Introduction: Teardrop Camper Made From Wood
I built this teardrop by closely following and inspired by the Instructable called Teardrop Trailer by e1ioan.
I didn't use any plans, just had a design in mind and researched as I went along.
Initially, I wanted to do this project as a group because I was not entirely confident I could pull this off alone, so I started a Meetup Group on Meetup.com called Lawrence Teardrop Camper Build and to my surprise, over 75 people signed up. But only one person showed up, Carlos. Every Saturday morning, Carlos would come over and help me. We worked in my garage. He was there for the duration of the build. I would work on the teardrop in the evenings after work, and on Saturday Carlos would come over and I would have 100 questions for him. He knew a lot, had a lot of great ideas and suggestions, and helped me extensively with running the electrical wires, the fan installation, and the stargazer window installation. Shout out to Carlos, wherever you are!
Step 1: Buy a Trailer and Assemble It
I bought my trailer from Harbor Freight in August 2017. It's rated to carry 1195 lbs and it's a 4' X 8' trailer. It was a steal at $299.99. However, I have since learned that Harbor Freight does not sell trailers anymore. It's a Chinese product (as are a lot of HF products) and the reviews I read were mostly positive, but for whatever reason, HF stopped selling them. [Update: HF started selling the trailers again for $349. YAY] The light kit that came with the trailer had to be replaced later, but overall, I was thrilled to get a trailer for $300. If I had known they were going to discontinue this item, I would have bought a few more.
I went to the HF store in Topeka, KS to buy the trailer. It comes in a few boxes, and it comes with a title. It's a little chore to haul it home and put it together. I had never put a trailer together before. I just laid everything out in the garage and read the instructions over and over and over. Take it slow. The instructions were excellent, and as long as you follow along and pay attention to detail, everything should go together well. Getting it square was another challenge, but eventually, I got it square.
I chose to register my trailer and get a license plate. I was told that plating it was optional in Kansas, but I did it anyway, since I knew I would be traveling out of state and didn't want to take any chances.
Step 2: Build the Deck
Once your trailer is assembled, you'll want to build the deck...the foundation of your teardrop home. That is done by going to your local Home Depot or Lowe's and buying a 4' X 8' piece of 3/4" plywood. You want your foundation to be very strong, so be sure to get 3/4" plywood.
I rented a Home Depot truck to haul my plywood. The HD guys will help you load up the truck. Less than $30, if you live close to the store.
Before laying down the plywood, you need a frame to set it on. I bought 2 X 4's and ripped them in half on my table saw. They fit perfectly on the trailer. I screwed the corners together, as well as the middle pieces, then bolted it to the trailer. There are pre-drilled holes in the trailer, but sometimes I wanted more holes to screw into, so I made my own using my hammer drill and a metal drill bit.
Once the framing is all in place, lay down your 4 X 8 plywood and bolt that into the frame. I used 5 1/2" hex bolts. I may have trimmed the plywood a bit. After it was all tightly secure on the frame, I slapped several coats of spar urethane on the top to make it pretty.
Now, you are ready to start building the body of the teardrop!
Step 3: Design !!!!!!!!!
Go online and find a teardrop design that you like. I spent many, many evenings scouring the internet for the perfect teardrop shape that made me squeal with delight. When I found the picture above I knew this was it, and I tried to create the exact same shape. l then practiced drawing it freehand on a piece of paper. This was a very important part of the process. I felt that in order to really get the shape I wanted, I had to know how to draw it.
Step 4: Create Your Side Pieces
I purchased 2 pieces of 1/2" birch plywood 4' X 8'. I chose birch because these would be the outside walls of my teardrop, and birch has a nice finish. I found out the hard way that there's a good side and a bad side of birch plywood. The good side should be showing. The bad side will be inside and covered with framing and insulation.
I laid my piece of birch plywood good side up and used a long piece of bendable plastic trim to outline the shape I wanted. I used little tiny nails to hold it in place to get my shape. Once I had the teardrop shape I wanted, and this was no easy task, I used a sharpie that I ran along the outside of the plastic trim. I then removed the trim and tiny nails, and used a jigsaw to cut out my shape. After cutting with a jigsaw, I had to do a ton of sanding to get it close to perfect. Once I had it nearly perfect, I used this as my template to create the other identical side.
As you can see, I placed my side pieces as far back as they would go on the foundation, leaving ample space in the front to build a box to hold the battery. This teardrop will run on solar power and all the wiring will connect to a little panel that's connected to a 12 Volt deep cycle marine battery.
