Introduction: Super-Sized RGB Seven-Segment Display Lamp
Hello all! I will be showing you how I constructed my Super-Sized Seven Segment Display RGB Lamp although you probably already gathered that from the title š. As seen in the images above, this project will be a scaled up version of a seven segment display which is most commonly used in the vast majority of digital clocks. In the real version, each of the seven segments can be independently controlled to form the numbers zero through nine. Although these displays come in a variety of sizes, the one I modeled this project after is aproximately 1cm X 2cm. However, since this Instructable was created with the intention of being entered into the Super-Size Speed Challenge, the one we'll be constructing is approximately 13cm X 20cm. Since this project utilizes an RGB floodlight it can display a wide number of shades and brightnesses.
A great thanks to Nikodem Bartnik for providing me the inspiration it took to finally complete my CNC router which will be utilized in this project. Although I modified his Dremel CNC to work with what I had, I wouldn't have done it without the inspiration and support of his project. I figured this design would be a great opportunity to discover the capabilities of my newly built DIY CNC router. However, the same result could most likely be achieved with a skilled jigsaw operator.
Supplies
- 13cm X 20cm X 1cm (5in X 8in X 0.25in) plank of wood or other suitable material
- RGB Floodlight or other light source
- Clear plastic bags to form a light diffuser
- Two screws or posts that are approximately 40mm in length and 3.5mm in width
- Sandpaper
- Stain (optional)
Step 1: Roughing Out the Design
I've had the idea for this project for about three months now but I never really took the time to really start working on it. Shown in the image above is a very rough sketch showing the basic dimensions of what would become the final product. Unfortunately, the design is not completely to scale but I felt that it created a much more aesthetically pleasing result at the end of the day.
Step 2: Converting to CAD and Generating the Toolpath for the CNC Router
Allow me to preface this step by saying I am definitely no CAD expert but I'm usually able to struggle my way through š.
- I created a rectangular sketch that matched the dimensions of the overall stock (the piece of wood or other material of your choice).
- I then extruded the sketch to match the thickness of the stock
Here is where it starts to get a little bit tricky. I had to find a way to accurately and efficiently place the seven rectangles that would eventually be cut out on the router.
- A point was placed in the exact center of the rectangle that was created in the previous steps
- Then the "Center Rectangle" option was used to create a 20mm X 60mm whose center matched the point that was placed in the previous step
- Another "Center Rectangle" was placed above the first rectangle with its center being 65mm away from the center of the first rectangle
- The second rectangle was mirrored using the "Mirror" function to result in three, equally spaced horizontal rectanglesTo create the vertical rectangles a "Center Rectangle" was placed on the top left. The center was 65mm from the top and 20mm from the side.
- The "Mirror" function was used again to create a rectangle of the same size and position but at the bottom left of the stock.
- The "Mirror" function was used one more time to mirror the last two rectangles on the opposite side.
- The "Extrude" function was then used to cut the rectangular shapes into the stock
- A toolpath was then generated using the manufacture environment in Fusion 360 to produce the CAM
I hope that made sense but if you have any questions on this instructable, or anything else for that matter, always feel free to comment and I will do my best to assist you. Also, the CAD file is available to be downloaded below as well as the simulation of the CAM.
Step 3: CNC Routing
The CAM (Computer-Aided Manufacturing) which is used to generate a toolpath for the CNC router using G-Code (a language the control board can understand) was exported from Fusion 360. The file was then opened in the program CNCjs which is responsible for sending the G-Code to the control board of the CNC router. The router was zeroed, and the proper safety measures were taken before the program was initiated. After eleven minutes and thirty-six seconds I had a (mostly š) finished product.
Step 4: Post-processing (Sanding and Staining)
After the routing was finished, a file was used to remove the majority of the rough edges left by the router. Then the piece was sanded with 80 grit, then 150 grit sandpaper. This process may seem tedious but it will pay off in the long run. This was a part of the project that I wish I had spent more time on. This is because the final product shows errors due to sanding such as "bowing" in the segments because of uneven pressure while sanding. Also, small fibers of wood can be seen protruding from the walls of the segment when the floodlight is off.
