesn't peel off and retains the marking for a longer duration compared to wood glue or glue stick. I first spray the glue on half the side and then place the template and gently squeeze the air out of the template.
Once the template is glued I start the cutting process. The plan was to first remove out one square piece and make the job lighter and easier to work with. I use the angle grinder to cut the area onto which the template is glued. After the cutting deburrs the edges and bring the material to the exact dimensions of the template. Now the master template is ready and on the basis of this, I am going to cut 5 more. The two of them didn't have an ellipse inside them and are going to be used for the tabletop. Once all the sheets have been cut off I start the refining work of the boundary and provide fillets.
Once that has been done with the help of an angle grinder I start the cutting process of the ellipse. Now during my work, I use two tools angle grinder and jigsaw and I found that if you start the initial cut with an angle grinder then it would be easy to finish that curved shape with a jigsaw but if you can stable your hand then I think an angle grinder would work fine for you. Just scour the line first over the outline than in the second pass you are able to remove out the material very easily. The scouring creates a path for the blade to remain in the desired path.
Step 3: Final Finishing of Cut Pieces
Once both inside and outside lines are cut out with the help of files and angle grinder I make lines smooth. The cuts with an angle grinder didn't come up so crisp. The one thing you need to take care of is that if your pieces have finished onto one of their sides then make sure that final shaping needs to be done by keeping the pieces in mirror position so that they come up with an exact image of each other. It's better to clamp the pieces together and then proceed.
Step 4: Cutting Down 11⁄2" Strips
Cutting the strips is definitely challenging for me and the problem is that I need to be straight as much as I can. For that, I use a straight edge cutting jig which I often used for my woodworking projects. This thing really didn't work as I expected because to use it properly I think I need a circular saw setup with a metal cutting blade which i didn't have at the moment so I draw a line with the help of a combination square and then cut it freehand but I tried to keep myself over the lines which I marked. But frankly, I didn't trust this method. Rather than this try to have a circular saw with a metal cutting blade onto it, which will give you a much better result.
Step 5: Tack Weld One Side With the Strip
The first thing is to weld the pieces together because in welding you always need to left room for mistakes and if you made everything rigid you can't correct your mistakes. Before starting the tack weld I kept a piece of the aluminium block as a heat sink and a bunch of clamps. For the welding I am using a tig machine, without this, it would be difficult to get good results without warpage. So I started with the outer boundary tack weld the strip. Now doing the initial tack weld is very easy compared to the time when you have to weld a second sheet. The current during this stage I kept is twice the welding current. Normally for tig welding formula is 40amp for 1mm in the case of stainless steel. For tack welding I use 80amps. So that with a quick burst the fusion gets done. Now the advantage is that less will be the time spent less distortion will take place and that aluminium chills the material a lot more faster. The same procedure has been carried out for the inner sides as well. It's better to remove the plastics and clean the surface with acetone to have a much cleaner weld.
Step 6: Welding the Second Sheet
Once the one side has been tack welded it's time for the second side ( backside). Now without the strip, the sheet has no strength and it's difficult to hold it to its place. So what I did is to place some welding rod over the edges to prevent the sheet from falling inside and because of this welding would be a lot more easier to do. There are few areas where the material gets sunk inside so I have to use a flat head screwdriver to pull it out and then make the tack weld.
Tip:- During the weld of the second sheet it would be good if you weld something inside to reinforce the material. Welding some vertical members on a few positions will make the job done much easier and safer. Although during my work I didn't face any issues like that, a new person will surely face it if I didn't work with stainless steel.
Step 7: Complete Weld
There is no problem in making a full weld but you need to have some patience while doing this on stainless steel. Stainless steel has a very less thermal conductivity which makes it difficult to work with if it's heated on a particular spot. To counter that it is good to flip the piece and change the weld areas. Make sure to provide some time for the material to cool down properly. It would be great to use aluminum heatsink wherever possible because they draw the heat out of steel very quickly and make the material ideal for working.
During this project, I highly depend upon pulse welding and it really eases the work but it doesn't mean that if your machine doesn't have this feature you are not able to do it. That tack welding process can be applied to full welding also. Remember heat is the enemy of stainless steel and keeping it cool during the work means you are very close to being able to achieve the final end product which you planned off.
Step 8: Grinding and Finishing.
Once the welding work is completed it's time for the finishing process. Since during this build I didn't use filler metal too much except over the area where some blow holes appeared there wasn't much of the grinding work that needed to be done and I really like the advantage of the tig machine here. In the past, I kept using a stick welder on stainless steel and there is always a big-time need to finish work but that's not the case here. I started with a 120 grit flap disk and then switched to the bench grinder wheels which are mounted on a drill machine. You really don't need to use this setup for the finishing, I used it because In my area the brush finish wheels are not available so I found this alternative. The way to do it is to just keep the scratch pattern in one direction in that way you are able to get the brushed finish look.
Now if you further investigate brushed finish then it's also of various types. Usually, there is a separate finish grade available for the brushed finish but you can relate it to the normal grit size of the sandpaper. Usually, a brushed finish doesn't go beyond 320 grit. In my case, the finish on steel I have is 120 grit and from hereafter, there is a 120 grit scotch Brite wheel is used. Usually, the finish starts from 60 grit. But if I suggest you then try to go with the wheels which are specifically available for a brushed finish. By that means you don't need to struggle a lot. Compared to a high gloss finish brushed finish is a lot easier to do.
You can also see the given video if you willing to know different type of brush finish
Step 9: Welding All the Pieces Together
Once the finishing is completed I start the work on connecting them together. First I marked the partition line onto the ellipse and the same thing has been done onto the square piece as well. From there after matched those lines and tack weld them. After that, I flipped that piece carefully and made a tack onto the backside as well and repeated the process one more time for the other piece also.
Step 10: Welding the Table Top.
To weld the tabletop I wanted a floating design and for that, I cut down some 1" round pipe 11⁄2" long and used them to raise the top. I marked the 4 locations and then welded the pieces onto the tabletop first. During this, I make sure that those pipe pieces remain straight so I kept on checking them with squares. Once the pieces welded onto the tabletop I welded it with the bottom section by centralizing it. There are few areas where it's difficult to weld so I leave it as it is.
Step 11: Finishing Touches
Once the welding work was completed I made a final pass with a scotch brite wheel. For the shoe, the plan was again a floating look so I used acrylic for that and cut it into square sections and then drill and countersink the holes. Since its sheet metal and threads are not going to be held, that's why I decided to use a nut riveter. With the help of this, I installed the thread inserts and mount the shoe to the bottom of the table.
Step 12: Finally
Overall I really like how this table came. During the start, it's just an idea and a hope which I wasn't sure whether I am able to build or not, but I think it went very well except for a few minor flaws here and there. I think if you wanted to build this then I definitely recommend you to pay attention to my tips which I mentioned. If you have any suggestions definitely let me know.
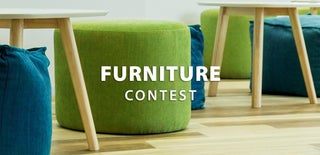
Grand Prize in the
Furniture Contest