Introduction: Transparent Maraca: 3D Printed in Vase Mode With Upcycled Plastic Filling
During an extended spell indoors, I've been collecting and making percussion instruments. It both helps pass the time, and reassures the neighbours that I'm still alive.
Among them is this 3D-printed maraca with a simple geometric design, which is not only printable without supports but also - to my absolute delight - works in vase mode.
A large nozzle is the key to success here. I'm using a Creality Ender 3 with an E3D Volcano hot-end and 1.2mm nozzle. Print time for the main shell is under 3 hours, but it's very sturdy and the single spiral wall is nicely resonant. This shaker is surprisingly loud!
Supplies
I used transparent PLA filament for the main shell because I wanted to see the filling, with a solid fluorescent colour for the plugs because I like shiny things.
The filling can be whatever you like, but I chose to upcycle some waste plastic. A little superglue holds it all together.
Step 1: It's an Egg on a Stick!
I opted for the simplest design possible: just two shapes fused together.
The handle is a plain old cylinder and the body is a stretched sphere. The simplicity meant I could model this very quickly in OpenSCAD and use parameters to tweak the sizes.
What looked most pleasing to my eye was an egg shape that is 50% taller than it is wide.
With a height of 120mm, and a handle of 80mm, this should be a good handheld size and comfortably fits in the Ender 3's build area.
Attachments
Step 2: You Can See Right Through Me
My Ender 3 has an E3D Volcano hot-end with a 1.2mm nozzle. I already knew that this makes a very tough single layer shell in vase mode and, with thick layers printed at high temperature it does a good job of keeping transparent filament... you know... transparent.
These vases (not my design) were printed at 200C (left), 215C (middle) and 230C (right) with 0.9mm layer lines, so I already knew I wanted to go hot and fat for this project.
Vase mode, however, is usually used for shapes with a wide neck like, well, vases - not for spheroids that taper back to a point. How could this possibly work?
Step 3: Everyone Loves Vase Mode
At first I thought about making the maraca in two halves. That somehow seemed like less of a challenge. It was only after a few tests that I realised that if one half of this perfectly symmetrical spheroid was printable, the other half must also be printable too.
My first result with 0.9mm layers gave a Spirograph-type pattern atop the dome. As the model narrows, the layers do not overlap enough to make the plastic adhere and, while very pleasing to look at, this construction fails on practicality.
With 0.6mm layers, the results looked better at first with only the very top layers failing completely, but there was still clearly too much overhang towards the top of the dome and the layers had not fused well enough. This one quickly became a Slinky.
A whole egg test at 0.3mm made it right up to about 8 layers (2.4mm) from the top before the structural integrity of the spiral failed. Better than I expected, and definitely usable!
I decided that having a small plug at the top of the maraca would not be a big deal. It's only about 10mm across which is the same diameter as the handle so, through happy coincidence, it's still balanced and symmetrical. Plus, there's no longer any question of how to put the filling inside!
At this resolution, the transparent filament is a little more opaque than I'd like but you can still see colours and shapes through the wall, and the slight opacity actually gives it a nice shimmer. Not exactly what I was going for, but I like it.
Step 4: Get It Off
In the two tests shown here, the egg on the left was printed in a spiral directly onto the build plate. Removing it was impossible without putting some strain on the opening, and it left that side a bit messy.
On the right, I used a raft but - ultimately - was not able to remove it confidently. While a thick nozzle creates very strong parts, it also makes very strong additions so rafts and supports can be rigid and difficulty to remove.
But if the egg shape can be printed in one piece (minus a small, handle-sized opening at each end) - there's no reason it has to print directly onto the build plate, right?
Step 5: Top Heavy
I flipped the model upside down and went for it. Bed adhesion concerns? Pah! With a big fat nozzle, it's going to stick!
To make a fixed opening at the top of the model, rather than just let the print fail towards the top of the spiral again, I made an adjustment in the slicer. I already knew it was good to 2.4mm from the top, so I just told it to stop printing there. The model is 190mm in total, so it stops at 187.6mm. (In Simplify3D: Advanced -> Stop printing at height).
That meant I didn't need to do any circle math and, later, fail to adequately explain that circle math here.
The minimum layer time was set to 15 seconds in my default profile. This meant the spiral grew very slowly, and this could probably be increased - I just didn't consider it. However, it was still under 3 hours to print the whole shell - at 190mm tall, and rock solid!
Step 6: I've Got Something to Put in You
This one piece shell is great and all, but now it has a hole at both ends, and it needs to be filled in such a way that the contents won't fly all over you when you're playing.
It's also desirable to only have filling within the egg part of the shell. It won't sound very good rattling around inside the hollow handle, so it's not as simple as printing a solid layer at the base to close the handle, or capping both ends.
I designed a big plug which gets shoved right up the hole in the bottom. I very carefully named it "Big Plug" and never, ever referred to it by any other name.
The squished layer at the end of the handle needed a little sanding on the inside to help get it in. I specifically use a cheap rotary tool with slow speed setting to prevent melting PLA when sanding. At 500rpm, it's fine.
It's a tight squeeze, but with a bit of persistence you can get it all the way in.
Attachments
Step 7: It's a Little Bit Funny, This Filling Inside
I wanted to use waste plastic for the filling. I have a lot of failed prints that I've been keeping in a box for such an occasion, and quite a few short lengths of filament from ends of spools.
Rice is a traditional maraca filling, so I chopped the filament into short lengths resembling colourful rice grains. In the end I used about 20g of filling, which takes much longer to chop up than you'd expect!
For another filling, I literally smashed up some failed prints with a mallet to make plastic crumbs. I wanted some larger chunks to give the second shaker a different sound.
Step 8: Shake It Baby!
For the top plug, I used the same file as the Big Plug but told the slicer to only print a few layers. After some experimentation, I found 5mm to be large enough to handle, but not so deep that it was visibly hanging inside the maraca.
The spiral wall means you can sort of twist this plug in like it has a thread, but don't be fooled. It give you a false sense of security, and it's just waiting for you to give it a good shake before wriggling loose. Video evidence attached.
Use a small amount of superglue to hold the top plug in place, and everything's groovy!
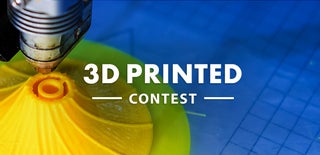
Participated in the
3D Printed Contest