Introduction: The Dragon Unifire Smoker
If you love BBQ, Smoked Ribs and want to tackle a decent size welding job than this is for you!
Also you might find lots of great tips for working with metal.
Step 1: Plans Make Detailed Plans
Make your design plans as detailed as possible. I used Autodesk Fusion360 Love it. Its a lot easier to make corrections and changes on paper or computer than in welded metal. But if you do happen to make a mistake (unlike wood or other materials) and cut a piece too short you can always just weld it back on.
Step 2: Tools Neeeded
1. a Mig welding machine with gas shielded wire
2. a metal cutting circular saw
3. angel grinder with cutoff wheels and grinding wheels
4. drill gun and drill bits
5. Jig saw with fine tooth Blades for metal
6. clamps and welding magnets and a bench vice
8. straightedge ruler and framingsquare and tape measure
9. a marker for metal or white wax pencil works good even chalk is ok
Step 3: Safety Equipment
Safety Equipment is very important
1. exhaust fan for fumes and ventilation.
2. welding helmet (wear a cap turned backward under the helmet).
3. welding gloves and welding sleeves or jacket.
4. face shield and work gloves for grinding and cutting.
5. respirator with new cartridges.
6, ear protection when grinding.
Step 4: Layout and Materials
Once you've gathered the necessary materials for your project you can begin to layout the parts and mark your cuts
sheet = 4' x 8' ft
I used :
2 1/2- sheets10 awg steel plate or 1/8" .125" or 3.2mm thick. for most of the construction
1- sheet 10 awg 3/4" expanded steel raised (Or if you prefer Flat)
60 ft. -Thick wall 1" square tubing
20 ft -1" x 1" Angle iron
20 ft.- 1" flat bar
8 ft. -1/2" round stock
12" - 5/8" OD 1/2" ID round tube (guides for 1/2" rod handles that must fit in it and turn freely)
32" -1 1/4" round tube (handle)
4" - 10 awg round tube (smoke stacks)
6 - Barrel hinges with grease nipples
4 - 5" Heavy duty casters with Brakes 2 that swivel 2 that don't (Important I'll explain why latter)
2 - Temperature gauges
2 - 1/2" black pipe couplings (do not use Galvanized when welded it makes toxic fumes)
spool of wire and a full bottle of gas for the mig welder.
Step 5: Start Cutting and Tack Welding the Frame
Cut carefully
I made all measurements on the frame pieces, in lengths of 1 whole inch increments.
Cut all your square tubing (1"x1") for the smoker's frame first
Refer to the drawing for specific dimensions but they don't have to be the same
I encourage you to change any size you wish to suit your needs
Try to be organized and take your time. The frame consists mainly of 3 dif. lengths of square tube
- 4(60"),uprights
- 8 (38") long horizontal cross members
- 2 (19") pieces for the fire box
- 12 (20") short members 10 for in-between the main frames.
one of these12 is used on front face frame and one on the back-copy.
Together with the two 19" pieces they make the fire box
Prep the cut ends for welding by cleaning and grinding a bevel along the perimeter of the end to be welded.
Good welds begin with clean metal, free of paint or oils to avoid weld contamination and poor welds.
Begin welding with the face frame, tack it all together only then make a copy of that frame for the back side
Make sure to keep everything square and flat. Now set the parts for the second frame on top of the first frame to ensure alignment.
after tacking all that together you should have 10 pieces of the 20" left over. Since the overall width was 22"
these pieces get welded in between the two frames. (1"+20"+1"=22")
using magnets and clamps to help hold it and always checking with a square
while continuing to tack it together. When the frame is fully assembled you can finish your welds
You will be making three types of welds on the frame (image) BUTT JOINT + FLARE BEVEL + FILET WELD
Step 6: A Word About Welding on Something Big Like This
Before we move on to body panels some good practical advice in welding.
