Introduction: Start Blacksmithing
In this Instructable I will show you how to start up a foundry of your own. Now I am in no means saying this is the only way to do it, I am just showing you how I did it. So, let's get started!!!
Step 1: Forge
Now, before you even start thinking about getting an anvil or hammers, I suggest you start looking for a nice forge. This will probably be the most expensive thing you will have to buy if you are getting a gas forge, so this will really decide wither or not you really want to get into blacksmithing. Now you have two choices: coal or gas. There are benefits to both.
With a gas forge it's a lot cleaner and easier to use. They are also more portable. But they have less control over temperature and can get very pricey for gas and the initial cost of the forge.
With a coal forge it's a lot cheaper (next to nothing) to buy/make and you can control the temperature better. But coal is also very messy and depending on where you live you might not have a source of coal nearby.
The choice is up to you. I went with a gas forge because it fit my needs better, but do some research to see which one is best for you.
Step 2: Anvil/Hammers
Now comes anvils and hammers. As you can see there isn't a whole lot to it. I got the hammers at Harbor Freight, but there are some nice ones at Lowe's or Home Depot. What I suggest you start out with is a good ball-pine hammer and a mini sledge hammer. Make sure they are not to heavy for you, because you will be swinging them for hours at a time.
As for the anvil, I got a small piece of railroad track to start out with. Anything big, flat and metal should work fine. It doesn't have to be shaped like an anvil to work. Also, make sure you have something to attach the anvil to, like a big log. I suggest you look on Craigslist for anything. I know Harbor Freight had a small 15 pound anvil at one point. If you want to get serious about blacksmithing, you will want to put some money behind a real anvil. They will work much better and allow you to have more control, but they are very expensive.
Step 3: Metal
Your are going to need some metal for smithing. You can get some rebar or any scrap bar metal you have lying around as long as its not galvanized. Galvanized metal is very dangerous and if you are not careful it can kill you. If you do want to use galvanized metal (not recommended at all) make sure you are in an open space with very good ventilation. But, again, i would suggest to just stay away from it. I used some old radiator bolts and rebar. Again, check on craigslist for anything someone wants to get ride of before going out and buying some.
Step 4: Optional Items
You can also get some chisels and punches to cut and punch your metal. Another thing that I still need to get are some good tongs. They are very useful for holding the metal when it gets to be small. You don't need them though it you keep the piece long until the last heat and cut it, but if you want to really get into smithing these will be a must have.
Step 5: Staring the Forge
By this point you have the bare essentials needed to start smithing. Your going to want to get you forge all set up and do an initial start up. Make sure you use precaution, as these things get insanely hot. Keep the forge well away from anything flammable, and be mindful about your surroundings. Always asume what you are picking up is hot!!!
Step 6: Start Hammering
Start pounding on that metal!!!! I don't suggest you wear gloves as they get in the way and can catch fire. But it's all a matter of preference. Also, hammering is not as easy as it looks. It takes months to even learn how to do it right, and years to master it.
Step 7: Example
I made a little holder for my hammer. There are numerous things you can make. Go onto YouTube for some great blacksmithing tutorials.
Step 8: Hope I Helped!
I hope this Instructable helped you in starting up in blacksmithing. Please feal free to leave comments on what you liked and didn't like, and post any pictures if you get started. Thanks for reading and hope you have fun blacksmithing!
Step 9: Pictures
The pictures of the coal forge, the second anvil, the blacksmith tongs, and the guy hammering are not mine. I found them on Google images to better help you with this tutorial.
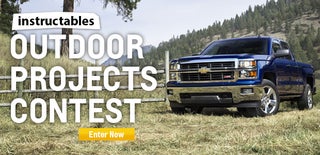
Participated in the
Instructables Outdoor Projects Contest

Participated in the
Manly Crafts Contest