Introduction: The Micro Scope | a Miniture GOTO Telescope.
“Somewhere, something incredible is waiting to be known.” - Carl Sagan.
The sky is a fascinating place, but the real interesting stuff resides far beyond the thin atmosphere. The Universe, the Milky Way and our Solar System is where it's at. To be able to peer far out through the sky and observe the galaxy and beyond, one needs a telescope.
This Instructable follows my journey as I develop a miniture GOTO telescope. We'll look through some of the research I perform, glimpse at my design process, observe the assembly & wiring processes, view instuctions for the software configuration and then finally step outside to scope out the cosmos.
The Micro Scope Features.
- Raspberry Pi 4B & HQ Camera.
- 300mm Mirror Lens.
- Canon EOS Lens compatible.
- NEMA 8 Geared Stepper Motors.
- Fully GOTO with tracking.
- GPS.
- WiFi Enabled.
- GT2 Belt Drive.
- Hand Controller.
- 3D Printed Parts.
- Tripod.
- OnStep Telescope Mount GOTO Controller.
- INDI Server.
- KStars/Ekos.
Bill Of Materials & 3D Printable Parts.
The BOM & STLs are available from Thingiverse (4708262). However, I recommend downloading The Micro Scope Build Pack as it contains extras not available from Thingiverse!
Updates.
21/03/2021 | Added the Universal Tripod Fixture.
Disclaimer: I am an amateur, in fact I'd call myself a n00b as I don't think I have even reached the level of amateur yet. There will be mistakes, errors and incorrect assumptions. This is, however, all part of the learning process and a big step towards finding the incredible in the unknowm.
I have started a Micro Scope subreddit | https://www.reddit.com/r/The_Micro_Scope/
Step 1: Research | the Thoughts-To-Idea Ratio.
One important part of any project, and an area which is not generally explored or discussed, is the time spent researching and developing an idea. It may be fair to say, that as much as 25% to 50% of the time involved in realising your idea could and should be taken up simply researching and exploring what is possible.
For the Micro Scope there are a few distinct areas that I will be concentrating on.
- The Optics.
- Software
- Electronics.
Drive Systems.
I shall breifly outline my requirements for each of the above, what I find along the way, and why I made the decisions contained therein.
The above topics are covered in a step-by-step fashion, however it is not usually that simple in reality. What may have been selected in one area will likey have an affect on another. For example, a particular software package could require different electroincs to previous requirements, resulting in changes to ealier choices made to the electrical components. Consider it more as an ongoing circulating feedback loop, than a linear process.
During my research I like to keep a text document of any interesting pages or sites I find while digging around. I don't keep track of every single page, but I do record any which bring to my attention useful information, or act as a launching point for other areas of research. You can download my notes for this project from here | notes.txt
Step 2: Research | Optics
Astronomy normally requires large telephoto lenses (mirrors!) with big light gathering cababilities. The Raspberry Pi HQ Camera uses small CS-Mount or C-Mount lenses. Unfortunately I struggled to find suitable lenses in those form factors that were at the right price-point for the project, and or had adequate telephoto capabilities.
After remembering the HQ Camera announcement post on the Raspberry Pi Blog where I saw the RPi HQ Camera adapted to fit onto a Canon lens. I did some basic googling, which spat out a C-Mount to Canon EOS Adapter by Arducam. The big benefit to the adapter is that it opens up the optical design to a huge amount of different full-frame lenses.
As this is a telescope we don't need, nor want, a variable zoom lens, what we desire is a fixed focal point prime lens. Naturally I spent some time researching prime lenses. I discovered a number of lenses around the 100mm range, both new and used, but what really peaked my interest was a Mirror Lens.
Mirror lenses, or catadioptric lenses, combine curved mirrors (catoptrics) with glass lens elements (dioptrics). Used only for telephoto lenses, the design provides a much shorter, lighter, and less expensive lens than a comparable conventional telephoto lens. (Camera Wiki).
The lens I have picked out is the Samyang 300mm f/6.3 Mirror Lens*. There are several reasons why I chose this lens, the main reason being the Canon EOS mount, others often required additional adaptors to fit. Seconly was the size, at only 64mm diameter and 74mm length it was 'on brand' with the small form factor of The Micro Scope. Lastly, the cost, the lens is very cheap for a 300mm focal length lens and all the reviews I watched or read gave generally positive reviews.
I uncovered an interesting quirk of using full-frame lenses with a small CCD as used in the HQ Camera; an increase in zoom, due to the crop-factor. For example, the 300mm full-frame lens equates to 1692mm with the HQ Camera. The disavantage is a reduction in the light received by the CCD, the f/6.3 full frame value drops to f/35.5 with the HQ Camera. This shouldn't be too much of a problem, but it is worth making note of regardless. There is an online calculator which will give approximate numbers for the HQ Camera. They also explain how it all works | https://mmcalc.com/
If you already have a Canon EOS DSLR camera you will likely find that your lenses are compatible with The Micro Scope. However, do bare in mind that the autofocus will not work. There is also an Arducam Nikon F-Mount to C-Mount adapter available. You will need to update the design to use the Nikon lenses (see The Micro Scope Build Pack for the design files).
*afflink
Step 3: Research | Software.
Having chosen the Raspberry Pi HQ Camera we are commited to using a Raspberry Pi in the telescope. It is worth looking to see what else we can do with the RPi, it may save some time and effort if we can use it to control the telescope's movement too.
Immediately after googling 'raspberry pi telescope control' I am presented with a huge number of results. Including some home builds with the Raspberry Pi controlling a telescope. There is one common feature to them all; none of them have the actual motor control via the RPi, that's done by the telescope mounts which have integrated drive systems. We're looking to design our own system so we'll need to find something which can run the motors for us too.
There was one very good thing I found called INDI. "What is INDI?" I hear you say.
