Introduction: Treehouse on Two Trees
I live in a place with many pine trees - every garden or back yard has at least two - but had never seen or heard about treehouses. When I saw one while surfing the internet I was instantly hooked. At first, I spent half a year gathering all the info I could find and daydreaming, yet feeling too small to commit to such a complex project and thinking that after enough time the "passion" will fade away. As things got worse, I started designing a treehouse with google sketchup, putting "on paper" the plans I would pick from the internet along with some ideas of my own.
Finally, 2 years ago, I decided to give it a shot. I gave myself a 50% chance that it would end to be a failure in which case I would have to tear it down (and cope with the dissapointment of my two daughters). Happily, it all ended well, and I am glad to share the whole project with you. At the time of posting this instructable the treehouse is still under construction, missing a ladder, deck rails, roof shingles and a few minor things here and there (fascia boards, wall trims). Most of them will be finished in the coming weeks - the roof shingles may have to wait until next spring, depending on how early the winter comes this year
The treehouse floor ended up roughly 2.2 X 1.6m (7'x5') and there is a 2.2 X 1.0m (7'x3') deck on the front, both sitting on a 2.2 X 2.6m (7'x8') platform. All up weight is 450Kg (1000 pounds). It is relatively small & light compared to what you will find in the internet. It took me 2 years (with some looong breaks) , working mostly on free weekends and some afternoons here and there. The total cost was 1,600 Eur including materials not used or purchased by mistake but excluding any tool. You can get away with much less if you have access to cheap wood.
Below you will find in detail all the steps it took me to complete. If you have already settled on a treehouse project you can skip steps 1 to 3, as you probably already know what tools, materials and plans you need.
Important note
The materials you will see in the next steps are chosen having in mind the small size/light weight and the generally mild weather here, so mind if you are planning to build something bigger or if your town is regularly visited by hurricanes/snow. The treehouse will need maintenace (mainly re-varnishing) and regular inspection for any parts looking about to fail. Last, you have to control the maximum number of people and weight on the treehouse (i.e. don't overload it).
Step 1: Tools and Materials
Tools
When I started the project, my only power tools were a hand drill and an orbital sander. So the first beams were cut with a hand saw plus a sanding block to square them. As time went by I got a number of power tools that I had already planned to buy. The list below includes the main tools that made life easier but don't let the lack of any put you off - a hand tool and time/patience will do the job.
Power Tools
- Drill, with a set of common wood bits, a hole saw bit and some long bits for wood.
- Orbital sander. You can live without one but your project will look way cooler if you sand all your wood before applying varnish/stain. All visible parts of my t/h have gone through P80, P150 and P250 grits
- Bench drill. Will help with the holes of step 8 (diagonal support) and the pilot holes for the rafters. Will also help standardize the pilot holes for the balusters. You can use a hand drill and a jig instead.
- Circular saw. You need a jig for cross cuts/ miter cuts plus a long 2.5m jig for ripping plywood boards (the standard size here is 2.5 x 1.25 meters). Just google "DIY Circular Saw jig" and you will find many ideas how to build something like the one in the pictures above. If you own a table saw you are fine without any jig.
- Router. It speeds up rounding all the exposed sharp corners and making rabbets for door/window hinges
- Jigsaw
- Belt sander
Other Tools
You need a long straight edge (I use a 20X40mm square aluminum tube) and a long "L" shape square ruler (I use a 40x60cm). You will need to screw a lot of lag screws/bolts so a ratchet is good to have. Also a digital angle meter comes handy for the rafters and roof sheathing. Other than that you will need common tools that you likely already have like a hammer, rasp, wire extention, chisel, clamps, hand saw, sanding block, spirit level, ladder etc.
