Introduction: The Chopping Machine
Have you ever felt too lazy to prepare your own meal? Or have you ever not wanted to do the manual labor it takes to make yourself food?
Even if you answered no to those questions you still may need the Chopping Machine in your life. Let this beast take care of your cutting needs and never lift a knife again!
In this Instructable I will show you how to make your very own Chopping Machine!
This idea was conceived with the aim to create an object that does something for the user that the user does not need done for them. Bringing to light the automation of things in today's society, where skill and professionalism is replaced by technology.
To be noted: this instructable illustrates the path I took to make my final prototype, it is not at a complete stage yet. There is one issue I had with the my design and I will address a solution when it comes up. The final product I intend to be wood and sheet metal instead of cardboard, with a cover for the motor. My vision for such a design is show up top.
Step 1: Things You Will Need:
Materials:
1 Cleaver, preferably with a partial tang (Ikea is a good source)
1 Cutting board (Ikea is also a good source)
1 24v DC motor with high torque capabilities
1 On/off switch
A power supply (do not get a power supply that has a higher output voltage than your motor)
1 Female jack for the power supply (make sure it fits, there is more than one size)
1/2 inch steel rod
1/2 inch dowel
Wires
Heat Shrink
Cardboard (larger than your cutting board and flat)
Carrot
Tools:
Electric drill with a variety of drill bits
Exacto knife with extra blades
Cutting mat (large is convenient)
Hot glue (lots of it)
Metal ruler
Pencil and eraser
Soldering iron, solder, steel wool
Multimeter (Volt-Ohm-Milliammeter)
Combination square
Screwdriver
Hacksaw
File
Step 2: The Concept
The Chopping Machine works by a snail shell shaped cam rotating by a motor. A peg extends out of the handle of the knife and rests on the edge of the cam. The knife pivots at the butt by a peg attached to the base of the contraption. As the cam rotates, the knife is raised, and after the peg reaches the "cliff" of the cam, the knife is dropped.
The cam shape can be described as a circle that gets bigger gradually, then suddenly smaller.
My inspiration for this system can be found here:
https://www.instructables.com/id/Linear-Motion-by-C...
I made an initial prototype to test the concept, with a cardboard knife and a single cam.
In my final prototype, I switched from a single cam to dual cams. Having only one cam caused the knife to twist on its pivot point, making it difficult to move the knife upwards. Having two cams providing upward force on both sides of the knife eliminated this issue.
I also moved the motor from the left side to the right, to give more space for the left hand to feed things under the knife. This is a personal preference, you can place your motor on any side you like!
Step 3: Drill Holes Into Knife
Choosing a knife
Since the choice of knife for this machine is based on weight, most dollar store kitchen knives are too light to give the knife enough cutting power. A cleaver design is generally your best bet, as it requires lots of metal to form the blade.
I bought a cleaver from Ikea for about $30 - a little steep for a knife we wish to drill holes in, but acceptable. At least it's not a $200 knife. The blade has a nice heft to it, and is very sharp, but the handle is a round shape with a rubber over molding. Not very easy to drill cleanly.
Two holes need to be drilled into the handle of the knife: one through the butt, and one through somewhere in the middle.
The good thing about cheaper knives is they tend not have metal all throughout their handle. If there was metal where you wanted to drill, chances are you would need a cobalt drill bit to get through. They can be had for around $10 each.
Drilling the holes
Clamp the knife securely in a vice before drilling.
Drill the pivot axis hole as close to the end of the handle as possible, in order to achieve the most leverage for the cam. Make the hole at least one drill bit size larger than the 1/4" peg which the knife will pivot on.
The hole for the rod that will ride on top of the cam, I will call the cam pin hole. If you put the hole farther away from the pivot point, the knife will be easier to lift, but the cam will need to be bigger to achieve the correct height. The cam may have to be so big that it interferes with the cutting board. Drill the cam pin hole somewhere in the middle of the handle. Stay away from the back of the handle because the blade is most likely to be close the back of the handle.
In an image above you can see I have the cam pin hole very close to the edge, and a little bit behind the middle of the handle. I managed to stay away from the tang of the knife for both drill holes with this positioning.