Step 5: Attach Your Side Pieces to Your Foundation
Attach your side pieces to your frame. The frame of the deck is basically half of a 2 X 4, so you've got 1 1/2" of meat to bolt into to hold up your side pieces.
I cut a couple 2 X 4 scraps to exactly the height I wanted and rested the side piece on top of the 2 X 4 scraps, as seen in the picture. This was challenging, as I was working alone, so I had to maneuver the heavy side so that it wouldn't fall over while I bolted it in. I used hex bolts, long enough to go through the birch plywood and the 1 1/2" deck framing. I used between 6 and 8 on each side.
As you can see from the pictures, I placed my side pieces towards the back of the trailer deck, leaving ample space in front to frame in a battery box. The teardrop electrical runs on solar power, and the energy from the solar power is stored in a 12 Volt deep cycle marine battery, which cost $377.28, which was way overkill, and I regret that.
Step 6: Purchases and Prices
Most of my purchases were on Amazon, so I've provided the complete product description copied and pasted from my Amazon purchase history.
Lensun 20W 12V Semi-Flexible Monocrystalline Solar Panel Kit with 10A PWM Solar Charge Controller and Two 5m Cables with MC4 Connetors for 12V Charge Battery for $119.99.
BESTEK 400W Power Inverter DC 12V to AC 110V Car Adapter with 5A 4 USB Charging Ports which is mounted inside the teardrop and is used for recharging my computer or phone while camping for $39.98. It's fun to watch Netflix in the teardrop at night while camping, so this little adapter is well worth the price. It converts battery power DC to AC, and is a lifesaver if you're not at a campground that has power.
Blue Sea 5025 ST Blade Fuse Block w/Cover - 6 Circuit w/Negative Bus consumer electronics for $44.41
acegoo RV Boat Recessed Ceiling Light 4 Pack Super Slim LED Panel Light DC 12V 3W Full Aluminum Downlights, Warm White (Silver) $32.99
2 of JR Products 12245 Black Triple SPST On-Off Switch with Bezel - the marine grade lightswitches inside the teardrop for $17.56.
My doors were Vintage Technologies WD24 RV Teardrop Passenger Side Black Insulated Foam Core Trailer Door 26" x 36" at $361.95 each, although I really only needed 1 door, but 2 looks nice too.
40 Ft X 1" Butyl Sealant Tape for sealing the doors.
I also have a Fan-tastic Vent fan, which are pretty standard teardrop fans and can easily be found online. I had a hard time installing it because the top of my teardrop is slightly rounded and caused some headaches.
I used Minwax Ipswich pine stain on the exterior birch plywood, as well as multiple coats of spar urethane with a gloss finish.
UPDATE: After the trailer was done, I took it to Eagle Trailer Company, a local trailer manufacturer. I was not super confident of its road-worthiness. I asked if they could reinforce it somehow, and they ended up welding a metal bar t-shaped the length of the trailer. Picture is above. It goes from the back, all the way to the tongue. That made me feel a lot better. They also suggested maybe upgrading to the next size tire in the future.
And finally, a 45" X 9" stargazer window, purchased from Frank Bear's RV & Teardrop Supplies in Union City, Michigan, for $176.70. That was a nightmare to install, and Carlos helped a lot with that. On my first trip to Arkansas camping, it rained and a leak developed in the well of the window. I have since sealed the leak. I haven't gazed at any stars yet, and the jury's still out on whether it's worth it to have a window over your head while sleeping.
Step 7: Insulation, Electrical, and More
I used styrofoam insulation and glued it to the side pieces. It was 3/4" thick. Not sure how much it will keep me warm, but it's filler material, something to fill the empty space between the exterior wall and the interior wall.
I can't go into a lot of detail about the electrical because I built this teardrop a year ago, my friend Carlos helped me on Saturday mornings and guided me a lot on the wiring, and I don't think I could provide detailed instructions. I did a ton of research online to sort of try to understand the whole concept, and I got a lot of help and guidance from a local Napa auto parts guy, where I bought my little fuses and some of the wiring. Basically, the wiring runs from the lights to the light switch, then along the top of the teardrop to the Blue Sea panel. And from the fan, to the light switch, then along the top of the teardrop to the Blue Sea panel. Keeping the wires straight was a real challenge, trying to remember what wire went where. The fan uses a 20 amp fuse, and the lights use a 5 amp fuse. I have 1 interior light and an exterior "porch" light on the right side of the teardrop, and I have 1 interior light, an exterior "porch" light, and the fan on the left side of the teardrop. I have 6 light switches in total, and only 5 are actually used.
