Introduction: TetraEden
"...design a plant growth chamber for use in space that makes effective and inventive use of the available volume on the space craft while also incorporating the necessary features for plant growth."
Fairchild Garden’s Growing Beyond Earth Contest Description
We found that this mission statement could be interpreted as two different design goals: to maximize either plant density in a given volume or the packing efficiency of the plants’ container. We initially prioritized the packing efficiency of the container, but as our project continued, our design was able to meet both criteria.
When we decided on the plants’ container-shape, there were a few factors that we considered: the shape’s internal surface-area to volume ratio, ability to tessellate, packing efficiency (regular versus irregular), and how flush the container’s surfaces would be to the surrounding walls.
The more surface area within a container, the more space there is to grow plants. That’s why the internal surface-area to volume ratio is so important - the more surface area contained within a container, the more plants that can be grown in a given volume.
Tessellation is also important. The ability to tessellate, or tile, is the ability for a group of identical containers to pack together with no empty space between them. This can be an ideal quality for a container given a certain room shape (i.e. choosing a cuboid container for a cuboid room might allow the containers to perfectly fill it).
Packing efficiency is the percentage of volume a container or multiple containers take up in a room. This factor is arguably the most important, as it can indicate the more efficient container shape when multiple containers are used to fill the room. For example, a container shape with a low volume might be able to fill a space in a way that creates a greater total surface area than shapes with a larger volume. Unfortunately, packing efficiency can be very difficult to measure, due to the various, possibly infinite, number of container arrangements in a given space. In computer science, this type of problem is considered an “NP-Complete” problem, meaning that one can only attempt to find a maximal or “best” solution through trial-and-error. In certain room shapes, one can avoid this, but for random room shapes this can be very difficult to decide.
Flushness, or how level a container’s surface is to the rooms’ walls, is a minor factor closely related to packing efficiency. However, it is a simpler, and arguably better, indicator of efficiency; especially when trying to determine the packing efficiency of a container given an irregular room-shape. Container shapes that tessellate may lose their packing advantage in irregularly shaped rooms; the more irregular the surface of the room is, the less efficiently tessellating containers can pack.
Current plant growing containers aboard the ISS are cuboid in shape. With this in mind, we examined a variety of container shapes. It was important to us that the container have as few parts as possible; although the ISS and future spacecraft may have the ability to replace parts in space, reuse or refurbishing of existing pieces would be more economical. Designs already submitted for this competition show unique containers separate of the parts designated for plant growth. This was something we wanted to avoid, as a great amount of surface area was left unused. In order to accomplish this, we decided that our container would be composed of separate polygonal panels, each having a majority of their surface area designated for plant growth. These panels would then be arranged so that they would enclose the space necessary to make the container. In this way, the parts designated for plant growth would no longer be housed within a container- instead, they would become the container!
If the panels were to be arranged in such a way, we wanted the joins of the panels to be flexible, so that the panels could be unfolded for harvesting. This coincidently allowed the container to “bend”; giving the container the some ability to fit on irregular surfaces and corners. However, this leeway depended on the shape of the container that the panels would form. In following with our decision to minimize the number of parts, we had decided the panels should be identically and regularly shaped, limiting the container’s shape to the platonic solids. After having chosen the shape of the container, we would specify the design of our panels. Below is our analysis of each platonic solid in list form:
Spheres
Surface Area to Volume Ratio: Lowest.
Spheres have the lowest surface area for a given volume of any shape (but the highest volume).
Packing Efficiency: Lowest.
Spheres have no flush surfaces, so regardless of the arrangement, when many are placed side by side, a great amount of space is left unused.
Flushness efficiency: Lowest.
Despite the few points of a sphere that can touch a surface, spheres leave the most unused space of any shape and fit worst against corners.
Dodecahedrons, Icosahedrons
SA to V ratio: Intermediate.
The many-faced platonic solids make better container shapes when compared to spheres, but in themselves lack any defining features in which to be considered.
Packing Efficiency: Intermediate.
Having flush faces makes these structures better able to pack than spheres, especially irregular dodecahedrons, but their sphere-like shape leaves them with similar unused space.
Flushness efficiency: Low.
These shapes can be made flush against obtusely angled corners, but are still inefficient in regularly shaped rooms.
Cubes
SA to V ratio: High.
Cubes have the 3rd highest surface area for a given volume compared to the other examined shapes.
Packing efficiency: Low (without tessellation).
Cubes are composed of 90 degree angles, which tessellate extremely efficiently in rectangular rooms- the predominant shape of rooms on the ISS. However, because our design allows plants to only use the space they need, the accommodating faces will inevitably separate at different rates, creating a rectangular prism that won’t pack ideally in a cubed room.
Flushness: Low (without tessellation).
Cubes can lay flush against right and obtusely angled corners. However, a cube that is too densely packed will not have room for its faces to maneuver against irregular surfaces and corners. This is specifically due to the cubes’ tendency to tessellate. Tessellation allows for maximal packing, but leaves little room for the container to bend against varied corners.
Octahedrons
SA to V ratio: High.
Octahedrons have a good surface area to volume ratio. However, there are shapes with a higher surface area to volume ratio that are worth considering.
