Introduction: Steel Strapping Stool
This is an instructable on utilizing a material that normal gets thrown out: steel band strapping. This was mostly an idea that Sam had and that we were both curious about. While some elements of this were planned there was not a ton of design. We both have some background in metal work and fabrication so the build went fairly smooth. There definitely were lessons learned. Thanks for checking out our instructable.
Also, Vote for us in the trash to treasure contest if it isn't too much trouble.
Step 1: Prep/clip Removal
The first image is a good representation of how much banding/strapping gets thrown away at our shared shop. This was not a particularly heavy package week at mhub (the manufacturing coworking space here in Chicago where this was built). We pulled the materials and snipped off the metal clips. While we did consider using them they seemed a dissimilar metal and so we decided not to use. The tool used was a sheer. Could have easily been done with snips.
Step 2: Cutting to a Consistent Size
We used a hydrolic sheer to cut to a consistent size. The sheer stop was not set correctly which threw off some of our calculations but it gave us nice clean ends. We did some back of the envelope calculations based on tightness of the weave and the needed seating area based on aesthetic choices around joining. Nothing complicated here.
Step 3: Underwater Basket Weaving
This was a bit fussy. Sam did the weaving. Apparently there is a minimum spacing needed because the straps only have so much give. We were both surprised that the straps do not do tight curves (they snap/sheer). We explored other weaving patterns but went with this straight forward over under matrix. It gets progressively easier once you have pieces in place. Use heavy objects to hold down initially.
Step 4: Welding/Fabrication
We tack welded a couple of the sniped ends. We ended up running significantly hotter than the gauge of sheet metal we were using hypothetically should be based on the Miller chart on our machine. Just check the underside for penetration and keep fiddling with settings. We got it right in about 5 setting changes. The coating did not seem to affect the final tack joins. Their placement was mostly based on aesthetic choices. The resulting surface is very flexible and bendy. Really quite giving and comfy and somewhat textile like (rattan like maybe but heavier weave?). The stool itself had some minor give. We did not account for the amount of give in the straps and probably should have built taller or made an accompanying stool.
Step 5: Finishing and Enjoying
This isn't some deep dive into making. We saw some scrap and said hey there is a use for that. Is it a material that we will consistently reach for in the future: probably not. It is/was interesting to explore and the result was fairly high quality relative to effort. We did not paint or grind to aesthetically sharp finish. That said the only real issue per se is perhaps the amount of give. We might add some rod cross bracing to reinforce. This was a fun way of upcycling a material that normally gets tossed. Hope you enjoyed our little weekend project.
Cheers,
Mhubian
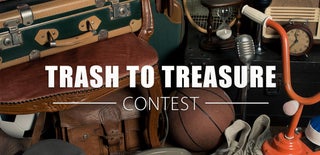
Participated in the
Trash to Treasure