Introduction: This High Voltage Click-Clack Toy Rocks!
Here are two electrostatic versions of a retro Click-Clack toy that were popular in high schools back in '70s. Version 1.0 is the super-budget model. Parts (excluding the power supply) amount to almost nothing. A description of the more expensive and upgraded 2.0 version pictured on the Intro page appears at the end of this i'ble.
I used conductive spheres to shuttle electric charges between the poles of a high voltage (HV) DC source. This shuttle assembly was made from two, foil-covered spheres joined by a non-conducting, plastic tube. The assembly was sandwiched between two stationary, dumbbell shaped electrodes. When the upper dumbbell was grounded with respect to the negatively charged lower dumbbell, the shuttle began to bounce between the HV poles with a clacking noise as charges were transferred from the lower to the upper electrode. This rocking motion completed the HV circuit.
I powered the project with an electronic air ionizer purchased at a rummage sale; but other sources of HVDC, such as a Van de Graaff generator could be used to rock this clacker. For a video clip about the project, click here.
Safety
If you choose a commercial air ionizer as the power source, use a model powered by a low voltage AC adapter. A line powered ionizer can be a serious shock hazard!!
* * *
Step 1: Tools & Parts
You probably have many parts to build the super-budget clacker among the disposable items left over from home delivery of fast food that end up in kitchen drawers. Exact dimensions are not crucial; but the shuttle assembly must be balanced carefully before it will rock with fairly steady beat. (With some minor tweaking, the 2.0 version can serve as a metronome for musicians : >D).
You will need: white and CA glues, cellophane tape, small hammer, scissors, a ruler, a small metal saw, an electric hobby drill with 1/8" and 1/16" bits, an electrical continuity tester as well as the following items. Remember, for this type of project there's always room to improvise.
A. Shuttle Assembly
Spherical Core Forms (2) Newspaper sheets to make ~1" dia balls.
Al Foil Foil (for wrapping hot heros to go) to
cover cores.
Dielectric Connecting Tube (1) Just a geeky name for a 5" x 1/8" non-conducting,
plastic straw (or use a 1/4" dia empty ball point
pen cartridge for better support).
Axle (1) paper clip.
B. Stationary Electrodes
Spherical Core Forms (4) Newspaper sheets to make ~1-1/2" dia
balls.
Al Foil Foil for covering cores.
Connecting Rods (2) 6" x 1/8" lengths from a heavy duty coat hanger.
C. Stationary Electrode Mounts
Dielectric Support Columns (4) 5-1/2" x 1/4" thick shake straws or something similar.
Stand-offs (4) Small plastic or stryo thread spools w/1/4" center hole.
Mounting Hardware (8) 1" x 18 gauge nails.
D. Shuttle Mounts (2) 4-1/2" x 1/2" dia, x-tra thick, smoothie straws or
something similar.
E. Project Base (1) Whatever works; try fast food take-out tray or 1/8" cardstock
cut to appropriate L&W.
F. PowerSupply & Accessories
HVDC Source (1) Small, commercial electronic air ionizer, such as the Micronta
Air Purifier (Radio Shack cat. no. 63-643) as shown
in picture or Van de Graaff, etc .
Input Terminals & Leads (2) Color coded, plastic push pins & insulated wire.
Step 2: Prepare 1st Core
Begin by prepping cores for the electrodes and the shuttle assembly using a composite of white glue and newspaper pages. This composite will solidify to about the hardness of a golf ball. (Note : the cores must be firm so each charged sphere of the assembly will contact the stationary electrode with that authentic CLACK ! before rebounding. Initially, I used rolled-up balls of Al foil -- much easier to make, but they didn't reproduce the right sound.)
Rip a full sized page into 1/4 sheets. Apply glue to one side and squeeze into a tight ball. Use just enough glue so the newspaper is moist but not dripping. (Too much glue? Just wrap another dry sheet around the ball.) Repeat this step until you have built up a 1-1/2" dia core; about four to five sheets are needed.
Continue rolling and squeezing the core thoroughly until the glue completely saturates the layers of newspaper. Squirt glue under any loose corners on the surface. After 20 - 25 min of smoothing out bumps, the core should feel really compact and look more or less spherical.
Step 3: Complete Remaining Cores
The remaining three electrode cores and the two shuttle cores are made the same way. However, use only two to three sheets for each shuttle core. Let the cores dry for at least day or two.
Step 4: Assemble Electrodes & Cover With Foil
Initially, I glued individual strips cut from the sandwich wrapping on the cores to make the conductive spheres; then smoothed out wrinkles by rolling the spheres on a desktop. After drilling one 1/8" hole in each 1-1/2" dia sphere, gluing and then inserting the connecting rod; achieving electrical continuity between the connecting rod and both spheres required more foil patches followed by more rolling to remove wrinkles... So forget this step, it's just too much work.