INDI Library is an open source software to control astronomical equipment. It is based on the Instrument Neutral Distributed Interface (INDI) protocol and acts as a bridge between software clients and hardware devices. Since it is network transparent, it enables you to communicate with your equipment transparently over any network without requiring any 3rd party software. It is simple enough to control a single backyard telescope, and powerful enough to control state of the art observatories across multiple locations.
For us it means we can install INDI server onto the Raspberry Pi and use it as an interface to control the telescope, including the camera, and we can add a GPS in there too! All we need to find is something to control the telescopes movement. Ideally we're looking for software and electronics for motors in bespoke telescopes and not something which plugs into already existing telescope GOTO mounts.
'diy goto telescope controller'
Amongst the first page results on google two articles pop up, one which mentions rDUINOScope and another which mentions OnStep.
After looking into each I have chosen OnStep. Why OnStep? Well rDUINOScope is limited to one or two boards, it is designed as a handheld controller which plugs into motors. What we require is something that can be integrated into the design to keep everything small and simple. OnStep is primarily firmware, which can be flashed to many different boards.
Step 4: Research | Electronics.
OnStep is compatible with a wide ranging selection of electronics boards. There is a Wiki article which explains each board; their advantages and disadvantages.
For The Micro Scope a big design requirment is a small form-factor. The most compact board and electronics combination I could see is the The WeMos R32 with CNC V3 Shield configuration.
We'll be using just two stepper motors, the CNC sheild has space for upto four drivers. There are also several other options that we will be tring to take advantage of, the clock interface, atmospheric sensors and the optional Smart Hand Controller.
The WeMos R32 is a Bluetooth and WiFi enabled board. The plan is to have the Micro Scope remotely controlled via a laptop or desktop pc. With the exception of the power cable and hand controller cables The Microscope will be wireless.
I wanted the internal wiring to be hidden and internal to the Micro Scope. There is a potential problem with this; The Micro Scope needs to rotate and having wires that are unable to rotate too means they can be twisted up and they will eventually break.
There are a total of eight wires that go into the scope. Two power wires, and six for the Smart Hand Controller. We could make a flexible coiled cable, but this would still be very limited in the number of revolutions we could make before breaking the cables. Without being able to see inside it is very hard to know how twisted the wires are. We need something which rotates and doesn't twist.
I spent a few moments searching the internet, as one does, and discovered a dandy little thing called a Slip Ring. Problem solved! With the slip ring the wires are able to rotate and not twist. I bought an 8-wire and a 6-wire miniture slip ring. We need two as we have two axes of rotation.
Step 5: Research | Drive Systems.
The wheels on the bus go round and round. The Micro Scope is not a bus and it does not have wheels, but it does need to go round and round. Because of this we need to give it a drive system.
Mounts.
Before we delive into the drive system we need to carry out a bit of investigation into the different types of telescope mounts, what it is exactly that we need to move, and how we can go about doing it.
The basic premise of tracking the night, or day, sky boils down to two basic movements; Left & Right (East & West) and Up & Down (North & South). The telescope is moved along these axes into position for observation with reference to the Right Ascention (RA) and Declination (DEC).
When looking at the drive system it is a good idea to look at a lot of telescope designs, big, small, space based, even ones mounted to a Jumbo Jet, all are worthy of investigation. The most popular designs I found are German Equatorial Mounts, Open Fork Mounts and Alt-Azimuth Mounts.
Hoping to keep the design compact I conclued that the German Equatorial Mount was not a good idea, the big counter-weights required to balance the telescope made this a bad choice in this case. The compact Open Fork Mount is what I chose. I had an idea to hide the motors and hopefully the electronics in the fork arms keeping everything nice and compact.
The German Equatorial Mount (GEM) does has an advantage over the Open Fork Mount. The GEM can be aligned to the polar axis, this mean that only one axis need to be driven to track the sky. The Fork Mount requires both axes move to track the sky, additionally the Fork Mount also suffers from Field Rotation. There is an easy way to correct both the field rotation and polar alignment when using a Fork Mount. By adding in an Equatorial Wedge the fork arms can be tiled back to align with the polar axis. The optional Adjustable Equatorial Mount is explored later in this guide.
Motors.
After picking the mount type we can move onto the drive system proper. Having done a little back and forth looking at the Electroincs and Software, the type of motor we need is a Stepper Motor. The Micro Scope needs to move in precise movements and using a BLDC requires encoders and extra control systems, the steppers do not. I do also have some experience with Stepper Motors.
Gearing.
A telescope needs to be able to move at the same speed that the earth rotates at. That is to say it must perform a single constant rotation in about 24 hours (A Sidereal Day). On top of that we want to be able to slew the telescope at a reasonable rate. Finding a motor that can do both is going to be difficult and will require some gearing. Standard practice is to attach the stepper motors to an already existing manually controlled telescope mount and simply adapt that for automation. The Micro Scope is different as it is an original build and doesn't already have manual controls.
Knowing the small form-factor of The Micro Scope it is best to look for small stepper motors with high ratio gear boxes already attached. The smallest motor I dared look at was a NEMA8. The particular motor I found came with a 90.25:1 planetary gearbox. I bought two.
Drive.
The last part to consider is the final drive. Taking power from the motor output shaft and moving the optics. As these parts will likely involve custom printed parts. I have purposely avoided gears (too much backlash), and opted for belt drive. During the design phase we'll see how much extra reduction we can get from the belt system.
Step 6: Design | Layout.
Having decided on all the parts we will be using in The Micro Scope, the next stage is to plan out how they all fit together. For this to happen we'll need CAD representations of each of the main components.
There are several repositories for CAD models and a quick search online should bring up most of the parts. Those which I have been unable to find I have modelled myself in Fusion 360. A large portion of the Electro-Mechanical CAD has come from grabcad.com.
I found a fantastic Pulley Template on Thingiverse which I used to help design the pulleys used in The Micro Scope.
