Introduction: Steel Truss Model
This model was constructed to show students and other makers how railroad bridges are designed and built, and I also wanted to show people how simple metalworking can be. This concept might be adapted for use in an Arduino-driven robot, advanced trebuchet, or perhaps even a sculpture, and the zinc-plated metal I used resists corrosion well
The design makes use of two 1/2 x 3/4 x 23 inch main beams spanning the length of the truss, reinforced by 1/2 x 4 3/4 inch cross members. The whole assembly is held together with 1/8 inch pop rivets, and I was able to create the prototype in this article within the space of an afternoon.
I built the truss out of scrap steel taken from a broken telescope tripod and the casing of an old computer DVD drive, and, as I already had rivets and a power drill, I only needed to buy a carbide drill bit. Building this model is a good hands-on way to learn about engineering trusses, and it is also a good rivets and sheet metal skill builder. The supplies you have may vary, but aside from tools, you should be able to build your own model steel truss for less than fifteen dollars - less than many Erector sets!
Step 1: Tools and Materials
This list is not exact, nor is it exclusive - you could easily substitute different rivet systems and/or starting materials, if those listed below are unavailable - but please use common sense and follow safety guidelines.
Tools:
- Drill or drill press. A corded drill is preferable, as you be be drilling several dozen holes
- 1/8 inch carbide drill bits; regular wood bits will dull very quickly drillling steel, so you need something harder
- Rivet gun, capable of riveting 1/8 inch pop-rivets
- Aviation snips, preferably both straight-cutting and curve-cutting pairs
- Dremel with abrasive cutting wheel (optional)
- Small crescent wrench
- Metal file (not shown)
Materials:
- 1/8 inch pop rivets
- Angle steel. I used scrap left over from a broken telescope tripod, but you could also use old curtain-rod railings
- DVD or CD drives. I took these from a defunct PC and used the motors for other purposes, leaving the mild steel casings in my collection of scrap metal; other sheet steel, like old tin cans, would also function but would not be as strong.
Please remember that you will be working with metal and with power tools. Aviation/tin snips leave sharp edges that will cut if you are not careful, and the shards left over from the drilling process make for very annoying splinters. With that in mind, here is the recommended safety equipment:
- Safety glasses or face shield
- Tough pair of gloves
- Closed - toe shoes
- Earplugs or earmuffs
- Magnet (for managing drill tailings)
Step 2: Making the Cross-members
My angle steel pieces were 23 inches long, and I wanted to have a distance of 3 inches between the main beams of the truss. I decided to cut 18 cross-members from our DVD drive cases, each measuring 1/2 inch wide by 4 3/4 inches long, to ensure that the angle between these cross-members would be close to 65 degrees and that the entire length of the main beams would be reinforced.
I marked out our cross-members on the drive's lid, which had a clean, flat surface, and proceeded to cut the strips out with aviation snips. I found that although the straight snips shear cleanly when you begin a cut, they start to get in the way as you get through to the middle of a piece of sheet metal; bent-handled snips (intended for cutting curves) allow you to keep your hand out of the way and make the cutting process much easier. Continue cutting until you have 18 strips, and perhaps a spare. Remember to straighten your strips after cutting; smaller sheet metal pieces tend to curl when manipulated with snips.
Step 3: Drilling the Cross Members
The next step is adding holes in the cross-members so that they can be joined with rivets. Mark the center of the holes 1/4 inch from the ends of the strip and centered relative to its sides; the photo above illustrates where the hole needs to be.
You should always wear gloves when using a power drill, but it is especially important when drilling metal. Not only is the spinning bit itself dangerous, but you can also hurt your bare hand quite badly if a strip of metal gets stuck on the drill and spins with it. Remember to go slowly and use oil as you drill, as this promotes cleaner holes, cooler drilling temperatures, and longer life of the bit.
I recommend that you ream out each hole slightly after drilling. Later in the build process, I discovered that 1/8 inch pop rivets are just large enough that they won't fit unless you modify the holes in the cross members.
Step 4: Final Assembly
When you have all 18 cross-members prepared, you are ready to assemble your truss. Instead of measuring, marking, and drilling the rivet holes in the main beams (as you did with the cross members), begin this step by squaring up those lengths of angle steel with three inches of separation between them on your work surface. Lay out nine of the cross members on top of the main beams: pieces rising from left to right should be on the bottom, while pieces falling from left to right should be placed on top of the first layer (as seen looking directly down on the truss).
Match up the holes in the cross-members to the middle of the main beams such that their centers are 1/4 inch from the top and 1/4 inch from the bottom of the sides of the main beams, positioned as shown (the holes are not visible but the pieces overlap the same). You will then drill through both pieces into the main beam to produce a hole that lines up exactly with the cross members used. Remember to ream the holes so that the rivets will fit.
Next, rivet your parts together. Insert and squeeze pop rivets into the holes your just drilled so that you join the first nine strips to the main beams, then, turn the assembly over and add the other nine strips. If you intend to use this model for anything besides static display (such as showing it to people at a Maker Faire), remember to file down the sharp edges of the cross members.
I hope you enjoyed this Instructable! If you have any questions, concerns, or need clarification, feel free to indicate so in the comments below.
You can find Valkyrie Aerospace's other projects at km4lvc.wordpress.com
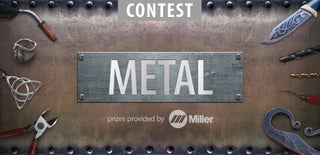
Participated in the
Metal Contest 2016