Introduction: Stylish Concrete Phone Stands
As mobile developers, we have a bunch of phones laying around on the desks. A phone stand dramatically improves the readability and handling; this model helps reduce the cable clutter, and is remarkably stable due to its weight.
Having experimented in a previous project, I wanted to redo it with some improvements:
- Slant should be 45°,
- there should be a slit to allow USB cord and plug connection,
- a cavity both decreases the weight, and provides room to roll the cable,
- I wanted a curved shape.
The mold allowed us to produce phone stands almost en masse (so far 6 pieces) in the office during lunch breaks, in 3 sessions of approx 20 minutes per stand.
It's incredibly fun to teach your colleagues concrete mixing in the office!
Step 1: Create the Mold (1)
The mold side is based on a piece of PVC pipe.
1-2. Cut the top at a 45° angle
3-4. Repeat, leaving a 1 cm-thick border at the bottom
5. Cut the base side at a right angle. With some cardboard, check with a real phone
6. On the bottom side, cut out a 5mm wide slot, from front to back;
on the front-top side cut out a 1.3 cm wide slot;
precisely cut the front side for later demolding.
Step 2: Create the Mold (2)
The mold base consists of 3 pieces of plywood.
The two large ones are glued together.
The small one, to create the USB plug groove, is removable, and holds thanks to a pin on one side, and a pin (or screw) on the other side.
It is time to precisely adjust the PVC so that there is no extra space.
The plywood shall be well coated with lacquer ow waterproof paint.
Step 3: Create the Cavity
The cavity is thin on the front, to pass the USB cable, and becomes a larger chamber to hold some loops of cable.
Making the insert out of 3 plywood pieces will best allow demolding.
(In an earlier attempt of making the insert in one piece resulted in breaking the concrete during demolding).
The wood pieces have to be coated with a waterproof paint, else the concrete will adhere to them.
Step 4: Get the Mold Ready
Tape the PVC piece.
Apply Vaseline to the insert.
Oil the inner side of the PVC, and the top sides of the plywood base.
Position the PVC on the base, and the insert on the PVC.
Tape everything together.
Find a container having a border such that the base can rest at 45°, leaving the surface horizontal.
Step 5: Mix and Pour the Concrete
Mix some fine-grained concrete. I had to sieve my one to remove the too coarse grains.
Mix slowly in order to not create too many bubbles.
With a stick or screwdriver, ensure that the concrete fills every corner of the mold.
Do not fill over the insert, so that it can be later demolded.
Tap to have the bubbles raise and pop.
Check the positioning so that the surface is at an horizontal level.
Step 6: Wait...
For this size, it will take between 4 to 7 days to cure.
Step 7: Demold
Time to carefully demold.
You can rectify the imperfections with sandpaper (and even a file).
You may apply some putty if desired. Personally, I did not, as some imperfections give its character to the concrete, and after some training I was satisfied with the results, using sandpaper only.
Check that the base does not wobble, and sand it until it stands stably.
Step 8: Seal
Applying concrete sealer is necessary to glue the sand grains together and avoid erosion by sole touch.
Step 9: Spray Paint
Apply a couple of thin layers of spray paint.
Personally I wanted a thin layer, letting the concrete character show through.
Depending on where you do this job, cover a large area with newspaper, as the paint is very volatile.
Optionally, you can stick paper or felt pads on the bottom to protect the surfaces it will stand on.
Step 10: Finished Product - Use It
Now the bonus is the cavity for the cable.
Here is how to have the roll stay into the chamber:
1. make a cable roll, leaving desired length free on each end,
2. twist the roll to make an "eight",
3. insert that into the chamber.
Step 11: Repeat - Improve - Many Times!
Several trials were made, as you can see on the last photo, from left to right:
- v0 - Made with a Tupperware. See https://www.instructables.com/id/Easy-Stylish-Concrete-Phone-Stand/
- v1 - Made with a PVC pipe. Problem: cavity insert in one piece, almost impossible to demold.
- v1.1 - The cavity insert is in 3 pieces. Problem: as the stand is too short, the USB cord bends too much.
- V2 - The final design.
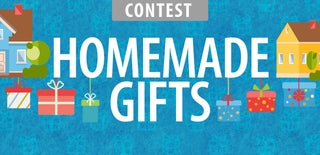
Participated in the
Homemade Gifts Contest 2016
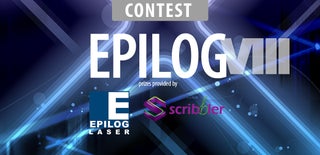
Participated in the
Epilog Contest 8
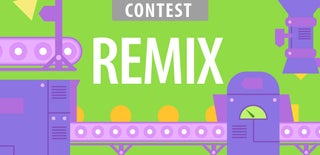
Participated in the
Remix Contest 2016