Introduction: Table Saw Caddy
If you're like me, you utilize a lot of smaller tools and items at the table saw. From push sticks to pencils, these things always seem to be in the way when you don't need them and out of reach or hard to find when you do need them. This project seeks to solve that issue as well as provide you drawings and videos to assist you in building your own version of the Table Saw Caddy. This project could easily be modified to fit your particular needs at many locations in the shop.
I should note that I used several joinery methods in this project that are absolutely not required. Projects like this are great for honing or learning new joinery skills which is what I did. Feel free to change any of my joinery methods for methods you wish to practice or learn.
Supplies
- Scrap Lumber - I used scrap hardwood left over from previous projects
- Wood Glue
- Blue Painter's Tape
- Metal Brackets - Sourced from the big box store
- Rubber Feet
- Epoxy (Optional)
Step 1: Drawings and Videos
I've included both my drawings as well as my video here for you. You can also find them as well as other projects on my website. Additionally, there are many other projects on my YouTube channel that you may also enjoy.
Attachments
Step 2: Tools
Listed below are the tools that I used based on the different joinery methods that I chose to use. These joinery methods are not required for this build and much simpler methods would work just as well.
- Table Saw
- Jointer
- Planer
- Router Table
- Bandsaw
- Bandsaw Dovetail Jig (Optional)
- Drills/bits
- Trim Router (Optional)
- Sanders
- Spindle Sander (Optional)
- Drill
- 1 1/2" Forstner bit
- Chisels
- Dovetail Saw
- Marking Gauge
- Marking Knife
Step 3: Lumber Selection
Although I used scrap walnut and cherry for this project, just about any lumber of choice will work. You could certainly purchase material for this project but, projects like this are a great way to reduce that pile of shop scrap and still get some use out of that lumber.
Since my lumber was unusable for my furniture projects, with the use of epoxy it became an excellent choice for some shop furniture.
Step 4: Stabilizing and Milling Lumber
For safety reasons, I started with lumber that was a little longer. I prefer to keep material longer than 12" to feed through my planer to avoid any kickback issues which could damage my planer.
With all material cut oversized, I filled the knots and defects with tinted epoxy and allowed to cure for about 18 hours. Although I used West Systems epoxy, there are faster curing epoxies available.
With all the knots and defects stabilized, I then milled the lumber per the plans and cut to final sizes.
Proper Milling:
- Flatten one face at the jointer
- Square up one edge at the jointer - Flat face against the fence
- Use the planer to get the opposing face flat and parallel to the jointed face and bring to final thickness
- Use the table saw to trim to final width.
Step 5: Pencil Box
While I was waiting for epoxy to cure, I had enough clear 1/2" thick walnut to work on the pencil box.
It's important to know the thickness of your table saw blade in order to make the splines for the miters which provide a great deal of strength for this mitered joint. In my case, I'm using a full kerf blade which is 1/8" thick.
Using scrap Cherry, I cut/milled some 1/8" thick cherry to use as spline material. A dry fit of the box will be required to measure the final width of these splines which will be installed during the glue up. You should also cut some additional material (about 12" long and 1" wide) for use in the center divider step of this instructable.
- Note: There are several woodworking ways to reinforce this joint. This is just the method I chose to use so, feel free to do something different.
After cutting the 4 sides of the box to a rough length, I used the Small Box Miter Sled to cut the miters on each side to 45 degrees as well as cut the kerfs for the splines. I used a stop block on the sled to ensure that each side was exactly the same length of about 3 1/2".
- Note: There's a separate Instructable for the Small Box Miter Sled that I used for this project. Although it is not required, this sled was used for making the 45 degree ends as well as the grooves for the splines.
With each side cut to identical lengths with 45 degree ends, I placed them upside down on the table and used blue painter's tape to tape them together at the seams. I then flipped them over, applied glue to each end, closed up and installed splines, allowed to dry.
Once the glue was cured, I trimmed the splines to be flush with the top and bottom of the box.
Step 6: Tray Parts
Since I'm still waiting for epoxy to cure, I decided to make the tray parts next.
Using 1/2" thick material, I cut the stock for the tray leaving them extra long. These will be cut to final lengths just before assembly. Finished length will be around 7 1/2" on the long side and 4 1/2" on the short side. They're also cut to around 2" wide. These final dimensions will be determined by the actual completed piece.
I laid out and marked for the single dovetail for the outside corner.
- Note - Although I used the bandsaw and a special jig at the bandsaw to cut one side of this joint, this joint can be completely cut by hand.
- Jig - If you want to make this 1 to 8 jig, use the following steps.
- Find some scrap material with parallel sides. Width doesn't really matter. Around 3 or 4 inches is fine.
- Measure over up 8" on one side and draw a line at 90 degrees at that point. Measure 1" over on that line and mark the location.
- Draw a line from the bottom corner to the mark you just made. This is the angle line to be cut.
- Cut that angle
- Apply a small support foot at the bottom to support work piece.
If you're cutting this dovetail by hand, simply follow traditional dovetailing methods to cut the dovetail.
- Set a marking gauge to the thickness of the material and mark the end of one board
- Use a marking knife to mark the dovetail
- Use a dovetail saw to cut on the waste side of the knife line.
- Use chisels to cut out the waste as well as pare down to the knife line.
