Introduction: Homemade Camper Trailer
I wanted a teardrop trailer. A box-shaped one. Similar to Australian offroad, off-grid ones.
Yet the needs and challenges were great:
- It had to (somehow) house 5 people.
- Low (-ish) cost.
- Smaller size than a regular trailer
- Towable by Skoda Octavia MK3
- Limited availability of materials. Typical caravan/camper/motor home materials are unavailable rare or very costly in eastern Europe (waterproof galley hinges, windows, doors, etc.)
- Usable/climbable roof.
Optional needs
- Kitchen/galley
- Room fo stuff
So our options were:
- Continue tent camping - not a fancy option after multiple trips per year.
- Buy a used caravan - a 5 bed one .... is a monster to tow around, carrying 5 bikes is a no-go, black water tanks.
- Buy a motor home - a used one here costs 15-30K€ based on condition. It's a pricey vacation for those 3-4 weekend trips during summer.
It took quite a bit of time to convince the Mrs., but the argument of a family project with the boys was the tipping point.
Budget and build time: the overall build took around 2 months to do and ended costing 3,300€. (3,900$), the platform included. Yet I fully believe the price could be reduced to 2,500€ (~3,000€), as I purchased some tools and some unnecessary stuff. I did the blueprints on Autocad prior and it saved alot of time and headaches.
This project was done in spring 2020 during the corona lockdown, thus, allowing the time necesary.
The whole build is a project in motion and will most def change in the future. Please do check the material list, blueprints, and build photos on the next steps.
Build video timelapse from start to finish: the photos or @ https://youtu.be/4g8BufVWj2Q
Step 1: 2. Vision, Trailer, Wood and Blueprints
1. Vision
The first step was to work on the vision. Therefore, my oldest kid drew our yard with a teardrop camper inside ;)
The next step was the blueprints. I was certain it will save me a ton of time, effort, and mistakes. It did - somewhat.
They tried to teach me Autocad and making blueprints in uni 20 years ago. It was quite an experience trying to remember and do all the drawings on Autocad this year :D
I've also googled, pinterested and forumed 300+ teardrop trailers. You can check some of that know-how below:
- Pinterest saves on box shaped teardrop trailers: https://www.pinterest.com/kmorkunas/teardrops-box...
- Teardrop and camper van interiors: https://www.pinterest.com/kmorkunas/teardrop-trai...
- Some more interiors, kitchens, etc. https://www.pinterest.com/kmorkunas/camper-vans-t...
Also, quite a few teardrop/camper ideas here on Instructables.
2. Trailer: Purchased a trailer from a Polish manufacturer - Temared Transporter. Dual-axis for stability and weight resistance. I could go with the single-axis but was a bit reluctant due to stability and safety once it's fully loaded. Trailer size is 3 x 1,5 meters (9,48 feet x 4.92 feet). Height from the ground to platform - around 40 cm.
3. Plywood pre-cut: had the plywood panels pre-cut on an industrial CNC machine using Autocad blueprints I've developed during the 2020 Q1 winter. Plywood is a special water-resistant type that is used in construction (FSF plywood). The thickness of the plywood is 12 mm (0,47 inch). 9mm would be more than enough (0,35 inch). That extra weight creeps in fast.
If necessary, cutting can be done at home using a jigsaw/circular saw, though it would be much more labor-intensive.
Plywood weight is around 8 kg per 1 m2.
4. Construction lumber: bought construction pine. I have much more skill working with wood and not welding metal. Thus, my choice. Although if you have access to aluminum welding, I'd recommend going that way.
The wood measurements are 4.5 x 7 cm (1,77 x 2,75 inches) .
1 meter lenght of this stud weights around 2 kilos, so you have to be cautious of the overall weight going in.
As I had no proper garage/shed to construct this, it was all done outside with whatever weather protection available.
Btw, you can see some of my other Instructables in the backgrounds - yard chessboard and pergola.
Step 2: 3. Tools, Materials
I only have basic woodworking skills and basic tools. Thus, had to improvise at times.
What really helped is that I marked all the screw/fixing positions in Autocad, which helped fixing plywood panels so much easier.
Tools were basic: electrical screwdriver, spirit level, saw, bunch of screws, metal threads to fix the construction to the trailer bed. Not much more, really.
Step 8 has a detailed budget.
