Introduction: The ULTIMATE Diy Boombox!
This thing is simply a gigantic ipod boombox......just way doper! I wanted to fully build a blasting boombox for my garage and here it is. The enclosure is made of 3/4" mdf and then I used some rattle can truck bed liner to paint it. Yup, truck bed liner. It came out so cool. All the wire work would be a waste if you couldn't see it so I added a plexiglass cut-out on top and mounted the controls and buttons to it. Also, it has a DC jack for charging and a 3.5mm audio jack to accept any audio source. The amp has the ability to take a mic input as well so you can possibly plug in a guitar or a microphone if you feel like it. Might be pretty awesome to plug in a mic and amp up your didgeridoo too!
Material needed:
-MDF 3/4" x whatever you want.
-plexiglass (I used some thin stuff from home depot)
-Wood Glue
-sand paper (I bought a multi grit kit from wallyworld)
-various little wood screws that you can scrounge up
-speakers (my sub is a pyle 8" and the mids/tweets are some boss 6 1/2" components. Both found on amazon for a STEAL)
-amp (also found on amazon which was normally 280 bucks that I scored for 70!)
-momentary push button switches if need be (I got mine from ebay on the cheap)
-good quality wire (I had a spool of 18awg black and got the 18awg red and 12awg red from home depot)
-1/8" heat shrink (whatever color you choose)
-solder
-zip ties
-truck bed liner spray paint (I found mine at home depot)
-primer spray paint
Alright....lets do this!
Step 1: Get the Electronics
I bought a Pyle PT1100 from amazon. Its a 1000w beast. Pyle makes their stuff very plain jane so its perfect for ripping apart. The components inside are just like if I were to buy some diy amp kit but way cheaper. The transformer would've cost me like 45 bucks alone. The sub is a dual voice coil 4 ohm 8" pyle blue wave. Mids and tweets are a component set from boss, so it comes with the crossovers too. These are "good" speakers from a lower quality brands. Any type you use will sound good when you good quality wire with good quality solder joints. The sky is the limit on the components...I chose these due to the fact this just a garage blaster not a center piece in my home.
Step 2: Build and Paint the Enclosure
I started off building the front panel first. Lay out your speakers to your liking. I didn't get too many pics during this portion of the build 'cuz it was so freakin' messy. My mdf is the pre-primed kind from home depot. 3/4"x11 1/4"x8'.
Drill nice clean pilot holes and use a router to route out the speaker holes. I made a circle jig out of scrap plexiglass (If you want more details on making one message me and I'll hook you up). After routing the holes out use a 45 degree chamfer bit to get that nice beveled edge. My garage was COVERED with dust and so was I after doing this. If you can do this outside I would recommend that because I looked like I had just got done shaping a surfboard or something after this step.
Measure out the top, back, bottom and sides to start making the actual box. I glued and clamped the front, sides, top and bottom and left the back open for wiring and access. This process didn't get pics like I said due to the fact that I had to work quickly and it was messy. No screws involved...just glue. Be liberal with the glue.
Let it dry.
Take the router to that sucker, again with the chamfer bit, and route all the corners off the box. I wised up and did this on my patio and once again I was COVERED in this light mdf dust. It gets everywhere.
Sand, sand and sand. Use a power hand sander and just have at it! I used 120, 220 then 400. Be careful not to take your corners off. Just soften 'em. Try and get everything nice and smooth. Dust her off.
PRIME! I made a "paint booth" in my garage by using plastic drop cloths duct taped to the ceiling and on the floor to keep the joint clean. Shake up the primer cans and spray nice thin and even coats. Don't lay it on too thick or it'll take multiple days to dry. I found this out the hard way.
Sand, sand and sand. Take it back out to the already thrashed patio and have at it. I used 220 all over. Repetitive, I know, but its well worth the effort in the end.
PAINT! Break out the truck bed liner cans and shake 'em up. Apply nice thin and even coats once again. I did three coats and I believe it took like 3 cans to complete.
I got a little ahead of myself and installed the speakers before I got a pic of the finished product, but you get the idea.
Step 3: Explode the Amp!