There are still a few areas to be decided on; the bearings, fixings, overall dimensions, belt length, pulley ratios, and general form. All this will fall into place as the overall design develops.
The first important step is figuring out how everything is positioned, to do this I have imported all the representative CAD into a single assembly in Fusion 360. From within this assembly we can play around and find the best layout for the parts.
Datum.
I always try to find a single point to work the design around. In this case the optics, or specifically the RPi HQ Camera. This will be the starting point from which all else extends from.
The Basics.
Having imported the main electro-mechanical parts into the general layout we can start to consider the other components, the GT2 Pulleys can be guestimated. We can also start considering which bearings we're going to use in the project too.
To Begin.
Once we're satisfied with the approximate arrangement of parts we can move onto designing the main assemblies.
- Camera.
- DEC Drive Arm.
- DEC Idle Arm.
- RA Base.
- Adjustable Equatorial Mount.
- Tripod.
- Smart Hand Controller.
The layout will be constantly updated with the latest version of each assembly and used to verify that everything fits together and that there is enough clearance between each part so there are no collisions.
Step 7: Design | the Main Assemblies.
Designing the main assemblies is where the bulk of the work resides. Checking back through the history in Fusion 360 I can see there is a three month period between the very first file save of the layout and the most recent full assembly version. That doesn't include all the time spent doing research beforehand.
Important points to think about when doing your design work.
- Avoid Feature Creep. It's also ok to simplify the design and remove features...
- Keep it simple, stupid. A point which I fall foul of all the time.
- Don't be afraid to change something completely and or restart from scratch.
- Refer to your research, and do more when required.
- Back-Up your work.
- If you get stuck on one area, try something else, you can always come back to it later.
- Most critically of all, don't rush.
As discussed previously, our starting point, or datum, is the camera and optics. Working out from there the first axis we encounter is the Declination, followed by the Right Asecntion, Adjustable Equatorial Mount and finally the Tripod Base.
There is a lot of back and forth between the assemblies, lots of printed parts to test the designs and check fitment. The last photo attached above shows a sample of the prototype parts I printed during the development.
Designing for 3D Printing.
This project is going to be entirely 3D Printed (excluding the electro-mechanical parts). There are a number of design 'must dos' to take into account when designing the parts. I won't go into too much detail, people have written books on the subject, but I shall mention a few anyway.
Part Orientation.
Keep in mind how the part will be orientated when printing. Pay particular attention to....
Overhangs.
Avoid them if possible. They require support. Small to medium sized cut-outs are generally fine though. Chamfers are your friend.
Pointy Corners.
Pointy or square edges on the print bed act as stress concentrators and are typically the starting point for the print coming off the bed. A small radius usually fixes this.
Nozzle Size.
Small features need a small nozzle. Don't make fine features if you are using a 0.8mm nozzle.
Holes.
They will be smaller than you expect. This can be a good thing if you are going to ream them out after, or bad if you want two parts to fit together.
Elephants Foot.
I always put a small chamfer (1-2 x the layer thickness) on all edges that will be printed first on the printer bed. This will help counter any inaccuracy in the first layer if the nozzle is too close to the bed.
Step 8: 3D Printing | the STLs.
I've chosen to use ColorFabb's XT-CF20 material to print all parts, with the exception of the pulleys which I have used Prusament Clear PETG and the Tripod Feet where I have used TPU (flexible).
XT-CF20 is a PET-G co-polymer carbon fibre reinforced material. PETG is commonly refered to as an engineering plastic. It is chemically resistant, easy to machine, and is stable in a wide range of temperatures. Adding in the carbon fibre increases rigidity and stiffness.
All parts are printed on the E3D ToolChanger. However, The Micro Scope is small and all parts will be able to fit into a standard 200x200x200 build volume. Obviously, not all at once.
Printer Settings.
- 0.4mm Nozzle X (0.25mm for the Pulleys).
- 0.2mm Layer Height (0.1mm for the Pulleys).
- 5 Top Layers.
- 4 Bottom Layers.
- 3 Perimiters.
- 14% Infil.
Dry Your Filament!
The difference is print quaility and material strength makes this a no-brainer. Don't believe me? Check Stefan from CNC Kitchen's video on the topic | https://www.youtube.com/
Download The STLs.
You can download a basic set of STLs from Thingiverse (4708262). However, I recommend downloading The Micro Scope Build Pack.
Step 9: 3D Printing | Post Processing.
Cleaning.
Most, if not all, printers require some sort of bed adhesive to help keep the part attached to the print bed during the printing process. After the part has cooled and has been removed from the bed there is often small amounts of this adhesive remaining on the part. An oftern overlooked part of post processing is cleaning off this adhesive from the part. I have found that a damp cloth or paper towel easily removes any residue from parts.
Reaming.
Clearing round holes for bolts and threads. 3D Printed holes never come out quite right and unless you can machine the holes mid print you're going to need to ream out the holes. I have a printed Set Of Reamers which I use to correctly size the holes.
It is important to remember that threaded holes need to be smaller than the designated screw diameter. For example, an M3 sized threaded hole has an internal diameter of 2.5mm, so the hole must be reamed out to 2.5mm and not 3mm. Similarly a correctly sized clearance hold for an M3 bolt to pass through is 3.2mm.
Tapping.
Tapping threads into 3D pritned parts is not to everyones likling. It is perfectly possible to screw an M3 bolt into a 3mm hole and everything be just fine. However, it can make dissasembly and maintenance tricky as the threads are poorly formed. For the best results one needs to thread the holes correctly.
Threading holes into plastic is not easy, but if it is done correctly you can get very good results. The biggest problem is caused by friction which melts the plastic parts. Taking your time and not rushing things is the way forward.
Required Tools.
- A set of Drill-Taps*.
- A Set of Spiral Taps*.
- Tap Handle*.
- Manual Thread Tapping Machine.
- Counter Sink Bit*.
- Set of Hole Reamers.
- A set of Allen Keys*.