Main Materials
- 6 lag screws for your main (holding) bolts - get the thicker you can find. I got 16x200mm (5/8"x8") but in many countries you can easily find 20x300mm (3/4"x12). Also you need matching washers. If you are planning to go big/heavy forget the lag screws and get Treehouse Attachment Bolts (TABs)
- 2 boards 50x250mm (2"x10") for your main beams
- 6 boards 50x150mm (2"x6") for your floor joists
- 2 boards 80x150mm (3"x6") for your floor end joists (or fascia or whatever thery're called)
- 20mm (1") thick tongue & groove planks for your (interior) floor
- 20x120mm (1"x5") treated wood for the deck floor
- 35x45mm (2"x2-1/2") wood for the wall frame
- 50x100mm (2"x4") boards for the top plates of the side walls
- 14mm thick tongue & groove planks for your exterior wall sheathing
- 6mm poplar plywood for the interior wall panelling
- 50x100mm (2"x4") boards for the rafters
- 10mm plywood for the roof sheathing (rated for exterior use)
- Western red cedar tiles and tar paper for the roof
All boards and planks are swedish pine, as it is broadly used here for porches/shelters and it is cheap. I don't include the lengths in the description, as they always depend on the size of every particular treehouse. Also these are only the main components - for the rest you will find more details in the steps below.
Step 2: Select the Trees
The trees that will host the treehouse are two pine trees (Pinus halepensis) that have a 50cm (20") diameter. At a height 1.8m (6') from the ground the minimum distance between them is 2.5m (8').
I know pines can handle some abuse - we have some trees with deep scratches that continue to grow and look fine. Nevertheless, I double checked with an agronomist, as the construction invlolves putting 3 lag bolts in each tree.
The tree on the right is leaning away from the other tree (which is ok) and it also tilts away from the house in the background (which creates a bunch of problems with the main beams). If one of your selected trees tilts too much in that direction, consider choosing another pair. Eventually, I had to chop a small triangular piece right above the main bolt, to make room for the main beam.
Step 3: Planning
First thing to do is collect from the internet and read as much material as you can. You can see what other people made here in instructables, in youtube and in some sites for general DIY (diychatroom.com, and finehomebuilding are two sites I got some ideas and posted some questions). Take notes and try to visualize the steps involved. There is also a book I found very helpful called "the complete guide to treehouses" - you find it here for free: https://www.scribd.com/doc/179028622/The-Complete-... Last, you can get ideas and techniques from similar projects. Google "wood balcony","deck", "tree platform" for the platform part of the t/h. Here you will find many deck guides/regulations that will help you understand the basics. Google "kids house", "wendy house", "garden shed" for the house that will sit on the platform.
The next thing is to start with a few sketches of what you would like to build. I can't stress enough how helping was the 3D modelling of the treehouse. From the initial 3D sketch-just a box between the trees on a 2D picture of the site- until the final model containing every little piece of wood. I used google sketchup (a great tool that is free) and it helped me spot and fix many issues before even nailing the first nail. Your first few sketches will help you settle on the basic layout (windows, doors, hatch door, decks) and some basic dimensions (house hight, roof slope, floor-to-ground hight).
Last, start asking in lumberyards about actual dimensions (in many countries they are not standard) and prices. Improve your rough sketches using the actual dimensions of the wood pieces you are planning to use.
Step 4: Installing the Bolts
First, you will need two boards of wood at least as long as the distance between the trees. Make sure that they are straight and square or the whole step will end with a poor result.
Think how high you want the floor to be from the ground and subtract 42cm (17") - i.e. the hight of the main beams + floor joists + thickness of floor boards. This way you calculate how high you need to make the holes for the bolts. Then, nail the boards temporarily on the trees, so that you can get them off and on easily but not too loosely so that they fall off on their own. The bottom of the boards needs to be at the hight you want your bolts.
With your spirit level adjust the height of the front board until it is parallel to the ground. Then let the spirit level sit on both boards near the tree on the left hand and adjust the height of the back board until it is level with the front board. Then put the level spirit on the back board and make it parallel to the ground by lifting/lowering its right edge. Continue working clock- wise untill you have both boards at the same hight and parallel to the ground.
When you are done with the leveling, mark on the trees the 4 points where the bottom of the boards toutch the bark of the trees. This is where you will be making the holes for the bolts and if you did a good job with the spirit level all your marks are at the same level and parallel to the ground. I put my marks at around 1.8m so that an adult will be able to walk under the treehouse without banging the head on the main beams. Also, at that hight the tree on the right hand was less tilted.
