Introduction: Stainless Steel Unicorn Sculpture
Hi everyone, this Instructables is all about making a stainless steel sculpture. This is my first sculpture and before this, I never made any sculpture, but recently in the past I made a stainless steel coffee table and the construction is just a little bit resembles that table, just giving me some confidence to proceed in sculpture making. To have some idea I first go with a paper version of this sculpture. I didn't make the exact same size of sculpture with paper because I just wanted to have some idea but even you are going to build a paper version that also seems difficult to me first. Once I completed that paper version It really boosted my morale to proceed with the metal version. But truly said even if you made a paper version of this, the metal version of that sculpture is difficult to work with because, in the end, it's metal and not flexible like paper. You can definitely reduce the welding joints by bending techniques but I didn't have a powerful sheet metal bender. The one I have made fillets during the bending so I totally avoid that because this sculpture has sharp bends plus I didn't know the bending angle. Now with a bigger 3d printed modal or a cardboard version can help to know the angles but the lack of tools allows me to proceed with the cut-out version and I stick to that plan only but good thing is that sticking with the plan really works as I wanted to be. If you have any tips for sheet metal sculpture making then definitely let me know. I am ok with welding but sculpture is a different thing I really need to know the tips from you guys. So definitely share your experience with me. Now Let's jump onto the building part.
Supplies
Material and tools needed.
For the material, I go with an 18 gauge stainless steel sheet. Since I wanted to hang it outside so I go with 304-grade steel. Now you can go with any material but if you want high gloss then I recommend you to stick with 304 grade rather than 202.
For the tools, I guess whatever sheet metal tools possible you can arrange that would be good for you but I didn't have so many sheet metal tools and for this, I use basic tools, and I think if you are a beginner then for this particular project these tools are sufficient.
1. Angle grinder.
2. Carbide scriber.
3. Ruler.
4. Belt grinder ( I just made a homemade version for this perticular project).
5. Grinding wheels.
6. Tig welder.
7. Safety equipment.
8. Hammer, mallet.
9. Welding clamps.
10. Pliers
Make sure to use all the safety measures while working don't try to copy my acts where I am not using safety measures properly during the initial tacking process. Argon is not a harmful gas but if you are working in a closed room then it might be dangerous to inhale and cause vomit and other problems, so make sure to do this in a well-ventilated room.
Step 1: Generating the Paper Templates
The first and foremost thing to do is to have a paper template. Now I provide paper templates for this perticular build in two different sizes one with flaps and the other is without flaps which are bigger ones and used for stainless steel sculpture. Now to generate the pdf templates you need a software named pepakura designer. The first thing to do is to visit any website for 3d files. For welding sculptures, it's good to proceed with these polygon-type designs because they actually required fewer tools and much easier to work with compared to those curved sculptures. But the software is actually capable enough to generate the pdf templates for any kind of shapes and the process is also the same. So after downloading the 3d Design open the Pepakura designer and import that file. Once you import it asks you about the face which needs to be placed on the top. You can leave it as it is. There is a scaling option that also comes up but initially, you can leave them as it is. So once you import the 3d file go to setting and select change to scale. From here you can increase or decrease the size of the modal. After changing the scale if you click on unfold your entire modal gets to open up onto a sheet. If you want to remove the flap just click onto 2d setting and uncheck the show flap tab. To disconnect any section click ctrl+n and to move or drag use Ctrl+m. Once you are happy with the layout just export it as pdf and make sure during printing, print it at 100 %. Make sure to have two copies of these templates. If something wrong happens you have a spare one, and after the cutting work, it shows you how important it is to have two copies.
Step 2: Making a Paper Model
For this process It is absolutely important to have a paper model, you can make a 3d printed modal but it's a costly and time-consuming process. The big reason for making a paper model is that it tells you the exact Bending direction that where you need to make the next bend. During this build, it happens much time that I am unable to assume that where I need to make my next bend but this paper model helps a lot to find out those directions. So the size of the paper model doesn't matter but it's good to make at least that size which seems good for taking reference.
Step 3: Cutting the Template and Gluing.