Take your time, rushing will mean the holes are damaged and you will have to reprint the part and start again. Also remember to check the depth of each hole so you do not go too deep.
- Begin by using the Drill-Taps. They have a drill at the front to cut the hole to the correct size before the threads begin to be cut.
- Only go approximately 1/2 way down the hole with the Drill-Tap.
- Pause for 5 - 10 minutes. This will allow any heat to dissipate.
- Careful back the tap out from the hole.
- Wait a further 5 minutes.
- Finish off the hole with the spiral tap, remembering to pause to allow heat to dissipate.
- Clean up the holes with the Counter Sink Bit.
- Check the thread has worked.
* Affiliate Links.
Step 10: Assembly | Preface.
This is not the final assembly, we're using these assembly steps to check the design, verify the fixings and to make sure everything moves as expected.
We'll need to add wiring, flash the firmware and then we'll probably be at a stage for the final assembly. After that we'll undoubtedly need to take it apart again before we do the final final assembly after which we can finally point it at the sky.
Bill Of Materials.
The BOM is available from Thingiverse (4708262) and Cults3d.com.
Step 11: Assembly | the Camera.
The Camera needs to be super sturdy. The RPi HQ Camera PCB is bolted to the back of the camera housing and held in place with a tripod thumb screw. The Arducam converter is also supported by the camera housing and screws into the RPi HQ Camera C-Mount. When everything is tightened together the CCD and optics will be Rigid AF™.
The Raspberry Pi is accessible by removing the GPS cover, named so as the buldge houses the GPS module. Removing the cover provides access to all the USB Ports, RJ45 socket and the SD Card. In the same housing is plenty of space the a DC-DC Buck converter to drop-down the 12v supply to the 5v the RPi needs to function.
Step 12: Assembly | the DEC Drive Arm.
Fitting the NEMA8 DEC drive motor, bearing, the OnStep WeMos + CNC Sheild and the TMC stepper drivers, plus the belt drive into the DEC Drive arm was quite a squeeze.
The NEMA8 motors require very low current so there should be no need for active cooling of the stepper drivers.
Step 13: Assembly | the DEC Idle Arm.
The Dec Idle Arm should really be called the DEC Idle And RA Drive And Power Slip Ring Arm, but it's a little long-winded. Perhaps the acronym DIARDAPSRA is easier to say instead? No? We'll stick with the DEC Idle Arm then.
As discussed, the DEC Idle Arm also features the RA drive motor and a Slip Ring to provide power to the Raspberry Pi. I have used a 6-wire Slip Ring to future proof it against any later upgrades.
Step 14: Assembly | the RA Base.
One of the larger more complex assemblies, the RA Base houses two large bearings, an 8-wire Slip Ring, a 144 teeth pulley and some cable sockets. We also bolt both the DEC arms to the RA Base.
Step 15: Optional | the Adjustable Equatorial Mount.
An equatorial mount is a mount for instruments that compensates for Earth's rotation by having one rotational axis parallel to the Earth's axis of rotation. This type of mount is used for astronomical telescopes and cameras. The advantage of an equatorial mount lies in its ability to allow the instrument attached to it to stay fixed on any celestial object with diurnal motion by driving one axis at a constant speed. Such an arrangement is called a sidereal or clock drive. (WikiPedia).
The Equatorial Mount requires that only a single axis, in this case the Right Ascention, needs to move to track the sky. The advantage of this is a much more stable, smooth and efficeient base for observation and astrophotography.
The Micro Scope is tilted backwards on it's base with the Forks (The DEC Arms) pointed towards the Celestial North Pole. This setup is typically refered to as an Equatorial Platform.
The Adjustable Equatorial Mount (AEM) comes in three base angles (25°,45°,65°) and can be adjusted +-15° to match your Latitude. I am in Oxfordshire and thus I have used the 45° AEM and adjusted it to 51°N.
The Adjustable Equatorial Mount is included as part of The Micro Scope Build Pack.
Step 16: Assembly | the Tripod.
A stable platform to affix the upper parts of the Micro Scope. Attach the AEM for complete control or the Tripod Fork Adapter for 'on the go' lifestyles.
The legs angle out by 55 dgrees and fold up into a compact base. If you have a multi-material printer there is the option of adding rubber feet and the Micro Scope text to the leg(s).
Step 17: Assembly | the Micro Scope.
With the sub-assenbles checked and verified we can assemble The Micro Scope itself. I've fitted the 300mm Samyang Lens & Hood to double check fitment.
The pulleys aren't affixed to the motor output shafts so I have to held it all up by hand. With the pulleys correctly affixed to the output shafts it will hold itself up. The high reduction planetary gearbox will prevent any back-driving from the weight of the assemblies.
Step 18: Optional | the Smart Hand Controller.
The Smart Hand Controller is a hand controller with display which can be used to setup and control OnStep. It's an adaptation (and extension in some respects) of Charles Lemaire's excellent "Teen Astro" hand controller firmware that allows it's use with a stock OnStep system. Nearly all features are supported so an SHC+OnStep is a stand-alone telescope controller capable of setup, alignment, and operation (gotos to stars, Messier/Herschel400 objects, the planets, etc.) (OnStep).
I purchased the electronics kit for the SHC here | https://baheyeldin.com/ | The case I designed myself in Fusion 360.
Alternative SHC Design.
Since making my Smart Hand Controller a new version has been released by another user which does not require the PCB. Details of the design can be found here | https://www.thingiverse.com/thing:4694885 | Read the OnStep thread here | https://onstep.groups.io/g/main/topic/shc_enclosure_printed_no/79192768
Step 19: Wiring + Assembly | Preface.
The Raspberry Pi & CNC Sheild use standard 0.1" headers, which you will need a selection of. The Smart Hand Controller uses RJ12 6P6C sockets and I will be using a cut and soldered 6P6C cable for that. The power connectors are standard 2.5 x 5.5 jack & sockets.