Step 4: Make Your Base
Sizing the base
Measure the width and length of your cutting board. Take the length of your cutting board, and add on the length of the handle of your knife. Then add roughly 2 inches. This will give you plenty of room to place your motor and knife mechanism, as well as your switch. You can keep the width of the base the same width as your cutting board. When marking your cardboard, a combination square finds itself useful in making consistent and fast 90degree angles.
Cutting and assembling the base
Cut out 4 sheets of this dimension, 2 with the opposite grain of corrugation. This will add structural integrity to your base. When cutting cardboard, be sure to use a metal ruler to keep your cuts straight. To achieve a clean cut, take your time and do several light passes until you cut into the cutting mat.
Hot glue the sheets together, alternating each sheet with the opposite corrugation grain. Be sure not to put hot glue too close to the edge of the cardboard or it will ooze out when you press the sheets together.
Hot glue your cutting board to your cardboard base. Ensure the cutting board is centered at the top edge of the cardboard.
Base risers
Since there will be wiring going underneath the base, it will not sit flat on a table. The easiest way to solve this is to add risers to the bottom.
Make 8 small rectangles at least 1.25 inches wide. They must all be the same width. Notch each rectangle once to the middle of its width, and make each notch as wide as a sheet of cardboard (1/8th inch). Fit the rectangles together by the notches. Now we have 4 risers.
Glue a riser to each the 4 corners of the base, being sure to stay close enough to the edge so you have ample room for the wiring.
Step 5: Affix the Knife
Measuring and positioning
Lay a few sheets of paper on your cutting board, and rest the knife edge on the board. Try to let as much of the edge touch the board as possible, and hold it there. Measure the distance between the center of the pivot hole and the surface of the cardboard. Take that dimension and add at least 3/4 inch to it. This will be the height of the pivot pin strut.
Make pivot struts
Make a rectangle (or any shape really) out of this dimension, and cut out 6 of them from cardboard. Alternate the grain of the cardboard for strength. Glue them together in 3's to end up with 2 of these struts.
Measure the combined thickness of the struts, and add the width of the end of the knife. This measurement will be the length of your pivot pin and the width which the struts will stand apart.
Make small right angle triangles out of cardboard to fit in between the pivot struts. These supports will increase the surface that is glued together. It will be more able to withstand the torquing forces of the motor.
Mark strut positions and glue the pieces in place.
Make pivot pin
Cut a segment of dowel or metal rod for your pivot pin, and assemble.
Step 6: Make the Cams
When drawing the shape of the cams, you may have to guess a little bit. You may wish to
Measure range of knife motion
1: With the knife pinned in the pivot struts, lift the knife to its balance point, then slightly lower it until it is pulling itself down towards the board. Measure the height from the board to the cam pin hole on the handle.
2: Lower the knife onto the cutting board gently. Measure the height from the board to the cam pin hole again.
Take the first height and subtract a 1/4 inch distance between the cam and the cardboard base. This is the maximum diameter your cam can be.
Form the cam shape
Make a cardboard square that is the cam diameter wide, and draw a circle in it. The circle should be tangential to the edges of the square. Take the second measurement and subtract a 1/4 inch. Mark the value through the center of the square. Draw a circle from the mark, around the center of the square. This is the smallest part of the cam. You should have two concentric circles on the square of cardboard.
Divide the circle into quarters, if you have not already. One quarter of the cam will be the smaller diameter circle. Having a quarter of the cam be small allows dwell time for the knife to fall and chop as the motor spins. From the end of that quarter, draw a curve that gradually meets the "cliff" of the cam. The shape of this curve affects the speed which the knife will be raised.
Cut out your seashell shaped cam and use it to trace and cut out layers of it. 3 layers of alternating corrugation is enough to support the weight of the knife. It is extremely important to have a clean cut for each piece, take your time and get through the cardboard with several light passes.
Hot glue the shapes together in alternating grain. Ensure that they are aligned properly. With 3 layers of cardboard for each cam, you should end up with 2 cams.
Cut a cam pin
Cut a long segment of dowel or metal rod that can span fully across the two cams.
Step 7: Make the Motor Mount
The motor I worked with had a plate screwed on its front which allowed me to put a piece of cardboard in between. Depending on the motor you get, this mounting method may or may not work for you.