You tack weld everything first and later you will finish the welds gradually in sections to avoid warping and distorting the metal. You want to assemble all your major components with each other tack them together firmly but in a manner that allows you to make adjustments or if need be, Once a part is tack welded adjustments can be made by persuasion with a hammer, leverage or clamp. If necessary any part can easily be freed from its tacks to make corrections. Never the less all tacks must be made stong enough to keep it together. (this reason is most important) When you start welding the whole seam on everything in a given section at the same time. Believe me you will warp the metal.
I do recommend that you make solid welds from end to end, on almost all the joints but do it in sections and spread the heat around moving from area to area and back until its all welded.
Step 7: Wheels and Handle
You might find this thing is getting pretty heavy and soon It'll be too heavy to move.
Good time to put wheels and a handle on this beast!
for the wheels I decided to make them replaceable and not permanently weld them on.
This was done by welding the bolts to the frame and try to keep the wheel base as wide as possible for stability.
To do this I weld the first bolt in the hollow of the vertical corners on all 4 corners.
Keeping the bolt heads flush or below the surface.
Now you got one bolt for each wheel mount the wheels and mark the remaining bolt locations.
for the remaining bolts i drill holes just big enough for the bolt head to squeeze through. with a hammer tap the bolt heads down flush and weld in the gaps formed by the round hole and hexagon bolt head.
I mentioned earlier that I would explain why I recommend two fixed wheels and only two that swivel.
Here's why: safety, control and stability. The completed smoker is very very heavy (600Lbs+) and will seriously injure a person were it to fall over on them.
So the fixed wheels offer a wider more stable wheel base. you want to put these on the heavier side, under the fire box. the two that swivel go on the side were you will put your handle. having this configuration enables control on uneven ground but stay away from grass and loose dirt.
okay enough about wheels time to make the handle.
Make it 24" plus 4 " long on each side for the radius and return legs.
Start with one piece 32" long 1 1/4" round tube and mark where the center of the radius will be on each side.
Around 5" inward because you will lose about 1" of length on each radius. start to remove pie sections about 1/8th wide and 1/8th apart cut half way through the pipe, from the center outward in both directions. I did 5 pie cuts total on each side . when done correctly the pipe should bend in a smooth radius and at 90 degrees to the handle. weld the seams and grind them smooth. Finally attach the handle to the frame just under the side panel.
Step 8: Face Panel and Dragon Body
Now that the frame is done its time for cutting the 10 awg panels
The front face panel starts as one piece including the three doors which we don't fully cut free until later just cutting around the door openings while leaving a tab section connected in the corners and middle of both doors ( To be cut later) This will ensure proper door alignment and will help keep the remaining narrow strips of metal around the doors from warping.
Now take the 1" flat bar and cut it to wrap it around the two top doors laid flat like a picture frame to create a door stop and seal. we'll call it the door jamb.
making sure it overlaps the relief cuts you made around the doors earlier centered to the 1"bar
One important note : the 1" bar piece in the middle was cut the full height of the jamb frame and is shared by both doors so it gets welded only to the door on the left which must open first. The rest of the jamb partsget welded on the door side only. You can put a couple tacks on the other side and remove them later when its time to open the doors.Do not cut the doors loose until you have the jambs and hinges tack welded firmly in place and the whole panel on the frame (but for now set the completed face panel aside for later)
Step 9: Smoke Stacks and Intake Vent
After completing the work on the Front panel.
The left side panel is where you will cut the hole for the intake vent.
at the level of the fires base. I cut a rectangular hole made a door slightly bigger than the opening and used some angle iron for the guides which need to be a little under twice the length of the opening.and one leg on these angle irons was shortened to make more of an "L" shape with the intake done tack the panel to the frame. The other shorter side is just plain so it can also go on the frame now.
If your ready take the top panel and cut the round holes for the smoke stacks
I used a Jig Saw for this and went through a few blades.
You can see in the video how much down force I put on the jig saw
to keep the saw from jumping and rattling around as I guide it around my marks.
A better tool for the job would be a plasma torch.
Once the two holes are cut and cleaned up with the grinder ,
Take the 4" tube and cut two equal lengths for the smoke stacks
And make the cuts as square as you can.