The rest of the connectors are really down to your own personal choice. You can also just solder all the connections, but that does make it difficult to disassemble.
You will of course need a soldering iron, solder, heat shrink and general making-stuff tools.
Step 20: Wiring + Assembly | the GPS.
The GPS cover was designed with the vision of fitting the NeoBlox GPS module inside. There is an excellent instructable explaining how it is configured to work with the Raspberry Pi | https://www.instructables.com
The connectors are standard .1" housings and plug directly onto the Raspberry Pi GPIO. I have wrapped the electronics in kapton tape to insulate the contacts to prevent short circuits.
I have split the wires into two singles and a pair. The UART TX/RX pins are next to each other on the RPi GPIO, but the 3.3v and GND pins are spread apart. It would have been possible to havea single housing for the GPIO, however, with the additional pins required for the power input I decided against it.
The GPS module has been secured into the housing with some double-sided sticky foam.
The software will be covered in a later step.
Step 21: Wiring + Assembly | the Raspberry Pi Power & DEC Idle Arm Slip Ring.
The DEC Idle Arm features a 6-wire Slip-Ring. Currently we only require two of those wires for power. The other four will be unused. However, instead of cutting them off or having them flapping around we're going to install a 6-wire connector block at each end of the slip ring.
I am using Molex microfit 3, primarily because I have a load of them in the workshop, but they are also pretty good latching connectors.
I have insulated the DC-DC Buck Converter in heatshrink. This particular model has an adjustable Potentiometer and I have carefully cut the insulation away around the component. If you too have a similar converter make sure you adjust the voltage before to connecting the RPi.
Step 22: Wiring + Assembly | the HQ Camera.
Installing the HQ Camera is pretty simple.
- Remove the Raspberry Pi from the Camera Housing.
- Install the FFC into the camera, check it is the correct way around.
- You'll need to lightly bend the FFC and fit the RPi back onto the stand-offs.
- Bend the FFC and insert in the CSI socket.
- Refit the back.
No need to fully tighten the screws as the back will need to come off again for the power cables.
Step 23: Wiring + Assembly | the DEC Idle Arm.
The wires from the slip ring need to pass through the DEC Idle Arm and bearing clamp, additionally make sure they are not pinched by the camera housing.
Step 24: Wiring + Assembly | the GPS Cover
I've put the GPS cover onto the camera assemlby to protect the internals during the rest of the wiring.
Step 25: Wiring + Assembly | the DEC Idle Arm Pulley.
The pulley needs to be positioned with the belt centre positioned 11mm from the face of the DEC Idler Arm.
Step 26: Wiring + Assembly | the RA Base Top.
After attaching the DEC Idle Arm to the RA Base Top a pair of 2-pin housings are attached to the motor wiring and fed through a pass-through hole.
I'm keeping all the colours the same through the wiring harness between connectors. I use completed connectors as a reference. It can be quite easy to get into a muddle and wires the connectors the wrong way. Take extra care!
As we are not using the full six wires in the slip ring I have only added the two we are using, the black and red wires (+ & -). If needs be additional wires can be added at a later date.
Step 27: Wiring + Assembly | the RA Base Bottom.
The RA houses an 8-wire slip ring. I'm using an 8-way connector on the one side, and a 6-way with a 2-way on the other. The 6-way is for the Smart hand Controller, the other is for power.
When connecting the RJ12 6P6C housing it is important to make note of the cable colours and pin numbers. We'll need this in a later step.
Step 28: Wiring + Assembly | the Adjustable Equatorial Mount.
To make thing easier I have bought a 6P6C RJ12 cable to cut in half. One end will be wired to the socket and the other will retain the plug. Take the extra time to make sure the cables are in the correct order when soldering to the socket. Also check the wires are fed down the correct channel into the correct recess for the socket. Similarly the power cables have their own socket and pocket too. Make sure to leave some slack so the AEM can be adjusted.
Step 29: Wiring + Assembly | the Tripod.
As with the AEM we need to wire in a RJ12 socket and a DC socket. Check the order of the wires match with the AEM.
When complete you can join the AEM and Tripod together.
Step 30: Wiring + Assembly | the CNC Shield.
The CNC Shield needs to have the resistor labelled R1 removed to prevent any damage to the WeMos board. The reasoning for this is explained in the OnStep Wiki.
I am installing the optional Smart Hand Controller, the pin-outs on the CNC Sheild for the datalines need to be connected to 3.3v via a resistor pull-up. I am using a 2k resistor array to do this. A short wire connects to the 3.3v pin on the CNC Shield.
I have installed the TMC2130 Stepper Drivers to check fitment. I advise taking them off and keeping them safe until they are actually required.
Step 31: Wiring + Assembly | the TMC2130 Stepper Drivers.
I'll be fitting TMC2130 Stepper Drivers to the CNC board. Other drivers are available. They can be configured to operate in two modes. The first mode requrieds we jumper the steppers and set the current for the motors using the onboard potentiometer. The other mode, the one I have chosen, is to use OnStep to control the drivers directly. This option requires soldering wires to the WeMos and CNC Sheild. The OnStep Wiki explains which connections need to be made.
Step 32: Wiring + Assembly | the WeMos & Wire Termination.
The 8-wire slip ring wires are terminated with standard 0.1" housings. Refer to the notes taken earlier about the colours and pin numbers. Check with OnStep Wiki and make sure they are connected to the correct pin-outs.
We still have to connect all the peripherals, flash the firmware and then make sure it all works!
Step 33: Software | OnStep.
Ironically this step is mostly about the hardware. The OnStep Wiki has the most upto date instructions and guides. The Forum is where you'll be able to ask questions and fill in the blanks, everyone on there is very helpful and you'll likely have things up and running in no time!
The WeMos R32 & CNC Shield combination is very new and still experimental, there is a long thread on the subject which I highly recommend looking through.