Take the radius of the "cliff" of the cam and add on a 1/4 inch. This will be the height of the center of the motor. Add on half of the height of your motor, and you have the vertical height of your motor mount.
Cut a strip of cardboard that is as wide as the surface you wish to mount the motor to, and make the strip long. Specifically, the length of the motor plus the height of the motor mount. Draw a line where the motor mount height ends and the motor length starts.
Mark where the center of the motor will be on the strip, and cut a hole large enough for the motor axle to fit through. Drill appropriate sized holes where the motor will screw in.
Bend the cardboard at the line between the motor length and the motor mount height.
Create 90 degree triangles to support the motor. Make sure they are short enough so the motor can still be attached to the mount.
Step 8: Make the Cam Axle Support
This step is to make a support for the other side of the axle. Take the cam axle height and add at least 1 inch to it. Make this out of 3 layers of alternating grain cardboard. When glued together, drill a 1/4 inch hole at the height of the cam axle. The size of hole to drill depends on the diameter of your axle.
Step 9: Make the Cam Axle
The diameter of your cam axle would best be the same diameter as motor shaft.
Measure and cut off a long enough section of dowel or metal to reach from the axle support to an inch past the cam.
File off the ends flat.
Draw a square on the end of the dowel.
Take your exacto knife and whittle off the dowel so it becomes square. You want to whittle all the way to the cam closest to the motor. Check that you are not going past the edges of the square you drew on the end.
Another way to make the axle is to mill a flat onto a dowel or metal rod. This will be stronger, but you may need more specialized tooling.
Step 10: Fix the Cam Shaft to the Motor
Completing the cam shaft
Stack the Cams on each other and drill a hole through it. The hole should be carefully placed so the cam does not interfere with the base when it rotates. Use a tiny drop of hot glue to temporarily hold the cams together while you drill.
Place the cams on the axle, and align them so both sides let the knife drop at the same time. Leave space at the square end of the axle to put in the axle support strut.
Hot glue the cams on the axle.
Attaching the cam shaft to the motor
Now, fixing the motor to the cam shaft is where I made a mistake. I used tape to bind the two together, which quickly failed.
My plan to solve this is to make the axle the same diameter as the motor shaft, and to make a coupling device that screws into the motor and axle.
Motors come in a variety of shapes and sizes: the diameter of your cam shaft
The coupling device would be a segment of metal tube with an inner diameter the same as the outer diameter of the motor shaft. Then drill and tap threads into the tube, so set screws can lock the motor and cam shaft together. The mechanical connection would be far superior to tape.
Make one of these couplings, and do not use tape.
Attaching the motor/cam shaft assembly to the base
With your knife resting on the board, fit the motor / cam assembly under the handle of the knife.
Mark the position you wish to glue it with a pencil and hot glue the pieces carefully spaced. Once the glue cools there is no going back.
Step 11: Fit in the Wiring
Drill holes into the cardboardbase
Holes need to be drilled for 3 places: the switch, behind the motor, and for the power source.
Wiring
Now that the holes are in place, you can plan out the wiring.
Thread the motor wires through the hole you drilled for it.
Starting with the female power supply jack, use a multimeter to find which prongs are postive and negative.
The circuit plan for this machine is very simple. A lovely illustration of the circuit by my professor is shown above, as well as a photograph of how I wired it. Step by step instructions follow.
Solder a red wire to the positive prong of the jack, and solder the switch to the red wire. Don't forget to put heat shrink on the wire before soldering! The other wire on the switch gets soldered to the red motor wire.
Solder a black wire to the negative prong. This wire gets soldered directly to the motor wire.
Now tape the excess wire to the bottom of the base, and congratulations, you are done! Just screw on the top of the switch and the AC power jack to finish up.
Thanks to
I would like to give great thanks to my instructors Garnet and Bobbi for helping me make this project possible.
Step 12: Extra Images
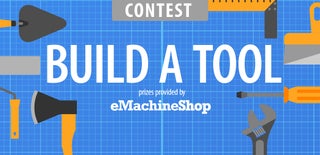
Participated in the
Build a Tool Contest 2017