Next, for each of the 4 anchoring points you will need the following components:
- Lag bolt: 16x200mm was the biggest I could find. If you can get 20mm (3/4") thick or even 25mm (1") it would be great - you will just need to adjust the dimensions of the other components
- Large matching washer for your lag bolt
- A piece of metal tube having an ID that matches your lag bolt -pick a thick one. I managed to find a piece of galvanized steel tube with ID 16mm OD 22mm and cut it in short pieces with a hack saw
- Custom Bracket. I ordered them from a local smith shop and they are made of 5x30mm metal strips. The inner dimensions of the square need to be a little wider than the OD of the metal tube, to allow for some movement after they are installed. Also, you need two wider brackets that will act as your "sliding" brackets, allowing your treehouse to kind of "float" on the trees in windy days.
- Custom washer. I had them made at a local machinist (see picture for dimensions). The inner diameter must equal the thickness of the lag bolt. The outer diameter is not critical - just make it so that it matches the OD of a hole saw that you already have. The custom washers are needed to provide additional support to the unthreaded part of the lag bolt. This part of the bolt, thicker and stronger than the threaded part, must bear all the lateral forces (weight of the treehouse).
All the components above need to be galvanized (or way more expensive stainless steel) so that they will resist corrosion. The custom made brackets and washers I put, were just painted with a galvanizing coating but this is a poor substitute of proper galvanizing.
Start by making a hole with your hole saw at the point you previously marked, around 5mm deep. Then clear the hole with a chisel so that your custom washer fits tightly. Move to a second round of hole saw + chisel, then a third round etc, until your custom washer is deep enough in the tree. How deep is deep enough? The idea here is that you need the lag bolt to protrude from the tree enough so there is room for the main beam to seat on top in a vertical position plus a clearance margin from the tree. At the same time you need the lag bolt to be deep enough in the tree so it holds well (theory goes that you need a penetration of at least 8 times the diameter of the lag bolt) taking into account how soft the bark of the tree is. In any case, make sure that the not threaded part of the lag bolts is at least 10mm inside the custom washer. After placing the custom washer, use a long drill bit with a diameter around 2/3 of the diameter of the lag bolt and drill a pilot hole in the hole left by the hole saw. Last install the 5 components listed above in the order shown in the 2nd picture.
Repeat the process for all 4 anchor points, make sure you put the 2 long brackets on the same tree and congratulations! You 're done with this step. Your neighbour still wonders why it took you so long to just "put some screws" on your trees.
Step 5: Installing the Main Beams
The main beams are 50x250mm (2x10) boards - make sure they are straight and square before buying . Call a friend to help you lift them on the anchor points. Mark where you need to cut them (leave a fair distance after the end of the bracket) and also where the bolts and the brackets will be along the board. If there is not enough room on the lag bolt for the beam to sit vertically, you can make a shallow recess for the end washer (see photo). I was unlucky to have to work with a quite tilting tree, so additionally to the recess I had to remove some material from the top of one beam and also to chop off a slice of the tree at one point. Before grabbing the saw, make sure there is no other alternative.
When you are happy with how the main beams sit on the anchor points (don't forget to leave a margin of at least 10mm between tree and beam), take them down for cutting, sanding and varnishing. Then, place them on the anchor points again and temporarilly secure them with two short 8mm lag bolts per bracket. Do a last check to see if they are parallel to the ground and sit at the same hight, just like you did in the previous step. Correct any discrepancy by making a shallow recess for the bracket where the beam needs to be lower (again, see photo) and/or with thin metal shims where the beam needs to be higher. When you finish with the levelling, replace the short 8mm lag screws with 8x150 lag bolts to secure the boards permanently.
Last, temporarilly connect the two main boards with a piece of wood and screws, so that they don't move while you will be working with the floor joists (next step).