Even though the WeMos R32 has onboard wifi you will still need a WeMos D1 Mini WiFi module. Instructions on how to setup and install the module are on the Wiki. This is not technically required as we are going to be using the onboard Bluetooth to connect OnStep to the Raspberry Pi. However, it is good to have as a backup. Remember to enable Blutetooth in the OnStep config.
There are several optional modules you can install, I have chosen only to fit the RTC*. There is plenty of space for the others.
Check the config.h wiki page for all the options.
Before you power things up remember to adjust the power output of the buck converters. Failure to do this will likely cook your electronics and release a cloud of magic smoke.
Adjust the current settings for the vref on the two stepper drivers. They need to be set to 2.5v.
You will also need an additional 5v Buck Converter. The WeMos R32 has an issue with the onboard 5v. It took a while to diagnose why the Smart Hand Controller wasn't powering up and the bad 5v turned out to be the cause.
Before fixing everything in place make sure all the motors turn. When you are happy with everything you can pack everything in. I have left the cover off the electronics and removed the GPS cover as the next stage is setting up the Raspberry Pi.
*The RTC was later removed as time information can be passed to OnStep via KStars, INDI and GPSD.
Step 34: Software | INDI.
We are going to compile & install a collection of software packages on & to the Raspberry Pi.
- INDI | The primary server.
- INDI Web Manager | A web based manager for INDI.
- INDI-3rdparty | A collection of third-party drivers.
- INDI-GPSD | The GPSD module for INDI (part of the 3rd party drivers).
- GPSD | The linux GPS daemon.
We will also have to configure the Raspberry Pi's Bluetooth connection, enable the camera, enable SSH, update the system and compile the software from source.
Raspberry Pi OS.
To begin, download the Raspberry Pi OS Lite | https://www.raspberrypi.org/software/operating-systems/ | You'll need to flash the .img file to an SD card. The RPi website also walks you through how to write the .img file to your SD Card. You'll also need a terminal program, I use PuTTY.
The lite OS does not include a desktop manager and as we will not be plugging in a HID or monitor we have to connect to the PI via SSH. SSH is not enabled by default. Before removing the SD Card from your PC, save a file to the boot partition called SSH do not give it a file extension. This will automatically enable SSH on boot.
When the SD Card is ready, insert it into the RPi. Also connect the DC DC Buck Converter, GPS and plug in a network cable (we will enable WiFi later). Plug in the SHC. Check the GPIO connections are correct!
When you are happy with everything, plug in the power supply. The RPi will take a few moments to power up, also check the SHC to make sure OnStep is still working fine. When the RPi is loaded, open PuTTY, enter the IP for the RPi and connect. Follow this guide to find the RPi's IP.
On first connecting to the RPi, the default login details are username: pi and password: raspberry. You will be prompted to change the default password. After logging in run the RPi config raspi-config. I reccomend expanding the file system, you'll have to enable the camera and change the hostname. You will need to disable shell access on the serial interface. You can also configure the WiFi. Reboot, log back in, then update the system with sudo apt-get update then sudo apt-get upgrade. Reboot again.
Bluetooth.
We're connecting to OnStep via BlueTooth. this gives us the advantage that we can control everything simply by connecting to INDI on the Raspberry Pi. The Raspberry Pi is far more powerful than the WeMos we are using for OnStep.
From the console type:
- sudo bluetoothctl (this loads into the Bluetooth controller).
- power on
- scan on
- Take a note of the MAC address of the device labelled Scope.
- pair [mac address]
- Type yes to complete the pairing.
- trust [mac address]
- type quit to exit.
OnStep will now be paired with the RPi and should connect automatically when Bluetooth is turned on.
While OnStep will connect to the RPi automatically on boot, we need to setup the connection as a serial port which INDI can interface with. We will do this by setting up a service.
Download the attached rfcomm.service.txt file.
From the console type;
- sudo nano /etc/systemd/system/rfcomm.service
- Paste the information from the text file into the console and repalce [mac address] with your MAC address from earlier. Exit and save.
- sudo chmod 644 /etc/systemd/system/rfcomm.service
- sudo systemctl daemon-reload
- sudo systemctl enable rfcomm.service
- sudo reboot
After the system has rebooted you can check the service has worked by typing;
- sudo systemctl status rfcomm.service
Exit with ctrl-c.
INDI.
Goto the INDI GitHub. Follow their instuctions to install INDI. We will be using the shallow clone as we are not doing any development work. Build indi-core.
GPSD.
There is a great guide available on Maker Pro that will get GPSD setup | http://maker.pro/ | There is one aprt that isn't covered which took me a while to figure out. GPSD needs to be told which serial port to look at and it doesn't look at the right one by deault. I found a guide which shows how to set the device for GPSD.
You'll need to sudo nano /etc/default/gpsd and edit the line DEVICES="" to change it to DEVICES="/dev/serial0"
INDI 3rd Party Drivers.
Goto the INDI 3rd Party Drivers GitHub. Again we only require the shallow clone. We will install the driver we want next.
indi-gps 3rd Party Driver.
Following from above, and on the same GitHub page, we only require a single driver from the 3rd party drivers; indi-gpsd. Follow the instructions for Building individual 3rd Party Drivers and replace the demonstrated driver of indi-eqmod with indi-gpsd.
INDI Web Manager.
Before we begin we need to install pip. This is easy todo by simply typing sudo apt-get install pip into the console. Next, head to the INDI Web Manager GitHub. Follow the instructions to install the manager. If everything has worked you can start the manager to check it's function with indi-web -v.
Once connected setup a new profile, and enable GPSD, LX200 OnStep, V4L2 CCD from the drop-down. Also tick the Auto-Start and Auto-Connect check boxes.
Lastly to enable the manager on boot follow the guide to install the manager as a service, similar to the one for Bluetooth.
Next.