Ebony wood stain was applied in order to provide a dark appearance, while still allowing the grain of the wood to show through nicely. To stain the wood, I used a slightly damp paper towel dipped in a small amount of stain (a little goes a long way trust me I speak from experience š.) If you yearn for a darker coloring you can apply additional stain as you go but be careful to not add too much that the grain is not visible. The grain of the wood can be identified by lines that run either horizontally, or vertically through the stock. In order to properly apply the stain, the paper towel should be run parallel to the lines using long strokes. If it is your first time staining wood I would recommend staining the back of the piece first in order to gain confidence.
Step 5: Fabricating a Light Difffuser for the RGB Floodlight
Originally, I planned to use a plastic diffuser sheet that I had salvaged from a broken LCD monitor. However, upon testing I discovered that the plastic sheet did not create the even glow I required. Eventually, sheets cut from recycled clear plastic bags were layered to create the diffuser. The sheets were cut slightly smaller than the dimensions of the overall stock (13cm X 20cm). In the end, I cut out about fifteen layers which I found was an acceptable compromise between evenly distributing the light and maintaining brightness.
Step 6: Modifying the RGB Floodlight (Optional)
The manufacturer of the floodlight placed the power cord in such a way that it is not ideal for our application. The strain relief nut assembly that ensures proper water proofing does not allow the cord to bend well. This means that the lamp is unable to properly sit on a flat surface. If you do not want to go though the hassle this step requires, you can simply mount the piece of wood "upside-down" with the cord coming out of the top of the floodlight. However, if you're a perfectionist, like me š, this step is for you. Before continuing be sure to unplug the floodlight from the power source.
- Remove the four screws on the front of the floodlight
- Try not to touch the inside of the front glass and bezel assembly while placing it somewhere safe and dust-free
- Remove the Silastic that locks the nut in place on the inside of the body
- Carefully loosen the nut on the side of the body
- Once the nut is free, attempt to pull the part that the nut threads onto away from the body towards the end of the plug. There is a rubber piece inside the assembly which makes it somewhat difficult to move. This rubber piece can be removed with diagonal cutters but be sure to not damage the wire
- Now the wire can be routed to the side while staying flush against the body
- In order to maintain some form of strain relief hot glue can be applied to fill the hole and hold the wire in place
- Once you are satisfied, replace the glass and bezel along with two of the bottom screws. (Do not tighten down the screws all the way. This will make sense later š)
Step 7: Attaching the Wooden Outline and the Diffuser to the Floodlight
Four screws, preferably with a point and around 0.25 inch long, are needed to attach the diffuser sheets to the back of the wooden piece. Using a screwdriver, slowly drive each screw through the plastic sheets and onto the back of the wooden piece while making sure the sheets stay taught. While doing this you need to constantly be aware of two problems that could occur. The first one being that the screws you picked are too long and are beginning to protrude through the front of the wooden piece. The second one being the screw is placed too close to the edge of the wooden piece which could cause the wood to crack. Next, use a drill bit to make two small holes in the wooden piece that line up with the two screw threads in the top of the floodlight. Pass the long screws through the wood piece and just enough into the floodlights. For additional style points you can color in the heads of the screw with a black permanent marker. As long as you remain careful and patient, this step should go smoothly and move you one step closer to a final product. However, if you do happen to make a mistake, just take a deeeeep breath and figure out how you are going to turn that mistake, into a feature.
Step 8: Possible Next Steps and Other Ramblings
As with every project I have ever completed, there are a number of things I would do differently if I was to redo this project. Since it involved so many skills, both new and old, there was a lot that I learned. For example, I learned that I should always make sure that when the router is running, the spindle is on to avoid breaking the end mill when it collides with the stock. In the future I would like to use RGB strips in combination with an Arduino in order to display specific numbers on the lamp. This would allow me to include features such as a countup or countdown timer.
In life you have to constantly and consistently keep moving forward. Stay in one place too long and you'll get stuck. This is why it bothers me when people ask me if I am "done" with a project. A true project, or anything for that matter, is never truly done. You should always keep looking at it and asking yourself a number of questions such as "What did I learn from this?" or "What could I do better next time?" Also, remember that you're always going to find faults in your own work no matter how perfect it turned out. During this project, I made a number of mistakes and miscalculations that I thought were going to ruin the whole project but I ended up learning from them. I broke my first end mill on my router, I got a splinter, I cut my finger but at the end of the day the final product and what I learned from it made it all worthwhile.
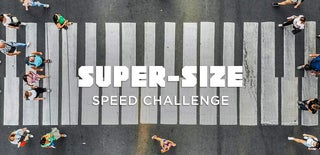
Participated in the
Super-Size Speed Challenge