Step 8: Create a Frame Around Your Side Pieces
You'll need a frame around the side pieces so that you have space for your insulation. Also, you'll need framing around your door. I glued my framing pieces around the inside of the side pieces using 4" pine. I used a jigsaw to round the corners. It doesn't have to be perfect. As you can see from the pictures, I cut my pine pieces to fit around the edges of the side pieces. Then I glued them and clamped them to dry. The frame is needed to have a way to hold the insulation in and to support the door, and also it is needed so that your interior wall has something to attach to. Once you have attached your framing, using glue and screws, it's time to glue in your insulation (I used styrofoam) and attach your interior walls, or "skin." The skin was 1/4" birch plywood.
Step 9: Bendable Plywood, Spars, and Battery Box
As of this writing, it was exactly a year ago that I built this teardrop, so I can't quite remember what I used for spars to join the sides of the teardrop. I think I bought 2 X 2's. Connecting the spars to the sides of the teardrop was challenging. On the one hand, I didn't want to ruin the perfect look of the exterior of the teardrop, but on the other hand, I needed to screw the spars in really well. I tried to countersink the screws, but some of them wouldn't go in far enough. Bottom line, the exterior of my teardrop looks a bit unprofessional. The spars have to be really solidly installed, because they are going to take a lot of pressure when the interior luan (thin, bendable plywood) is installed. I placed the spars at even intervals until I got up to where my Fan-tastic Vent Fan was going, and then measured carefully and placed the spars so that they would frame the fan. Very close to the fan, I also had to be careful to measure for the Stargazer window.
After the spars are installed, and all necessary fan framing and stargazer window framing is done, the luan needs to be installed in the interior. Luan is super thin plywood that can be purchased in 4' X 8' sheets. Fortunately, my local HD has lots of it in stock, but I've heard it can be hard to find. Luan bends easily in 1 direction, and that happens to be the direction that produces the most waste for my project, so when all was said and done, I had purchased about 8 sheets and wasted a bunch of it. It's thin and flexible, and really hard to cut accurately on a table saw. It flops around like a dying fish as it falls off the end of the table saw, and doesn't want to stay still against the fence. Ugh! Total PITA. Once cut, I had to squeeze it in through the slats, then climb into the inside of the teardrop and basically push it into shape against the slats. Once I got it in place, I realized I had cut it just a bit too narrow, so I had to pull it out and cut another piece. The next piece was too wide. It was very frustrating trying to measure it accurately and get it in place. Luan is great, but I hate it while loving it. Finally after 3 tries, I got the measurement right. The back of my teardrop is sharply curved, and getting the luan into place, hoping it wouldn't crack from the pressure, was really, really, really difficult. Lots of swearing, lots of sweating, but finally it went in. Remember that I mentioned that luan bends easily in 1 direction? Well, the piece I put in was bent in the opposite direction, because at the time I didn't realize it bent easily in 1 direction. So it's a small miracle that I was able to get that piece in without it cracking.
Side note about seams: where there were seams on the exterior, I used bondo. Just use blue painter's tape about an inch from the seam on each side, apply bondo, remove the tape while the bondo is still wet, and wait. It dries as hard as a rock, can be sanded (use a respirator and eye protection), and can be stained easily, and it looks very nice. Where there were seams on the interior, I just glued a thin piece of trim that I made out of scrap wood, and held it in place with a couple pieces of 2 X 4 wedged against the floor until it dried.
While installing the luan, I also started making a battery box. This protects my battery from the elements. My father helped me make a simple hinged lid for it, and I was pretty happy with the way that came out. Not thrilled, but it serves the purpose. If I could do it over again, I would make the battery box a little bigger and spend more time on the design. I drilled 2" holes in each side of the battery box and purchased Vintage Technologies TA19 RV Teardrop Trailer Camper 2" Floor Vent 2 PACK. Apparently batteries need air (who knew?) so this provides some ventilation.
The solar panel lays flat against the outside of the teardrop, has wires running down through holes in the battery box to the charge controller, which connects to the battery.
As for the solar panel itself, I read that some people glue their solar panel to the teardrop, but it's really not as flexible as you'd think, and I didn't trust that I could find glue that would hold it down well, so I connected it with tiny bungee cords. I enjoy creating my own inventions and coming up with solutions, even though they are usually stupid. The little bungee cords work fine. At the top, they are connected to 2 little (glued on) hooks, like you would use in a kitchen to hold keys. It's simple and it works, even going 70 mph on the highway.