Put the covers back on The Micro Scope. We may need to adjust the motor connectors in case we have them the wrong way around, we'll do that in a later step after we install and setup the control software on a PC or laptop. You can also fit the lens too. Be extra careful not to get dust on the CCD.
Attachments
Step 35: Software | KStars & EKOS.
KStars is free, open source, cross-platform Astronomy Software. It provides an accurate graphical simulation of the night sky, from any location on Earth, at any date and time. The display includes up to 100 million stars, 13,000 deep-sky objects, all 8 planets, the Sun and Moon, and thousands of comets, asteroids, supernovae, and satellites. For students and teachers, it supports adjustable simulation speeds in order to view phenomena that happen over long timescales, the KStars Astrocalculator to predict conjunctions, and many common astronomical calculations.
Ekos is an advanced cross-platform (Windows, OSX, Linux) observatory control and automation tool with particular focus on Astrophotography. It is based on a modular extensible framework to perform common astrophotography tasks. This includes highly accurate GOTOs using astrometry solver, ability to measure and correct polar alignment errors , auto-focus & auto-guide capabilities, and capture of single or stack of images with filter wheel support. Ekos is shipped with KStars.
There are other OpenSource Astronomy packages, Stellarium, Sky Planetarium, for example. I have chosen KStars as it is what I am familiar with and I know how to make things work (sort of).
Download KStars from their website | https://edu.kde.org/kstars/ | Install after downloading. Open after installing.
When the program loads go through the setup wizzard. I didn't install any extra data packs, you can add them later.
Next click Tools > Ekos.
You'll be presented with another wizard. Follow through entering the required data.
- Mount: LX200 OnStep
- CCD: V4L2 CCD
- Aux 1: GPSD
To start EKOS click the play button. Everything should now connect and the INDI Control Panel will open. You may need to go through and adjust a few of the settings. If LX200 OnStep isn't connected make sure the connection tab is set to serial with the port as /dev/rfcomm0
It should be possible to check the camera is working by opening the V4L2 CCD tab and going to the streaming tab. Check the lens cap is off, then click stream. If everything is working you should see a camera feed from the Micro Scope.
When you are happy, exit the control panel and return to EKOS. Head to the Mount tab. Turn tracking on, wait a few seconds for the button to go red, then turn it off again. When the off button is red again click Mount Control and a new window will pop up. You should be able to move the Micro Scope around with that control panel.
For the next step, we need to go outside!
Step 36: Outside | First Use.
I have adjusted the Adjustable Equatorial Mount (AEM) to 51.75°N, I'm in Oxford, UK.
As I am a complete novice to Astronomny I have bought a Solar Filter so I can try and setup The Micro Scope during the day before taking it out at night where I'll likely have trouble seeing. It is vitally important that you use a solar filter when pointing The Micro Scope at the sun.
First Test.
I have installed my 18mm-55mm Canon Lens while I figure things out. I later swap to the Samyang 300mm lens. I'm using the Pinebook Pro with KStars.
Taking advantage of the shadows from the sun it was relatively easy to get the sun into frame. The focus was a bit tricky but after some fettlling all was good. The first few photos are in B&W mode, I forgot the sun is in colour.
The images are the Sun at 18mm, 55mm and 300mm. I didn't have an unobstructed view when taking the shots so you'll have to excuse the trees. I managed to get quite a good video of the Sun tracking past the trees with the 18mm-55mm Lens.
Second Try.
The Clouds got in the way most of the time so I enver managed to get anything good. However I did have a clear view of the Sun. I also found out that I need to have good WiFi signal to make things run smoothly. Additionally I need a power-pack......
SER Files.
SER files are used for planetary, lunar and solar captures and SER player allows these captures to be viewed in the same way AVI files are viewed with a standard video player. KStars records the videos as SER files. I have downloaded Ser Player to view and export these files.
Step 37: Optional | the Power Pack.
After the first few attempts at using The Micro Scope two things became appartent. Firstly I need a good WiFi signal otherwise trying to adjust the focus etc becomes very difficult due to the lag. Secondly, running mains cables out through doors limits where I can go. Making a powerpack, and including a WiFi router as part of the pack will solve both these issues.
Power!
Before we can pick a battery pack we'll need to understand the power requirements of The Micro Scope. I have a bench DC power supply which I have hooked up to The Micro Scope. The PSU has been set to 12v and the Scope has been powered up. The PSU has a current display which we can reference to see how many amps are being drawn by the Scope.
WiFi.
We don't need a Multi-Port Pro Gamer 5G RGB WiFi Router. We want small, cheap, and low power. After spending a few hours researching options I have chosen the low-cost and tiny GL.iNet GL-MT300N-V2 (Mango) Wireless Mini Portable VPN Travel Router*. The router is powered via USB and requires very little power to run, 5W. This should be perfect for the Power pack.
The Battery.
The Scope requires ~0.6A at 12V (7.2W), the WiFi Router requires ~1A at 5V (5W). Together our engery needs are approximately 12.2Ws an hour. The battery I have chosen is a 12v 15000mAH LiPo*, which includes a charger. The battery provides 180W of power allowing for ~14 hours of continuous use. That should be more than enough.
Assembly.
Print out the parts with the same settings as you have been using for the other printed parts. I have chosen to use XTCF-20 again, but you can use anything really.
I suggest purchasing and checking the dimensions of the DC-DC Buck Converters before printing the parts as the two I had had different mountings patterns. You'll be able to adjust the positions in Fusion if you downloaded The Micro Scope Build Pack.
Be extra careful when wiring up the pack, check the polarites. I tried to use different sized DC Jacks so that I couldn't plug the charger into the output port by accident.
I put in a switch on the battery output, in addition to the switch on the battery, because the battery pack needs to be on for it to charge. I also made a short jumper cable to run between the power pack and the scope.
Power Up.