Step 3: 4. Framework and Outside, Constructing, Failing, Re-constructing
So, most of the process is clearly visible in the attached photos. I have many hours of filmed content as well. Hopefully, one day I'll upload it to youtube.
Some key points:
Structure - I used a structure similar to house building, as this is the only one I had experience with. The whole thing was way too bulky and heavy. Thus, in the second half of construction I had to remove the "double / second" layer of most studs.
- First step - form a wooden rectangle and fix it to the trailer bed. I used threaded rod and two nuts with washers. Drilled a hole in both the wood and the bed's iron side.
- Second step - all walls were made modular, one by one. Thus, the first one to raise was the back wall that will hold the window and ventilator. All corners got an extra iron corner for stiffness.
- Third step - left wall - quite a simple module.
- Fourth step - side wall that will house the door and the galley door. I was trying to fit the pre-cut plywood panels as much as possible.
- Fifth step - Upper/roof studs.
- Sixth step - front wall and the sloping angled roof.
- Seventh step - adding plywood panels.
- Eight step - giant f-up and realising the whole thing is too heave. Removal of 30-40% of wooden frame. You can see the updated structure in the "inside" photo, covered by green tarp.
- Ninth step - adding door, window, weatherproofing.
- Tenth step - adding a coat of arms of Lithuania on the side :D .
Doors and windows were bought at a local plastic windows/doors manufacturer. As the Chinese companies on Alibaba wanted ~1000€ for a single door to be shipped to my location. Kind of overprices imho.
Step 4: 5. Inside and Electricity
So we added some wooden interior to the teardrop trailer.
Added a few boxes inside to put ... stuff.
The walls include 1 inch of insulation and a thin layer of plastic for vapour protection.
I also tried my best to add some ventilation.
4 ceiling LED lights added.
On the bottom, I've added 1 inch pressured insulation.
The mattress is a queen size IKEA (140 m x 200 m.)
Overall inside height of the finished interior is around 130 cms. Very comfy to sit it.
The teardrop has 4 LED lights inside, 1+2 sockets (220V, via extension cord from outside), 1 ventilator and some outside LED lights.
Step 5: 6. Adding Metal Sheet Cover
So, I've seen many teardrops using a sheet of aluminum for the cover.
My challenge was - the roof was to be fully usable, climbable, etc.
There is a layer of tar plastic underneath for waterproofing. Dunno if it was really necessary, but I was scared of leaks after reading quite a few horror stories.
It was not easy, but I found some metalworks people, that were willing to take my € and put formed metal sheets on the teardrop for water protection.
The plywood sides are extended both outwards by some 0.5-1 cm and downwards (compared to trailer bed), thus any rainwater slides away and not inside the construction itself.
Step 6: 7. Roof Rack
Found a decent welding guy, who was able and willing to weld a roof rack for me.
My boys tested their scouting tent on top of the trailer. They absolutely love sleeping at that spot.
It's mainly for the protection of the tent. Tried to carry a bike tied on top, but it's tricky to get it on and off.
Step 7: 8. Budget
The most interesting part. Tried to track all the expenses associated. The prices are in €.
The total cost ended up being 3,300€. (3,900$), the platform included. Yet I fully believe the price could be easily reduced to ~2,500€ (~3,000€), as I purchased some extra tools and quite a bit of unnecessary stuff.