Once the print has been made I cut them with a paper cutter and they all are ready to glue onto the steel. To minimize wastage I glue them in a tightly packed manner. During this one thing you should take care is to provide an optimum gap for the blade to move and leave the provisions of blade thickness also. To glue them I use spray adhesive and then stick all of the templates onto the material.
Step 4: Scribing the Outlines.
Once the material is glued onto the material I decided to mark the scribe line. The problem with the paper templates is that during cutting with the cutoff wheel they start to burn and you lost the reference and for this perticular build it's absolutely necessary to have an exact outline of those pieces. So that's the reason why you need to scribe the lines. Since stainless is a hard material so carbide scriber is a good tool to scribe those outlines with a straight edge. Once the marking has been done the pieces are ready to be cut.
Step 5: Cutting the Pieces.
After scribing the lines I start the cutting process. Since the surface is big that's why I decided to trim it down first in a manageable size and then proceed with the cutting process. I use an angle grinder and cut off the disk to do this task. Now since I have scribe line reference that's why I don't have to worry about burning those templates. Just by following those lines, I am able to cut all those pieces. The time taken is around 8hr. to do all the cutting process. You can definitely use laser for this work and all the above preparation can be avoided and I guess that would be a lot more precise and accurate build. Once all the pieces are cut down they are ready to grind out.
Step 6: Grinding and Straightening the Pieces.
After cut down all the pieces the major work is to grind down all the pieces to the exact marked location where we scribed the lines. Because at this point the templates have no use just to know which side needs to connect with which one. Grinding is necessary because of welding even though after doing this there are still areas that occur where there is a small amount of gap. The need for grinding is because the cutoff wheel is not capable of making straight cuts, no matter how careful you remain it is still wobbliness in the lines. In that case belt, sander comes handy. Now I didn't have one so I made it out of scratch just to fulfill the purpose. To show you how I made that's a different topic. But the belt sander gives straight lines during grinding. I carefully grind these pieces until I reached those scribed lines which were actually needed for this build. Now we have precise pieces ready to join.
Step 7: Aligning / Aranging the Cut Outs.
Once the grinding work is finished I start the alignment of these pieces. Since I already mentioned the alphabet onto the pieces that's why it wasn't a huge deal for me to find the right side but there are a few pieces onto which the template has been fade away due to dipping them in water. That's why I printed two sets of templates and suggest doing the same. After that, I align all the pieces together in the right orientation to start the next process. Once the pieces have been arranged in the correct manner with the help of cellophane tape I connected them together. Now at this point, a polythene type tape is necessary because it has a tendency to stretch compare to masking tape. Now once the pieces have been taped it's time to start the tack welding process.
Step 8: Tack Weld Pieces.
Once the tape joining of the pieces completed it's time for the tack weld. Now at this point, I have to find where to start. So to that, I take reference from the paper modal and find that the biggest piece is onto the neck side that's why I started from that. I found out that piece and its adjacent pieces to start the tracking process. Now here is a tip that first, you tack them on a flat surface and then bend them. In that way, there is no problem of falling out those pieces but there is a slight problem that sometimes the bending radius is tight, and in that way, those tacks resist the bending of pieces. So to avoid those problems I go one by one also on some of the sides. And to find out where I am going to face that problem I took that reference from the paper modal.
There are many areas where the joint didn't come as expected. In that area, I took the reference from other pieces and proceed with my work. This problem mainly faced in the bottom area where I have to join that entire headpiece to the frame area. Some time to bring the sheet to the exact location I use welding clamps because with bare hands it's difficult to apply force in a closed section, but those clamps are strong enough to increase your power and then you are easily able to bend those pieces. To provide bottom pieces some rigidness I welded some flats onto them. During the tack welding process make sure not to make a complete weld because welding shrinks and eventually going to deform and you are not able to add other pieces and not able to join them. But once the entire chamber gets closed then you can proceed with welding.
Step 9: Cleaning
Once the tack welds are done I start the cleaning process with the help of acetone. To remove the black oxides from the tack welds I use the chemical name weldbright. After that rinse that chemical with water and allow it to dry once it's dried out completely with the help of rag and acetone clean it thoroughly and start the welding process.
