Introduction: Steel Bamboo
This project is entered in the Steelworking Contest, please vote if you like it.
NOTE: In the image above I just show a short section with a single node as an example
PROJECT SUMMARY: I'll explain a technique I came up with to transform galvanized steel pipe into faux bamboo poles to create a building material that has the beauty of bamboo but with the strength, versatility, and longevity of steel. They can be used for a variety of home projects from porch swing or hammock supports, to birdbath columns, or shade sail support beams, and also for interior uses like a custom bamboo desk (On my list of future projects).
(Ignore my Side Stories if you want to get straight to the build.)
SIDE STORY: I came up with this technique a few years ago when I was building a lightweight suspension shade system made from 1/8" wire rope and a layer of reed fencing material to cover my BBQ area. I needed a higher anchor point than I could get with my property's block fence which is only five feet tall, so I was setting some electrical conduit vertically in the ground. While working with the pipe, I noticed some metal rings I had on my bench for a different project and thought, "Hey, that'd be cool to use those to create the nodes on bamboo stalks, but surely they are not the proper size." Guess what?, they WERE the perfect size. And thus:
Steel Bamboo was born.
Supplies
- 1-1/4" Electrical Conduit Pipe
- 1-1/2" Metal Rings (Carried by Ace Hardware)
- 2-Part Metal Putty Epoxy
- Smaller Diameter Wire (4mm Bonsai Copper Wire Recommended)
- Bondo Glazing Putty
- 400 Grit Sandpaper
- Primer and Base Coat Spray Paint
- Additional Non-Aerosol Paint (Optional)
TOOLS:
- Metal Cut-Off Saw
- Artist Paint Brushes (Optional)
Step 1: Gather the Materials
One of the two key materials is the Electrical Metal Tubing (EMT), which is a galvanized steel tubing. This tubing is ideal for both compressive and lateral load uses (within reason obviously). It lends itself very well to a variety of typical DIY home projects. Dimensionally, the tubing and rings are:
1-1/4" EMT OD = 1.510"
1-1/2" RING ID = 1.540"
NOTE: I'm just going to show the process on a short piece of tube. Initially I was going to do two nodes, but was rushed for time so just did a single. (Ignore the second ring in the picture above.)
Step 2: Add Ring(s)
Slide the ring onto the tube, mix a small amount of the two-part epoxy, and secure the ring as shown. Apply the epoxy to JUST this one side. (Dipping your finger in water gives more control to smooth the epoxy.)
NOTE1: The right side in the images above will become the "Top" side of the bamboo.
NOTE2: I think I may have used the Marine Epoxy last time I did this. It was easier to work with than the metal version and has a longer working time too. (Either will work and both will stand up well to outdoor environments.)
Step 3: Fill & Blend Top of Node
Once the epoxy has set from the previous step, add another layer, blending approximately as shown above.
Step 4: Fill Underside of Ring
Mix a smaller amount of epoxy and fill in the underside of the ring. Goal is to fill the void and just get a flat edge or slightly curved in the downward direction.
Step 5: Secure Temporary Wire
For this step, we need to add a loop of wire that will serve as a form to be removed later. Many different types/sizes of wire can be used for this step. I found that soft copper bonsai training wire works well. (This is 4mm diameter.) Use tape, masking or duct or aluminum, as I used, to secure the wire in place.
IMPORTANT: Adjust the spacing of this wire from the ring by 1/2 to a full diameter of the copper wire as shown in the second image above. You will need this spacing to be able to remove the wire later.
Step 6: Create the Bottom of the Node
Similarly to the top portion of the node, mix the epoxy, and apply to the copper wire.
Step 7: Remove Tape & Wire Form
Wait for the epoxy to set (just the working time, you don't have to wait for the full 60 minute cure time.) and gently remove the tape and the wire.
NOTE: The gap between the wire and the ring we set in the earlier step can now be used to push the wire into to allow the wire to be removed.
Step 8: Fill & Blend Bottom of Node
Just like in step 3, add additional epoxy to blend into the main tube on the bottom side of the node.
Step 9: Wet Sand
Use the 400 grit wet sandpaper to get a smooth surface.
Step 10: Prime Paint
Clean thoroughly, and apply a coat of primer paint. (Color doesn't matter.) Allow to dry overnight.
Step 11: Bondo Time
Use Bondo Automotive Glazing Putty as the final step in creating the contours of the node. Use the same 400 grit wet sandpaper between applications. Usually takes about three progressively smaller applications and sanding steps to get to a finished surface. The main goal with this step is to perfectly blend from the epoxy to the top and bottom sides of the nodes into the main tubing.
Step 12: Base Coat
Previously, I had to paint mine a light tan to avoid the notice of my HOA, but for this example I figured I'd go for natural green. (This spray paint is "Valley Green" from Hardcore Brand Spray Paint)
Step 13: Final Touches
At this point, you can leave it as is or choose another shade of green or brown and simply paint the gap between the upper and lower portions of the node. This would be my standard choice as I'm not artistically inclined, but with the help of my oldest, she was able to take it to the next level with three additional shades of green, light and dark brown, a white, and a yellow.
Step 14: Finished!
Thanks for taking the time to read through my Instructable. Please send me any questions or comments you might have. I try to answer them all. Stay safe and healthy! Happy DIY'ing!
Remember to vote in the Metalworking Contest.
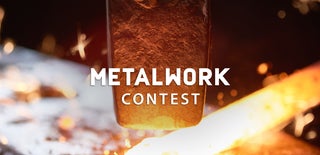
Participated in the
Metalworking Contest