Packing efficiency: High.
Octahedrons can pack very densely together. However, the square rim around the middle of the solid does not allow it to pack in as densely as Tetrahedrons.
Flushness: High.
Having both of right and acute angles allows for great adaptability to a variety of irregular surfaces. That said, having right angles limits the amount of arrangements that fit multiple containers against acutely angled corners.
Tetrahedrons and triangular bipyramids (an arrangement of tetrahedrons)
SA to V ratio: Highest.
Tetrahedrons have the highest surface area to volume ratio of the platonic solids.
Packing efficiency: Highest (regular vs irregular).
Tetrahedrons have the highest packing efficiency. Experimentally, they have the highest random packing efficiency when compared to other shapes. An arrangement of tetrahedrons – called “triangular bipyramids”, in which two tetrahedrons are joined face-to-face, can be additionally arranged to have the densest packing of any shape yet known. The appearance of the triangular bipyramid is almost identical to that of the octahedron; however, the triangular bipyramid has internal faces while the octahedron does not. It is for this reason that the octahedron can’t achieve the highest packing efficiency – it does not have a large enough surface area to volume ratio.
Having examined the aforementioned shapes, we concluded that the tetrahedron would be the most suitable container shape. Its theoretically and experimentally high packing efficiency, it’s simplicity of construction, and its ability to handle irregular room shapes made it a clear winner. Theoretical advantages aside, we choose not to pursue the triangular bipyramid arrangement due to time constraints, although our design could readily accommodate such.
Flushness: Highest.
All angles that a tetrahedron, or a triangular bipyramid, possess are acute, making it able to fit into very tight corners and press densely against irregular surfaces!
Worthy Mentions
It should be noted that we also chose to not pursue an additional design feature due to time constraints: gradually growing containers! Currently, ISS plant-growing containers are designed with their plants growing on some lower surface with a light source placed above them. These containers have varying amounts of unused space between the plant and the light; to make room for future plant growth. To minimize this unused space, we wanted the plants to only use the space they needed by having the container panels slowly push apart as the plants’ height increased. This would have allowed the container to accommodate the height of the plants throughout their various stages of growth.
Step 1: Producing the Components
In this prototype, each panel’s base is composed of ¼ inch thick acrylic, cut into equilateral triangles with 26.5 cm dimensions. We modeled the panel bases and other parts in the open-source vector graphics software “Inkscape”. We then imported the schematic into the “RDWorks” software application before uploading it to the laser cutter for fabrication.
Step 2: Outer Borders
After all parts were cut, we first glued the outer border-walls against the rim of the panel bases, yielding a ½ cm tall outer border around the triangle.
Step 3: Inner Borders
The inner border-walls were then glued on top of the panel-bases in the shape of a triangle, 0.825 cm from the outer border, forming a second, smaller triangle at the center with a 23 cm length. This creates a trench around the triangle wide enough to lower an LED strip into it at a 60 degree angle, allowing light to be cast onto adjacent panels.
Step 4: Tubing
1/4 inch thick plastic tubes were cut into six, 5 cm long pieces. They were to be wedged through identically drilled holes on the outer and inner panel-walls. These would have allowed water to feed into the inner panel cavity; however, due to time constraints, we were unable to complete this step.
Step 5: Plants and Hydroponics
Burlap pieces were cut into the triangular shape of each panel cavity and glued on top of them. We had planned for nutrients to flow through the plastic tubes linking each side of the panels; the cohesive and adhesive properties of water would draw the water beneath across the entire piece of burlap; initiating the growth of the microgreens. This effect would be more obvious in space, where water droplets can bounce and float their way to the burlap; the panel’s hydrophobic surface causing water droplets to remain anywhere except the panal cavity surface, ensuring the water is absorbed by the burlap. The adhesive property of water also secures tiny seeds to the surface of the burlap – in our case, microgreens, without other securing bonds. Simply spraying water onto the burlap and sprinkling microgreen seeds on top would create a ready-to-grow surface that can be immediately attached to a panel.
Step 6: Cutaway Schematic for Each Panel
A
Thickness of panel base/ borders- .25 in (.635 cm).
B
Panel dimensions- 26.5 cm.
C
Height of inner border/ outer border above panel base - .5 cm.
D
Total outer border height- .726 cm.
E
Distance between inner and outer borders- .826 cm.
F
Panel cavity dimensions- 23 cm.
Step 7: References
Step 8: Special Thanks to All That Made This Project Possible!
Mason Innovation Exchange (MIX) at George Mason University
Staff
Kathy McCabe: Supplied components and contributed to design.
Amanda Jarvis: Supplied components and contributed to design.
Nova Labs Makerspace (Reston, Virginia)
Kathy McCabe: Technician
Step 9: A Final Note From the Team...
The pictures showing flourishing micro greens on the panels are modified images of our prototype to show the ideal vision of our design.
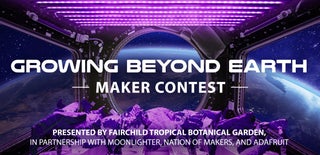
Second Prize in the
Growing Beyond Earth Maker Contest