Step 10: Complete Welding
Now once the entire frame is tack welded it's time for the full weld. I didn't attach the one part of the bottom was just to avoid any thermal warpage. I made a table like this in the past that's why I know that. To weld the body it's good to have a piece of aluminum. Since stainless doesn't radiate heat quickly that's why the aluminum base seems to draw some amount of heat through that. Because there are so many welds that are going to heat up a lot.
Welding the thick base went with a different approach. It's a two-wall construction the top is attached to the head while the bottom one is a separate piece. Want to reduce the weld in this area that's why I cut down strips and bent them in the shape according to the periphery of the base. With the help of bench vice and mallet, I bent them into the desired shape, and once they already I start the tack weld first onto the head area. To hold the strips to their place I use welding clamps and then tack weld them. This area went pretty well because all the welds go with just fusion welding. Once the bottom layer gets tack welded I made a complete weld and the entire piece is ready for further processing. The backplate onto which the entire headpiece is welded I welded a pipe frame inside it to avoid deformation of such a large piece of the sheet without having any vertical member inside it to provide strength.
So few tips to remember here.
1. Try to switch the welding areas. Try to alter the position of the welding area.
2. If it's possible to clamp a piece of aluminum use that. It draws the heat very quickly.
3. Try to fill the gaps first so that you are able to do fusion welding, that would be good and easy to do.
4. If you are using a filler rod then it's good to keep the amps setting at 50 amps. Too much current creates heat and warps the metal. Usually, formula is 40 amps per mm.
By following these things you are really able to make good welds. Just make yourself comfortable first and then start the weld, so that you are able to make a good weld. There are a few areas where grinding isnt possible so try to make a good weld bead to get a nice and smoother result.
Step 11: Grinding and Polishing.
Grinding and polishing on stainless is not a big thing for me but this project is a bit harder and I would say things didn't go good as I intended to go. There are many places where I should grind first and then weld it to the adjacent side but the downside is that, by welding the part become rigid and if further refinement is needed I won't be able to do that. Also, the material thickness is not enough to provide room for error which I made a lot.
There is a total of around 100 parts and all of them attached to one another, so work is definitely increased a lot. Having a sheet metal bender is absolutely necessary for this build, it will eventually going to reduce the grinding work a lot. To me, it took 2 days of grinding and polishing work. I started with a 120 grit flap disk and goes up to 320 grit. From thereafter I switch the wheel and use a 400, 600 grit scotch Brit wheel. Make sure as the grit size increase try to do the process at slow rpm. Usually, I recommend 4000-6000 rpm would be sufficient enough with some wd40. Once it's done buff the piece and it's all new and shiny. You can weld a clip also so that you can hang it wherever you want.
Step 12: Conclusion and Final Shots
There are so many things I went wrong and I think if I suggest then you can take the following
precautions. Believe me, those gonna save your time a lot.
1. Use a laser cutter for cutting parts and avoid the separation where you can create Bends by sheet metal bender. For this perticular work, you actually need a sharp line sheet metal bender, which is capable of creating sharp lines.
2. Material needs to choose thick 18gauge is a lot thinner. I would suggest going with 14 gauge because at high temperature the material tends to warp especially stainless. Mild steel has less distortion but then you need some other operations to prevent it from rusting.
3. Tig welding is absolutely mandatory for this project. You don't need a bigger cup to make these welds. With number 4 or 5 cups to are easily able to get a good result and save a lot of argon compare to 10 number cup.
4. Having scrap pieces of aluminum is always good to cool down your material to avoid warpage.
5. The bottom plate needs to be constructed in one single sheet that definitely uses a little more material but it's worth enough compared to those separate sections.
If you have suggestions then please let me know.
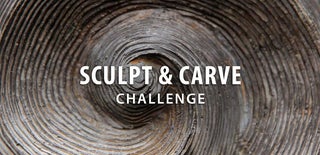
Grand Prize in the
Sculpt & Carve Challenge