Introduction: The $45 Drill Press Cart - Intro
I have a very small shop. I wanted to put my drill press in the shop. I did not want to take up space on my workbench and I didn't want to stuff it in the corner where the walls would get in the way when I worked on larger pieces. The solution was a cart, but there is a reason why drill presses are not sold with wheels on them.
The Problem
A drill presses is very top heavy. It needs a stable base. If the floor is not completely flat, it is fairly easy for the center of gravity (cg) to shift outside of the area enclosed by lines connecting the contact points between the base and the floor while moving the base. When that happens, the drill press tips. Even if the cg doesn't cross the line, a drill press being moved on wheels has momentum. When a wheel hits an obstacle, the bottom of the cart stops moving, but the momentum continues to push the cg. Because the cg is high, there is a lot of mechanical advantage so even a little momentum can cause a tip.
The solution is to space the contact points as far apart as possible and to lower the cg as much as possible. There is a limit to how wide and deep you can make a drill press base since you need to be able to easily reach the press handle. Likewise, there is a limit to how low you can Lower the heaviest part of the press.
Step 1: The $45 Drill Press Cart - the Base
The solution
The solution, is to use a small drill press on a small cart and add weight to the bottom of the cart. While I could have made a complete cart from scratch, I decided to save some time and start with a low workstation table that is sold by Harbor Freight. The US General Adjustable Height Heavy-Duty Workstation is a small table designed to hold small shop tools. It has a steel frame and a dense particleboard top. What it does not have is wheels. My plan was to add wheels to the workstation, but I did not want to increase the height any more than necessary.
To attach the wheels, I planned to use two pieces of “one by” lumber. I wanted to attach the lumber to the bottom of the lower shelf. However, the length of the steel sport legs below the lower shell would interfere with the swiveling of the wheels. While I could have left the legs their full-length,and put the wheels in board further, or put them on “two by” instead of “one by” lumber, each of these solutions cause a problem. If I move the wheels in further, the contact points of the cart would be closer together. This would make it less stable. It would also make it hard to engage the locking lever on the caster wheels. If I use the thicker pieces of wood to attach the caster wheels, the cart would be higher. That also would make the cart less stable. The solution was to cut the support legs off about three quarters of an inch below the bottom shelf. While this only took about an inch and a half off of the legs, it was enough to allow the casters to turn freely when they are close to the edges of the cart. After shortening the legs, I assembled the rest the stand per the instructions that came with it.
Step 2: The $45 Drill Press Cart - the Wheels
For the wheels, I chose 4 inch locking cast-iron casters sold by Rockler. There are several important traits to these wheels. First, the wheels have a fairly large diameter. This will make it easier to move the cart over uneven surfaces and minor shop debris. Second, the wheels are locking. This will make the cart more stable when I am using the press. Third, the wheels are very heavy. This will help lower the center gravity of the cart. Finally, the wheels were very inexpensive. In fact, these were the lowest cost wheels of this diameter that I found on any websites or in the local hardware stores.
Flipping the stand over a I measured and cut two pieces of one by eight lumber to just fit between the legs. I wanted to place the wheels as close as possible to the edges of the cart. However, I wanted to make sure that the bolts going through to hold the wheels in place would not interfere with attaching the base to the rest of the cart. Since the lumber was going to be attached to the steel frame of the lower shelf using wood screws I place the wheels that they were just inside the thickness of the steel base for the lower shelf. I marked these edges and used transfer punch to Mark the center of each of the holes I then drill the holes attach the casters using flathead machine screws countersunk into the top side of the wood and nuts and washers from the bottom. I then attach the boards, with the casters on them to the bottom of the cart using wood screws through the steel frame of the bottom shelf. Not only did the wood screws go through the steel frame, but they also went through the particleboard that makes the bottom shelf. This made the bottom shelf more stable. However it did result in their being tiny points from the screws sticking up in the bottom shelf. I rounded these off using a Dremmel.
Step 3: The $45 Drill Press Cart - the Result
I placed a drill press on top of the cart and position it so that the front of the press was on one of the narrow faces of the cart. This put the heaviest part of the drill press, the motor and support column, very close to the center of the cart. Since there is still room on the back half of the cart, I put small belt Sander there. Both the sander and the drill press have mounting holes so that they can be bolted onto a shelf. Even without the tools bolted to the top of the cart, I found that they are quite stable for the small uneven areas cart has to cross in my shop. However, long-term it will make more sense to bolt these down "just in case".
On the bottom shelf, I added various pieces of wood and other material that was laying around shop. If I find the need to make center gravity lower, I can take these pieces out and instead put in paving stones such as are commonly available at Walmart, or home-improvement stores. Another alternative would be to seal the area where the bottom shelf meets the steel frame using tape or caulk and then fill the bottom shelf with gravel and QuikCreete.
As built, I spent $45: $25 for the base form Harbor Freight and $5 each for the casters from Rockler. If you don't have extra wood, screws, nuts, washers, and bolts lying around your shop, repeating this project might cost you $50 to $55.
With how easy it is to position the cart, I find that I pull it out for some quick task every day that I am in the shop. The four inch wheels have no problem going over the edges of the cardboard I have covering most of the shop floor. The back to back placement of the drill press and the sander keeps each from interfering with work being done on the other. There is no noticeable flexing of the cart when moving or using the tools. When I am done with the task, I simply unplug the tool and roll the cart back into the corner.
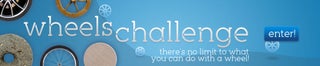
Participated in the
Wheels Challenge