Introduction: Toy Car Shelf
If your 9 year old kid is anything like mine, they've got a big box of toy cars. Whenever they want to play with a specific one, they sift through the box for a while and then declare it lost. A helpful parent then has to take a valuable few minutes of their day to sift slightly deeper and find it.
To solve this terrible problem, we decided my son would construct a display shelf for the wall of his bedroom.
Step 1: Work Out the Dimensions
First look for a handy space on the wall where you want to put the shelf. After moving a few posters we found a space around 900mm wide and 900mm high (Sorry to the good people of the USA, Liberia and Mynamar who still use the imperial system).
Given 900mm was about our maximum width we/he then lined up his cars on the floor in lines about 900mm long. There were about 8 rows, so we decided on 10 shelves to allow for future expansion, We measured the widths of a few cars, and decided our shelves need to be about 40mm deep.
We were guessing we'd be using wood around 12mm thick. Therefore our space between shelves should be around (900mm - (10 shelves *12mm)) / 9 gaps = 87mm. This seemed like a reasonable number - the tallest truck was about 50mm high.
Step 2: Go to the Hardware Store and Gather Your Materials
Armed with our rough dimensions in our heads we went off to the hardware store to find something to start the construction. We were willing to vary the dimensions about to fit whatever they had in stock.
We found dressed (smooth) pine board that was 42mm x 12mm x 1800mm. Since they were exactly twice the intended length of our shelves, we bought 5 of those.
We knew we were going to need 6 x 900mm lengths of dowelling to hold the shelves together. If you are making much wider shelves, I'd get 8 lengths of dowel. If you are making narrow ones - say 450mm, then just get 4 lengths, We selected 6mm dowelling, chosen by the scientific method of holding various diameters up against the shelving wood and deciding what looked about right.
Step 3: Measure and Cut
First check all your wood is exactly the same length. We wrongly assumed it was - actually they varied by a few mm. Once we figured that out we cut them all to exactly 1800mm.
Do all your marking at once, before you cut. Since you are marking where to drill the holes it is really important to take you time over this step, as the more accurate you are here the better the end result.
We decided our dowels were going through the centre of each shelf, and 30mm from each end. Each of our boards was 2 shelves. Therefore we needed marks at 30mm, 450mm, 870mm, 900mm (the cutting line), 930mm, 1350mm, & 1770mm. You'll need to adjust these, based upon the width of your shelves.
Don't measure every board! The room for error is too great. We measured these marks on just one board, then held another board against it and transferred the marks across. Now we had 2 boards with identical measurements. Sandwich all the boards together as shown, with the two marked boards at the top and bottom of the stack. Take your time to get the ends all lined up, then draw a line between the marks with a straight edge. Use a soft pencil and don't press too hard or you'll need to spend a lot of time sanding later on.
Now cut the boards in half. Since it was my son doing it, I got him to use a hand saw. If I'd been doing it myself I would have used a power miter saw. This makes a cut 2-3mm wide, so I would have needed to keep that in mind when doing the measurements above.
Step 4: Measure in for Your Holes
You need to decide how far in from the sides you want your dowels to be. 7mm seemed like a good gap to us, and therefore the holes needed to be centred 7mm + 3mm = 10mm in from each side (3mm is the radius of the dowel).
You don't want to measure in on each board individually - the room for variation is too great. If you have a wood scribe tool, or combination square then use that. If not then just find something 10mm wide, hold one edge against the edge of the board and mark on the other side.
Step 5: Drill Your Holes
If you've got a drill press, use it. You need the holes to be as perpendicular as possible. Otherwise google how to drill a straight hole without a drill press - there are a few common methods that are all good.
Make sure you've got a sacrificial piece of wood to drill into, otherwise you'll tear out a bit of the wood on the bottom when the drill goes through.
We had 60 holes to drill which is quite a lot when you are a kid without a drill press. Take a break halfway through to avoid getting sloppy.
We also found that our 6mm dowel wouldn't go through our 6mm holes without a lot of force. You need it to be snug but not too tight as you need to slide the shelves on 6 dowels at once during assembly. 6.5mm seemed to do the trick, Check this out on a scrap piece of wood before you start,
If you don't want the dowels to stick out the top and the bottom, then just drill halfway through on the top and bottom boards. Otherwise you are just making every shelf identical.
Step 6: Pre-assemble
Slide all the shelves on to make sure it all looks good. Take it inside and hold it onto the wall to make sure it fits like you thought it would.
Once we were happy we figured out the spacing between shelves, and how far apart the bottom edge of each shelf was going to be and took it all apart again. SInce we'd decided to stick some dowel out the top and bottom, the spacing was slightly smaller than what we'd figure early on, but still good.
If you plan to paint or varnish it with a brush, I'd do it at this stage as it is going to drive you nuts if you try it once it's assembled. If you are spraying it, then do it at the end.
We then took it all apart.and marked the shelf spacing on what was to be the back of each dowel.Again we held them all together and marked across all of them at once.
You then need to slide it all together, lining up the bottom of the shelves against those marks on the dowels. This made sure our spacing was all consistent.
Step 7: Glue or Nail It Together
We used a hot glue gun and put a blob at the back of each dowel on the underside of the shelf. The outsides were done first, and then the middle last, taking care to make sure the shelves we lined up with those marks on the dowels. You could probably use some less ugly glue, or a very fine panel pin nailed though the back of the shelf and into the rear dowel. Maybe even a staple if you have a staple gun with long staples.
Once the glue has set, you're all done. Spray paint or varnish it if you like. If you pre-painted it, you might need to touch up the paint on the dowels.
Step 8: Hang It on the Wall and Load It With Cars
We made some hangers using some ugly bits of metal strapping screwed to the back of the top shelf and then screwed to the wall. This was because he was excited to hang it up before dinner tiem. There will be much better ways of doing this, depending on what your wall is made of. Have a look for floating shelf fasteners in the hardware store. It isn't going to hold a huge weight so you can go for some pretty small fasteners.
That's it - all done. My son did most of the work himself with my guidance on the measurements and helping him hold the drill straight up and down. SInce it was finished he's brought a few kids home from school to show them what he made. I've also noticed that a wider range of cars get played with as they are all on display.
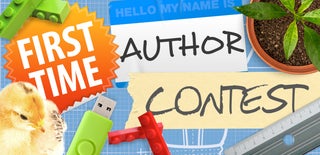
Participated in the
First Time Author Contest
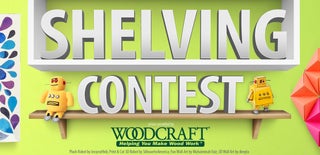
Participated in the
Shelving Contest