* * *
Here's better approach: cut a large square of foil and wrap it tightly around the sphere and rod assembly; it's not as neat, but it works. Also, the foil keeps the assembly together until the glue dries. :>)
Step 5: Check Electrical Contact for Stationary Electrodes
Obtaining continuity shouldn't be a problem with the the quick fix from the previous step.
Both foil-covered assemblies should have minimal resistance as indicated on the tester.
Step 6: Assemble Dielectric Supports
Insert one end of each thick shake straw into the center hole of a thread spool. Wrap several layers of tape around the straw if the hole is too large for a snug fit. Repeat this step for the remaining 3 straws. Construction Tip : straws that have vertical lines along the length make it easier to line up the mounting nails in the next step.
Step 7: Attach Supports to Stationary Electrodes
Hammer a 1" x 18 gauge nail perpedicularly through a straw about 1-1/2" from the base into to each sphere as shown. The nail will secure the straw to the lower stationary electrode. Repeat this step for the remaining 3 supports, BTW, it's best to complete this assembly on a desk or tabletop.
Now repeat these steps w/the upper stationary electrode. Adjust the height of the straws in the spools as needed to make the entire structure level on a flat surface.
Step 8: Mount Stationary Electrode Assembly
Cement spools to a convenient base, I used a scrap of 1/8" cardstock cut to size.
Step 9: Charge Shuttle Asembly
Drill a 1/4" hole in each 1" dia sphere. Insert spheres onto each end of the pen cartridge; secure w/glue. Locate and mark the balance point of the assembly. Carefully stick a push pin through this point to make the shutle axle entry hole.
Straighten a paperclip to make the charge shuttle axle. Insert one end of the clip perpedicularly through the hole. I made bases for the shuttle mounts from 1/2" x 1/2 dia wood plugs cut from a dowel and inserted into one end of each straw.
Important Note: the shuttle assembly must be equidistant from upper and lower electrodes so that each sphere of the shuttle contacts a stationary sphere simultaneously (it's embarrassing to say how long it took to [almost] achieve this requirement! :> o). Once you determine the optimum shuttle height and repositioned the stationary electrodes as needed, hold the mounts in position and mark the location; drill a 1/16" hole in each straw to accommodate the axle. Glue mounts to the base. Lastly, insert the shuttle-axle assembly between the mounts and lock the in place by bending axle ends at 90 degree angles.
Step 10: Final Assembly & Power on Procedure
Use push pins inserted into the upper and lower stationary electrodes to secure HV leads to your power source.
Initially, when power was applied, the shuttle was as stiff as an arthritic knee in the winter. The holes in the shuttle mounts were binding the axle; one charge collector keep bumping a support column and the other collector still wasn't contacting the stationary electrode.
After correcting these problems, the shuttle began to oscillate after slight push but without that trademark CLICK-CLACK sound; so on to version 2.0...
Step 11: The Clacker 2.0: Upgraded, Accessorized & Wireless!
Both stationary and shuttle electrodes for the 2.0 version were made from birch wood balls sprayed with conductive metal paint. Connecting rods between the stationary electrodes were sheathed with heat shrink to reduce corona loss.
Quarter inch acrylic rods with a painted wood ball glued to each end supported the stationary electrodes and preserved the project's dumbbell design. Dielectric and shuttle assembly mounts were similar to those in the budget model. Color-coded, HV leads were used to apply power from the ionizer in a base made from a discarded jewelry box.
I accessorized the project with four ceramic insulators as stand-offs and used a 1/4 W neon bulb as an power-on indicator. The yellow furballs were placed near the lower electrodes to indicate electric field intensity the same way long human hair flies upwards near a VdG discharge terminal. But these guys with their buzz cuts weren't very useful. :>(
The Clacker 2.0 can be powered by this homemade VdG (output: ~50 kV @ 2 uA) pictured here; or the commercial air purifier (output: ~7 kV DC @ 35 uA) shown in Step 1. Power transmission was completely wireless using a VdG. BTW, a ground return connection to the VdG chasis wasn't needed. The shuttle rocked from the ion stream that passed through the air to the small antena (made from a headless finishing nail) on the upper electrode.
If you want to use the 2.0 clacker as a metronome, adjust shuttle tempo by changing the distance between your VdG and the antena. Slight changes in horizontal distance will produce big changes in tempo so you can keep the beat to those various Old School jams from back in day.
Rock On!! (:>D
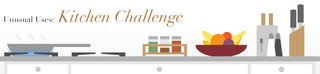
First Prize in the
Unusual Uses: Kitchen Challenge