Step 6: Installing the Floor Joists
The floor joists are 50x150mm boards (2"x6") - there are 6 joists each one 2.1m (7 ft) long.
Start by cutting, sanding and varnishing the 50x150 boards. Then put the first (right-most) joist on the beams, and make sure it is square (vertical) to one of the beams. The main beams are probably not parallel to each other (as you look them from above) as one tree might be thicker than the other. So you need to pick a main beam for reference and square all the joists with that one. Use two long clamps to secure the joist on the beams and attach it with a joist hanger (the black metal strip shown in the picture) and 8x40mm lag bolts. Put six lag bolts on every joist hanger - 3 on the joist and 3 on the beam. In the photos above you will see twice as many bolts that are totally unnecessary (I tended to overbuild in the beggining).
Then, continue as before with the last (left-most) joist.
After that, finish with the in-between joists while checking with your long straight edge that all joists are aligned ( their edges are in the same line). For the spaceing between the joists, take into account what will be placed above. In the above sketch the 4th joist from the left will hold the treehouse front wall right above. Also, the first set of joists leaves an opening for a trap door and the last set leaves room for the tree that goes through the deck.
Step 7: Completing the Floor Frame
To complete the frame there are two additional boards connecting the edges of the floor joists - lets call them end joists. These are 80x150mm (3"x6") boards, i.e. the same hight (150mm) as the floor joists but a little thicker (80mm vs 50mm) to facilitate the next step (diagonal support). They are cut so that on each side they are around 200mm longer than the end of the frame. Towards the edge of the board you need to make a 16mm hole for a 16mm eye bolt that will hold the steel rope for the diagonal support (see the sketch above).
First start by cutting, sanding and varnishing the 80x150 boards. Mark 200mm from each edge (this is where they will join with the edges of the outer floor joists) and make the 16mm holes for the eye bolts. Then place 2 stop blocks on each side of the frame and secure them in place with a long clamp (see 2nd photo). Now you have a convenient holder for the end joist while you will be connecting it to frame with joist hangers. On each joist hanger put four 6x60mm lag screws on the end joist (2 on each side), and three 6x lag screws on the floor joist (1 on each side and one longer on the bottom). My boards were a little scewed so I just clamped them straight before fixing the joist hanger (3d photo).
Step 8: Diagonal Support
Typically, a tree house is supported (in addition to anchor points) with "knee braces" i.e. boards of wood with one end on the tree and the other end near the edge of the platform, placed at 45 degrees. I didn't like how the knee braces looked in my design as the board edge towards the tree came too low, placing too much wood below the floor and spoils the illusion that the house floats in the air. Thus, I came with the idea to diagonally support the platform from above using steel wire (see 1st pic). Have in mind that this (unconventional) design will not work in heavier projects, as the bolt holding the steel rope may eventually enlarge the hole in the wood that hosts it, making the platform unstable. The components used for this part of the project were selected oversize -mostly 16mm (5/8")- on purpose, as they look better /more impressive while being just a little more expensive than the next smaller size.
The anchoring components towards the side of the platform, bottom to top (as seen in the 2nd pic):
- 16mm (5/8")bolt
- 16mm washer (OD 48mm, thickness 2mm)
- 16mm washer (again)
- 16mm safety washer
- 16mm eye bolt with female thread
- 12mm (1/2") shackle
- 12mm turnbuckle
12mm (1/2") shackle
8mm (5/16") steel wire
The anchoring components towards the side of the tree, are shown in the 3d pic, and they are the same as those used in step 4, except for the thick custom made washer which we don't need here as the lag bolt will protrude just a little.
I first started by placing all the eye bolt components - I used some red threadlock (loctite). Then, I calculated how high on the tree I need to make the hole for the lag bolt that will hold the other end of the steel wire. The wire needs to form an angle of around 60 degrees with the platform - so this is a good opportunity to dig out of the dust your high school math books.
After finding the right hight, I repeated what I did in the 4th step, only this time making just a shallow recess with the hole saw for the thin washer to sit inside.