Weld them to the top plate ( mistake #1 = I weld all the way around the smoke stack before getting the other one on or even getting the panel tacked down to the frame. And I got some major warp-age!)
I used lots of clamps to get the piece to lay flat on the frame in order to tack it down. but before you do that.
Next you can cut the parts in the illustration at the top of this step
the triangular shape fin is for the vent top lid it will pivot from the small edge of this piece where you will weld a small section of 1/2" ID tube (Aprox. 2" long) so the handle can go through and come down the sides flush to the sides surface.you will need two of each shape one for each side.
at this time weld only the fin to the smoke stack side perpendicular to it and on the side closes to the edge. The lid handle and smoke stack top go on after the top plate is on the frame and side panels are also attached to the frame.
weld the top plate with both smoke stacks and fins to the frame and now the rest of the sides and bottom panels can be welded to the frame all panels should now be in place except the face and back panels.the back should be the last panel to go on . But before putting them on do the Guides for the pullout shelves . this will give you the freedom to work inside the smoker with out too much trouble.
Step 10: Temp Guages and Double Wall Doors
Its now time for the whole face panel together with doors, door jambs, and hinges can be tacked to the square tube frame. When you are sure nothing will move on you complete the cuts to release the doors from the face plate. With the hinges already in place the doors swing open and can now be lifted off the hinges and the welds can be completed without bending or moving half the hing gets welded to the door (with grease nipple) the other half (with the pin) gets attached to the face panel make these welds strong!
Double wall doors optional.
Being able to lift the doors off you can drill the hole for the gauges and weld into the hole a 1/2" pipe coupling so the temp gauge will thread onto itall the way but check the gauges dial readout is level and the right side up before welding the coupling,
Step 11: Water Pan and Smoke Diverter
Water pan and smoke flow control
I made a water pan/tray that fits snugly into the space under the bottom shelf. It needs to be just under the total depth of this space(20") and about 30"wide leaving about 4" of open space for the Dragons smoke to flow . So the smokey flavor (dragon breath) enters the chamber through an opening in the middle. It then hits the bottom of the water pan effectively heating your soaked apple wood chips and or other spices and favorite flavors. Go up and out along the bottom either to the right and Left or both sides depending on the pan center location in relation to the smoke entrance opening. This is where the smoke will pass through. and that space can be moved right or left. The pans bottom is made in sort of a wide "v" shape but the side pieces on the front and back are left rectangular and sit flat on the inside of the smoker. the left and right sides of the pan are only on the top part of the pan to hold water the bottom half is open and is where the smoke will come into the cooking area.The pan can move right and left to effectively control the direction of smoke flow together with the smoke stack lids and intake door this gives the user excellent control of the cooking/smoking environment.
Attachments
Step 12: Pull Out Shelfs and Ash Trays
Make three shelves pretty strait forward just make a frame form 1" square tube and put some expanded metal on top. add some support to the expanded mesh towards the middle. I put in two supports made of 1" angle iron turned up so the corner is up and supporting the mesh that way it will also allow oils and juice to drip off.
In the fire box
there are two components here :
1) The combustion container for wood and charcoal whatever fuel you desire. Its made of expanded metal all around.with 1" x 1" Angle Iron in the corners and around the bottom. The ashes fall though and into the-
2) Ash collector situated right below with solid 10 awg meal sides and bottom. no frame necessary here.
That's pretty much it!
I worked on it about 4 to 6 hrs a day for a month except weekends!
Step 13: Finish All Your Welds
Finish all your welds and clean everything up with the grinder
finally paint it with high heat paint on the outside only!
Step 14: Time to Light a Fire
Before its ready to cook you must season the inside surfaces by burning some logs of your choice and flavor. Also spray the inside cooking area with some cooking oil of your choice during the initial log burn.
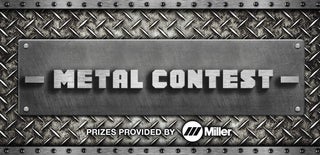
Participated in the
Metal Contest 2017