Prices
Trailer and registration
- Trailer-platform, leg holders, locking, 2 belts, 1110
- Registration 7.08
- Tech. inspection 2.3
- Insurance, 1Y 14.09
Key parts, materials, services
- Window and door 425
- Wood 4.5x7 160
- LSFS boards 223
- CNC cutting help 30
- CNC rent 150
- 4x iron legs (zinked) 23.46
- Extra wooden roof support (45x120x4800) 10
- Roof hydro insulation Indextene HDPE Super 105.58
- Roof rack, welding services (logistics + 4 hours of welding) 120
- Roofrack iron 60
- Wooden inside panels 100
- Nightshades for window 75
Other bits and bobs
- TORX screws 10
- Iron corners for harder fix 9.74
- Confirmate drilling rod 7.24
- Polyurethane glue for wood 12.99
- Working gloves 1.09
- Working gloves 2.59
- Red permanent marker 0.69
- Blueprints color printing and lamination for outside use 5.84
- Various TORX screws 57.9
- Cargo holding belts 20.88
- Cargo net 5.53
- Makita electrical screwdriver 89
- Iron corners wide 13.6
- Drill bit 1.11
- White marker 0.69
- Threaded rods x24 12.6
- Washers 2.09
- Nuts 2.39
- Drill feathered 1.59
- Filming tripod 22.99
- Film for painters, thin, for roof protection against water 3.07
- Extra food, round, for roof 3.3
- Metal washers 2.05
- Metal drill 2.9
- 4x LED light 7.96
- Electricity socket 1.95
- Fan 11.89
- Electricity socket 3.49
- Electricity switch 4.45
- Electricity panel 0.77
- Electricity plug 1.25
- Electricity socket 2.12
- El. wiring 5.97
- Screws 1.34
- Screws 12.15
- Rent, circular saw 9
- Screws 4.3
- Insulation foam 6.78
- Metal ventilation grates 2.51
- Plastic wiring holders 2.33
- Metal ventilation grates 3.39
- Brown silicone 7.27
- electricity circuit breaker 3.87
- Wire connectors 2.84
- Acrylic brown paint for plywood edges 8.54
- Weather protective tent, green, 2m x 3m, 2 units 6.78
- Rulers, 3 units 5.67
- Work gloves, 2 pairs 1.58
- Rubber window seals, 3 packs 4.65
- Hot air gun 17.49
- Plastic sheet for internal insulation 10.2
- Safety glasses 1.6
- Nails 0.77
- Jigsaw blades 2.86
- Special insulation tape for windows 24.49
- Electrical circuit breaker box 3.49
- Insulation foam 4.49
- Wiring 5.53
- Nuts and bolts 6.86
- Nuts and bolts 2.01
- Floor insulation mat 3.91
- Paintbrush 1.81
- Wooden panel holders 1.36
- Wooden panel holders 2.44
- Paint, enamel, brown 2.58
- Insulation foam 4.49
- Wooden corner 11.97
- Wooden door trim, 2 sets 45.8
- Paint, wood 10.15
- Wood drill bits 2.9
- Screws 5.49
- Paintbrushed 5.38
- Internal wood paint 19.86
- Enternal paint 10.08
- Wooden corner 7.1
- Various stuff: roof rack plastic plugs, extra paint, etc. 30
- Conrete paving blocks for parking area 36
- Drill for steel 3
- Various bits and bobs 4
Step 8: 9. Camping Out
Few photos of the rig in action. We've also purchased and extra tent to expand the livable area, as sometimes the summer are a bit wet here.
For now, the rig easily accomodates 4-5 people (2 + smallest kiddo) inside and 2 boys on top). The oldest boy (14yo) prefers to sleep in a hammock outside or in a side tent, being a scout and all ;)
Overall it tows well, easy to set-up, level and use.
Step 9: 10. Advice, Tips, Tricks, Etc.
My inspiration:
- Pinterest saves on box shaped teardrop trailers: https://www.pinterest.com/kmorkunas/teardrops-box...
- camper van interiors: https://www.pinterest.com/kmorkunas/teardrops-box...
- more interiors, kitchens, etc. https://www.pinterest.com/kmorkunas/teardrops-box...
- Instructables on teardrop trailers: https://www.instructables.com/outside/howto/campe...
The good, the bad, the ugly
- Galley/kitchen looks nice in photos. For me - completely useless. Will switch to independent box type camp kitchen.
- I've tried to add the most silent ventilator I could find (22db), but is still too loud at night. Thus, we usually sleep with the doors slightly open.
- Four corner "legs" really help with stability and noise reduction.
- Yes, that's a geocaching travelbug sticker on the side ;)
What's next?
- I'm thinking of removing the side door and the galley completely and doing just one liftable side door out of plywood. For me, it's much more practical and fast when there is a bit of camp equipment to load up and transport.
- Also thinking about moving the back wall "inside" by around 40 cms and creating a platform to store/transport the bikes.
- 100+ hours of constructional video content will (one day) end up on youtube.
Feel free to ask/comment/discuss. I'll try to participate as much as I can.
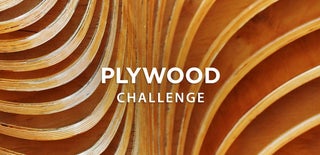
First Prize in the
Plywood Challenge