Then, I connected the two anchor points with a thin string, marked, cut and measured the exact distance between them. Last, I subtracted the length of turnbuckles and shackles to find how long the steel wire needs to be. As the trees are not straight, each of the 4 pieces of steel wire had different lengths. I double-checked the dimensions and ordered the four pieces ready with the loops made by the seller. If you are going to make the loop yourself you need a thimble (shaping the loop) and a ferrule (securing the loop) - you can have them made for a small additional cost.
Last, I adjusted the turnbuckles. You need to find the sweet spot where the steel wire is just about to lift the platform, not too slack but not releasing the weight from the main anchor points of step4.
After finishing this step, you can climb on the platform and walk around stepping on the joists. This is the time to check that it is rock steady and not making any noise as you walk. It is also a step guaranteed to make your day.
Step 9: Completing the Floor
I first started with the frame for the trap door (yellow boards in 1st pic). I Picked a convenient corner of the platform and made a frame leaving a 10-15cm distance from where the walls will be. The boards for the frame don't need to be as thick as the floor joist - they won't hold any big load. I put the frame in place with corner braces where there was enough space and pocket screws where there was not, making sure the frame is flush with the upper edges of the joists.
The floor has two sections: the interior floor (yellow-brown in the 2nd pic) made of 20mm (3/4") tongue and groove planks, and the deck floor made of 20mm (3/4") treated wood.
Starting with the deck floor, I first calculated to 12mm the needed gap between the planks so they can be spaced evenly across the deck without the need for an odd (rip cut) plank. Then I found a strip of wood 12mm wide and use it as a jig. I also clamped a board at the edge of the deck, to help with aligning the edge of the planks with the frame (as shown in the 3d pic). Every plank sits on 2-1/2 joists (the last joist is shared with the planks for the interior floor) - so each is mounted with six 4x50mm inox screws (2 screws over each joist). With the help of some cardboard I made a template for cutting the planks at the point the tree comes out of the deck (4th pic).
For the interior floor, I started by ripping the groove of the 1st T&G plank placing it at the edge of the platform right next to the trap door frame. Fixing with screws the side of the plank that will be under the wall, I nailed the other side (side with the tongue) with 2x45mm nails over every joist. The nails go at an angle just above the tongue so they are hidden by the groove of the next plank (google how to install T&G planks if it's your first time). The rest of the floor is mostly like doing a jigsaw puzzle, you only need to rip the last plank so it is flush with the floor frame.
Step 10: 10. Trap Door
First, you need to put some strips of wood on the trapdoor frame to hold the trapdoor when closed. I put some 20x20mm strips I had on all 4 sides of the opening. I made some indents to accomodate the corner braces of the previous step. If there is going to be any rubber strip between the frame and the trapdoor, you need to take it into account when placing the 20x20 strips.
The trapdoor itself is made of of the same planks used for the interior floor, fixed with screws on two vertical planks. Recesses for the hinges and the handle were made with a forstner bit and a chisel. Make sure to check that they are both sharp - I regret that I didn't.
That's all. Don't forget to round all sharp corners of the frame and the trapdoor before sanding/painting.
Step 11: Wall Frames
Steps 11 to 14, i.e. most of the house, were built in my workshop over the winter. That saved a lot of trouble, climbing up and down the t/h all the time.
The wall frames are made of 33x42mm boards (white in 1st pic), except the top plates of the side walls (brown in 1st pic) which are made of 44x95mm (nominal dimension is 50x100mm or 2"x4"). The 33x42 boards were connected with 6x80mm inox screws (1 screw in every junction), using an angle clamp to hold them while making the pilot holes. The thick 44x95 plates of the side walls were connected to the studs (the vertical boards) with angle braces and then 6x80mm screws through pocket holes (see last two pictures).
I left for the moment all the horizontal boards for the door and window frames, and put them later while placing the exterior siding (next step).
The top plates of the side walls were made of thicker boards, so that they hold an extended roof overhang (60cm or 2") without the need of knee braces. The overhang will cover most of the deck.