Once the interior luan was installed completely, I started putting the styrofoam insulation in the exterior spaces between the spars and the interior luan. Very simple, but you must use a special kind of glue that won't melt the styrofoam, Loctite PL 300 Foamboard Adhesive.
Step 10: Battery Box Update
4/28/19 The battery box I built out of plywood rotted after 1 year exposed to a Kansas winter. Even with a custom waterproof teardrop cover, moisture got in.
So, I wheeled it into the garage for repairs. I was pretty sad for a week. But then I came up with a great idea. I would create a battery box using pine, and then use stained and polyurethaned cedar on the outside of the pine. No Kansas winter was going to penetrate this battery box.
Pictures will be added very soon.
Step 11: Exterior Luan Installation
This was probably the most rewarding part of the project, because once that exterior luan is glued on and stained and polyurethaned, wow, it starts to really look like a teardrop! It was easier than I expected. I bought 2 ratchet straps, measured my luan to overlap the sides, as shown in picture 1, and put super heavy construction glue on the slats, and ratcheted the luan down with all the strength I had, and let it sit for a day.
Then the challenge of trimming that overlap. I had to read a lot about how to do this, as I had never used a router before. I ended up buying a Makita trim router, light enough for me to handle, but powerful enough to get the job done. I had no clue what kind of bit to buy, and after a lot of trial and error and wasted money, I found the right one. It worked like a charm. Very messy, must use eye protection and a face mask, but very rewarding and I was so impressed with this tool.
Then I purchased the aluminum trim, and that just nails in easily. As an extra precaution, I ran a bead of silicone under it before nailing it in, just to make sure it didn't fly off while I was driving.
Step 12: Doors
Everyone in the world said I needed 2 doors, but really? My husband wants to go camping with me about as much as he wants to learn how to knit. Not much. So why did I buy 2 doors? Because everyone said I needed 2 doors. You only need 2 doors to avoid crawling over the other person in the middle of the night when you have to go to the bathroom.
I purchased my 2! doors on Amazon from Vintage Technologies. They are 26" X 36" and came with really great instructions. They cost $361.95 each. I followed the directions, measured twice, and cut once, and it was surprisingly easy. I purchased butyl tape separately, which is used as a gasket to seal the door in place. No water has ever leaked in except when I left the door window open while driving in the rain.
The doors have windows and screens, which works perfectly with the Fan-tastic Vent Fan. While camping, I opened the door window a bit, turned on my fan, and the two worked together to create wonderful cool air flow and kept me comfortable all night. Don't ask me how the bugs got in, though. I have no idea. They loved my computer screen and we watched a movie together.
Step 13: Interior !
I wanted to show my finished teardrop to my sister, who was visiting. The first thing she asked was, "where's the kitchen?"
There's no kitchen ! My teardrop is simple. It's a place to sleep, an alternative to tent camping, provides shelter, light, and a fan.
For the interior, I purchased a custom futom from customfutons.net. I also purchased a custom futon cover. It was $578, and I know that seems expensive for my little teardrop, but it fit perfectly and is so darn comfy. Andy at customfutons.net has made a couple of these for me, and he does great work. It fit perfectly! My first night camping in Bull Shoals, Arkansas, I slept through the night, got about 9 hours of sleep.
Those light switches are so cute! And check out the stargazer window!
Step 14: Costs
Step 13. Isn't 13 an unlucky number?
$ xxxx.xx
I'm an accountant. I saved every receipt. I can't bring myself to add it all up. Let's just say it was unreasonably expensive. This includes the bondo, bungee cords, c-clamps, custom futon, Fan-tastic Fan, gorilla glue, hex bolts, hitch labor, Home Depot truck rental, jack stands, respirators, shelf brackets, stain, Stargazer window (which is super sexy), the trailer hitch installation (U-Haul), the trailer, trailer tags, urethane, wood filler, and loads of wood. So much wood.
It all adds up !
Plus, while at Lowe's one day, I felt I deserved a new DeWalt portable table saw because my old table saw wanted to retire. And a new DeWalt miter saw...because our kitten was turning 1.
And life is short.
Go camping, build a fire, and have fun !
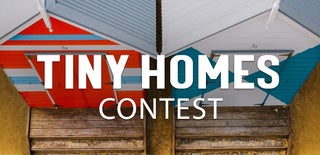
Second Prize in the
Tiny Home Contest