- Use this board as the pattern to mark the other board
- Repeat the earlier process to remove the waste material from this board. - Be sure to stay on the waste side of the knife line.
Note - This is a very simplified process for cutting dovetails. There are numerous videos and tutorials for learning this skill.
Once the joint is fitting as you want it to, set the parts aside for assembly and install later in the project.
Step 7: The Base
With stock cut to final size per the plans, there's a little bit of joinery work to do before assembly. As with the rest of this design, these joinery methods can be changed out for other methods if you wish.
Layout the location of the joinery
- Measure over 2" for the center point of the sliding dovetail
- Measure over the final thickness of the angled side for the rabbet. This rabbet goes on the same side of the base as the sliding dovetail.
- Note: This should be 1/2" but, it's common to not be exact dimension.
Using the table saw with the blade set to 3/8" high, remove some of the material at the sliding dovetail. This will help the dovetail bit at the router table by reducing the amount of material needed to be removed there.
Use the router table and a dovetail bit set to 3/8" high to finish cutting the sliding dovetail. Be sure to center the bit on the grooves you just cut at the table saw.
Important: Do not adjust the height of the bit when finished! We'll need this setting for cutting the male portion of this joint.
The only thing left to do to the base is to cut the rabbet on the edge to fit the outside angled side. Either install a dado stack in the table saw or make a few cuts with a single blade. The blade height should be set to 3/8"
Step 8: Center Divider
We'll start by cutting the male portion of the sliding dovetail. Adjust the router table fence so that only a small portion of the dovetail bit is protruding. With the center divider vertical and against the fence, run each side for the divider creating the male portion of the dovetail.
- Note - It's important to use some scrap here to set up the router table appropriately.
To cut the handle, use a 1 1/2" Forstner bit and drill a hole per the plans. Use the bandsaw or jig saw to finish the cuts creating the handle. Be sure to sand this area well.
To make the spline in the top, adjust the table saw fence so that the table saw blade is set to the center of the divider standing vertically. Adjust the height of the table saw to 1" and rip a kerf down the length of the to top of the center divider.
Next, install the spline material left over from the pencil box step with some glue and allow to dry.
Once the glue is cured, spend some time rounding off corners and sanding for finish.
Locate the dowel hole for the quick clamp and drill half way into the center divider. This dowel can now be installed with a little glue.
- Note - I made something slightly different in the videos but, the dowel is what I used in the prototype and it worked just fine.
Drill the holes in the very top to fit the items you wish to store there. Although I added sizes in the plans, these holes and mortise are specific to my needs so, make sure that you make these fit your needs.
Step 9: Outer Side
This side's shape was made to fit my custom push sticks that I use at the table saw. This shape could easily be modified to fit your needs/wants.
Once the piece is cut to final size and shape per the plans, sand and prep for finish.
- Note - As you'll see in the video, I inlaid a laser engraved logo into this side. This is an option if you'd like to inlay something more fitting for you in this location.
Step 10: Assembly
There's quite a few parts that have to go together! I'm going to assume you used my joinery methods in this step but, if you used different joinery methods, you may need to perform your glue up slightly differently.
- Glue in the center divider. Since this is a sliding dovetail, no additional clamping should be needed and it should be a good snug fit. If you changed this to a dado, some screws through the bottom would add some reinforcement.
- Glue the outer side - This may require a couple clamps to ensure it's seated well in the rabbet and is square.
- Note - A couple brad nails from the bottom could be used.
- Install the pencil box in the outer most corner. There should be a gap between the box and the center divider to allow for the clamp bar.
- Cut the tray parts to final length and install on the base. These final measurements should be directly from your project.
- Note - The pencil box and the tray parts are held down with glue only and clamped until the glue was dry.
Step 11: Finish
Just about any finish will work on this project. Shop furniture is a great place to use up finish before it goes bad or try a new finish that you haven't used before.
In this case, I kept it simple and applied a few coats of stray lacquer.
Note - If you're using lacquer as I did, be sure you're in a well ventilated area and wear an appropriate respirator.
Step 12: Bits and Bobs
There's a few additional metal parts added for additional function. All of these pieces were painted to match. These are all optional items that you may or may not want/need. These can now be installed.
- Angle Bracket - Added to the side of the pencil box. This is a steel bracket so that the magnetic base of my Wixey gauge (Digital Angle Finder) will stick to it.
- Z Bracket - Added to the outer side to allow a tape measure to slide on/off using the belt clip on the tape measure.
- T-Track - Added to the center divider to hold the flip stops for my Rip-Flip
- Rubber Feet - Certainly an optional item but, I had them on hand and now don't worry about the caddy scratching the top on my saw.
With the exception of the T-Track, these pieces were all sourced from the big box store.
Step 13: Closing
I've been woodworking for a great many years. This is one of those projects that I should have done a long time ago! Knowing exactly where to find and grab things at the table saw has improved my efficiency a great deal!
I do hope you enjoyed this project! As several have said, this could also be reconfigured and used at a few other power tool locations in the shop!
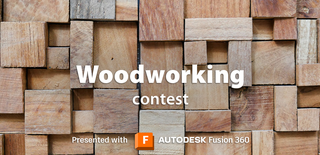
Runner Up in the
Woodworking Contest