Joining all the frames, I get a "box" measuring 2.16m front&back, 1.6m sides and 1.6m high
Step 12: Exterior Wall Siding
For the wall siding I used 14mm thick T&G planks and nailed them on the frame with two 2x40mm nails on every junction with the frame boards. Using a short piece of metal rod and the hammer, I pushed the nail heads a little inside the planks so that they can be covered with wood filler and not be visible.
The horizontal sides of the window&door openings were all made close to the edge of some plank to minimize the need for trimming. After arranging the TG planks to create an opening, I placed the horizontal boards at the edges of the openings, thus completing the wall frame of the previous step (see 2nd pic).
The bottom plank of each wall will need to go about 40mm lower than the bottom plates of the frame so that it will cover the sides of the floor planks. So I temporarilly fixed them with screws on the frame, ripped the bottom to get rid of the groove (3d pic) and then put them aside for later. Also, the top plank of each wall need to match with the roof and rafters, so I saved them for later.
After completing with the siding, it was time to join the 4 walls and have a first look of how the house will look. I joined them with three 8x90mm screws + nuts + washers in every corner. The last pic shows how the back wall and the side wall join and the overlapping pattern of the wall siding.
Step 13: Ridge Board and Rafters
The hardest part with the roof for me was all the calculations required for the rafter dimensions. There are some practical tricks in the net that may help you and if you want more than that, I added an excel sheet where you can type the input values and have all the other values you will need - just round the figures to the rearest 0.5mm.
The input values for the calculations are (all symbols are described in the first pic):
- The inclination ratio. I chose a value of 0.5 meaning when you move 1cm along the wall, the roof rises 0.5cm
- (A) The width of the front wall (final width including siding and everything) divided by 2. This is the middle of the wall (mark it with a knife) - the ridge board has to be right above. In my case A=2270/2=1135mm
- (a) The hight of the rafter boards. The actual dimensions of the boards I selected for rafters were 45x95mm, so a=95
- (b) The overhang of the roof. The norm is 1' or 300mm overhang but I decided to make it shorter to 200mm
- (c) The length of the top side of the "bird's mouth" (the small indent at the wall-rafter joint). I chose a value of 45mm as it looked ok for the thickness of the walls.
- (RB) the thickness of the ridge board. I used a 19x145mm board so RB=19
After writing down all the other values derived from the input values, I cross cut the 19x145mm board that will make the ridge board and I made two supports to hold it up. Each support is a sandwich of 35x45mm boards with a piece of 19x145mm in the middle and is mounted on the wall at the middle point with metal brackets (see 3d & 4th pic). The length of the supports is calculated so that the top of the ridge board is 651mm above the walls (H=651)
After that, I set the angles to the cross cut jig and the belt sander jig to 26.6 degrees, and cut a test rafter using a scrap piece of wood a x (L+e) to account for the lost length of the diagonal cut . The "bird's mouth" was rough cut with a hand saw and then shaped with a sanding block. When I was happy with how the rafter looks and how it fits on all rafter marks left and right, I cut the real rafters. If the board and walls are less than perfectly squared (I had +/-1mm discrepancies) it is better to cut the rafters a little longer and then sand them to fit tightly against the ridge board.
Last, I temporarilly mounted the 2 rafters right above the front wall and the other 2 of the back wall, and rough cut the exterior siding of the roof in a triangular shape (sorry - no picture for this sub-step)
The rafters and siding are not permanently installed on the wall until step 15
Attachments
Step 14: Interior Wall Sheathing
At this point, I test fitted some 6mm poplar ply sheets that will make the interior wall sheathing. No pictures for this step, but it is a quick and easy one. I just used some 3mm screws to temporarilly attach the ply on the inside of the walls, marked where the openings will be for door&windows and also the top end of the sheathing. Then, I roughly cut the ply, leaving some margin that will be trimmed flush after the final assembly on the tree.
Step 15: 15. Assembling the House on the Platform
After disassembling and carrying everything from the workshop to the site, I used my car as a platform to help lift the walls. Each wall was around 25kg heavy, so I had to ask a friend for a helping hand.