I have configured the router as an access point and if I plug a cable into the WAN port it will forward an internet connection. I added the access point information to The Micro Scope RPi configuration and set it as priority 1 so the scope will attempt to connect to the router before trying anything else. The router takes about 30 seconds for the WiFi to come online and it should be powered up first before turning on the Micro Scope.
*Afflink
Step 38: OutSide | the Sky at Night.
I'm pretty sure that somewhere it is night time, just not where I happened to have been. Anyway, technicalitites aside I'm outside. The Micro Scope is powered on, the new Power Pack is switched on, the WiFi is working and we are all connected together. The Micro Scope is pointed at the biggest star in the sky, the Sun.
It is mid-January and I'm in England. I managed to get about an hours worth of sunlight before the clouds closed back up and called an end to the excursion. I recorded about 6gb of video data of the sun. Some of it was clear and some of it was not. To remove all the bad frames and end up with a final image there are a few programs we need to run the data through.
Planetary Imaging PreProcessor (PIPP).
The PIPP cleans up the recorded .ser videos. In this case I combined all the clips into a single video.
In the above video you can see how the PIPP has processed the images and kept the Sun centred in the frame.
Registax.
Registax processes the video and combines all the frames into a single image. This works great for low-light deep space images. I was hoping it would bring out some detail in the sun from the data I have captured. However, I think I need to work more on getting the camera focused better. This is where my inexperience comes in!
The final photo from Registax is still pretty good though and I am happy with progress. Next time it will be dark where I am, and light somewhere else!
Step 39: Outside | in the Dark!
Fast forward to February the 22nd. The skies have cleared and the Moon is up. The Power pack has been charged and the Micro Scope setup outside.
I have set the camera resolution to 4056x3040 in the INDI control panel. I have had to adjust the white balance so the image isn't washed out too.
I spent a good few hours getting images and by the end of the session I had over 20gb of data. The raw data has been run through PIPP and an image of the Moon compiled.
I discovered that setting the camera mode to greyscale I could get a much higher datarate without any real loss of image quality.
There is still a huge amount for me to learn. This has only been my second time outside where I have been able to get useable results. I'm fairly certain I am using the Preview equivilent of Astrophotography by recording the stream. There is a whole imaging tab in INDI that I need to explore.
This is not the end, this is only just the beginning......
You can download the original 1.4GB .SER file here | Download.
Step 40: Epilogue | Modifications.
This Instructable has tracked the development, building and testing of The Micro Scope. Changes have been made to the design to fix any issues encountered, to add in some features and to make things easier for anyone else who would like to build their own Micro Scope.
Some of the changes include.
Under-cutting bearing faces.
- Under-cutting the bearing faces makes post-process sanding of the faces considerably easier.
Added access to the RA belt.
- I found it a little tricky to get the belt onto the RA pulley as the belt kept being pushed down. Adding an inspection hole in the RA Bottom provides room for a tool to keep the belt from being pushed aside.
Corrected DEC Arms Screw positions.
- I made an error where the cover hole aligned with the bearing clamp bracket hole below, this can be seen in the assembly photos. This meant I could not ream and thread the bearing clamp hole and could only use four screws and not five as intended.
Added Air Vents for the Raspberry Pi.
- The camera assembly felt warm enough to warrant slots in the GPS Cover for passive air flow inside the Raspberry Pi Housing.
Added alignment notches.
- Slewing The Micro Scope into Polar Alignment can be a bit hit and miss. Adding notches which align when in the correct orientation should make this process less reliant on laser-eyeballing.
Simplified the electronics package.
- Taking out the RTC and WiFi modules removes unnecessary parts. The GPS on the RPi and the Bluetooth on the Wemos & RPi do the same job, plus much more.
These changes have all already been applied to the CAD and the drawings, plus the BOM has been adjusted accordingly. Any changes I make in the future will be added to the updated design files too. All the design files are available as part of The Micro Scope Build Pack. Details of which are on the next steps!
Step 41: Update | 21/03/2021 | Universal Tripod Fixture.
The Universal Tripod Fixture adapts The Micro Scope to be compatible with standard 1/4 - 20 UNC threaded photography & videography tripods.
The assembly is very similar to the AEM & Tripod. A DC jack and RJ12 connection is included in the Fixture. Follow earlier steps to match the wiring.
I'm using a Pronged T-Nut to help spread the load. I fet a small hex nut was probably not upto the task of holding the weight of the scope securely on a tripod. The additional size of the T-Nut ensures there is no chance of part-failure.
The CAD, BOM & Drawings have all been updated with the new parts. The Universal Tripod Fixture is only available as part of The Micro Scope Build Pack.....
Step 42: The Micro Scope Build Pack.
Excited about making your own Micro Scope?
I have put together a pack of all the parts you'll need to build your own Micro Scope. Including a list of all the electronics, a list of all the fixings, assembly drawings, hole and thread drawings and of course the full Fusion 360 CAD.
Using the Build Pack you'll be able to take advantage of the Adjustable Equatorial Mount, which is not included in the basic STLs download from Thingiverse.
The Fusion 360 Master Files allow you to edit, modify, and or add features to The Micro Scope. You'll be able to export updated STL files and print your own modified parts!
The Micro Scope Build Pack.
- The Micro Scope Fusion 360 CAD Master Files.
- Reference Drawings of the Assemblies.
- Reference Drawings Detailing Hole & Thread Dimensions.
- The Adjustable Equatorial Mount STL Files.
- The Adjustable Equatorial Mount STEP Files.
- The Adjustable Equatorial Mount Fusion 360 Master Files.
- The Micro Scope STL Files Complete Pack.
- The Micro Scope STEP Files Complete Pack.
- A Complete List of Components.
- A Complete List of Fixings.
The Micro Scope Build Pack is available to download from Cults3d.com
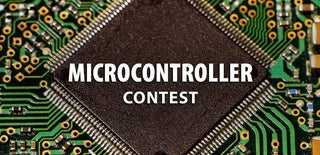
Second Prize in the
Microcontroller Contest