Here's the fun part. Fully take the amp apart. Label all ribbon cables with a small permanent marker number on the boards themselves. 1-1, 2-2, 3-3 and so on. This may seem daunting if you know nothing about electronics, but it's literally as simple as making sure to mark where all the connections go so that you don't get confused later. Take pics of EVERYTHING. You will most likely have to refer back to the pics later.
Desolder all ribbon cables and the pots that you'll be mounting on the plexiglass later. I like to use a solder sucker then use some desolder braid to get the rest of the solder off. Do not be too rough with this process and take your time. If you're too rough you could possibly damage the solder points on the board and then you'll have to go into repair mode....and we don't want that. We're removing the ribbon cable and replacing it with our own wire because most likely the ribbons won't be long enough to accommodate a new lay out that differs from the original amp enclosure.
Step 4: Lay Out the Plexiglass and Amp Board
Lay out your back panel. I chose to keep the crossovers close to the amp's speaker inputs. The other boards are not shown due to the fact that uh, well, er I forgot to take a pic of that. OOps. You'll see in upcoming pics what's what.
Plexi lay out, is by your preference. I found middle, then spaced everything out at 1.5" apart. Additional switches are for selecting inputs which I placed in between the first row. To drill the plexi use a little pilot bit and then use a step bit to to increase the hole size to the appropriate size for your components.
I opted to use a dc jack for charging because it seemed like it was going to be difficult to try and cut a little bitty rectangle for the usb. To wire a dc jack from a usb cable, just cut the end off and strip it back 'till you see the four wires. Use only the red for the center of the jack and black for the casing. Cut the rest off. Yeah, its that simple.
Wiring the 3.5mm audio jack is also very simple as well. Take any rca jack cable and cut one end off. Split into 2 pieces and strip the casing off. You'll be left with a conductor and a ground for each side. Twist the grounds together and solder to the center casing. Left tab (typically square) gets the white wire. Obviously, the red goes to the right. Easy too, huh.
Step 5: Wire the Lid
Up next is wiring the plexi panel and running the wires to the back panel. Label or number your wires. You can buy some wire labels from home depot. I personally got all the components mounted and then went from left to right and numbered each termination 1, 2, 3 for pot one 4, 5, 6 for pot two and so on. WRITE THIS DOWN. If you forget what's what....well that would just suck.
You can also get adhesive cable tie mounts from home depot too. These are perfect to zip tie to.
Solder and all wires by tinning the termination point and the wire then together. Use your 1/8" heat shrink on all terminations. A "third hand" is wonderful for doing this. Solder all wires BEFORE mounting to the panel. Then mount them.
Do your best and routing the wire. Crossed up wires look ugly and unprofessional, but are sometimes hard to avoid. Try and keep the neatness on the visible side. Nothing in electronics is more impressive than perfect wiring. Its cool to waste zip ties. Sometimes I'll use one just to hold the wires and cut when I'm done.
Once you've got your fat bundle of wires looking tasty, run them along the corners of the box and to the back panel where we'll terminate later.
Split that python of wires!
Step 6: Wire All the Back Panel
I'm going to keep this step nice and simple.....
Looking at the pics explains it all. Seriously, split your wires up to where they need to go (cuz you labeled them and took pics remember).
Solder some short little "break out" wires to the boards. I used some nice stiff 22awg wires. Strip the end and stick it in the hold. Solder to the pads and trim them as short and the other solder joints. Dip you friends tooth brush in some rubbing alcohol and clean the new joints up.
Now, strip the break out wire and the terminating wire and tin both ends. Don't forget the heatshrink. Bend the stiff break out wire so its in a good position to solder them together. Yeah yeah this is easy, right.
Finally use a heat gun to shrink up the heat shrink.
Step 7: Finish!
Connect the remaining power wires from the transformer in the same manner as the previous step AND THEN.......
Take a good look at all wiring to make sure all is legit. If you deem them good to go, look at them one time just to be sure.
FLIP THE TOGGLE!!!
Your boombox should fire up perfectly if you labeled everything correctly. Mine did of course. Plug in your ipod, throw on some Rebelution and kick back with a few beers as you enjoy your new one-of-a-kind-super-sick boombox!!
ENJOY
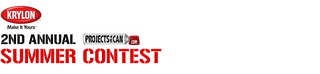
Participated in the
2nd Annual Krylon Summer Contest