For aligning the first wall, I clamped a board on the side of the t/h platform.A leftover piece of the same boards used for the wall studs is temporarily mounted with screws to provide diagonal support until the second wall is bolted against the first wal (2nd pic).
When all the walls were put to place and bolted to each other, I fixed them on the platform with ten 8x120mm lag bolts (I think 6x120 would be fine) - 3 bolts on each long wall and 2 bolts on each short one.After this, I added the bottom T&G plank to complete the wall siding. This bottom plank goes 40mm lower than the bottom plate of the wall so that to protect the floor planks (4th & 5th pic).
I made a shallow hole on every roof rafter with a 25mm forstner bit to make room for a washer and nut. Then I drilled the center of the shallow hole all the way to the other side with a 5mm bit. Last, I mounted the rafters on the walls with 8x140mm lag bolts (1 bolt per rafter), and on the ridge board with long 6mm screws (2 screws per rafter).
Before placing the interior sheathing, I put some black and red pairs of wires that will be hidden inside the walls. They all start at the same point (shown at the 7th pic) where a small box will be placed to accomodate a small 12V battery and some switches. From there, two pairs go up the ceilng, another two outside the house and last pair goes over the deck. They will be used for some lights, a ceiling fan and whatever other project- some may be left idle.
Last, I fixed the interior sheathing with 3mm screws and small nails. All nails and screws go a little deeper than the surface of the sheathing and they are covered with wood filler so that they don't show. At this point, I trimmed flush to the rafters all interior and exterior wall sidings that were roughly cut oversized in the previous steps.
Step 16: Roof Sheathing
The first thing to do here is to put some stop blocks at the end of the rafters.These will hold the large plywood panel until it is fixed with screws. For the roof sheathing I used 9mm plywood for exterior uses (WBP ply). I cut the edge of the ply with the same angle as the roof (26.6 degrees) and applied a light clear coating. The 1st pictures shows a scrap piece of sheathing that I used to check that the two angles match.
After putting the ply sheets at place, I attached them with 4x35mm screws. Unfortunately, the ply sheets were not wide enough to cover the entire roof, so I had to add two stripes of ply towards the top of the roof putting silicone at the junctions.
Eventually, I had to climb on the roof to place all the screws. The 9mm ply is not thick enough so you have to step mainly over the rafters - I draw lines on the sheathing to always know where the rafters are. Some scrap pieces of board screwed over the rafters will help to have something to grab when up on the roof. I also put some nails to keep the wire extension from sliding down.
Step 17: Windows
The shutters for the two small windows, were made of four pieces of 10mm T&G boards (vertically aligned) nailed on two (horizontal) pieces of the same material. The technique is exactly the same as the trapdoor of step 10. The exterior trim for the small windows is made of 10mm waterproof plywood that has been painted with mineral based paint after several hands of filler+sanding. For each frame, I glued together 4 pieces of ply with half lap joints made on the router table.
Surprisingly, the main window was the most time consuming part of the whole project. I had to do and re-do things a number of times as there are many parts that need an alignment as close as possible to prefection. The basic idea here was to glue together two "layers" of wood boards, the top layer being more narrow, so that there is a rabbet/recession for the 4mm thick acrylic glass. The rest of the story is better explained by looking at the comments on the photos.
Step 18: Door
The door is simply a frame made of the same material as the wall studs with 10mm T&G for exterior siding and 6mm poplar ply for the interior siding. Again, I first bought all the hardware and then designed the door so that everything fits nicely. Both int & ext siding are fitted in a rabbet made on the frame (see 3d photo). Then, I applied a dark brown varnish on the visible part of the door frame to make a contrast with the siding.
Step 19: Roof Shingles
Coming soon (er or later)
Step 20: Deck Rails
Coming soon
Step 21: Ladder
Coming soon
Step 22: Finishing Details
Coming soon
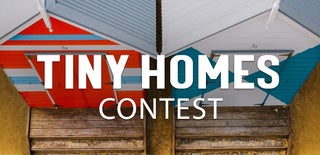
Participated in the
Tiny Home Contest